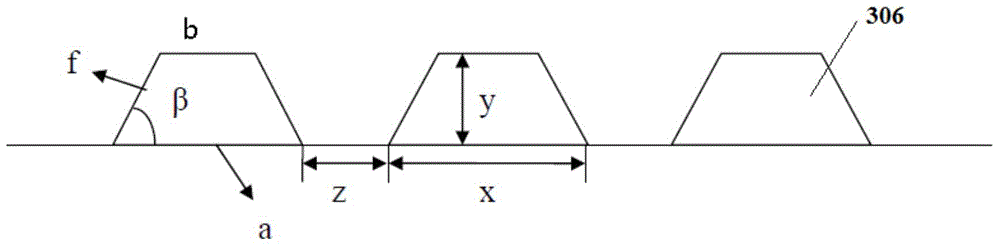
本發(fā)明涉及一種殼層分布型催化劑及其制備方法,本發(fā)明還涉及一種費托合成方法。
背景技術(shù):
:在催化劑孔道深處反應生成的產(chǎn)物分子如不能及時擴散出去而進一步發(fā)生反應,一方面影響催化劑的選擇性,另一方面將影響催化劑的壽命。尤其是對內(nèi)擴散為控制步驟的反應,希望反應發(fā)生在利于反應物和產(chǎn)物擴散的位置,一般希望發(fā)生在催化劑表層。另外,在催化劑的成本中,活性組分的成本所占的比例較大,如果將利用率不高的分布在孔道深處的組分移至接近催化劑表層的區(qū)域中,無疑會顯著提高催化劑的活性和選擇性。對于在固定床反應器中進行的如費托(FT)合成這類氣-固-液多相反應體系,催化劑的顆粒尺寸一般為幾個mm,因此,擴散控制對催化活性的影響難以避免。人們注意到:由FT合成得到的重質(zhì)石蠟通常以液態(tài)、汽溶膠或漿態(tài)形式附著在催化劑表面,對反應物H2和CO在催化劑顆粒內(nèi)部的擴散產(chǎn)生影響。在反應物的內(nèi)擴散過程中,H2的擴散速度比CO快,CO在催化劑顆粒內(nèi)的擴散限制作用明顯強于H2。因顆粒的粒徑不同,導致了顆粒內(nèi)部CO濃度梯度的差異,影響了CO與金屬活性中心位的結(jié)合,使得在活性中心上吸附的H/C比增大,碳鏈增長幾率降低,降低了C5+的選擇性?,F(xiàn)有技術(shù)表明,相對于活性組分呈均勻分布的催化劑而言,活性組分非均勻分布的催化劑,如殼層型催化劑,由于擴散限制小,可顯著地提高如費托合成這類反應中的C5+選擇性,降低甲烷的選擇性,更適合用于費托合成這類反應。US5545674公開了一種制備殼層型催化劑的方法,該方法將載體在金屬 絲網(wǎng)上攤開,將金屬絲網(wǎng)在加熱爐中加熱至140℃以上,然后從爐中取出。將含負載組分的溶液噴涂于金屬絲網(wǎng)上的熱載體上,含負載組分的溶液在熱的載體表面被蒸干,再將帶有催化劑的金屬絲網(wǎng)放回加熱爐中重新加熱。如此反復多次,直到負載足夠的負載組分。US7087191公開了一種制備殼層分布型催化劑的方法,該方法將含活性組分的粉末和含難熔金屬氧化物的粉末用稀釋劑做成糊狀或泥漿狀,然后噴涂于表面經(jīng)過處理變得粗糙的惰性固體顆粒上,然后干燥、焙燒。這種方法可以保證催化劑活性組分不進入起載體作用的固體顆粒的內(nèi)部,但活性組分以粉末狀存在,粉末顆粒內(nèi)部的活性組分不能完全發(fā)揮作用,并且粉末靠物理作用與惰性固體顆粒表面粘在一起,這種物理粘接力比溶液浸漬法制備的催化劑中活性組分與載體表面間的化學鍵的結(jié)合力要弱許多。因此,與由活性組分的溶液制備的殼層分布型催化劑將相比,這種由活性組分粉末制備的方法降低了活性組分的利用效率,另外,使用中在氣流的沖刷下活性組分粉末也較容易從惰性固體顆粒表面脫落。US5545674公開了一種殼層分布型催化劑的制備方法,該方法通過使用具有中間干燥或燃燒步驟的浸入或噴霧方法將鈷尤其是硝酸鈷溶液反復浸漬到粒狀載體上。這些方法是繁瑣和費時的,并且采用多次浸漬方法,一些金屬會超出預期的外層滲入到載體中。CN101318133A公開了一種用于制備石腦油和柴油的殼層型催化劑,該催化劑以活性炭為載體,采取噴涂的方式將溶液噴到滾動的載體上,然后將催化劑在惰性氣體中干燥或焙燒。但是,該方法制備的催化劑的殼層率不高。US4599481公開了一種由一氧化碳與氫催化反應生產(chǎn)烴的方法,該方法包括在125-350℃,壓力5-100巴(bar)條件下將一氧化碳和氫與催化劑接觸,所述催化劑含有載體和負載在該載體上的鈷,所述鈷在載體上的分布滿足(∑Vp/∑Vc)<0.85,其中,∑Vc代表催化劑顆粒的總體積,Vp為催化 劑中殼層體積。當在殼中鈷的含量大約為90%時,催化劑有高的活性和選擇性。該催化劑的制備方法是先用水處理載體,之后浸漬硝酸鈷溶液,然后干燥和焙燒。這種制備方法對時間的要求很嚴格,并且操作繁瑣,不容易規(guī)?;a(chǎn)。CN102451722A公開了一種蛋殼型加氫催化劑的制備方法。該方法采用含有增稠劑和活性金屬分散劑的活性金屬水溶液浸漬載體,其中在通入空氣鼓泡的條件下進行浸漬,再經(jīng)干燥和焙燒,得到蛋殼型加氫催化劑。該方法能有效調(diào)節(jié)蛋殼型加氫催化劑表面活性、金屬殼層的厚度以及活性金屬的分散度,能穩(wěn)定加氫催化劑上的活性金屬組分,減少活性金屬組分的流失,降低催化劑生產(chǎn)成本。但是,這種制備方法對時間的要求很嚴格,并且操作繁瑣,不容易規(guī)模化生產(chǎn)??梢?,仍然需要繼續(xù)探索制備殼層分布型催化劑的方法。技術(shù)實現(xiàn)要素:本發(fā)明的目的在于提供一種殼層分布型催化劑及其制備方法,由該方法制備的催化劑殼層率高。根據(jù)本發(fā)明的第一個方面,本發(fā)明提供了一種殼層分布型催化劑的制備方法,該方法包括將多孔載體置于中空容器中,將含有催化活性組分的溶液噴涂在所述多孔載體表面,所述溶液的總噴涂量小于所述多孔載體的總孔體積,所述中空容器具有用于接收多孔載體的可開合進料口以及用于輸出多孔載體的可開合出料口,所述中空容器的軸線相對于水平面為傾斜設(shè)置,進料口位于較高的軸向一端,出料口位于較低的軸向另一端,在噴涂過程中,對所述中空容器進行抽真空,且用于抽真空的抽氣口布置在由多孔載體形成的層中,負載有溶液的多孔載體通過所述出料口離開中空容器,同時通過所述進料口向中空容器中補充多孔載體,將離開中容器的多孔載體進行干燥以及 可選的焙燒。根據(jù)本發(fā)明的第二個方面,本發(fā)明提供了一種由本發(fā)明的方法制備的殼層分布型催化劑。根據(jù)本發(fā)明的第三個方面,本發(fā)明提供了一種費托合成方法,該方法包括在費托合成反應條件下,將合成氣與催化劑接觸,其中,所述催化劑為采用本發(fā)明的方法制備的對費托合成反應具有催化作用的殼層分布型催化劑。根據(jù)本發(fā)明的殼層分布型催化劑的制備方法,制備的催化劑的殼層率高,能重復穩(wěn)定地生產(chǎn)殼層分布型催化劑。采用本發(fā)明的方法能穩(wěn)定地生產(chǎn)殼層分布型催化劑的原因可能在于:在將含有催化活性組分的溶液噴涂到多孔載體表面時,附著在多孔載體表面的溶液在浸漬進入多孔載體的孔隙的過程中,由于吸附放熱,使得部分溶劑揮發(fā)形成蒸氣,這些蒸氣的存在會導致催化活性組分向多孔載體的芯部遷移,破壞形成的殼層結(jié)構(gòu);根據(jù)本發(fā)明的方法在噴涂的過程中,進行抽真空,且用于抽真空的抽氣口填埋在由多孔載體形成的層中(即,用于抽真空的抽氣口布置在由多孔載體形成的層中),將彌散在多孔載體之間的溶劑蒸氣及時并充分抽出,能有效地降低催化活性組分向多孔載體的芯部遷移的趨勢,從而提高制備的催化劑的殼層率。根據(jù)本發(fā)明的殼層分布型催化劑的制備方法,操作過程簡單易控。并且,根據(jù)本發(fā)明的殼層分布型催化劑的制備方法,在制備過程中,能連續(xù)將負載了催化劑活性組分的多孔載體從中空容器中卸出,同時連續(xù)向中空容器中補充新多孔載體,從而能實現(xiàn)連續(xù)化作業(yè)。因此,根據(jù)本發(fā)明的殼層分布型催化劑的制備方法特別適于規(guī)?;瘜嵤?。將由本發(fā)明的方法制備的殼層分布型催化劑用作費托合成反應的催化劑,能獲得較高的C5+烴類選擇性和較低的甲烷選擇性。附圖說明附圖是用來提供對本發(fā)明的進一步理解,并且構(gòu)成說明書的一部分,與下面的具體實施方式一起用于解釋本發(fā)明,但并不構(gòu)成對本發(fā)明的限制。圖1是用于制備本發(fā)明的殼層分布型催化劑的裝置的結(jié)構(gòu)示意圖。圖2是用于說明中空容器的內(nèi)壁上設(shè)置的揚料板的結(jié)構(gòu)示意圖。附圖標記說明101:多孔載體儲罐201:含有催化活性組分的溶液儲罐202:泵301:中空容器302:進料口303:出料口304:噴桿305:抽真空管線306:揚料板307:底架308:升降部件309:基座310:動力產(chǎn)生部件311:傳動部件401:干燥帶402:殼體具體實施方式以下對本發(fā)明的具體實施方式進行詳細說明。應當理解的是,此處所描述的具體實施方式僅用于說明和解釋本發(fā)明,并不用于限制本發(fā)明。在本發(fā)明中,“軸向”和“徑向”是相對于中空容器而言的,即沿中空容器的轉(zhuǎn)軸方向延伸的方向為軸向方向,而垂直于該軸向方向為徑向方向,需要說明的是這些方位詞只用于說明本發(fā)明,并不用于限制本發(fā)明。在本發(fā)明中,“任選的”表示可以包括與“任選的”相接的技術(shù)特征,也可以不包括與“任選的”相接的技術(shù)特征。在本發(fā)明中出現(xiàn)的數(shù)值范圍均包括構(gòu)成該數(shù)值范圍的兩個端值。根據(jù)本發(fā)明的第一個方面,本發(fā)明提供了一種殼層分布型催化劑的制備 方法,該方法包括將多孔載體置于中空容器中,將含有催化活性組分的溶液噴涂在所述多孔載體表面,在噴涂過程中,對所述中空容器進行抽真空。根據(jù)本發(fā)明的方法,含有催化活性組分的溶液的總噴涂量小于所述多孔載體的總孔體積。從進一步提高制備的催化劑的殼層率的角度出發(fā),含有催化活性組分的溶液的總噴涂量為VL,所述多孔載體的總孔體積為VC,VL/VC=0.01-0.99;優(yōu)選地,VL/VC=0.1-0.8;更優(yōu)選地,VL/VC=0.2-0.7;進一步優(yōu)選地,VL/VC=0.2-0.6。本發(fā)明中,VC等于多孔載體的質(zhì)量(以克計)乘以多孔載體的吸水率(水的密度為1g/cm3),吸水率為單位重量的載體的吸水量。具體地,可以采用以下方法測定吸水率:可以將載體(重量計為w1,以克計)用水以載體(以重量計)與水(以體積計)的比例為1:3浸漬2小時,過濾后,將固體瀝干,接著稱取瀝干的固體的重量(重量計為w2,以克計),由以下公式計算吸水率:根據(jù)本發(fā)明的方法,可以采用常見的各種方法將含有催化活性組分的溶液噴涂在多孔載體表面。優(yōu)選地,將含有催化活性組分的溶液以霧化液滴的形式噴涂在多孔載體表面。從進一步提高最終制備的催化劑的殼層率以及催化效率的角度出發(fā),所述霧化液滴的大小優(yōu)選在1-600微米的范圍內(nèi),更優(yōu)選在20-400微米的范圍內(nèi),進一步優(yōu)選在50-300微米的范圍內(nèi),更進一步優(yōu)選在60-200微米的范圍內(nèi),如在100-200微米的范圍內(nèi)。本發(fā)明中,霧化液滴的大小采用馬爾文粒度分析儀來測量,為體積平均粒徑。在具體操作過程中,可以通過調(diào)節(jié)噴射壓力來調(diào)節(jié)形成的霧化液滴的大小。根據(jù)本發(fā)明的方法,所述中空容器具有用于接收多孔載體的進料口以及用于輸出多孔載體的出料口,所述中空容器的軸線相對于水平面為傾斜設(shè)置,進料口位于較高的軸向一端,出料口位于較低的軸向另一端,在噴涂的 過程中,負載了含有催化活性組分的溶液的多孔載體持續(xù)向出料口移動,并最終離開中空容器,這樣可以相應地向中空容器中連續(xù)補充多孔載體,從而實現(xiàn)連續(xù)化作業(yè)。通過改變中空容器傾斜的角度,可以對多孔載體在中空容器中向出料端的移動速度進行調(diào)節(jié)。一般地,中空容器的軸線相對于水平面的傾斜角度α為1°-45°更優(yōu)選為1°-15°,進一步優(yōu)選為2°-10°。所述中空容器可以為常見的各種形狀,優(yōu)選為筒狀。優(yōu)選地,將所述進料口和所述出料口設(shè)置成料斗的形式。所述料斗優(yōu)選具有可開合頂蓋和可開合底蓋,這樣可以在不對中空容器內(nèi)的抽真空效果產(chǎn)生明顯影響的條件下,實現(xiàn)連續(xù)進料和出料。具體地,在向作為進料口的料斗中送入多孔載體時,可以將與中空容器相接的底蓋閉合,料斗中的多孔載體的量滿足要求時,則可以閉合頂蓋,并在需要時開啟進料口的底蓋,以向中空容器內(nèi)部輸送多孔載體;在需要將中空容器中的多孔載體輸出時,可以開啟出料口與中空容器相接的頂蓋,使多孔載體進入作為出料口的料斗中,此時出料口的底蓋閉合,出料完成后,閉合出料口的頂蓋,同時開啟出料口的底蓋,將料斗中的多孔載體卸出。從進一步提高含有催化活性組分的溶液與多孔載體接觸的均勻性的角度出發(fā),噴涂的過程中,優(yōu)選使多孔載體處于運動的狀態(tài)。所述運動的形式可以為振動、滾動、翻動和滑動中的一種或兩種以上的組合。在實際操作過程中,可以使中空容器以軸線為中心進行轉(zhuǎn)動,從而帶動中空容器中的多孔載體運動。一般地,中空容器的轉(zhuǎn)速可以為2轉(zhuǎn)每分鐘至15轉(zhuǎn)每分鐘,優(yōu)選為4轉(zhuǎn)每分鐘至12轉(zhuǎn)每分鐘,更優(yōu)選為5轉(zhuǎn)每分鐘至10轉(zhuǎn)每分鐘。中空容器的內(nèi)壁面上優(yōu)選設(shè)置揚料板,這樣在中空容器轉(zhuǎn)動時,多孔載體可以在揚料板的攜帶下被揚起一定的高度,從而實現(xiàn)對多孔載體進行更為有效地翻動,以使含有催化活性組分的溶液更為均勻地被噴射在多孔載體表面,從而使得制備的催化劑具有更為均勻的組成。揚料板可以為各種能夠?qū)? 現(xiàn)上述功能的構(gòu)件。在一種優(yōu)選的實施方式中,如圖2所示,揚料板306為固定在中空容器301的內(nèi)壁面上的凸起。該凸起從中空容器301的內(nèi)壁朝向中空容器301的轉(zhuǎn)動中心凸出,以能夠在中空容器301轉(zhuǎn)動的同時將多孔載體提升到一定高度后再拋下,從而實現(xiàn)對多孔載體進行翻動。如圖2所示,所述凸起包括條狀結(jié)構(gòu)主體,優(yōu)選該條狀結(jié)構(gòu)主體沿中空容器301的軸向方向布置。更優(yōu)選地,揚料板306包括多列平行設(shè)置的凸起,其中相鄰兩列之間的間距可調(diào),這樣能夠改變多孔載體的翻料頻率,繼而改變浸漬效果。具體地,相鄰兩列凸起的間距為越小則翻料的頻率越大。作為一種優(yōu)選方式,相鄰兩列凸起之間的間距為z,且滿足為0<z<R,優(yōu)選為0<z<0.25R,更優(yōu)選為0<z<0.125R,進一步優(yōu)選為0.1R≤z≤0.12R,其中,R為中空容器301的半徑(為內(nèi)半徑),以實現(xiàn)最好的浸漬效果。另外,每條凸起的布置方向除平行于軸向方向外,還可以與軸向方向具有一定角度的布置,或者多條凸起之間成角度地交錯布置,對于這些布置方式均應落在本發(fā)明的保護范圍中。從進一步提高翻動效果的角度出發(fā),如圖2所示,凸起的徑向截面為多邊形,該多邊形包括固定在中空容器301的內(nèi)壁面上的底邊a,以及與底邊a鄰接的翻料邊f(xié),底邊a和翻料邊f(xié)之間的夾角β優(yōu)選為45°-90°,更優(yōu)選為60°-80°。其中,該夾角β的選擇決定了多孔載體被提升的高度,例如當夾角β為銳角時,由于方便多孔載體滑落,因此能夠降低多孔載體的提升高度,因此增加了每個多孔載體被翻動的頻率,同時加快了多孔載體軸向運動的速度。如圖2所示,該徑向截面除包括底邊a外,還包括上邊b,當上邊b的長度等于底邊a時,徑向截面為矩形,而當上邊b的長度為0時,則徑向截面為三角形,當上邊b的長度小于底邊a時,徑向截面為梯形。為了保證翻 料效果,優(yōu)選地,設(shè)計徑向截面的底邊a的長度為x,徑向截面的高為y,其中滿足:0.25y≤x≤2.5y,優(yōu)選滿足:1.5y≤x≤2.4y,從而使得多孔載體既能夠被提升,也能夠及時被拋下,從而達到最優(yōu)選的浸漬效果。根據(jù)本發(fā)明的方法,在噴涂的過程中,對中空容器進行抽真空。與在噴涂過程中不進行抽真空相比,通過抽真空能顯著提高制備的催化劑的殼層率,從而實現(xiàn)穩(wěn)定重復地制備殼層分布型催化劑。從進一步提高制備的催化劑的殼層率的角度出發(fā),所述抽真空的條件使得中空容器內(nèi)的相對真空度在-10kPa至-100kPa的范圍內(nèi)。更優(yōu)選地,所述抽真空的條件使得中空容器內(nèi)的相對真空度在-30kPa至-95kPa的范圍內(nèi)。進一步優(yōu)選,所述抽真空的條件使得中空容器內(nèi)的相對真空度在-40kPa至-80kPa的范圍內(nèi),如在-50kPa至-80kPa的范圍內(nèi)。本發(fā)明中,相對真空度=中空容器內(nèi)的絕對壓力(以kPa計)-101.3。所述相對真空度可以由真空壓力表測定。根據(jù)本發(fā)明的方法,優(yōu)選地,所述抽真空的條件使得所述中空容器內(nèi)由含有催化活性組分的溶液中的溶劑產(chǎn)生的分壓在0-30kPa的范圍內(nèi)。所述抽真空的條件使得所述中空容器內(nèi)由含有催化活性組分的溶液中的溶劑產(chǎn)生的分壓優(yōu)選為不高于20kPa,更優(yōu)選為不高于15kPa。在確保能夠獲得較高的殼層率的前提下,從進一步降低運行成本的角度出發(fā),控制抽真空的條件使得所述中空容器內(nèi)由含有催化活性組分的溶液中的溶劑產(chǎn)生的分壓為不低于0.1kPa即可。所述分壓可以由真空表測定。根據(jù)本發(fā)明的方法,一般在進行噴涂之前,預先對具有多孔載體的中空容器進行抽真空,優(yōu)選使得具有多孔載體的中空容器內(nèi)的相對真空度處于前文所述范圍之內(nèi),并將該相對真空度作為基準真空度,在噴涂的過程中,根據(jù)中空容器內(nèi)的相對真空度調(diào)整抽真空的條件,使得由含有催化活性組分的溶液中的溶劑產(chǎn)生的分壓處于前文所述的范圍之內(nèi)。噴涂過程中,中空容器內(nèi)的相對真空度與基準相對真空度之間的差值作為由含有催化活性組分的 溶液中的溶劑產(chǎn)生的分壓。根據(jù)本發(fā)明的方法,用于抽真空的抽氣口布置在由多孔載體形成的層中,即用于抽真空的抽氣口被填埋在由多孔載體形成的固體顆粒層中。用于抽真空的抽氣口可以朝向承載多孔載體的內(nèi)壁(即,與含有催化活性組分的溶液的噴涂方向一致),也可以背向承載多孔載體的內(nèi)壁(即,與含有催化活性組分的溶液的噴涂方向相對)。優(yōu)選地,所述抽氣口朝向承載多孔載體的內(nèi)壁,這樣能獲得進一步提高的殼層率,同時還能進一步降低含有催化活性組分的溶液的損失量。在實際操作過程中,可以通過在中空容器中布置真空管線,并在真空管線上開設(shè)抽氣口,從而實現(xiàn)在噴涂過程中進行抽真空。所述抽氣口的數(shù)量根據(jù)具體情況可以為一個或多個,多個抽氣口之間可以為等間隔,也可以為非等間隔,或者為等間隔或非等間隔的組合(即,部分抽氣口之間為等間隔設(shè)置,剩余部分抽氣口之間為非等間隔設(shè)置)。抽氣口的形式可以為常規(guī)選擇??梢酝ㄟ^在用于抽真空的管線上設(shè)置開口,從而形成所述抽氣口。所述開口的口徑優(yōu)選不大于多孔載體的粒徑。優(yōu)選地,在抽氣口上安裝過濾網(wǎng),以避免固體顆粒進入抽真空管線中??梢允褂糜诔檎婵盏墓芫€密封穿過中空容器的側(cè)壁,從而深入中空容器內(nèi)部。用于抽真空的管線與中空容器之間優(yōu)選為可轉(zhuǎn)動連接,這樣在中空容器轉(zhuǎn)動時,用于抽真空的管線不會隨中空容器轉(zhuǎn)動。用于抽真空的管線位于中空容器內(nèi)的部分可以根據(jù)中空容器的內(nèi)部形狀進行彎折,以使其能填埋在多孔載體形成的層中。用于抽真空的管線的數(shù)量可以為一根或兩根以上。在用于抽真空的管線的數(shù)量為一根時,用于抽真空的管線位于中空容器內(nèi)的部分可以呈蛇形彎折,以擴大抽氣口的覆蓋區(qū)域,從而將在多孔載體形成的層的各個位置區(qū)域中產(chǎn)生的蒸氣及時并充分地抽吸出去。在用于抽真空的管線的數(shù)量為多根時,多根用于抽真空的管線可以為沿與中空容器的轉(zhuǎn)軸方向平 行的方式排列,以擴大抽氣口的覆蓋區(qū)域;多根抽真空管線之間也可以為相互交叉,只要能使抽氣口位于由多孔載體形成的層的多個位置區(qū)域即可。可以沿中空容器的徑向設(shè)置一層或多層抽真空管線,多層抽真空管線之間可以為等間隔,也可以為非等間隔,每層抽真空管線可以具有一根或多根抽真空管線。根據(jù)本發(fā)明的方法,在噴涂過程中,對于中空容器內(nèi)的溫度沒有特別限定,可以在常規(guī)溫度下進行。一般地,在噴涂過程中,可以將中空容器內(nèi)的溫度控制在0-70℃的范圍內(nèi),優(yōu)選將中空容器內(nèi)的溫度控制在30-50℃的范圍內(nèi)。根據(jù)本發(fā)明的方法,所述多孔載體可以為常見的適于作為催化劑載體的多孔物質(zhì)。具體地,所述多孔載體可以為耐熱無機氧化物、硅酸鋁和活性炭中的一種或兩種以上。所述耐熱無機氧化物是指在氧氣或含氧氣氛下,分解溫度不低于300℃(例如:分解溫度為300-1000℃)的無機含氧化合物。所述多孔載體的具體實例可以包括但不限于:氧化鋁、氧化硅、氧化鈦、氧化鎂、氧化鋯、氧化釷、氧化硅-氧化鋁、硅酸鋁和活性炭中的一種或兩種以上。優(yōu)選地,所述多孔載體為氧化硅、氧化鋁、氧化硅-氧化鋁、硅酸鋁、氧化鈦、氧化鋯和活性炭中的一種或兩種以上。更優(yōu)選地,所述多孔載體為氧化鋁。本發(fā)明對所述載體的形狀沒有特別地限定,可以為常規(guī)形狀,例如,可以為球形、片形、條形等,優(yōu)選為條形。根據(jù)本發(fā)明的方法,所述多孔載體的平均粒徑可以根據(jù)催化劑的具體種類進行選擇,優(yōu)選在0.5-6mm的范圍內(nèi),更優(yōu)選在1-4mm的范圍內(nèi)。所述含有催化活性組分的溶液的溶劑可以為常規(guī)選擇,例如可以為水、醇、醚、醛和酮中的一種或兩種以上的混合物。優(yōu)選地,所述溶劑為水和/或醇,如水、甲醇和乙醇中的一種或兩種以上的混合物。從環(huán)境保護和降低 成本的角度出發(fā),所述溶劑更優(yōu)選為水。根據(jù)本發(fā)明的方法,所述催化活性組分的種類可以根據(jù)預期催化劑的使用場合進行選擇,以能夠獲得具有預定催化性能的催化劑為準,如第VIII族金屬元素和/或第VIB族金屬元素。在本發(fā)明的一種優(yōu)選的實施方式中,所述催化活性組分的種類使得由本發(fā)明的方法制備的殼層分布型催化劑對費托合成反應具有催化作用。在該優(yōu)選的實施方式中,所述催化活性組分可以為對費托合成反應具有催化作用的組分,優(yōu)選地,所述催化活性組分選自第VIII族金屬元素,具體可以為鐵、鈷和釕中的一種或兩種以上。根據(jù)本發(fā)明的方法,可以通過將含催化活性組分的化合物溶解在溶劑中,從而提供所述含有催化活性組分的溶液。含催化活性組分的化合物的種類可以根據(jù)溶劑的種類進行選擇,以能夠溶解在所述溶劑中為準。例如,在所述溶劑為水時,所述含催化活性組分的化合物可以為水溶性化合物。在本發(fā)明的一種實施方式中,所述催化活性組分為第VIII族金屬元素時,所述含催化活性組分的化合物可以為以第VIII族金屬為陽離子的水溶性非金屬含氧無機酸鹽、以第VIII族金屬為陽離子的水溶性有機酸鹽和以第VIII族金屬為陽離子的水溶性鹵化物中的一種或兩種以上。優(yōu)選地,所述含催化活性組分的化合物為以第VIII族金屬為陽離子的硝酸鹽、以第VIII族金屬為陽離子的醋酸鹽、以第VIII族金屬為陽離子的硫酸鹽、以第VIII族金屬為陽離子的堿式碳酸鹽和以第VIII族金屬為陽離子的氯化物中的一種或兩種以上。具體地,所述含催化活性組分的化合物可以選自但不限于硝酸鎳、醋酸鎳、硫酸鎳、堿式碳酸鎳、硝酸鈷、醋酸鈷、硫酸鈷、堿式碳酸鈷、氯化鈷、氯化鎳、氯化釕和硝酸釕中的一種或兩種以上。所述含有催化活性組分的溶液中催化活性組分的濃度可以根據(jù)催化劑中催化活性組分的預期負載量進行選擇,沒有特別限定。根據(jù)本發(fā)明的方法,所述含有催化活性組分的溶液在多孔載體上的負載 量以能夠確保最終制備的催化劑負載有足量的催化活性組分為準。一般地,所述催化活性組分在所述多孔載體上的負載量使得以最終制備的催化劑的總量為基準,以氧化物計的催化活性組分的含量為0.5-60重量%,優(yōu)選為1-50重量%,如10-30重量%。根據(jù)本發(fā)明的方法,所述含有催化活性組分的溶液還可以含有至少一種催化助劑組分和/或至少一種表面活性劑。所述催化助劑組分例如可以為磷元素和/或氟元素。在所述催化劑對費托合成反應具有催化作用時,所述催化助劑組分可以選自Li、Na、K、Mg、Ca、Sr、Cu、Mo、Ta、W、Ru、Zr、Ti、Re、Hf、Ce、Mn、Fe、V和貴金屬(如Pt、Pd、Rh和Ir中的一種或兩種以上)中的一種或兩種以上。所述催化助劑組分在所述含有催化活性組分的溶液中含量以最終制備的催化劑具有預期的催化助劑組分含量為基準。一般地,以最終制備的催化劑的總量為基準,以氧化物計的所述含催化助劑組分的含量可以為0.1-30重量%,優(yōu)選為0.5-15重量%,更優(yōu)選為1-5重量%。在所述催化劑對費托合成反應具有催化作用時,所述表面活性劑可以為離子型表面活性劑和非離子型表面活性劑中的一種或兩種以上。所述離子型表面活性劑包括陰離子型表面活性劑、陽離子型表面活性劑和兩性離子型表面活性劑。所述陰離子型表面活性劑的具體實例可以包括但不限于羧酸鹽型(如肥皂、油酸鉀等)表面活性劑、磺酸鹽型(如烷基苯磺酸鈉等)表面活性劑、硫酸酯鹽型(如十二烷基硫酸鈉等)表面活性劑和磷酸酯鹽型(如C16H33OPO3Na2等)表面活性劑。所述陽離子型表面活性的具體實例可以包括但不限于:銨鹽型表面活性劑、季銨鹽型(如十六烷基三甲基氯化銨等)表面活性劑。所述兩性離子型表面活性劑的具體實例可以包括但不限于甜菜堿型表面活性劑和氨基酸型表面活性劑。所述非離子型表面活性劑的具體實例可以包括但不限于聚乙二醇型表面活性劑(如脂肪醇聚氧乙烯醚、烷基苯 酚聚氧乙烯醚、脂肪酸聚氧乙烯醚、聚氧乙烯脂肪胺和聚氧乙基烷基酰胺,其中,氧化乙烯重復單元的重復鏈節(jié)數(shù)n可以為常規(guī)選擇,一般地,n=l-10)和多元醇型表面活性劑(如蔗糖的衍生物、山梨糖醇的衍生物和甘油醇的衍生物等)。本發(fā)明優(yōu)選所述表面活性劑為非離子型表面活性劑中的一種或兩種以上。所述表面活性劑在含有催化活性組分的溶液中的濃度優(yōu)選為0.01-10重量%。根據(jù)本發(fā)明的方法,噴涂完成后,將得到的負載有溶液的多孔載體進行干燥。所述干燥的溫度以能夠脫除負載在多孔載體上的溶液中的溶劑為準。一般地,所述干燥可以在50-300℃的溫度下進行,優(yōu)選在60-250℃的溫度下進行。所述干燥可以在常壓下進行,也可以在減壓的條件下進行。在本發(fā)明的一種優(yōu)選的實施方式中,所述干燥在常壓(即,1標準大氣壓)的條件下進行,所述干燥的溫度優(yōu)選在130-230℃的范圍內(nèi),更優(yōu)選在140-160℃的范圍。在本發(fā)明的另一種優(yōu)選的實施方式中,所述干燥在壓力(以表壓計)為-0.5kPa至-60kPa、優(yōu)選為-5kPa至-45kPa的條件下進行,所述干燥的溫度優(yōu)選在100-220℃的范圍內(nèi),更優(yōu)選在120-160℃的范圍內(nèi)。在上述兩種優(yōu)選的實施方式下進行干燥,制備的催化劑具有更高的殼層率,并且制備的殼層分布型催化劑中,殼層厚度更薄(即,沿催化劑的徑向截面,催化活性組分富集在更外層的徑向截面上),其原因可能在于:在用于噴涂的含有催化活性組分的溶液的體積不高于多孔載體的總孔體積時,多孔載體的芯部充當了吸附干燥劑的角色,吸附在多孔載體的外層溶液中的溶劑由于毛細凝聚作用有向多孔載體芯部遷移的趨勢,溶解在溶劑中的含催化活性組分的化合物也隨之向芯部遷移,從而影響殼層率;在上述兩種優(yōu)選的實施方式中,脫除溶劑的條件能有效地降低溶劑向多孔載體芯部的遷移趨勢,從而能夠獲得更高的殼層效率和更薄的殼層厚度。根據(jù)本發(fā)明的方法,所述干燥的持續(xù)時間可以根據(jù)干燥的溫度和壓力進行選擇,以能夠?qū)⒇撦d在多孔載體上的溶液中的溶劑全部或基本全部脫出為準。一般地,所述干燥的持續(xù)時間可以為1-48小時,優(yōu)選為1.5-24小時,更優(yōu)選為2-10小時,如2-5小時。根據(jù)本發(fā)明的方法,經(jīng)干燥的多孔載體可以直接用作催化劑,也可以進行焙燒后作為催化劑。本發(fā)明對于焙燒的條件沒有特別限定,可以為常規(guī)選擇。一般地,所述焙燒可以在300-600℃的溫度下、優(yōu)選在400-500℃的溫度下進行。所述焙燒的持續(xù)時間可以為1-48小時,優(yōu)選為2-12小時,更優(yōu)選為2-5小時。本發(fā)明的方法特別適于連續(xù)進行,這樣能夠以較高的生產(chǎn)效率制備具有較高殼層率的殼層分布型催化劑。在本發(fā)明的一種優(yōu)選的實施方式中,根據(jù)本發(fā)明的方法在一種制備系統(tǒng)中實施,從而連續(xù)制備殼層分布型催化劑。以下結(jié)合圖1對該制備系統(tǒng)進行詳細說明。所述制備系統(tǒng)包括含有催化活性組分的溶液供給單元、多孔載體供給單元、浸漬單元、真空單元以及干燥單元,所述含有催化活性組分的溶液供給單元用于向所述浸漬單元提供含有催化活性組分的溶液,所述多孔載體供給單元用于向所述浸漬單元提供多孔載體,所述浸漬單元用于使含有催化活性組分的溶液與多孔載體接觸,所述干燥單元用于將經(jīng)浸漬的多孔載體進行干燥,其中,所述浸漬單元包括用于承載多孔載體的中空容器301,中空容器301軸向一端設(shè)置有用于接收多孔載體的進料口302,軸向另一端設(shè)置有用于輸出多孔載體的出料口303。進料口302和出料口303各自設(shè)置成具有可開合頂蓋和可開合底蓋的料斗。如圖1所示,所述含有催化活性組分的溶液供給單元包括含有催化活性組分的溶液儲罐201以及用于連通含有催化活性組分的溶液儲罐201和中空 容器301中的噴桿304的管線,從而能連續(xù)地向中空容器301中送入含有催化活性組分的溶液。根據(jù)具體需要,可以在管線上設(shè)置泵202以提高輸送的效率,同時提高送入噴桿304中的含有催化活性組分的溶液的壓力,為噴射提供必要的壓力。還可以在管線上設(shè)置閥門,以控制管線的連通與斷開,并調(diào)節(jié)含有催化活性組分的溶液的流量。如圖1所示,所述多孔載體供給單元用于向中空容器301提供多孔載體。所述多孔載體供給單元包括多孔載體儲罐101,所述多孔載體儲罐101的多孔載體出口的位置與中空容器301的進料口302的位置相對應,以將多孔載體通過進料口302送入中空容器301中。如圖1所示,中空容器301內(nèi)布置有噴桿304,噴桿304上設(shè)置有用于將含有催化活性組分的溶液噴射在多孔載體表面的至少一個霧化噴嘴。中空容器301內(nèi)布置有用于進行抽真空的抽真空管線305,抽真空管線305布置為靠近中空容器301中承載多孔載體的內(nèi)壁,且抽真空管線305與中空容器301中承載多孔載體的內(nèi)壁之間的距離足以使抽真空管線305上的抽氣口被填埋在由多孔載體形成的層中。抽真空管線305與真空單元相接。浸漬單元還包括用于支撐中空容器301的基座,中空容器301可轉(zhuǎn)動地連接至基座。中空容器301的軸線相對于水平面為傾斜設(shè)置,使得進料口302位于較高的軸向一端,出料口303位于較低的軸向另一端。通過將中空容器301傾斜設(shè)置,可以實現(xiàn)在浸漬過程中,使多孔載體由進料端向出料端的移動,并最終離開中空容器301,從而能持續(xù)向中空容器301中補充多孔載體,實現(xiàn)連續(xù)化作業(yè)。如圖1所示,可以通過在浸漬單元中設(shè)置傾角調(diào)節(jié)裝置對中空容器301的傾斜角度進行調(diào)節(jié)。所述傾角調(diào)節(jié)裝置一般通過升降部件將中空容器301的軸向一端抬起,并通過調(diào)節(jié)抬起的高度來調(diào)節(jié)中空容器301的傾斜角度。 所述升降部件可以采用各種驅(qū)動方式,優(yōu)選通過液壓方式驅(qū)動升降部件。在一種優(yōu)選的實施方式中,所述傾角調(diào)節(jié)裝置包括底架307以及用于改變底架307相對于水平面的傾斜角度的升降部件308,中空容器301設(shè)置在底架307上。在該優(yōu)選的實施方式中,升降部件308通過調(diào)節(jié)底架的傾斜角度,從而實現(xiàn)對中空容器301的傾斜角度進行調(diào)整。在該優(yōu)選的實施方式中,底架可以設(shè)置在用于支撐中空容器301的基座之上,也可以將用于支撐中空容器301的基座設(shè)置在底架之上。優(yōu)選地,將用于支撐中空容器301的基座設(shè)置在底架之上。具體地,如圖1所示,所述中空容器301通過基座309設(shè)置在所述底架307上,所述基座309固定連接至所述底架307,所述中空容器301可轉(zhuǎn)動地連接至所述基座309。優(yōu)選地,如圖1所示,所述浸漬單元還包括用于驅(qū)動中空容器301轉(zhuǎn)動的驅(qū)動裝置。如圖1所示,所述驅(qū)動裝置通常包括動力產(chǎn)生部件310和傳動部件311,傳動部件311用于將動力產(chǎn)生部件310輸出的動力傳動至中空容器301并使其轉(zhuǎn)動。動力產(chǎn)生部件310可以為各種能夠產(chǎn)生并輸出動力的部件,如電機。傳動部件311可以為各種動力傳遞部件,如傳動齒輪、蝸輪蝸桿、傳動帶和螺旋中的一種或多種的組合??梢愿鶕?jù)預期的浸漬效果對中空容器301的轉(zhuǎn)速進行調(diào)節(jié)。一般地,驅(qū)動裝置使得中空容器301的轉(zhuǎn)速為2轉(zhuǎn)每分鐘至15轉(zhuǎn)每分鐘,優(yōu)選為4轉(zhuǎn)每分鐘至12轉(zhuǎn)每分鐘,更優(yōu)選為5轉(zhuǎn)每分鐘至10轉(zhuǎn)每分鐘。所述真空單元包括真空泵(未示出)、用于連接所述抽真空管線305和所述真空泵的管線(未示出)以及用于調(diào)整真空度的閥門(未示出)。所述真空泵可以是常見的可以抽吸氣體從而產(chǎn)生真空的泵,如機械真空泵。所述真空泵也可以為兩種以上類型的真空泵的組合。通過所述閥門可以對中空容器301中的真空度進行調(diào)節(jié),一般設(shè)置在用于連接抽真空管線305和真空泵的管線上。根據(jù)具體需要,可以在用于連接抽真空管線305和真空泵的管線 上設(shè)置冷阱。通過設(shè)置冷阱可以捕集從中空容器301中抽出的氣體,從而減少進入真空泵的氣體的量,延長真空泵的使用壽命。所述冷阱可以為常見的各種冷阱,沒有特別限定。所述干燥單元用于將來自于浸漬單元的經(jīng)浸漬的多孔載體進行干燥。如圖1所示,所述干燥單元可以包括干燥帶401,用于接收從中空容器301輸出的經(jīng)浸漬的多孔載體,并使該經(jīng)浸漬的多孔載體在干燥帶401承載表面上進行干燥。干燥帶401的材質(zhì)以能夠承受干燥所需的溫度為準。一般地,干燥帶401的材質(zhì)足以承受50-300℃的溫度、優(yōu)選可以承受100-250℃的溫度。根據(jù)需要,可以將干燥帶401布置在一殼體402中,殼體402中設(shè)置有抽真空的管線,這樣能夠在減壓的條件下進行干燥。根據(jù)具體需要,所述浸漬系統(tǒng)還可以包括焙燒裝置,以對經(jīng)干燥的多孔載體進行焙燒。所述焙燒裝置可以為常用的能夠?qū)崿F(xiàn)焙燒功能的裝置,沒有特別限定,如焙燒爐。在根據(jù)本發(fā)明的方法采用上述制備系統(tǒng)實施時,可以采用以下工序進行。將多孔載體裝入多孔載體儲罐101中,將含有催化活性組分的溶液置于含有催化活性組分的溶液儲罐201中。通過升降部件調(diào)節(jié)中空容器301的傾斜角度后,將多孔載體連續(xù)送入中空容器301中。開啟動力產(chǎn)生部件310驅(qū)動中空容器301轉(zhuǎn)動。開啟真空單元中的真空泵以通過抽真空管線305進行抽真空,直至中空容器301內(nèi)部空間的真空度穩(wěn)定。開啟連接含有催化活性組分的溶液儲罐201和噴桿304的管線上的閥門,將含有催化活性組分的溶液儲罐201與噴桿304連通,從而將含有催化活性組分的溶液通過噴桿304上的霧化噴嘴噴射在多孔載體的表面,進而被多孔載體所吸附。在噴射的過程中,持續(xù)開啟真空單元中的真空泵以通過抽真空管線305進行抽真空。在噴射的過程中,中空容器301內(nèi)的多孔載體持續(xù)向出料口303移動,并最終通過出料口303被轉(zhuǎn)移至干燥帶401上,進行干燥;在此過程中,多孔載體儲罐101持續(xù)向中空容器301補充多孔載體,從而實現(xiàn)連續(xù)化作業(yè)。干燥完成后,可選地將經(jīng)干燥的多孔載體送入焙燒裝置中進行焙燒。根據(jù)本發(fā)明的第二個方面,本發(fā)明還提供了由本發(fā)明的方法制備的殼層分布型催化劑。由本發(fā)明的方法制備的殼層分布型催化劑具有較高的殼層率。本領(lǐng)域技術(shù)人員通常也將“殼層分布催化劑”稱為蛋殼型非均勻分布催化劑,簡稱蛋殼型催化劑,其定義為本領(lǐng)域技術(shù)人員公知,例如可以參見(朱洪法編著的《催化劑載體制備及應用技術(shù)》書中的第199-200頁(石油工業(yè)出版社2002年5月第1版)中的定義。本發(fā)明中,殼層率通過掃描電子顯微鏡-能譜分析(即SEM-EDX,ScanningElectronMicroscope-EnergyDispersiveSpectrometry)方法測得。具體方法包括:隨機選取30個催化劑顆粒并將催化劑顆粒沿徑向切開,用SEM觀測催化劑顆粒的截面粒徑,之后用EDX沿徑向截面掃描得到催化活性組分的徑向分布。由于掃描電鏡-X射線能譜(SEM-EDX)表征結(jié)果中沿載體徑向每一點的記數(shù)率與該點元素含量相互對應,雖然記數(shù)率的大小可能并不代表該點元素的真實含量,但記數(shù)率的大小能夠反映該點元素含量高低。因此,為了表示催化活性組分和催化助劑沿載體徑向的分布規(guī)律引入分布因子σ,σ為催化活性組分和催化助劑在催化劑中心處的濃度與除中心外的某一位置處的濃度之比。一般而言,所述“蛋殼型催化劑”是指:催化劑的分布因子σ為0≤σ<0.95的一類催化劑,其中,某一位置上濃度為除中心點之外的某點附近(位置偏差≤20nm)20個數(shù)值點記數(shù)率的平均值;中心處濃度為中心點附近(位置偏差≤20nm)20個數(shù)值點記數(shù)率的平均值。本發(fā)明所述的殼層分布催化劑指的是催化劑中的活性金屬組分主要分布在殼層。將測試的30個催化劑顆粒中為殼層分布 型催化劑的顆粒所占的百分比稱為殼層率。其中,殼層厚度是指催化活性組分和催化助劑的分布因子滿足0≤σ<0.95的部分的厚度。根據(jù)本發(fā)明的催化劑特別適于作為受內(nèi)擴散控制的反應的催化劑,如費托合成反應的催化劑。由此,根據(jù)本發(fā)明的第三個方面,本發(fā)明還提供了一種費托合成方法,該方法包括在費托合成反應條件下,將合成氣與催化劑接觸,其中,所述催化劑為由本發(fā)明的方法制備的對費托合成反應具有催化作用的殼層分布型催化劑。根據(jù)本發(fā)明提供的催化劑,在使用前,優(yōu)選在氫氣存在下,將氧化態(tài)的活性金屬組分進行還原活化。所述還原活化的條件可以包括:還原溫度可以為200℃至1000℃,優(yōu)選為200℃至800℃,還原時間可以為1-96小時,優(yōu)選為2-24小時,所述還原活化可以在純氫中進行,也可以在氫和惰性氣體的混合氣體中進行,如在氫氣與氮氣的混合氣中進行,氫氣壓力可以為0.1-4MPa,優(yōu)選為0.1-2MPa,所述惰性氣體是指在本發(fā)明的條件下,不參與化學反應的氣體,如氮氣和零族元素氣體。根據(jù)本發(fā)明的費托合成方法,對于費托反應的具體反應條件沒有特別限定,可以在常規(guī)條件下進行。具體地,溫度可以為170-350℃,優(yōu)選為180-300℃;總壓力可以為1-20MPa,優(yōu)選為1.5-15MPa;合成氣的氣時體積空速可以為1000-20000h-1,優(yōu)選為2000-18000h-1。以下結(jié)合實施例詳細說明本發(fā)明,但并不因此限制本發(fā)明。以下實施例和對比例中,采用X-射線熒光光譜法測定制備的催化劑的組成。以下實施例和對比例中,通過掃描電子顯微鏡-能譜分析(即,SEM-EDX,ScanningElectronMicroscope-EnergyDispersiveSpectrometry)方法確定催化活性組分沿多孔載體徑向的分布,并計算殼層率。以下實施例和對比例中,采用馬爾文粒度分析儀測定霧化液滴的大小,為體積平均粒徑。以下實施例和對比例中,采用以下方法確定噴涂過程中,中空容器內(nèi)由溶劑產(chǎn)生的分壓采用以下方法測定:在裝填多孔載體后且噴涂開始前,對中空容器進行抽真空直至中空容器內(nèi)的相對真空度穩(wěn)定,以該相對真空度作為基準相對真空度,將噴涂過程中測定的相對真空度與基準相對真空度之間的差值作為由溶劑產(chǎn)生的分壓。以下實施例中,采用圖1所示的制備系統(tǒng)制備催化劑,其中,中空容器301為筒形,其軸向長為5米,徑向內(nèi)徑為1.2米。實施例1-12用于說明本發(fā)明。實施例11、將200kg由1.6mm孔板擠出的蝶形γ-氧化鋁顆粒(顆粒長度為2-4毫米,吸水率為0.8毫升/克)作為多孔載體并放入多孔載體儲罐101中。2、將硝酸鈷溶解于水中,配制成浸漬液(以CoO計,硝酸鈷的濃度為330克/升)并將其置于浸漬液儲罐201中。3、將多孔載體送入中空容器301中,同時轉(zhuǎn)動中空容器301(中空容器301的內(nèi)壁設(shè)置有揚料板306,揚料板306的徑向截面為梯形,x=2.4y,β為60°,z為0.12R;中空容器301的軸線相對于水平面的傾斜角度為2°;轉(zhuǎn)動速度為5轉(zhuǎn)/分鐘),同時啟動真空泵對中空容器301進行抽真空(其中,在中空容器301中沿轉(zhuǎn)軸方向,等間隔布置3根抽真空管線305,每根抽真空管線305上的抽氣口均填埋在由多孔載體形成的層中并且抽氣口為沿抽真空管線305等間隔分布,抽氣口朝向承載多孔載體的內(nèi)壁,即抽氣口朝下),將中空容器301內(nèi)的相對真空度穩(wěn)定為-60kPa(即,基準相對真空度)。然后,維持中空容器301的轉(zhuǎn)動條件不變,伴隨抽真空,向中空容器301 中送入浸漬液,將浸漬液通過霧化噴嘴以霧化液滴的形式噴涂在多孔載體表面。其中,浸漬液的噴入量VL與多孔載體的總孔體積VC的比值滿足VL/VC=0.23,霧化液滴的大小為200μm;中空容器301內(nèi)的溫度為30℃,噴涂過程中,調(diào)整抽真空的條件使得由水產(chǎn)生的分壓最高為10kPa。4、在浸漬過程中,經(jīng)浸漬的多孔載體被連續(xù)送入干燥帶401上進行干燥,其中,干燥在常壓下進行,溫度為160℃,浸漬后樣品在干燥帶401上的停留時間為3小時。同時,連續(xù)向中空容器301中送入新鮮多孔載體。5、將干燥后的樣品在460℃的溫度下,焙燒5小時,從而得到催化劑。該催化劑的組成以及殼層率在表1中列出,沿多孔載體的徑向截面由外層至芯部,鈷元素的相對百分含量在表2中列出。對比例1采用與實施例1相同的方法制備催化劑,不同的是,步驟3中,噴涂的過程中,不開啟真空泵,即在噴涂的過程中,不進行抽真空。制備的催化劑的組成以及殼層率在表1中列出。對比例2采用與實施例1相同的方法制備催化劑,不同的是,中空容器301中不設(shè)置抽真空管線305,其中,用于穿過抽真空管線305的位置為一開口,噴涂過程中,該開口為敞開。制備的催化劑的組成以及殼層率在表1中列出。對比例3采用與實施例1相同的方法制備催化劑,不同的是,抽真空管線305上的抽氣口沒有填埋在多孔載體形成的層中。制備的催化劑的組成以及殼層率在表1中列出。實施例2采用與實施例1相同的方法制備催化劑,不同的是,步驟3中,噴涂過程中,不調(diào)整抽真空的條件,由水產(chǎn)生的分壓最高為30kPa。制備的催化劑的組成以及殼層率在表1中列出,沿多孔載體的徑向截面由外層至芯部,鈷元素的相對百分含量在表2中列出。實施例3采用與實施例1相同的方法制備催化劑,不同的是,步驟4中,干燥的溫度為120℃。制備的催化劑的組成以及殼層率在表1中列出,沿多孔載體的徑向截面由外層至芯部,鈷元素的相對百分含量在表2中列出。實施例4采用與實施例1相同的方法制備催化劑,不同的是,步驟4中,干燥在減壓的條件下進行,壓力(表壓)為-45kPa,溫度為160℃。制備的催化劑的組成以及殼層率在表1中列出,沿多孔載體的徑向截面由外層至芯部,鈷元素的相對百分含量在表2中列出。實施例51、將200kg由1.6mm孔板擠出的蝶形γ-氧化鋁顆粒(顆粒長度為2-4毫米,吸水率為1.0毫升/克)作為多孔載體并放入多孔載體儲罐101中。2、將鉬酸銨、偏鎢酸銨、硝酸鎳和磷酸溶解于水中,配制成浸漬液(MoO3的濃度為225克/升,WO3的濃度為99克/升,NiO的濃度為50克/升,磷元 素的濃度為39克/升)并將其置于浸漬液儲罐201中。3、將多孔載體送入中空容器301中,同時轉(zhuǎn)動中空容器301(中空容器301的內(nèi)壁設(shè)置有揚料板306,揚料板306的徑向截面為梯形,x=2y,β為60°,z為0.12R;中空容器301的軸線相對于水平面的傾斜角度為5°;轉(zhuǎn)動速度為8轉(zhuǎn)/分鐘),同時啟動真空泵對中空容器301進行抽真空(其中,在中空容器301中沿轉(zhuǎn)軸方向,等間隔布置3根抽真空管線305,每根抽真空管線305上的抽氣口填埋在由多孔載體形成的層中并且抽氣口為沿抽真空管線305等間隔分布,抽氣口朝向承載多孔載體的內(nèi)壁,即抽氣口朝下),將中空容器301內(nèi)的相對真空度穩(wěn)定為-70kPa(即,基準相對真空度)。然后,維持中空容器301的轉(zhuǎn)動條件不變,伴隨抽真空,向中空容器301中送入浸漬液,將浸漬液通過霧化噴嘴以霧化液滴的形式噴涂在多孔載體表面。其中,浸漬液的噴入量VL與多孔載體的總孔體積VC的比值滿足VL/VC=0.5,霧化液滴的大小為120μm;中空容器301內(nèi)的溫度為50℃,噴涂過程中,調(diào)整抽真空的條件使得由水產(chǎn)生的分壓最高為15kPa。4、在浸漬過程中,經(jīng)浸漬的多孔載體被連續(xù)送入干燥帶401上進行干燥,其中,干燥在常壓下進行,溫度為140℃,多孔載體在干燥帶401上的停留時間為5小時。同時,連續(xù)向中空容器301中送入新鮮多孔載體。5、將干燥后樣品在480℃的溫度下,焙燒4小時,從而得到催化劑。該催化劑的組成以及殼層率在表1中列出,沿多孔載體的徑向截面由外層至芯部,鉬元素的相對百分含量在表2中列出。對比例4采用與實施例5相同的方法制備催化劑,不同的是,噴涂的過程中,不開啟真空泵,即在噴涂的過程中,不進行抽真空。制備的催化劑的組成以及殼層率在表1中列出。對比例5采用與實施例5相同的方法制備催化劑,不同的是,抽真空管線305上的抽氣口沒有填埋在多孔載體形成的層中。制備的催化劑的組成以及殼層率在表1中列出。實施例61、將200kg由1.6mm孔板擠出的蝶形γ-氧化鋁顆粒(顆粒長度為2-4毫米,吸水率為1.0毫升/克)作為多孔載體并放入多孔載體儲罐101中。2、將偏鎢酸銨和硝酸鎳溶解于水中,配制成浸漬液(WO3的濃度為402克/升,NiO的濃度為25克/升)并將其置于浸漬液儲罐201中。3、將多孔載體送入中空容器301中,同時轉(zhuǎn)動中空容器301(中空容器301的內(nèi)壁設(shè)置有揚料板306,揚料板306的徑向截面為梯形,x=1.5y,β為75°,z為0.10R;中空容器301的軸線相對于水平面的傾斜角度為8°;轉(zhuǎn)動速度為5轉(zhuǎn)/分鐘),同時啟動真空泵對中空容器301進行抽真空(其中,在中空容器301中沿轉(zhuǎn)軸方向,等間隔布置3根抽真空管線305,每根抽真空管線305上的抽氣口填埋在由多孔載體形成的層中并且抽氣口為沿抽真空管線305等間隔分布,抽氣口朝向承載多孔載體的內(nèi)壁,即抽氣口朝下),將中空容器301內(nèi)的相對真空度穩(wěn)定為-80kPa(即,基準相對真空度)。然后,維持中空容器301的轉(zhuǎn)動條件不變,伴隨抽真空,向中空容器301中送入浸漬液,將浸漬液通過霧化噴嘴以霧化液滴的形式噴涂在多孔載體表面。其中,浸漬液的噴入量VL與多孔載體的總孔體積VC的比值滿足VL/VC=0.3,霧化液滴的大小為200μm;中空容器301內(nèi)的溫度為45℃,噴涂過程中,調(diào)整抽真空的條件使得由水產(chǎn)生的分壓最高為10kPa。4、在浸漬過程中,經(jīng)浸漬的多孔載體被連續(xù)送入干燥帶401上進行干燥,其中,干燥在減壓下進行,壓力(為表壓)為-8kPa,溫度為120℃,多 孔載體在干燥帶401上的停留時間為2小時。同時,連續(xù)向中空容器301中送入新鮮多孔載體。5、將經(jīng)干燥的多孔載體在500℃的溫度下,焙燒2.5小時,從而得到催化劑。該催化劑的組成以及殼層率在表1中列出,沿多孔載體的徑向截面由外層至芯部,鎢元素的相對百分含量在表2中列出。對比例6采用與實施例6相同的方法制備催化劑,不同的是,噴涂的過程中,不開啟真空泵,即在噴涂的過程中,不進行抽真空。制備的催化劑的組成以及殼層率在表1中列出。對比例7采用與實施例6相同的方法制備催化劑,不同的是,抽真空管線305上的抽氣口沒有填埋在多孔載體形成的層中。制備的催化劑的組成以及殼層率在表1中列出。實施例7采用與實施例6相同的方法制備催化劑,不同的是,步驟4中,干燥的溫度為80℃。制備的催化劑的組成以及殼層率在表1中列出,沿多孔載體的徑向截面由外層至芯部,鎢元素的相對百分含量在表2中列出。實施例8采用與實施例6相同的方法制備催化劑,不同的是,步驟3中,抽氣口為背向承載多孔載體的內(nèi)壁(即,與浸漬液的噴射方向相對,即抽氣口朝上)。制備的催化劑的組成以及殼層率在表1中列出,沿多孔載體的徑向截面由外層至芯部,鎢元素的相對百分含量在表2中列出。表1編號CoO,wt%WO3,wt%MoO3,wt%NiO,wt%P,wt%殼層率,%實施例111.4////98對比例111.6////68對比例211.8////70對比例311.0////77實施例211.8////88實施例311.7////91實施例411.5////96實施例5/4.09.62.11.697對比例4/4.39.42.21.569對比例5/3.98.71.41.277實施例6/13.4/0.86/98對比例6/13.5/0.83/72對比例7/13.0/0.81/79實施例7/13.4/0.83/90實施例8/13.2/0.83/92從表1的結(jié)果可以看出,由采用本發(fā)明的方法制備的催化劑具有較高的殼層率,從而能重復穩(wěn)定地制備殼層分布型催化劑,使得制備的催化劑具有穩(wěn)定的催化活性。將實施例1與對比例3、實施例5與對比例5、實施例6與對比例7進行比較可以看出,如果抽真空管線的抽氣口沒有填埋在由多孔載體形成的層中,制備的催化劑的殼層率仍然比較低,其原因可能在于吸附過程中產(chǎn)生的溶劑蒸氣可能被包埋在由多孔載體形成的層中,無法被及時抽出,并且即使被抽吸出來,蒸氣也需要穿過由多孔載體形成的層,從而無法及時消除由此產(chǎn)生的負面影響。表2*:沿催化劑的徑向截面,用EDX沿徑向截面從最外層向芯部掃描,等間隔取5個點分別測量各點處催化活性組分的濃度,得到各催化活性組分的濃度與該點處鋁元素濃度的比值。實施例9-12采用下述方法測試由實施例1-4制得的催化劑的性能。測試過程在固定床費托合成反應器中進行,催化劑用量為5克。催化劑在使用前進行還原。還原在常壓下進行,其它條件為:氫氣流量為1000NL/(g-cat·h),以4℃/min的升溫速率升溫至400℃,保持5h。費托合成反應溫度為220℃,H2/CO比為2,壓力為2.5MPa,氣體時空速率(GHSV)為2000h-1。結(jié)果在表3中列出。對比例9-11采用與實施例9-12相同的方法測試由對比例1-3制備的催化劑的性能。結(jié)果在表3中列出。表3表3中,XCO表示CO的轉(zhuǎn)化率,和分別表示C5以上(含C5)烴類的選擇性和CH4的選擇性。具體定義見下面的表達式:XCO=V1×c1,CO-V2×c2,COV1×c1,CO]]>Sc5+=ncon-nc4--nCO2ncon]]>SCH4=nCH4ncon]]>其中,V1和V2分別表示在標準狀況下,某時間段內(nèi)進入反應系統(tǒng)的原料氣的體積和流出反應系統(tǒng)的尾氣體積;c1和c2分別表示原料氣和尾氣中對應物質(zhì)的含量。ncon為某時間段內(nèi)通過反應床層參與反應的CO的摩爾數(shù),為轉(zhuǎn)化成CO2的CO的摩爾數(shù),為轉(zhuǎn)化成CH4的CO的摩爾數(shù),為轉(zhuǎn)化成CH4、C2烴、C3烴、和C4烴的CO的摩爾數(shù)。從表3的結(jié)果可以看出,由本發(fā)明的方法制得的催化劑對C5+烴類具有更高的選擇性,對甲烷的選擇性較低,同時還能獲得較高的CO轉(zhuǎn)化率。當前第1頁1 2 3