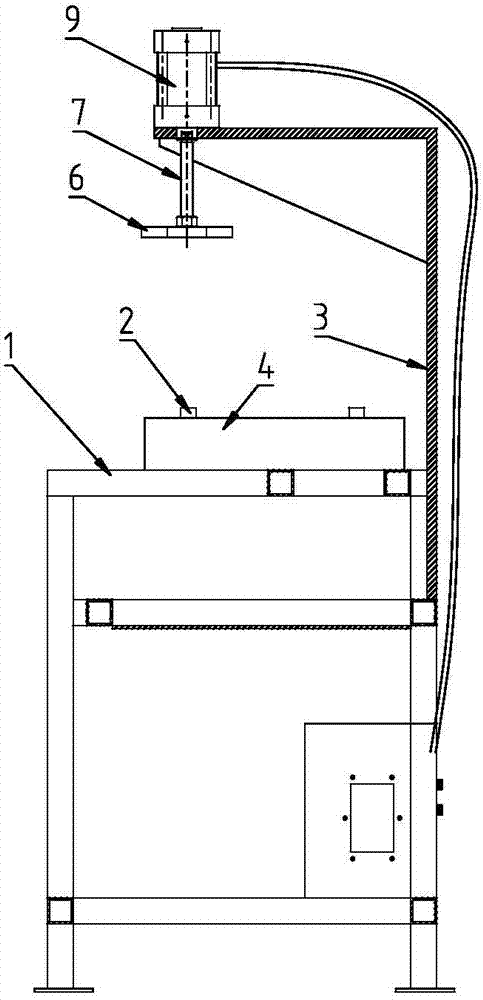
本發(fā)明涉及汽車零部件加工技術(shù)領(lǐng)域,具體是涉及一種彈簧壓緊裝置。
背景技術(shù):目前,一些靠彈簧減震的前懸置在裝配過程中常出現(xiàn)因左右彈簧壓縮量不同導(dǎo)致駕駛室歪斜的情況,并且懸置開檔尺寸因彈簧柔性變形而難以控制,兩邊安裝面常常呈喇叭口狀或者平行四邊形狀,從而對(duì)該種懸置與駕駛室的裝配造成極大困擾。另外,在初期壓縮彈簧的方法主要是用撬棍靠人力擠壓,經(jīng)測(cè)算彈簧達(dá)到指定壓縮量需要用1.5米的撬棍人工用力壓縮,并且要堅(jiān)持到兩邊彈簧都固定好才能松開,相當(dāng)費(fèi)時(shí)費(fèi)力,并存在很大的安全隱患。
技術(shù)實(shí)現(xiàn)要素:針對(duì)現(xiàn)有技術(shù)中存在的技術(shù)問題,本發(fā)明的目的在于提供一種結(jié)構(gòu)簡(jiǎn)單、加工便捷的彈簧壓緊裝置。為了實(shí)現(xiàn)上述目的,本發(fā)明所采用的技術(shù)方案為:一種彈簧壓緊裝置,包括機(jī)架,機(jī)架的上、中、下部依次設(shè)有氣缸、水平操作臺(tái)、PLC控制箱,水平操作臺(tái)上布置有兩個(gè)平行排布的裝配臺(tái),裝配臺(tái)的頂部平面設(shè)有若干個(gè)固定銷,兩個(gè)裝配臺(tái)的相對(duì)側(cè)開設(shè)有定位孔;氣缸通過氣缸柱塞與處于水平操作臺(tái)正上方的壓板連接;工件底部裝配于裝配臺(tái)之上,PLC控制箱控制氣缸運(yùn)行使壓板壓緊工件頂部。本發(fā)明的彈簧壓緊裝置,其有益效果表現(xiàn)在:1、在裝配前將連接板開檔尺寸固定死,避免了因彈簧壓縮變形帶來的工件扭曲和開檔尺寸超差,影響工件與駕駛室的安裝。2、由于氣缸通過壓板將力均勻傳遞到左右兩邊,并且工件的連接桿為剛性元件,所以兩邊彈簧壓縮量基本一致,避免了因兩邊彈簧壓縮量相差較大導(dǎo)致的駕駛室歪斜現(xiàn)象。3、液壓缸由PLC系統(tǒng)進(jìn)行控制,操作簡(jiǎn)單、使用方便,減輕了人力負(fù)擔(dān),安全性也有所提升。附圖說明圖1為本發(fā)明彈簧壓緊裝置的主視圖。圖2為本發(fā)明彈簧壓緊裝置的側(cè)視圖。圖3為工件的結(jié)構(gòu)示意圖。圖4為裝配工件的主視圖。圖5為裝配工件的側(cè)視圖。具體實(shí)施方式為進(jìn)一步描述本發(fā)明,下面結(jié)合附圖和實(shí)施例對(duì)本發(fā)明作進(jìn)一步詳細(xì)說明。圖1和2所示的一種彈簧壓緊裝置,包括機(jī)架3,機(jī)架3的上、中、下部依次設(shè)有氣缸9、水平操作臺(tái)1、PLC控制箱8,水平操作臺(tái)1上布置有兩個(gè)平行排布的裝配臺(tái)4,裝配臺(tái)4的頂部平面設(shè)有若干個(gè)固定銷2,兩個(gè)裝配臺(tái)4的相對(duì)側(cè)開設(shè)有定位孔10;氣缸9通過氣缸柱塞7與處于水平操作臺(tái)1正上方的壓板6連接;工件底部裝配于裝配臺(tái)4之上,PLC控制箱8控制氣缸9運(yùn)行使壓板6壓緊工件頂部。請(qǐng)結(jié)合圖3,該彈簧壓緊裝置的具體工作過程如下:首先,裝配臺(tái)4經(jīng)過校平,在同一水平面上。左工件11、右工件12穿過前后兩個(gè)固定銷2分別固定在裝配臺(tái)4的上平面之上,并與其貼平。左工件11、右工件12內(nèi)側(cè)的連接板上并排有四個(gè)圓孔,插銷5穿過連接板插入定位孔10中,從而使工件與裝配臺(tái)4的內(nèi)側(cè)面貼平。左工件11、右工件12和上工件15通過螺栓14連接,彈簧13放置在工件的彈簧座里(請(qǐng)參閱圖4和5所示)。其次,踩下進(jìn)程踏板(與PLC控制箱8相連接),壓板6在氣缸9的驅(qū)動(dòng)下接觸上工件15的連接桿,并使上工件15繞螺栓14轉(zhuǎn)動(dòng),從而向下壓縮彈簧13。PLC控制箱8已對(duì)氣缸9的行程設(shè)定好,當(dāng)達(dá)到最大行程后,氣缸持續(xù)保壓,直至彈簧固定好后,踩回升踏板,氣缸柱塞7上升回歸零位。以上內(nèi)容僅僅是對(duì)本發(fā)明的構(gòu)思所作的舉例和說明,所屬本技術(shù)領(lǐng)域的技術(shù)人員對(duì)所描述的具體實(shí)施例做各種各樣的修改或補(bǔ)充或采用類似的方式替代,只要不偏離發(fā)明的構(gòu)思或者超越本權(quán)利要求書所定義的范圍,均應(yīng)屬于本發(fā)明的保護(hù)范圍。