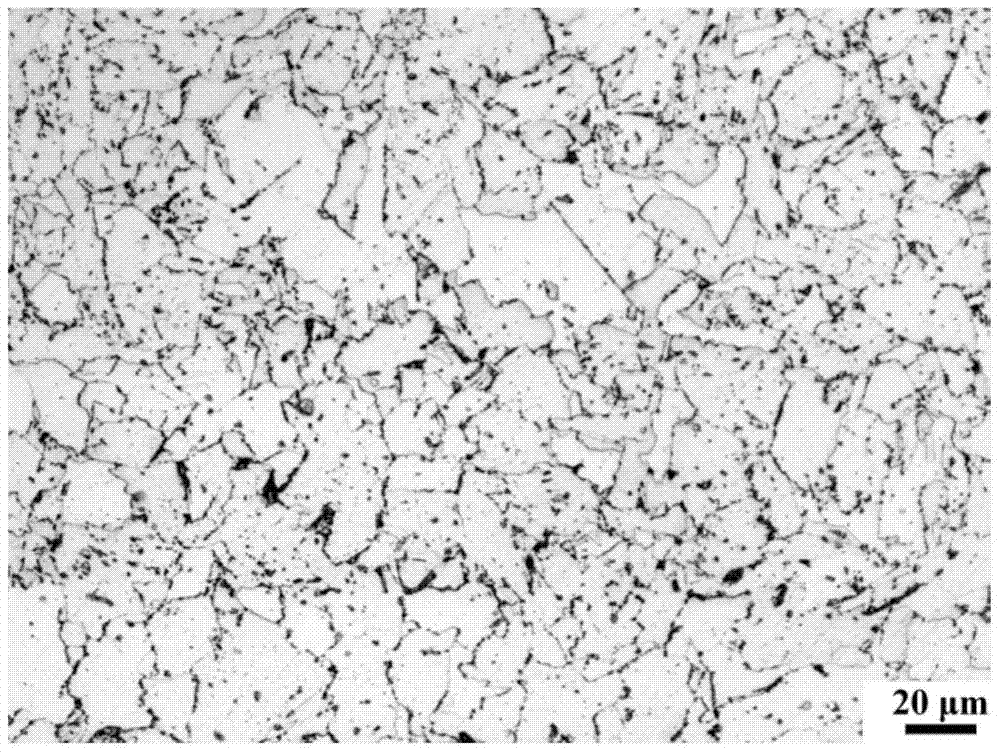
本發(fā)明屬于冶金技術(shù)領(lǐng)域,涉及一種高強(qiáng)度特厚鋼板及其生產(chǎn)方法,具體涉及一種多相納米析出復(fù)合強(qiáng)化型超低碳高強(qiáng)度特厚鋼板及其生產(chǎn)方法。
背景技術(shù):高強(qiáng)鋼是重要的工程結(jié)構(gòu)材料之一,廣泛應(yīng)用于各類工程機(jī)械、礦山機(jī)械、橋梁結(jié)構(gòu)、建筑結(jié)構(gòu)等領(lǐng)域中。隨著高層建筑、跨海橋梁、深海采油平臺、大型水電站等基礎(chǔ)建設(shè)的蓬勃興起,鋼結(jié)構(gòu)不斷向著大型化、重型化發(fā)展,一些鋼結(jié)構(gòu)件形狀越來越復(fù)雜、所承受的約束力也越來越大,普通強(qiáng)度級別、厚度級別的鋼板已不能滿足鋼結(jié)構(gòu)的建設(shè)需要,對高強(qiáng)度、大厚度(≥100mm)鋼板的市場需求越來越大。近年來,礦山機(jī)械、國家體育館、央視主樓等重型機(jī)械和大型建筑的部分構(gòu)件采用了高強(qiáng)度大厚度鋼板,如礦山用的油壓挖掘機(jī)重量達(dá)到300~800噸/臺,使用的鋼板強(qiáng)度達(dá)500~800MPa,厚度達(dá)40~250mm,美國舊金山新海灣大橋使用了最厚140mm的結(jié)構(gòu)鋼板,國內(nèi)深海采油平臺用齒條鋼最大厚度已應(yīng)用到220mm,水電站發(fā)電機(jī)組用鋼的最大厚度已達(dá)到300mm。以上設(shè)備和建筑用鋼不但實(shí)現(xiàn)了強(qiáng)度和厚度的提高,同時(shí)還要求鋼板具有良好的內(nèi)部質(zhì)量和厚度方向性能。高強(qiáng)度特厚鋼板的生產(chǎn)在工藝上主要分為調(diào)質(zhì)和非調(diào)質(zhì)兩種。調(diào)質(zhì)工藝穩(wěn)定性較好,主要是通過馬氏體相變強(qiáng)化來得到高強(qiáng)度。但是,對于100mm以上的大厚度鋼板,由于厚度方向上淬火冷速不同,存在著厚度方向組織性能不均、淬火開裂等問題。非調(diào)質(zhì)工藝主要是熱機(jī)械控制軋制+控制冷卻工藝,綜合利用各種強(qiáng)化手段來得到大厚度和高強(qiáng)度的目的,此方法生產(chǎn)周期較短,制造成本也較低。但是對于大厚度鋼板,也存在著板型較差、厚度方向組織性能不均勻等問題。目前已有不少高強(qiáng)度特厚鋼板的制造專利,從成分上看,專利CN101463449A、CN102080190A等,為了得到高強(qiáng)度,其都是采用中碳成分體系,過高的碳含量對鋼板的焊接性能不利;從工藝上看,目前已有的高強(qiáng)度特厚鋼板專利,基本上都是采用離線/在線淬火+回火的熱處理工藝來獲得高強(qiáng)度,如專利CN101633996A等,淬火工藝受鋼板厚度限制,鋼板越厚,其心部不能淬透,鋼板性能存在板厚效應(yīng),同時(shí)對于高強(qiáng)度特厚鋼板,合金含量較高,淬火易出現(xiàn)開裂;從強(qiáng)化機(jī)制上看,現(xiàn)有專利都是通過得到馬氏體相變強(qiáng)化來達(dá)到高強(qiáng)度的目的,如專利CN102226255A等,而馬氏體相變伴隨著體積膨脹,鋼板中會存在著較大的組織應(yīng)力。因此,現(xiàn)有特厚板的生產(chǎn)技術(shù)存在以下幾個(gè)問題:1)鋼板采用在線/離線淬火/控冷工藝生產(chǎn),鋼板經(jīng)水冷后,由于厚度方向上冷速不同,使得厚度方向上組織性能不均勻,心部和表層組織性能差別較大;2)由于鋼板合金較高,鋼板經(jīng)水冷后內(nèi)應(yīng)力較大,易開裂,且板型難以保證;3)在特厚板的生產(chǎn)中,為了保證鋼板的淬透性,碳含量較高,對焊接不利。
技術(shù)實(shí)現(xiàn)要素:針對現(xiàn)有技術(shù)存在的諸多問題,本發(fā)明的目的在于提出一種高強(qiáng)度特厚鋼板及其生產(chǎn)方法,該發(fā)明無需水冷、無需控制軋制、無需控制冷卻,僅采用超低碳成分,合理匹配Ni、Cu、Al和Ti合金含量,輔以普通軋制+正火+回火工藝,即可得到高強(qiáng)度特厚鋼板。為實(shí)現(xiàn)上述發(fā)明目的,本發(fā)明采用如下技術(shù)方案:一種高強(qiáng)度特厚鋼板,化學(xué)成分以重量百分比計(jì)包括:C0.0025~0.025%,Si0.16~0.36%,Mn0.85~1.15%,Ni2.1~4.5%,Cu0.8~1.2%,Ti0.008~0.035%,Al0.8~1.2%,其余為Fe和不可避免的雜質(zhì)。以下對本發(fā)明的高強(qiáng)度特厚鋼板中所含組分的作用及其用量的選擇具體分析說明:C:C對鋼板的強(qiáng)度、韌性和焊接性能起著重要的作用。C含量過高時(shí),對焊接性能和韌性不利,碳含量較低時(shí),可保證一定的韌性和良好的焊接性,但對強(qiáng)度不利。本發(fā)明中,高強(qiáng)度特厚鋼板的強(qiáng)度不依賴于C,故C含量選擇在0.0025~0.025%。Si:Si可增加鋼的強(qiáng)度,但損害低溫韌性及焊接性能,同時(shí)Si在煉鋼中可起脫氧的作用。本發(fā)明中,高強(qiáng)度特厚鋼板的強(qiáng)度不依賴于Si,Si僅起脫氧的作用,因此Si的含量控制在0.16~0.36%。Mn:Mn在鋼中可提高鋼的淬透性,并起到固溶強(qiáng)化作用,但過高的Mn含量易形成偏析。本發(fā)明中,高強(qiáng)度特厚鋼板的強(qiáng)度基本不依靠Mn的固溶強(qiáng)化,因此Mn的含量控制在0.85~1.15%。Ni、Al、Ti、Cu:Ni能提高鋼的淬透性,顯著改善鋼材的低溫韌性,是提高強(qiáng)韌性的有利元素,Al在鋼中起脫氧作用,Ti在鋼中的作用是固氮和完全脫氧,Cu在鋼中可起到固溶強(qiáng)化作用,回火時(shí)能形成納米富Cu相析出。但在本發(fā)明中,主要是利用Ni與Al、Ti、Cu形成納米級金屬間化合物析出和納米富Cu相析出來提高鋼的強(qiáng)度,故Ni含量控制在2.1~4.5%,Al含量控制在0.8~1.2%,Ti含量控制在0.008~0.035%,Cu含量控制在0.8~1.2%。所述高強(qiáng)度特厚鋼板的生產(chǎn)方法包括以下步驟:(1)按照鋼板的化學(xué)成分,冶煉、澆鑄成鋼錠;(2)加熱工序中,鋼錠加熱溫度為1160~1240℃;(3)軋制工序中,開軋溫度≤1120℃,終軋溫度≥940℃,軋后空冷至室溫;(4)熱處理采用正火+回火工藝,正火溫度為860~920℃,保溫時(shí)間為2~4h;回火溫度為480~540℃,保溫時(shí)間為4~10h。以下對熱處理工藝進(jìn)行詳細(xì)說明:正火工藝:正火是為了使Ni、Cu等合金元素充分固溶于奧氏體中,為后續(xù)時(shí)效析出做準(zhǔn)備。正火溫度過低則Ni、Cu等合金元素不能全溶于奧氏體中,溫度過高則奧氏體晶粒長大嚴(yán)重,對韌性不利,故選擇溫度為860~920℃,保溫時(shí)間為2~4h?;鼗鸸に嚕夯鼗鹗菫榱耸筃i3Al、Ni3Cu、Ni3Ti和富Cu相充分析出,而這些析出物的析出峰值溫度在500~520℃,析出時(shí)間約4-10h。而當(dāng)溫度超過480~540℃這個(gè)范圍或是時(shí)間少于4h時(shí),析出較少或基本不析出,保溫時(shí)間超過10h時(shí),析出基本達(dá)到飽和。故選取回火溫度為480~540℃,保溫時(shí)間為4~10h。進(jìn)一步,所述生產(chǎn)方法制得的鋼板的組織為鐵素體,鐵素體基體中分布有Ni3Al、Ni3Cu、Ni3Ti三種納米級金屬間化合物和富Cu相。進(jìn)一步,所述生產(chǎn)方法制得的鋼板的厚度≥100mm,屈服強(qiáng)度Rp0.2≥900MPa,抗拉強(qiáng)度Rm≥1000MPa,斷后伸長率≥12%。與現(xiàn)有技術(shù)相比,本發(fā)明具有以下有益效果:1、采用超低碳成分,碳含量≤0.025%,合理配置Ni、Cu、Al和Ti合金含量,輔以正火+回火工藝,所制得鋼板的組織...