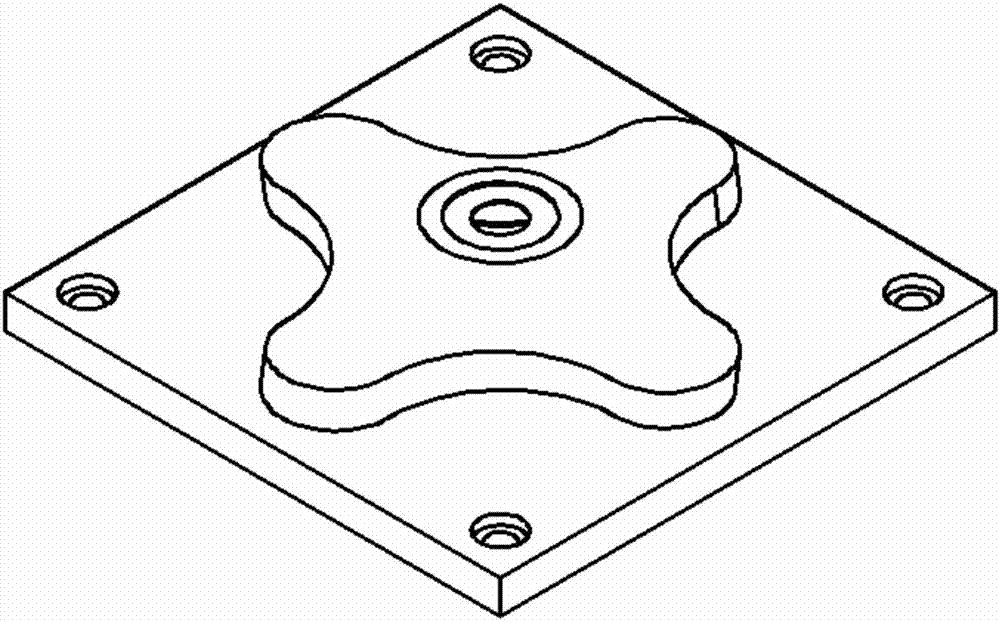
本發(fā)明涉及一種航天航空、汽車、船舶及核電等關(guān)鍵件在多品種、小批量等加工方法,尤其是一種綜合檢測數(shù)控機床加工精度的方法。
背景技術(shù):
:五軸聯(lián)動數(shù)控機床在航空航天、汽車制造等先進(jìn)制造業(yè)中的地位和整體技術(shù)水平過程中所起的作用十分巨大。所以,對于五軸數(shù)控機床的加工精度提出很高的要求。檢測數(shù)控機床加工精度方法主要有直接測量法和間接測量法,直接測量法就是利用各種測量精度的工具對機床的加工精度進(jìn)行直接測量;間接測量法基本就是用機床對標(biāo)準(zhǔn)的機械試件進(jìn)行加工,通過分析標(biāo)準(zhǔn)試件的加工精度是否達(dá)到標(biāo)準(zhǔn)試件的精度標(biāo)準(zhǔn),來推斷待加工機床是否達(dá)到性能標(biāo)準(zhǔn)要求,并且根據(jù)具體的加工精度對比相應(yīng)的測試標(biāo)準(zhǔn)值,用來判斷機床的綜合精度是否達(dá)到性能標(biāo)準(zhǔn)要求。目前,五軸聯(lián)動數(shù)控機床誤差辨識的思路是通過機床加工誤差的檢測與評定,來評價機床的加工性能。目前比較常用的五軸數(shù)控機床誤差表示方法主要有以下幾種:方法1.基于球桿儀的誤差辨識方法:球桿儀的兩端有高精度鋼球組成,一端固定,另一端連接著一個高精度位移傳感器。兩個鋼球兩端通過三點定位的磁性吸座進(jìn)行定位,一端吸附在主軸上,另一端則吸附在工作臺上,如圖3所示。其主要是用于測量數(shù)控機床兩周聯(lián)動精度的測量,分別可以測量x-y,x-z和y-z平面的兩軸聯(lián)動精度。當(dāng)工作臺相對于主軸作圓周插補運動時,形成一個模擬切削的圓弧軌跡,傳感器采集兩鋼球間距離的變化并傳遞給計算機,經(jīng)過軟件診斷分析,得到兩軸聯(lián)動的圓度精度并分離出各種單項誤差,如反向間隙、反向躍沖、伺服不匹配、比例不匹配、直線度、垂直度、周期誤差以及橫向間隙等。方法2:基于nas979(美國國家宇航標(biāo)準(zhǔn))檢測試件的誤差方法:美國nas979制定了“圓形-菱形-方形”形試件切削試驗標(biāo)準(zhǔn),通過試切該檢測試件,分別檢測機床沿x坐標(biāo)的直線度,x、y、z坐標(biāo)之間的垂直度,以及數(shù)控插補的直線度、圓度和x-y平面上孔的位置精度等。因為機床各坐標(biāo)軸的誤差與行程之間存在線性關(guān)系,該標(biāo)準(zhǔn)可依據(jù)機床各坐標(biāo)的行程范圍,以確定切削試件的相應(yīng)尺寸。這樣使得利用小尺寸試件檢測大行程的工作精度更加合理方法3:基于“s”形試件的五軸數(shù)控機床的誤差辨識方法:基于三坐標(biāo)機測量得到的“s”形試件法向誤差逆向溯源出對機床加工產(chǎn)生主要影響的機床因素,并且通過神經(jīng)網(wǎng)絡(luò)進(jìn)一步確定了主要因素對機床精度的影響水平。因此,采用該方法不僅能夠?qū)C床精度進(jìn)行評判,而且當(dāng)機床精度達(dá)不到要求時還能給出機床精度的優(yōu)化方案,從量值上對影響機床精度的相關(guān)因素進(jìn)行調(diào)整,從而達(dá)到機床各部件的高精度要求。方法4:基于激光干涉儀的九線辨識法:九線辨識法的精髓在于只檢查機床工作臺坐標(biāo)系中九條直線上的位置誤差和直線度誤差,可以實現(xiàn)對機床二十一項基本幾何誤差的辨識。首先選擇三個平動軸中的一個平動軸運動,而另外兩個軸保持靜止,在工作臺坐標(biāo)系中選擇三條直線,測量出三條直線上各點的位移誤差,在測量另一條直線誤差的同時,測量出一個方向的直線度誤差,基于測量出來的直線度誤差和位移誤差建立起六個線性方程,求解方程組就可以得到運動軸的六項基本誤差,同理便可以求解出另外兩個平動軸的十二項基本誤差。最后通過讀取激光干涉儀在測量直線度誤差時直線偏離基準(zhǔn)的修正角便可以得到3項垂直誤差。綜上可知,現(xiàn)有辨識方法的主要缺點為:目前的數(shù)控機床誤差辨識方法并不能全面反應(yīng)機床的切削加工性能,而且主要是在空載低速的情況下對機床的靜態(tài)因素進(jìn)行辨識。無論以上哪一種辨識方法都是要先用待加工機床對零件進(jìn)行加工,加工結(jié)束后再對零件進(jìn)行精度測量,或者在加工的過程中對零件進(jìn)行精度檢測,遠(yuǎn)遠(yuǎn)不能滿足現(xiàn)代加工的需求。技術(shù)實現(xiàn)要素:針對以上缺陷,本發(fā)明是要提出一種基于“x”形航空薄壁標(biāo)準(zhǔn)試件的數(shù)控加工機床優(yōu)選方法。本發(fā)明的技術(shù)方案是:一種基于“x”形航空薄壁標(biāo)準(zhǔn)件的數(shù)控加工機床優(yōu)選方法,具體步驟是:(1)對于待加工零件進(jìn)行有限元模擬切削分析,計算出待加工零件的加工難度系數(shù);(2)再通過機床加工難度系數(shù)與工件復(fù)雜度等級差映射關(guān)系表:δmδca級δm≤1δc≤0.5b級1<δm<20.5<δc<0.8c級2≤δm0.8≤δc對零件的加工難度進(jìn)行劃分;(3)通過對待加工零件的加工難度系數(shù)等級劃分,選擇相對應(yīng)的待加工機床,既可以避免使用加工精度不夠的機床加工,又可以避免使用精度過高的機床。所述機床加工難度系數(shù)與工件復(fù)雜度等級差映射關(guān)系表建立方法:(1)獲取基于的“x”形航空薄壁標(biāo)準(zhǔn)件的理論加工復(fù)雜度系數(shù)理論加工復(fù)雜度系數(shù)由特征加工剛度和平均值δk與動態(tài)剛度和平均值δc組成,其中:特征加工剛度和平均值式中:ξ為工件特征相關(guān)系數(shù);i、n為加工工件變形節(jié)點;j為x、y、z三個方向;f為切削力;δ為變形量;動態(tài)剛度和平均值同理,運用以上方法,對加工過程中不同工序的動態(tài)剛度和平均值計算,得到δkave,該值越小,加工整體動態(tài)剛度變化越弱,加工復(fù)雜度越高;式中:δkf為加工完成后被加工工件特征結(jié)構(gòu)的平均剛度,δkave為各個工序被加工工件特征結(jié)構(gòu)剛度和的平均值;(2)構(gòu)建各企業(yè)獨有的機床加工難度系數(shù)與工件復(fù)雜度映射關(guān)系對比“x”形航空薄壁標(biāo)準(zhǔn)件在企業(yè)所有可用機床上加工的實驗結(jié)果δc',并對比理論δc,即可獲得機床加工難度系數(shù)并最終構(gòu)建各企業(yè)獨有的機床加工難度系數(shù)與工件復(fù)雜度映射關(guān)系。本發(fā)明的有益效果是:根據(jù)“x”形新型航空薄壁標(biāo)準(zhǔn)試件的特點對綜合檢測數(shù)控機床進(jìn)行了更加深入的科學(xué)研究,重新建立新的數(shù)學(xué)模型,先對“x”形新型航空薄壁標(biāo)準(zhǔn)試件進(jìn)行有限元模擬切削加工與分析,計算出“x”形新型航空薄壁標(biāo)準(zhǔn)試件的加工復(fù)雜系數(shù),根據(jù)表1的系數(shù)等級劃分,采用相對應(yīng)的數(shù)控機床加工“x”形新型航空薄壁標(biāo)準(zhǔn)試件。相應(yīng)地,當(dāng)生產(chǎn)需要加工其他的薄壁零件時,可以先對其零件進(jìn)行模擬切削加工與分析,計算出其零件的加工復(fù)雜系數(shù),根據(jù)表1的系數(shù)等級劃分,采用相對應(yīng)的數(shù)控機床進(jìn)行加工,首先,可以滿足零件的加工精度要求,還可以極大地節(jié)省成本與資源。附圖說明圖1為本發(fā)明的機床難度系數(shù)與工件復(fù)雜度確定流程圖;圖2為本發(fā)明的基于“x”形新型航空薄壁標(biāo)準(zhǔn)系列試件a的a面示意圖;圖3為本發(fā)明的基于“x”形新型航空薄壁標(biāo)準(zhǔn)系列試件a的b面示意圖;圖4為本發(fā)明的基于“x”形新型航空薄壁標(biāo)準(zhǔn)系列試件b的示意圖。具體實施方式下面結(jié)合附圖和具體實施例,詳細(xì)的說明本發(fā)明專利的設(shè)計原理。如圖1所示,一種基于“x”形航空薄壁標(biāo)準(zhǔn)件的數(shù)控加工機床優(yōu)選方法,具體步驟是:(1)對于待加工零件進(jìn)行有限元模擬切削分析,計算出待加工零件的加工難度系數(shù);(2)再通過機床加工難度系數(shù)與工件復(fù)雜度等級差映射關(guān)系表1:表1δmδca級δm≤1δc≤0.5b級1<δm<20.5<δc<0.8c級2≤δm0.8≤δc對零件的加工難度進(jìn)行劃分;(3)通過對待加工零件的加工難度系數(shù)等級劃分,選擇相對應(yīng)的待加工機床,既可以避免使用加工精度不夠的機床加工,又可以避免使用精度過高的機床。所述機床加工難度系數(shù)與工件復(fù)雜度等級差映射關(guān)系表建立方法:(1)獲取基于的“x”形航空薄壁標(biāo)準(zhǔn)件的理論加工復(fù)雜度系數(shù)理論加工復(fù)雜度系數(shù)由特征加工剛度和平均值δk與動態(tài)剛度和平均值δc組成,其中:特征加工剛度和平均值式中:ξ為工件特征相關(guān)系數(shù);i、n為加工工件變形節(jié)點;j為x、y、z三個方向;f為切削力;δ為變形量;動態(tài)剛度和平均值同理,運用以上方法,對加工過程中不同工序的動態(tài)剛度和平均值計算,得到δkave,該值越小,加工整體動態(tài)剛度變化越弱,加工復(fù)雜度越高;式中:δkf為加工完成后被加工工件特征結(jié)構(gòu)的平均剛度,δkave為各個工序被加工工件特征結(jié)構(gòu)剛度和的平均值。(2)構(gòu)建各企業(yè)獨有的機床加工難度系數(shù)與工件復(fù)雜度映射關(guān)系對比“x”形航空薄壁標(biāo)準(zhǔn)件在企業(yè)所有可用機床上加工的實驗結(jié)果δc',并對比理論δc,即可獲得機床加工難度系數(shù)并最終構(gòu)建各企業(yè)獨有的機床加工難度系數(shù)與工件復(fù)雜度映射關(guān)系。實施例:如圖2,3所示,本發(fā)明的基于的“x”形航空薄壁標(biāo)準(zhǔn)系列試件a的切削加工工序是先加工b面,待b面加工結(jié)束,翻轉(zhuǎn)180°,在試件a的型腔內(nèi)放上“x”形新型航空薄壁標(biāo)準(zhǔn)系列支撐件b,如圖4所示定位結(jié)束,再加工a面。加工復(fù)雜度系數(shù)由是由特征加工剛度和平均值δk與動態(tài)剛度和平均值δc組成,特征加工剛度和平均值主要是評價該待分析零件綜合抵抗變形的能力,該系數(shù)越小,能力越弱,加工復(fù)雜度越高。特征加工剛度和平均值:對“x”形新型航空薄壁標(biāo)準(zhǔn)系列試件a的加工仿真結(jié)果分析,獲取該薄壁件變形節(jié)點的剛度和,最后再計算其平均值,以此評價該零件綜合抵抗變形的能力,該系數(shù)越小,能力越弱,加工復(fù)雜度越高。特征加工剛度和平均值:式中:ξ為工件特征相關(guān)系數(shù)(與工件特征等有關(guān));i、n為加工工件變形節(jié)點;j為x、y、z三個方向;f為切削力;δ為變形量。動態(tài)剛度和平均值:同理,運用以上方法,對加工過程中不同工序(假定n道工序)動態(tài)剛度和平均值計算,得到δkave,并定義工件加工復(fù)雜度指標(biāo)為:通過本發(fā)明的以上數(shù)學(xué)模型,結(jié)合有限元方法,可以獲取標(biāo)準(zhǔn)件的理論加工復(fù)雜度值,此時將標(biāo)準(zhǔn)件在企業(yè)所有可用機床上加工,實驗測試δc',再對比理論δc,獲得即可以得到表1中所示的機床難度系數(shù)與工件復(fù)雜度等級映射關(guān)系,需說明的是表1具體的值是特殊案例下的參考值,如對于具體企業(yè)的案例需要根據(jù)本發(fā)明方法重新計算。通過本發(fā)明建立表1的工件復(fù)雜系數(shù)與機床加工難度系數(shù)的映射關(guān)系,可以評判機床的加工工件的能力,從而為工件選擇什么類型、哪臺機床提供選擇依據(jù)。映射關(guān)系的建立,可通過本發(fā)明中基于“x”形航空薄壁件標(biāo)準(zhǔn)件的復(fù)雜度計算方法,確定企業(yè)所有機床的加工難度等級,具體方法為:首先使用有限元方法,可以獲取標(biāo)準(zhǔn)件的理論加工復(fù)雜度值,對比標(biāo)準(zhǔn)件在企業(yè)所有可用機床上加工的實驗結(jié)果δc',并對比理論δc,即可獲得并最終構(gòu)建各企業(yè)獨有的機床加工難度系數(shù)與工件復(fù)雜度映射關(guān)系。當(dāng)前第1頁12