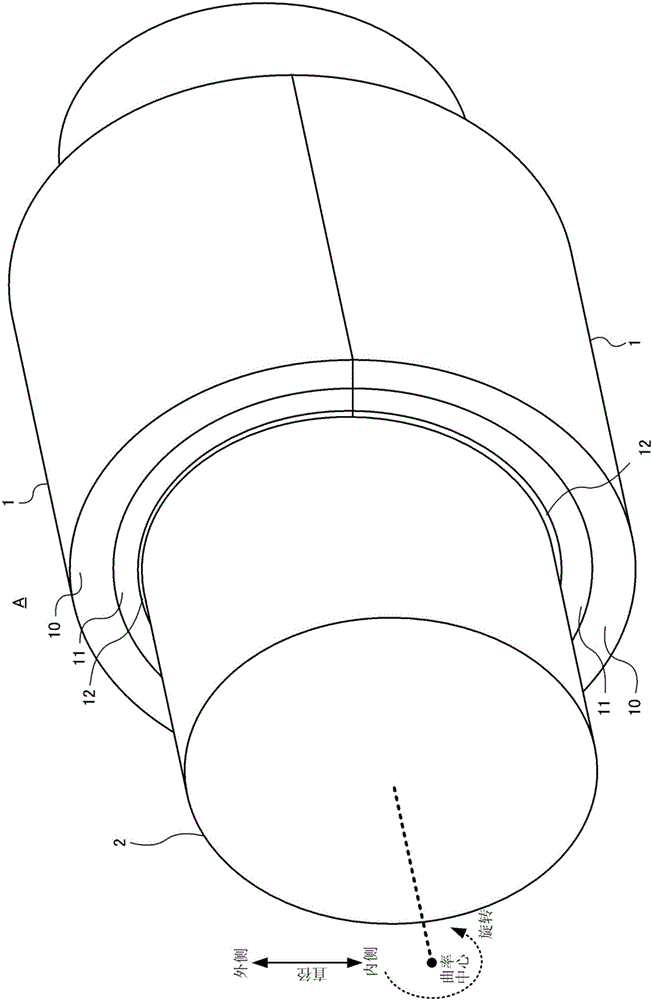
本發(fā)明涉及配合軸在滑動面上滑動的滑動構件和滑動軸承。
背景技術:
:已知如下技術:在Cu合金上形成Bi覆蓋層,使配合構件在該覆蓋層上滑動(參照專利文獻1)。在專利文獻1中,在Bi覆蓋層的下層形成Ag中間層。由此,能提高由Bi產(chǎn)生的磨合性,并且能通過Ag防止疲勞斷裂?,F(xiàn)有技術文獻專利文獻專利文獻1:日本特開2006-266445號公報技術實現(xiàn)要素:發(fā)明所要解決的問題然而,在專利文獻1中,存在如下問題:覆蓋層的Bi的結晶組織是柱狀晶,在柱狀晶的晶粒邊界容易產(chǎn)生解理斷裂。特別是,在Bi的結晶粒徑小的情況下,存在如下問題:在疲勞時容易產(chǎn)生晶粒邊界處的解理斷裂。本發(fā)明是鑒于所述問題而完成的,其目的在于提供一種能防止疲勞時的滑動面的解理斷裂的技術。用于解決問題的方案為了達成所述目的,在本發(fā)明的滑動構件和滑動軸承中,在基層上形成有覆蓋材料的覆蓋層,所述覆蓋材料的覆蓋層具有配合構件的滑動面。而且,覆蓋層具有晶粒的粒徑為大于等于3μm且小于等于7μm的覆蓋材料的結晶組織。如此,通過將覆蓋材料的晶粒的粒徑設為大于等于3μm,能促進疲勞時的晶粒內(nèi)的位錯。即,通過促進晶粒內(nèi)的位錯的移動,能增大覆蓋層的延展性,能防止疲勞時的解理斷裂。另一方面,通過將覆蓋材料的晶粒設為小于等于7μm,能防止由于強度下降,反而疲勞斷裂得到促進。圖1是表示結晶粒徑與屈服應力的關系的圖表(引用:T.G.Nieh,LawrenceLivermoreNationalLab)。如該圖所示,結晶粒徑在10~20nm左右屈服應力變得最大,并且在與該結晶粒徑相比結晶粒徑變大的區(qū)域中,根據(jù)Hall-Petch(霍爾-佩奇)關系,結晶粒徑越大,屈服應力越減小。在屈服應力服從Hall-Petch關系的結晶粒徑的區(qū)域中,雖然覆蓋層提前屈服,但在粒徑大的晶粒內(nèi)容易使位錯移動,能使覆蓋層塑性變形。即,能利用比使晶界解理的應力小的應力使覆蓋層塑性變形,能防止覆蓋層的解理斷裂。此外,覆蓋材料可以是Bi、Sn、Pb、In或者Sb。Bi、Sn、Pb、In、Sb均硬度(例如莫氏硬度)較小,適合作為覆蓋材料。此外,即使在具備本發(fā)明的特征的滑動軸承中,也可發(fā)揮以上所說明的本發(fā)明的效果。附圖說明圖1是表示結晶粒徑與屈服應力的關系的圖表。圖2是本發(fā)明實施方式的滑動構件的立體圖。圖3的(3A)是疲勞試驗的示意圖,(3B)是疲勞損傷面積率的圖表。具體實施方式在此,按照下述順序對本發(fā)明的實施方式加以說明。(1)第一實施方式:(1-1)滑動構件的構成:(1-2)計量方法:(1-3)滑動構件的制造方法:(2)實驗結果:(3)其他實施方式:(1)第一實施方式:(1-1)滑動構件的構成:圖2是本發(fā)明的一實施方式的滑動構件1的立體圖?;瑒訕嫾?包含:里襯金屬10、襯里(lining)11和涂層(overlay)12?;瑒訕嫾?是將中空狀的圓筒在徑向上二等分的呈對開狀的金屬構件,剖面是半圓弧狀。通過組合兩個滑動構件1成為圓筒狀,形成滑動軸承A?;瑒虞S承A在形成于內(nèi)部的中空部分軸支承圓柱狀的配合軸2(發(fā)動機的曲軸)。配合軸2的外徑形成為略小于滑動軸承A的內(nèi)徑。向形成于配合軸2的外周面與滑動軸承A的內(nèi)周面之間的間隙供給潤滑油(發(fā)動機油)。此時,配合軸2的外周面在滑動軸承A的內(nèi)周面上滑動。滑動構件1具有如下構造:按照遠離曲率中心的順序,依次層疊有里襯金屬10、襯里11和涂層12。因此,里襯金屬10構成滑動構件1的最外層,涂層12構成滑動構件1的最內(nèi)層。里襯金屬10、襯里11和涂層12分別在圓周方向上具有一定的厚度。里襯金屬10的厚度是1.3mm,襯里11的厚度是0.2mm,涂層12的厚度是12μm。涂層12的曲率中心側的表面的半徑(滑動構件1的內(nèi)徑)是40mm。以下,所謂的“內(nèi)側”是指滑動構件1的曲率中心側,所謂的“外側”是指滑動構件1的曲率中心的相反側。涂層12的內(nèi)側的表面構成配合軸2的滑動面。里襯金屬10由鋼形成,所述鋼含有0.15wt%的C,含有0.06wt%的Mn,剩余部分由Fe構成。需要說明的是,里襯金屬10由能介由襯里11和涂層12支承來自配合軸2的荷載的材料形成即可,也可以不由鋼來形成。襯里11是層疊于里襯金屬10的內(nèi)側的層,構成本發(fā)明的基層。襯里11含有10wt%的Sn,含有8wt%的Bi,剩余部分由Cu和不可避免的雜質形成。襯里11的不可避免的雜質是Mg、Ti、B、Pb、Cr等,是精煉或者廢料中混入的雜質。不可避免的雜質的含量在整體中小于等于1.0wt%。涂層12是層疊于襯里11的內(nèi)側的表面上的層,構成本發(fā)明的覆蓋層。涂層12由Bi和不可避免的雜質構成。不可避免的雜質的含量為小于等于1.0wt%。本實施方式中,涂層12具有由Bi的晶粒構成的結晶組織,構成涂層12的Bi的晶粒的平均粒徑是4μm。對以上說明的滑動構件1進行疲勞試驗的結果是,疲勞損傷面積率為10%,良好。通過將涂層12的晶粒的粒徑設為4μm,能促進在疲勞時晶粒內(nèi)的位錯,能防止晶界處的解理斷裂。即,通過促進晶粒內(nèi)的位錯的移動,能增大涂層12整體的延展性,能防止在疲勞時的解理斷裂。此外,通過將覆蓋材料的晶粒的粒徑設為7μm,能防止由于強度下降反而疲勞斷裂得到促進。(1-2)計量方法:通過以下方法計量在上述實施方式中示出的各數(shù)值。利用ICP發(fā)射光譜分析裝置(島津制作所制ICPS-8100)計量構成滑動構件1的各層的元素的質量。各層的厚度按以下順序進行計量。首先,利用截面離子拋光儀(日本電子制IB-09010CP)研磨滑動構件1的徑向的剖面。然后,利用電子顯微鏡(日本電子制JSM-6610A)以7000倍的倍率對滑動構件1的剖面進行拍攝,由此獲得觀察圖像(反射電子像)的圖像數(shù)據(jù)。然后,利用圖像解析裝置(NIRECO公司制LUZEXAP)對觀察圖像進行解析,由此計量膜厚。按照以下順序計量涂層12中的Bi晶粒的平均粒徑。首先,利用截面離子拋光儀研磨涂層12的任意剖面。利用電子顯微鏡(日本電子制JSM-6610A)以7000倍的倍率對涂層12的剖面中面積為0.02mm2的任意觀察視野范圍(長度0.1mm×寬度0.2mm的矩形范圍)進行拍攝,由此獲得觀察圖像(反射電子像)的圖像數(shù)據(jù)。然后,在觀察圖像中進行切片法,由此計量Bi晶粒的粒徑。該切片法中,用形成于觀察圖像上的線段所通過的晶粒的數(shù)量去除該線段的長度,由此計量該線段上的晶粒的粒徑。進而,對多個線段的每一個線段進行計量,將所計量的晶粒的粒徑的算術平均值(合計值/線段數(shù))作為平均粒徑。疲勞損傷面積率按照以下的順序計量。首先,通過圖3A示出的疲勞試驗裝置進行疲勞試驗。如圖3A所示,準備在長度方向的兩端形成有圓柱狀的貫通孔的連桿R,在一端的貫通孔軸支承試驗軸H(淡的剖面線)。需要說明的是,在軸支承試驗軸H的連桿R的貫通孔的內(nèi)周面形成與滑動構件1同樣的涂層12(深的剖面線)。在試驗軸H的軸向上的連桿R的兩外側軸支承試驗軸H,以3000轉/分鐘的轉速使試驗軸H旋轉。將試驗軸H相反側的連桿R的端部連結于在連桿R的長度方向上往復移動(3000往復/分鐘)的移動體F,將該移動體F的往復荷載設為50MPa。此外,向連桿R與試驗軸H之間供給120℃的發(fā)動機油。通過持續(xù)以上的狀態(tài)50小時,進行涂層12的疲勞試驗。然后,在疲勞試驗后,以從與該表面正交的直線上的位置、將該直線作為主光軸的方式拍攝涂層12的內(nèi)側的表面(滑動面),獲得作為該拍攝的圖像的評價圖像。然后,利用雙筒望遠鏡(放大鏡)觀察并確定評價圖像上所呈現(xiàn)的涂層12的表面中的損傷的部分,將作為該損傷的部分的面積的損傷部面積除以在評價圖像所呈現(xiàn)的涂層12的整個表面的面積,將所獲得的值的百分率作為疲勞損傷面積率來進行計量。(1-3)滑動構件的制造方法:首先,準備具有與里襯金屬10相同厚度的低碳鋼的平面板。接著,在由低碳鋼形成的平面板上噴灑構成襯里11的材料的粉末。具體而言,按照上述襯里11中的各成分的質量比混合Cu粉末、Bi粉末和Sn粉末并噴灑于低碳鋼的平面板上。只要能滿足襯里11中的各成分的質量比即可,也可以將Cu-Bi、Cu-Sn等合金粉末噴灑于低碳鋼的平面板上。粉末的粒徑通過試驗用篩子(JISZ8801)調整為小于等于150μm。接著,對低碳鋼的平面板、噴灑于該平面板上的粉末進行燒結。控制燒結溫度為700~1000℃,在惰性氣氛中燒結。燒結后進行冷卻。當結束冷卻時,在低碳鋼的平面板上形成有Cu合金層。該Cu合金層包含冷卻過程中析出的軟質Bi粒子。接著,對形成有Cu合金層的低碳鋼進行沖壓加工,以便形成將中空狀的圓筒在徑向上二等分的形狀。這時,以使低碳鋼的外徑與滑動構件1的外徑一致的方式進行沖壓加工。接著,對在里襯金屬10上所形成的Cu合金層的表面進行切削加工。這時,以使在里襯金屬10上所形成的Cu合金層的厚度與襯里11相同的方式控制切削量。由此,能通過切削加工后的Cu合金層形成襯里11。切削加工例如通過設有由燒結金剛石形成的切削工具件的車床來進行。接著,通過電鍍,在襯里11的表面上層疊僅12μm厚的作為覆蓋材料的Bi,由此形成涂層12。Bi的電鍍順序如下。首先,在電解液中向襯里11的表面通入電流,由此對襯里11的表面進行脫脂。接著,對襯里11的表面進行水洗。進而,通過對襯里11的表面進行酸洗,去除不需要的氧化物。之后,對襯里11的表面再次進行水洗。當完成以上的前處理時,通過向浸漬于電鍍液的襯里11供給電流,進行Bi的電鍍。涂層12中的Bi的電鍍條件如下。電鍍液的組成設為含有Bi濃度:40~60g/L,有機磺酸:25~100g/L,添加劑:0.5~50g/L。電鍍液的溫度調整在40~60℃之間。進而,向襯里11供給的電流采用占空比為50%的矩形脈沖電流,其平均電流密度設為4~8A/dm2。層疊了涂層12之后,進行水洗和干燥,完成滑動構件1。通過進一步地將兩個滑動構件1組合成圓筒狀,形成滑動軸承A。(2)實驗結果:[表1]樣品平均拉徑[μm]疲勞損傷率[%]12.5382312341045145716表1表示按涂層12中的Bi的平均粒徑對疲勞損傷面積率進行計量的結果。按照與上述的制造方法同樣的方法,制造Bi的平均粒徑不同的樣品1~5(樣品3是所述實施方式)。不過,通過調整涂層12的電鍍中的電流密度,調整Bi的平均粒徑。由于具有涂層12的電鍍中的電流密度越大、Bi的平均粒徑越大的性質,因此,目標平均粒徑越大,將電流密度調整得越大。圖3B是按Bi的平均粒徑來表示疲勞損傷面積率的圖表。如該圖所示可知,通過在Bi的平均粒徑為2~3μm的區(qū)域增大平均粒徑,急劇地抑制疲勞損傷面積。此外,可知通過在Bi的平均粒徑為大于等于4μm的區(qū)域增大平均粒徑,疲勞損傷面積稍微增大。推定這是由于當Bi的平均粒徑變大時,強度下降導致的。因此,可知為了獲得作為滑動軸承A所需的耐疲勞性,理想的是將Bi的平均粒徑設為大于等于3μm且小于等于7μm。(3)其他實施方式:在所述實施方式中,對構成軸支承發(fā)動機的曲軸的滑動軸承A的滑動構件1進行了例示,但通過本發(fā)明的滑動構件1也可以形成其他用途的滑動軸承A。例如,通過本發(fā)明的滑動構件1可以形成變速器用的齒輪襯套(gearbush)、活塞銷襯套/轂(boss)襯套等。此外,襯里11的基質(matrix)不限于Cu合金,根據(jù)配合軸2的硬度來選擇基質的材料即可。此外,覆蓋材料只要是比襯里11軟的材料即可,例如可以是Pb、Sn、In、Sb的任一種。即使在Pb、Sn、In、Sb中,也能通過增大晶粒的粒徑來提高延展性。附圖標記說明:1:滑動構件2:配合軸10:里襯金屬11:襯里11b:Bi粒子12:涂層當前第1頁1 2 3