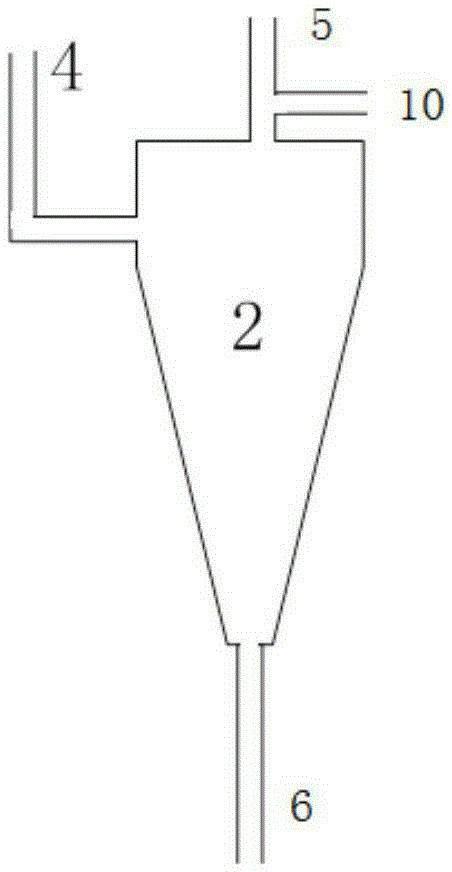
本發(fā)明涉及石油煉制領(lǐng)域,具體地,涉及一種漿態(tài)床加氫裂化方法。
背景技術(shù):
:進入21世紀以來,石油產(chǎn)品消費量隨著世界經(jīng)濟規(guī)模的擴張而不斷增大。但是受原油資源儲量的限制,未來石油資源供應(yīng)緊張是必然的趨勢。為緩解這一趨勢的發(fā)展,超重稠油、油砂及天然瀝青和頁巖油等非常規(guī)石油資源的開采受到廣泛的重視。在全球的原油供應(yīng)中,高硫、高金屬、高殘?zhí)康牧淤|(zhì)原油比例將逐年上升。因此,重質(zhì)油的高效加工和充分利用已成為全球煉油工業(yè)關(guān)注的焦點。重油的輕質(zhì)化技術(shù)可以分為加氫路線和脫碳路線兩大類。近年來,隨著環(huán)保法規(guī)的日益嚴格和產(chǎn)品質(zhì)量標準的不斷升級,加氫路線產(chǎn)品在雜原子含量、苯及烯烴含量及穩(wěn)定性等方面的優(yōu)勢日趨明顯。另外,加氫工藝在資源利用效率和節(jié)能減排等方面也具有脫碳工藝不可比擬的優(yōu)點。因此,劣質(zhì)渣油加氫工藝及相關(guān)組合工藝成為近年來煉油科技工作者們工作的重點之一。渣油加氫技術(shù)主要有固定床、移動床、沸騰床及漿態(tài)床等四類,其中固定床渣油加氫因工藝技術(shù)相對簡單、投資相對較低而得到最廣泛應(yīng)用。但是,由于受到催化劑使用周期的限制,固定床渣油加氫技術(shù)對原料性質(zhì)有嚴格的限制,一般認為,固定床技術(shù)適用于處理殘?zhí)恐敌∮?5%、金屬(Ni+V)含量小于200μg/g的原料。雖然相對于固定床有較寬的原料適應(yīng)范圍,但是因移動床技術(shù)設(shè)備復(fù)雜,投資和運營成本較高,而使其大規(guī)模工業(yè)應(yīng)用受到一定限制。沸騰床和漿態(tài)床技術(shù)能夠?qū)崿F(xiàn)催化劑的在線置換,而具有加工更為劣質(zhì)原料的優(yōu)勢,在原油劣質(zhì)化趨勢不斷加劇的今天而備受青睞。沸騰床是目前使用較多的渣油加氫的設(shè)備。正常操作時,催化劑懸浮于反應(yīng)器內(nèi),形成膨脹的催化劑床層。床層液速小于催化劑顆粒的帶出速度。氣相則從反應(yīng)器底部的氣體分布器進入床層,以氣泡形式通過床層,流出反應(yīng)器,因床層貌似沸騰而得名。此外,通過反應(yīng)器內(nèi)催化劑的在線置換,排出積累的焦炭和失活催化劑,并維持反應(yīng)器內(nèi)催化劑活性穩(wěn)定,進而達到拓展原料適用性,提高操作苛刻度,延長操作周期的目的。雖然這種床層較固定床高效,但是在催化劑運用方面還有許多可改進的地方,其中之一便是催化劑顆粒較大,單位重量催化劑的表面積較低,利用率不高;另一方面,催化劑在反應(yīng)器內(nèi)呈“沸騰”狀態(tài),催化劑顆粒間相互碰撞和摩擦的機率增大,容易出現(xiàn)磨損和催化劑破裂,增大了催化劑損耗,并影響下游裝置的操作。CN1458234A公開了一種渣油加工方法及設(shè)備,并具體公開了采用在一個反應(yīng)器內(nèi)設(shè)置多段不同功能的沸騰床以加工渣油,其催化劑基質(zhì)為氧化鋁,活性組分為鉬和鎳,催化劑粒徑在50-400μm之間。催化劑粒徑減小后,帶出速度隨之降低,為了維持沸騰床的操作模式,床層中的液相線速必須下降,否則催化劑被帶出,影響下游操作。漿態(tài)床加氫裂化技術(shù)相對于沸騰床技術(shù),具有更廣的原料適用性,可以加工世界上所有的劣質(zhì)重油,并且催化劑成本更為低廉,反應(yīng)設(shè)備簡單,投資較低。使用漿態(tài)床處理原料油的共同特點是催化劑與原料油混合后一起進入反應(yīng)器,反應(yīng)一定時間后,油、劑又一起從反應(yīng)器流出,并通過未轉(zhuǎn)化油攜帶催化劑返回反應(yīng)器的形式,提高催化劑使用效率并提高原料轉(zhuǎn)化率。但這種操作模式下,原料單程轉(zhuǎn)化率較低,多次循環(huán)后催化劑活性難以維持,考慮到催化劑使用成本,使得反應(yīng)器中的催化劑含量處于較低水平,現(xiàn)有技術(shù)的催化劑添加量一般為0.1-5%(以活性金屬計,占原料油的重量)。目前,漿態(tài)床渣油加氫工藝所使用的催化劑的功能比較單一,活性組元僅能提供加氫的功能,無法提供足夠的裂化活性促進渣油油中瀝青質(zhì)等大分子的裂化。 CN1219569A公開了一種活性金屬無機鹽為前驅(qū)物的水溶性漿態(tài)床催化劑催化劑,活性成分為Mo、Ni、Co、W等金屬氧化物或無機鹽。此類催化劑除了具有功能單一的缺點外,添加進入反應(yīng)體系時需要進行高速剪切以促進分散,導(dǎo)致整個工藝過程能耗增加。CN102049252A公開了一種將活性金屬負載到活性炭上的懸浮床催化劑及制備方法。該催化劑的活性炭載體強度較低,在反應(yīng)器內(nèi)或者后續(xù)分離過程中,容易磨損或粉化,影響下游操作。上述目前的渣油漿態(tài)床反應(yīng)體系中,瀝青質(zhì)等大分子的裂化主要依靠高溫,發(fā)生熱裂化反應(yīng),導(dǎo)致較高的焦炭和氣體產(chǎn)率。因此,為了克服現(xiàn)有技術(shù)的上述缺陷,本領(lǐng)域內(nèi)亟需找到一種新的能夠在高含量的催化劑的存在下加工重質(zhì)原料油的加氫裂化方法。技術(shù)實現(xiàn)要素:本發(fā)明的目的是克服采用現(xiàn)有技術(shù)的方法加工原料油時存在的反應(yīng)器中催化劑含量低以及原料油轉(zhuǎn)化率低的缺陷,提供一種新的能夠在高含量的催化劑的存在下加工重質(zhì)原料油的漿態(tài)床加氫裂化方法。為了實現(xiàn)上述目的,本發(fā)明提供一種漿態(tài)床加氫裂化方法,該方法在設(shè)置旋液分離器的漿態(tài)床反應(yīng)器中實施,該方法包括:將原料油、氫氣和加氫催化劑引入漿態(tài)床反應(yīng)器中進行加氫反應(yīng),并且將所得到的反應(yīng)物料通過旋液分離器進行分離,分離所得的富固含量組分從所述旋液分離器下部的底流管引出以循環(huán)回所述漿態(tài)床反應(yīng)器的內(nèi)腔中;分離所得的貧固含量組分從產(chǎn)物油出口引出至所述漿態(tài)床反應(yīng)器之外;分離所得的氣相從氣相出口引出至所述旋液分離器之外。本發(fā)明提供的上述漿態(tài)床加氫裂化方法能夠在高含量的催化劑的存在下加工重質(zhì)原料油。具體地,本發(fā)明通過提高漿態(tài)床反應(yīng)器內(nèi)加氫催化劑藏量、強化加氫反應(yīng)過程達到促進瀝青質(zhì)等大分子轉(zhuǎn)化的目的,另一方面,通 過優(yōu)化反應(yīng)器的結(jié)構(gòu)和形式,改變反應(yīng)器液體物料的運動方式,提高液體運動速度,防止焦炭生成及沉積,延長操作周期,提高原料適用性。而且,應(yīng)用本發(fā)明的方法進行漿態(tài)床加氫裂化方法時,能夠強化熱、質(zhì)傳遞效果,提高重質(zhì)油和/或高芳烴油的轉(zhuǎn)化率。另外,優(yōu)選情況下,本發(fā)明的方法還能夠使用具有強化加氫處理能力成型微球催化劑,克服現(xiàn)有技術(shù)的催化劑活性難以維持、功能單一的缺陷。本發(fā)明的其它特征和優(yōu)點將在隨后的具體實施方式部分予以詳細說明。附圖說明附圖是用來提供對本發(fā)明的進一步理解,并且構(gòu)成說明書的一部分,與下面的具體實施方式一起用于解釋本發(fā)明,但并不構(gòu)成對本發(fā)明的限制。在附圖中:圖1是本發(fā)明的一種優(yōu)選實施方式的旋液分離器的結(jié)構(gòu)示意圖。圖2是本發(fā)明第一種優(yōu)選實施方式的反應(yīng)器結(jié)構(gòu)示意圖。圖3是本發(fā)明的第二種優(yōu)選實施方式的反應(yīng)器結(jié)構(gòu)示意圖。附圖標記說明1、反應(yīng)器殼體2、旋液分離器內(nèi)腔3、套筒4、旋液分離器入口5、氣相出口6、底流管7、氣體分布器8、反應(yīng)器內(nèi)腔9、出氣口10、產(chǎn)物油出口11、進氣口12、卸劑口13、加劑口14、原料油入口具體實施方式以下對本發(fā)明的具體實施方式進行詳細說明。應(yīng)當理解的是,此處所描述的具體實施方式僅用于說明和解釋本發(fā)明,并不用于限制本發(fā)明。本發(fā)明提供了一種漿態(tài)床加氫裂化方法,該方法在設(shè)置旋液分離器的漿態(tài)床反應(yīng)器中實施,該方法包括:將原料油、氫氣和加氫催化劑引入漿態(tài)床反應(yīng)器中進行加氫反應(yīng),并且將所得到的反應(yīng)物料通過旋液分離器進行分離,分離所得的富固含量組分從所述旋液分離器下部的底流管引出以循環(huán)回所述漿態(tài)床反應(yīng)器的內(nèi)腔中;分離所得的貧固含量組分從產(chǎn)物油出口引出至所述漿態(tài)床反應(yīng)器之外;分離所得的氣相從氣相出口引出至所述旋液分離器之外。所述漿態(tài)床加氫裂化方法適應(yīng)于本領(lǐng)域內(nèi)常規(guī)的需要進行加氫裂化的原料油。優(yōu)選地,所述原料油為重質(zhì)油和/或高芳烴油;所述高芳烴油的餾程為300-550℃,且芳烴含量大于80重量%;所述重質(zhì)油包括減壓渣油、重質(zhì)原油、超重質(zhì)原油、油砂、天然瀝青、頁巖油和煤焦油中的至少一種。更加優(yōu)選所述原料油為重質(zhì)油和高芳烴油,所述重質(zhì)油和高芳烴油的重量比為0.1:1至1.1:1。本發(fā)明的重質(zhì)油的特點是,相對密度較大,一般大于1.0,膠質(zhì)及瀝青質(zhì)等大分子、硫氮雜原子及金屬含量高。優(yōu)選在將所述高芳烴油引入漿態(tài)床反應(yīng)器中之前,先對所述高芳烴油進行加氫處理,使得加氫后的原料油中的氫碳原子比在1.3-1.6:1之間。優(yōu)選情況下,所述加氫催化劑中含有載體和活性金屬元素,所述載體包括氧化硅-氧化鋁和氧化鋁,所述活性金屬元素包括鐵、鈣和鉬,所述催化劑為微球型,且平均粒徑為20-200μm;優(yōu)選為50-120μm;更優(yōu)選為60-100μm。優(yōu)選以所述催化劑的總重量計,所述活性金屬元素以氧化物計的含量為10-40重量%。更加優(yōu)選以所述加氫催化劑的總重量計,鈣和鉬以氧化物計的含量分別為0.1-1重量%和5-10重量%。在本發(fā)明中,所述反應(yīng)物料并不特指僅含有原料油、加氫催化劑和氫氣的物料,本文中的反應(yīng)物料泛指參與加氫反應(yīng)過程的所有物料,包括固相、氣相和液相物料,也包括反應(yīng)物、生成物等。優(yōu)選氫氣從位于漿態(tài)床反應(yīng)器的殼體底部的進氣口進入漿態(tài)床反應(yīng)器的內(nèi)腔中,引起反應(yīng)物料在漿態(tài)床反應(yīng)器的內(nèi)腔中進行相對運動從而有利于漿態(tài)床反應(yīng)器中反應(yīng)的進行。優(yōu)選所述旋液分離器包括旋液分離器入口、旋液分離器內(nèi)腔、氣相出口、產(chǎn)物油出口和底流管。物料通過旋液分離器入口進入旋液分離器內(nèi)腔中利用自身的離心力進行分離,分離得到氣相物從所述氣相出口引出至所述旋液分離器之外,分離得到固含量較小的組分從位于旋液分離器上部的產(chǎn)物油出口引出至所述旋液分離器之外,分離得到的固含量較大的組分從位于旋液分離器下部的底流管引出至所述旋液分離器之外。優(yōu)選地,先將所述原料油進行加熱預(yù)處理后再引入所述漿態(tài)床反應(yīng)器中進行加氫反應(yīng)。所述加熱預(yù)處理是為了使得進入所述漿態(tài)床反應(yīng)器中的反應(yīng)物料能夠更加高效地進行加氫反應(yīng)。優(yōu)選所述加熱預(yù)處理的條件包括溫度為350-500℃;更優(yōu)選為360-460℃。也可以先將部分氫氣預(yù)熱后引入所述漿態(tài)床反應(yīng)器中,氫氣預(yù)熱溫度在360-550℃之間,優(yōu)選為370-500℃。優(yōu)選情況下,所述漿態(tài)床反應(yīng)器中進一步設(shè)置有使得所述反應(yīng)物料在所述漿態(tài)床反應(yīng)器的內(nèi)腔中進行內(nèi)循環(huán)的套筒,所述套筒的下部通過內(nèi)徑小于所述套筒內(nèi)徑且伸入所述套筒內(nèi)部的導(dǎo)管與所述漿態(tài)床反應(yīng)器的殼體上的進氣口連通,所述氫氣通過所述進氣口依次引入至所述導(dǎo)管和所述套筒中。通過設(shè)置所述套筒,并且氫氣從所述進氣口進入所述套筒內(nèi),使得套筒內(nèi)的 反應(yīng)物料中的氣含量明顯比套筒外的反應(yīng)物料中的氣含量要高,從而推動套筒內(nèi)的反應(yīng)物料向上運動,而套筒外的反應(yīng)物料相對向下運動,如此在漿態(tài)床反應(yīng)器的內(nèi)腔中形成內(nèi)循環(huán),促進了反應(yīng)物料中氣、固、液三相之間的相互反應(yīng),從而能夠提高反應(yīng)效率。要求引導(dǎo)氫氣的所述導(dǎo)管的內(nèi)徑小于所述套筒的內(nèi)徑是為了使得所述漿態(tài)床反應(yīng)器的內(nèi)腔中的反應(yīng)物料能夠從所述套筒的底部進入所述套筒中。因此,本領(lǐng)域技術(shù)人員能夠據(jù)此確定所述導(dǎo)管和所述套筒的內(nèi)徑的比值。所述套筒可以為一根或至少兩根。優(yōu)選套筒為至少兩根,至少兩根的所述套筒下部的所述導(dǎo)管與所述進氣口之間設(shè)置有氣體分布器;所述氫氣通過所述進氣口依次引入至所述氣體分布器、所述導(dǎo)管和所述套筒中。所述氣體分布器的設(shè)置是為了能夠使得進入所述漿態(tài)床反應(yīng)器的內(nèi)腔中的氫氣能夠更加均勻地分布,氫氣經(jīng)氣體分布器平均分配到每個內(nèi)置的套筒底部,在此處的氣體分布器將氫氣分散成小氣泡,每個套筒內(nèi)的氣泡均向上移動,使套筒內(nèi)的氣含量大于套筒外的氣含量。憑借套筒內(nèi)外流體密度的差異,在一定的垂直距離范圍內(nèi)形成壓差,該壓差推動套筒外流體向下流動,在套筒內(nèi)流體向上流動,如此形成內(nèi)循環(huán)。從而有利于漿態(tài)床反應(yīng)器的內(nèi)腔中反應(yīng)的高效進行。優(yōu)選所述貧固含量組分中的固含量不高于0.5重量%。優(yōu)選所述富固含量組分中的固含量為5-50重量%;更加優(yōu)選所述富固含量組分中的固含量為10-40重量%。優(yōu)選地,所述套筒的長度為所述漿態(tài)床反應(yīng)器的內(nèi)腔的長度的2/5至4/5。所述漿態(tài)床反應(yīng)器的內(nèi)腔的長度與所述漿態(tài)床反應(yīng)器的內(nèi)腔的內(nèi)徑之比可以為5-20:1;優(yōu)選所述漿態(tài)床反應(yīng)器的內(nèi)腔的長度與所述漿態(tài)床反應(yīng)器的內(nèi)腔的內(nèi)徑之 比為8-15:1。優(yōu)選地,所述漿態(tài)床反應(yīng)器的內(nèi)腔的內(nèi)徑為50-6000mm;進一步優(yōu)選所述漿態(tài)床反應(yīng)器的內(nèi)腔的內(nèi)徑為300-5000mm。優(yōu)選地,所述套筒的內(nèi)徑為所述漿態(tài)床反應(yīng)器的內(nèi)腔的內(nèi)徑的1/100至3/4。優(yōu)選地,所述導(dǎo)管伸入所述套筒內(nèi)部的長度為所述套筒的長度的1/1000至1/10。根據(jù)本發(fā)明的一種優(yōu)選的具體實施方式,本發(fā)明所述的將所述反應(yīng)物料通過旋液分離器中進行分離在圖1所示的旋液分離器中進行,具體地:所述旋液分離器包括旋液分離器入口4、旋液分離器內(nèi)腔2、氣相出口5、產(chǎn)物油出口10和底流管6。物料通過旋液分離器入口4進入旋液分離器內(nèi)腔2中利用自身的離心力進行分離,分離得到氣相物從所述氣相出口5引出至所述旋液分離器之外,分離得到固含量較小的組分從位于旋液分離器上部的產(chǎn)物油出口10引出至所述旋液分離器之外,分離得到的固含量較大的組分從位于旋液分離器下部的底流管6引出至所述旋液分離器之外。所述旋液分離器可以為設(shè)置在所述漿態(tài)床反應(yīng)器的內(nèi)腔中的一級或至少兩級旋液分離器。或者所述旋液分離器為設(shè)置在所述漿態(tài)床反應(yīng)器的內(nèi)腔之外的一級旋液分離器。優(yōu)選地,所述旋液分離器為設(shè)置在所述漿態(tài)床反應(yīng)器的內(nèi)腔中的一級或至少兩級旋液分離器。所述反應(yīng)物料從旋液分離器入口沿切線方向進入,控制所述氫氣進入所述漿態(tài)床反應(yīng)器中的流量,使得所述反應(yīng)物料在經(jīng)過所述旋液分離器的入口時的速率為5-15m/s;優(yōu)選控制所述氫氣進入所述漿態(tài)床反應(yīng)器中的流量,使得所述反應(yīng)物料在經(jīng)過所述旋液分離器的入口時的速率 為7-12m/s。在旋液分離器內(nèi)腔中形成旋轉(zhuǎn)運動,依靠離心力對所述反應(yīng)物料進行分離。漿態(tài)床反應(yīng)器內(nèi)置旋液分離器時,優(yōu)選所述旋液分離器入口為喇叭形,在反應(yīng)器液面處或液面下方,反應(yīng)物料從旋液分離器入口沿旋液分離器圓周的切線方向進入。所述至少兩級的所述旋液分離器中的前一級的旋液分離器中分離得到的貧固含量組分進入相鄰的后一級旋液分離器中,分離得到的富固含量組分從底流管返回至所述漿態(tài)床反應(yīng)器的內(nèi)腔中,以及最后一級旋液分離器中分離得到的貧固含量組分從所述產(chǎn)物油出口引出至所述漿態(tài)床反應(yīng)器之外。所述漿態(tài)床反應(yīng)器的內(nèi)腔是由漿態(tài)床反應(yīng)器殼體構(gòu)成的內(nèi)部空間。本領(lǐng)域技術(shù)人員可以根據(jù)本發(fā)明的描述結(jié)合本領(lǐng)域內(nèi)的常規(guī)技術(shù)手段確定本發(fā)明的所述漿態(tài)床反應(yīng)器的內(nèi)腔的容積與所述旋液分離器的容積,優(yōu)選情況下,所述旋液分離器的容積與所述漿態(tài)床反應(yīng)器的內(nèi)腔的容積之比為1:100至1:1000。根據(jù)本發(fā)明的第一種優(yōu)選的具體實施方式,本發(fā)明所述的漿態(tài)床加氫裂化方法在圖2所示的漿態(tài)床反應(yīng)器中進行,具體地,該漿態(tài)床反應(yīng)器包括:反應(yīng)器殼體1,該反應(yīng)器殼體的下部設(shè)置有卸劑口12、進氣口11和原料油入口14,該反應(yīng)器殼體的上部設(shè)置有出氣口9和加劑口13;所述反應(yīng)器殼體1的內(nèi)部空間構(gòu)成反應(yīng)器內(nèi)腔8,該反應(yīng)器內(nèi)腔的上部設(shè)置有旋液分離器,所述反應(yīng)器內(nèi)腔中的反應(yīng)物料從旋液分離器入口4進入所述旋液分離器的旋液分離器內(nèi)腔2中進行分離,分離所得的富固含量組分從所述旋液分離器下部的底流管6返回至所述反應(yīng)器內(nèi)腔8中,分離所得的貧固含量組分從產(chǎn)物油出口10引出至漿態(tài)床反應(yīng)器外,分離所得的氣相從氣相出口5引出至所述旋液分離器之外。該反應(yīng)器內(nèi)腔8的底部還設(shè)置有使得反應(yīng)物料在所述反應(yīng)器內(nèi)腔8內(nèi)進行內(nèi)循環(huán)的套筒3,所述套筒3的下部通過內(nèi)徑小于所述套筒內(nèi)徑且伸入所述套筒內(nèi)部的導(dǎo)管與所述反應(yīng)器殼體1的進氣口11連通。 并且,所述套筒3為1根或至少兩根,所述旋液分離器設(shè)置為兩級或兩級以上,至少兩根的套筒下部的所述導(dǎo)管與所述進氣口11之間設(shè)置有氣體分布器7。根據(jù)上述第一種優(yōu)選的具體實施方式,催化劑和原料油分別從所述反應(yīng)器殼體1的加劑口13和原料油入口14進入所述反應(yīng)器內(nèi)腔8中,并且氫氣依次通過進氣口11、氣體分布器7以及導(dǎo)管分別引入到圖2中的套筒3內(nèi),套筒內(nèi)充滿含有氣、固、液三相的反應(yīng)物料,引入的氣體使得套筒中的反應(yīng)物料的氣含量增加,從而向上運動,并且相對地,套筒外的反應(yīng)物料沿著所述套筒外壁向下運動,如此形成內(nèi)循環(huán),同時,反應(yīng)器內(nèi)腔8中的氣、固、液三相反應(yīng)物料從旋液分離器入口4進入第一級的旋液分離器的旋液分離器內(nèi)腔2中進行分離,所得的氣相通過氣相出口5引出至所述旋液分離器之外,分離所得的富固含量組分從所述旋液分離器下部的底流管6返回至所述反應(yīng)器內(nèi)腔8中,分離所得的貧固含量組分引入第二級的旋液分離器的旋液分離器內(nèi)腔2中進行分離,所得的氣相通過氣相出口5引出至所述旋液分離器之外,分離所得的富固含量組分從第二級的旋液分離器下部的底流管6返回至所述反應(yīng)器內(nèi)腔8中,分離所得的貧固含量組分從產(chǎn)物油出口10引出至反應(yīng)器外。從所述氣相出口5引入的氣相通過出氣口9引出至漿態(tài)床反應(yīng)器之外。反應(yīng)完的催化劑從卸劑口12引出至漿態(tài)床反應(yīng)器之外。根據(jù)本發(fā)明的第二種優(yōu)選的具體實施方式,本發(fā)明所述的漿態(tài)床加氫裂化方法在圖3所示的漿態(tài)床反應(yīng)器中進行,具體地,該漿態(tài)床反應(yīng)器包括:反應(yīng)器殼體1,該反應(yīng)器殼體的下部設(shè)置有卸劑口12、進氣口11和原料油入口14,該反應(yīng)器殼體的上部設(shè)置有出氣口9和加劑口13;所述反應(yīng)器殼體1的內(nèi)部空間構(gòu)成反應(yīng)器內(nèi)腔8,該反應(yīng)器殼體1的外部設(shè)置有旋液分離器,所述反應(yīng)器內(nèi)腔中的反應(yīng)物料從旋液分離器入口4進入所述旋液分離器的旋液分離器內(nèi)腔2中進行分離,分離所得的富固含量組分依次從所述旋液 分離器下部的底流管6和連接所述底流管末端和所述反應(yīng)器內(nèi)腔的引導(dǎo)管返回至所述反應(yīng)器內(nèi)腔8中,分離所得的貧固含量組分從產(chǎn)物油出口10引出至漿態(tài)床反應(yīng)器之外,分離所得的氣相從氣相出口5引出至所述旋液分離器之外。該反應(yīng)器內(nèi)腔8的底部還設(shè)置有使得反應(yīng)物料在所述反應(yīng)器內(nèi)腔8內(nèi)進行內(nèi)循環(huán)的套筒3,所述套筒3的下部通過內(nèi)徑小于所述套筒內(nèi)徑且伸入所述套筒內(nèi)部的導(dǎo)管與所述反應(yīng)器殼體1的進氣口11連通。并且,所述套筒3為1根或至少兩根,所述旋液分離器設(shè)置為1級,套筒下部的所述導(dǎo)管與所述進氣口11之間設(shè)置有氣體分布器7。根據(jù)上述第二種優(yōu)選的具體實施方式,催化劑和原料油分別從所述反應(yīng)器殼體1的加劑口13和原料油入口14進入所述反應(yīng)器內(nèi)腔8中,并且氫氣依次通過進氣口11、氣體分布器7以及導(dǎo)管分別引入到圖3中的套筒3內(nèi),套筒內(nèi)充滿含有氣、固、液三相的反應(yīng)物料,引入的氫氣使得套筒中的反應(yīng)物料的氣含量增加,從而向上運動,并且相對地,套筒外的反應(yīng)物料沿著所述套筒外壁向下運動,如此形成內(nèi)循環(huán),同時,反應(yīng)器內(nèi)腔8中的氣、固、液三相反應(yīng)物料從旋液分離器入口4進入旋液分離器的旋液分離器內(nèi)腔2中進行分離,所得的氣相通過氣相出口5引出至所述旋液分離器之外,分離所得的富固含量組分依次從所述旋液分離器下部的底流管6以及連接所述底流管末端和所述反應(yīng)器內(nèi)腔的引導(dǎo)管返回至所述反應(yīng)器內(nèi)腔8中,分離所得的貧固含量組分從產(chǎn)物油出口10引出至漿態(tài)床反應(yīng)器之外。從所述氣相出口5引入的氣相通過出氣口9引出至漿態(tài)床反應(yīng)器之外。反應(yīng)完的催化劑從卸劑口12引出至漿態(tài)床反應(yīng)器之外。優(yōu)選情況下,所述加氫反應(yīng)的條件包括:溫度為360-480℃,壓力為12-25MPa,氫油體積比為500-2000:1,漿態(tài)床反應(yīng)器內(nèi)腔中的液時體積空速為0.1-5.0h-1。更加優(yōu)選所述壓力為15-22MPa;特別優(yōu)選所述壓力為18-20MPa。優(yōu)選所述漿態(tài)床反應(yīng)器的內(nèi)腔中的反應(yīng)物料中的加氫催化劑的平均含量為5-50重量%;優(yōu)選為10-40%重量%。新鮮的加氫催化劑從漿態(tài)床反應(yīng)器上部的加劑口進入漿態(tài)床反應(yīng)器中,從漿態(tài)床反應(yīng)器下部卸劑口卸出,維持漿態(tài)床反應(yīng)器內(nèi)腔中反應(yīng)物料的平均固含量基本不變。特別地,在沒有相反說明的情況下,本發(fā)明中有關(guān)催化劑的含量均是以催化劑中的活性金屬的氧化物計的含量。優(yōu)選地,控制所述氫氣進入所述漿態(tài)床反應(yīng)器中的流量,使得所述漿態(tài)床反應(yīng)器的內(nèi)腔中的反應(yīng)物料在所述套筒外的向下流動的平均速率為0.1-0.3m/s。分離所得的氣相從氣相出口引出至所述旋液分離器之外,氣相流出漿態(tài)床反應(yīng)器后經(jīng)冷卻、分離形成輕質(zhì)烴油和干氣,干氣大部分循環(huán)使用,按比例將其余部分凈化除去甲烷、乙烷、二氧化碳、一氧化碳及其它雜質(zhì)氣體,然后循環(huán)使用。分離所得的貧固含量組分從產(chǎn)物油出口引出至所述漿態(tài)床反應(yīng)器之外,所述貧固含量組分從產(chǎn)物油出口引出后,卸壓后依次經(jīng)常壓分餾塔和減壓分餾塔分離,得到減壓渣油,部分減壓渣油可循環(huán)加工,另一部分可進行帶出催化劑分離處理。以下將通過實施例對本發(fā)明進行詳細描述。其中,漿態(tài)床反應(yīng)器中的反應(yīng)物料中的加氫催化劑的平均含量通過床層密度差計算得到。以下實施例和對比例中所使用的原料油為塔河減壓渣油或者為塔河減壓渣油和高芳烴油,所述塔河減壓渣油的性質(zhì)如表1中所示。所述高芳烴油為催化裂化油漿,且高芳烴油的餾程為300-550℃,芳烴含量為85重量%。表1項目>430℃塔河減壓渣油分析方法密度(20℃)/(g·cm-3)1.0241GB/T2540(殘?zhí)?/重量%22.7GB/T17144(元素)/重量%C85.84SH/T0656H10.12SH/T0656S2.80GB/T17040N0.45化學(xué)發(fā)光法(四組分)/重量%RIPP10-90飽和分23.7芳香分34.9膠質(zhì)21.7瀝青質(zhì)19.7(金屬)/(μg·g-1)RIPP124-90Ni49V325餾程/℃ASTMD6352初餾點3895%42110%43850%58870%63690%實施例1-8用于說明本發(fā)明的漿態(tài)床加氫裂化方法。實施例1本實施例中的漿態(tài)床反應(yīng)器為內(nèi)置旋液分離器的漿態(tài)床反應(yīng)器,本實施例采用圖2所示的漿態(tài)床反應(yīng)器進行漿態(tài)床加氫裂化方法。具體的操作方法如本發(fā)明的上述第一種優(yōu)選的具體實施方式所述。其中,套筒的長度為漿態(tài)床反應(yīng)器的內(nèi)腔的長度的3/5;套筒的內(nèi)徑為300mm,反應(yīng)器內(nèi)腔的內(nèi)徑為5000mm,所述導(dǎo)管伸入所述套筒內(nèi)部的長度 為200mm,底流管的長度為100mm,所述漿態(tài)床反應(yīng)器的內(nèi)腔的長度與所述漿態(tài)床反應(yīng)器的內(nèi)腔的內(nèi)徑之比為10:1。兩級旋液分離器的容積相同,且旋液分離器的容積與漿態(tài)床反應(yīng)器的內(nèi)腔的容積之比為1:800。漿態(tài)床反應(yīng)器的內(nèi)腔中的反應(yīng)物料在套筒外的向下流動的平均速率為0.2m/s;所述反應(yīng)物料在經(jīng)過所述旋液分離器的入口時的速率為8m/s。使用的加氫催化劑的組成如下:以加氫催化劑的總重量計,以氧化物計的Fe含量為30重量%、以氧化物計的Mo含量為8重量%、以氧化物計的Ca含量為0.8重量%。所述加氫催化劑的平均粒徑為80μm;將所述加氫催化劑進行硫化處理,待用。本實施例中的原料油為塔河減壓渣油和高芳烴油,且塔河減壓渣油和高芳烴油的重量比為3:1;本實施例的加氫反應(yīng)的條件如表2中所示;加氫反應(yīng)的結(jié)果如表3中所示。實施例2實施例2采用與實施例1相似的方法和裝置進行,所不同的是,原料油中塔河減壓渣油和高芳烴油的重量比為7:1。加氫反應(yīng)的條件如表2中所示;加氫反應(yīng)的結(jié)果如表3中所示。實施例3實施例3采用與實施例1相似的方法和裝置進行,所不同的是,加氫催化劑的平均粒徑為150μm;加氫反應(yīng)的條件如表2中所示;加氫反應(yīng)的結(jié)果如表3中所示。實施例4實施例4采用與實施例1相似的方法和裝置進行,所不同的是:加氫反應(yīng)的溫度不同,具體的加氫反應(yīng)的條件如表2中所示;加氫反應(yīng)的結(jié)果如表3中所示。實施例5實施例5采用與實施例4相似的方法和裝置進行,所不同的是:加氫反應(yīng)的溫度不同,具體的加氫反應(yīng)的條件如表2中所示;加氫反應(yīng)的結(jié)果如表3中所示。表2反應(yīng)條件實施例1實施例2實施例3實施例4實施例5壓力/MPa1818181818溫度/℃420420420430440催化劑平均含量/重量%40%40%40%40%40%液時體積空速/h-10.20.20.20.20.2氫油體積比10001000100010001000表3實施例1實施例2實施例3實施例4實施例5產(chǎn)物分布/重量%氣體(C1-C4)4.074.354.245.417.21汽油(IBP-180℃)20.8917.2318.9721.1120.31柴油(180-350℃)35.0632.8534.7137.5236.31蠟油(350-524℃)36.2438.9836.5532.7731.17渣油(>524℃)5.628.236.496.217.81生焦率0.691.041.530.831.28合計102.57102.68102.26103.85104.09轉(zhuǎn)化率(>524℃)/%91.0488.0690.3190.7388.34實施例6本實施例中的漿態(tài)床反應(yīng)器為外置旋液分離器的漿態(tài)床反應(yīng)器,本實施例采用圖3所示的漿態(tài)床反應(yīng)器進行漿態(tài)床加氫裂化方法。具體的操作方法 如本發(fā)明的上述第二種優(yōu)選的具體實施方式所述。套筒的長度為漿態(tài)床反應(yīng)器的內(nèi)腔的長度的3/5;套筒的內(nèi)徑為300mm,反應(yīng)器內(nèi)腔的內(nèi)徑為5000mm;所述導(dǎo)管伸入所述套筒內(nèi)部的長度為200mm;底流管的長度為100mm,所述漿態(tài)床反應(yīng)器的內(nèi)腔的長度與所述漿態(tài)床反應(yīng)器的內(nèi)腔的內(nèi)徑之比為10:1。旋液分離器的容積與漿態(tài)床反應(yīng)器的內(nèi)腔的容積之比為1:600。漿態(tài)床反應(yīng)器的內(nèi)腔中的反應(yīng)物料在套筒外的向下流動的平均速率為0.2m/s;所述反應(yīng)物料在經(jīng)過所述旋液分離器的入口時的速率為8m/s。使用的加氫催化劑組成與實施例1中的加氫催化劑相同,所述加氫催化劑的平均粒徑為80μm;將所述加氫催化劑進行硫化處理,待用。本實施例中的原料油為塔河減壓渣油和高芳烴油,且塔河減壓渣油和高芳烴油的重量比為3:1;本實施例的加氫反應(yīng)的條件如表4中所示;加氫反應(yīng)的結(jié)果如表5中所示。實施例7本實施例中的漿態(tài)床反應(yīng)器為外置旋液分離器的漿態(tài)床反應(yīng)器,本實施例采用圖3所示的漿態(tài)床反應(yīng)器進行漿態(tài)床加氫裂化方法。具體的操作方法如本發(fā)明的上述第二種優(yōu)選的具體實施方式所述。其中,旋液分離器的結(jié)構(gòu)和形狀與實施例6中涉及的旋液分離器相同,且本實施例中的漿態(tài)床反應(yīng)器的內(nèi)腔與實施例6中涉及的漿態(tài)床反應(yīng)器的內(nèi)腔容積相同,所不同的是旋液分離器的容積與漿態(tài)床反應(yīng)器的內(nèi)腔的容積之比為1:400。反應(yīng)物料在經(jīng)過所述旋液分離器的入口時的速率為6m/s。使用的加氫催化劑與實施例6中的加氫催化劑相同。本實施例中的原料油為塔河減壓渣油和高芳烴油,且塔河減壓渣油和高 芳烴油的重量比為3:1;本實施例的加氫反應(yīng)的條件如表4中所示;加氫反應(yīng)的結(jié)果如表5中所示。表4反應(yīng)條件實施例6實施例7對比例1對比例2壓力/MPa18181818溫度/℃420420420420催化劑平均含量/重量%3030510液時體積空速/h-10.20.20.20.2氫油體積比1000100010001000表5實施例6實施例7對比例1對比例2產(chǎn)物分布/重量%氣體(C1-C4)3.073.355.246.41汽油(IBP-180℃)18.8917.4312.9713.51柴油(180-350℃)34.0631.8529.7130.5蠟油(350-524℃)35.7436.9834.5432.77渣油(>524℃)7.629.2314.5313.32生焦率2.693.044.275.34合計102.07101.88101.26101.85轉(zhuǎn)化率(>524℃)/%88.6386.2278.3280.12對比例1利用內(nèi)環(huán)流漿態(tài)床小型連續(xù)實驗裝置,對實施例1中的原料油進行了常規(guī)漿態(tài)床加氫裂化反應(yīng),反應(yīng)條件如表4所示。其中,催化劑為環(huán)烷酸鐵,添加量為5重量%(以催化劑中的活性金屬單質(zhì)計)。反應(yīng)結(jié)果見表5。與實施例1相比,原料轉(zhuǎn)化率較低,僅為78.32%,而生焦率較高達4.27%。對比例2本對比例采用與對比例1相同的裝置和催化劑,所不同的是:將催化劑 加入量提高至10重量%。結(jié)果:反應(yīng)過程中焦炭產(chǎn)率達5.34%,影響小型連續(xù)裝置的操作。從上述實施例和對比例的結(jié)果可以看出,本發(fā)明提供的上述漿態(tài)床加氫裂化方法能夠在高含量的催化劑的存在下加工重質(zhì)原料油。而且,應(yīng)用本發(fā)明的方法進行漿態(tài)床加氫裂化方法時,能夠強化熱、質(zhì)傳遞效果,提高渣油轉(zhuǎn)化率。以上詳細描述了本發(fā)明的優(yōu)選實施方式,但是,本發(fā)明并不限于上述實施方式中的具體細節(jié),在本發(fā)明的技術(shù)構(gòu)思范圍內(nèi),可以對本發(fā)明的技術(shù)方案進行多種簡單變型,這些簡單變型均屬于本發(fā)明的保護范圍。另外需要說明的是,在上述具體實施方式中所描述的各個具體技術(shù)特征,在不矛盾的情況下,可以通過任何合適的方式進行組合,為了避免不必要的重復(fù),本發(fā)明對各種可能的組合方式不再另行說明。此外,本發(fā)明的各種不同的實施方式之間也可以進行任意組合,只要其不違背本發(fā)明的思想,其同樣應(yīng)當視為本發(fā)明所公開的內(nèi)容。當前第1頁1 2 3