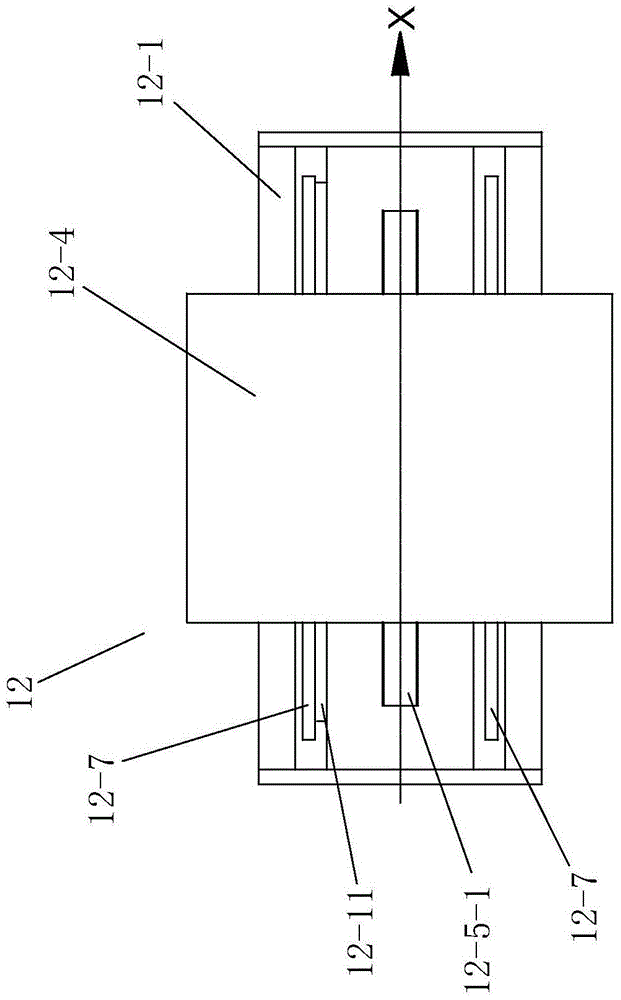
本發(fā)明涉及機械制造領域,具體涉及一種應用平面共軛凸輪輪廓檢測和磨削加工裝置對平面共軛凸輪輪廓進行檢測和磨削的精確控制方法。
背景技術:凸輪機構是主要由凸輪、從動件和機架組成的傳動機構。凸輪按照形式的不同通常分為盤形凸輪、移動凸輪和圓柱凸輪三種。盤形凸輪又分為盤形內凸輪和盤形外凸輪,因為盤形內凸輪很少被采用,故通常所稱的盤形凸輪均指盤形外凸輪。按照從動件的運動軌跡的不同,凸輪又分為平面凸輪和空間凸輪。平面凸輪是指凸輪運動平面與從動件的運動平面互相平行或重合,盤形凸輪和移動凸輪均屬于平面凸輪,而空間凸輪是指從動件的運動軌跡為空間曲線,圓柱凸輪屬于空間凸輪。凸輪按照外部約束形態(tài)的不同又可分為溝槽凸輪、凸緣凸輪、等幅凸輪和共軛凸輪。共軛凸輪通常指相互固結的一對盤形凸輪(也即雙盤形凸輪)。該對凸輪的各自的輪廓(也即凸輪的周向外側表面)分別與同一從動件上相應的運動副元素相接觸。共軛凸輪的2個凸輪按一定位置固裝在同一軸上,使這兩個凸輪各自分別在推程和回程時保持共軛性,進而保證雙盤形凸輪與從動件鎖合。按照從動件的不同的運動形式,雙盤形凸輪又分為擺動從動桿共軛凸輪和直動從動桿共軛凸輪。共軛凸輪的第二種形式是:在同一個環(huán)狀的盤形凸輪上,設置2個盤形輪廓部位,也即在凸輪的周向內側表面和周向外側表面各設有相應的一個凸輪輪廓部位(簡稱為內外輪廓),并且內外輪廓的形狀相似,由于這種共軛凸輪的從動件的運動平面與凸輪運動平面互相平行或重合,故可稱為平面共軛凸輪。平面共軛凸輪可以廣泛應用于各種自動化機械中,如紡織經(jīng)編機、印刷機等,其中紡織經(jīng)編機上鉤針凸輪就是上述定義的平面共軛凸輪。平面共軛凸輪輪廓磨削屬于非圓磨削,輪廓曲線復雜而且內外輪廓尺寸還要保證尺寸共軛一致性,從而磨削加工與檢測難度均較大?,F(xiàn)有技術對平面共軛凸輪輪廓進行磨削加工的設備主要采用數(shù)控加工中心或者專用磨削機床,磨削加工中,還需要對平面共軛凸輪的內外輪廓和加工誤差進行檢測、對內外輪廓磨削余量以及磨削進給量進行確定等,上述的檢測多采用人工在線操作方式或者采用離線檢測方式,不僅檢測精度不高,而很難保證平面共軛凸輪內外輪廓尺寸共軛一致性,還存在磨削加工效率很低的問題。中國專利文獻CN102589469A(申請?zhí)枮?01210026457.0)公開了一種“平面共軛凸輪輪廓檢測裝置及其控制方法”。該文獻所涉及的平面共軛凸輪的檢測裝置雖然可以對平面共軛凸輪的內外輪廓同時進行測量,從而能保證凸輪共軛一致性,但其屬于接觸式測量,測量精度還有待于進一步提高。另外,該測量裝置僅僅只是離線測量裝置,不具有磨削加工的功能。中國專利文獻CN201195276Y(專利申請?zhí)?00820034576.X)公開了一種“在線測試數(shù)控凸輪磨床”。該文獻所述的磨床是一種在對凸輪進行磨削加工的同時還可同步對凸輪進行在線測試的磨床。該文獻中所涉及的凸輪按照其附圖所示,應該為平面盤形凸輪,所以其進行的測量和加工也只是實施在盤形凸輪的輪廓(也即周向外側)上。該文獻的測試雖然是在線自動測試,但是,其測量精度仍較低。中國專利文獻CN102147238B(專利申請?zhí)?01110051991.2)、CN102175181B(專利申請?zhí)?01110051993.1)、CN102122144B(專利申請?zhí)?01110051996.5)和CN102200762B(專利申請?zhí)?01110096390.3)分別公開了一種“凸輪輪廓檢測裝置”、“凸輪輪廓檢測裝置的檢測方法”、“用于凸輪輪廓檢測的數(shù)控系統(tǒng)”和“凸輪輪廓檢測用數(shù)控系統(tǒng)”。所述的這四種檢測裝置或檢測系統(tǒng)工作時,都要先將凸輪從加工設備上取下,然后進行檢測,如檢測不合格,還需將凸輪裝回加工設備重新定位繼續(xù)加工,導致工作效率大大降低,而且所述的檢測的對象都是平面盤形凸輪外輪廓。中國專利文獻CN101434053B(專利申請?zhí)?0081020397.4)、CN101561250B(專利申請?zhí)?00910052043.3)和CN101259596A(專利申請?zhí)?00810023391.3)分別公開了一種“凸輪非圓磨削的自動定位及在線測量方法和裝置”、“大尺寸凸輪非圓磨削智能尋位及在線測量方法”和“一種數(shù)控凸輪磨床”,所述的3篇文獻中的第一篇其在線測量屬于接觸式測量,測量精度低,接觸測量過程中可能造成加工后的凸輪表面受到損傷,而且測量頭易磨損。第二篇文獻其在線測量屬于激光圖像測量,檢測裝置復雜,制造維護成本較高。上述的前2種凸輪輪廓磨削裝置和檢測方法都只用于平面盤形凸輪外輪廓。第三篇文獻則是只能進行加工,檢測時仍需將凸輪將設備上取下通過另外的檢測設備進行檢測。
技術實現(xiàn)要素:本發(fā)明的目的是提出一種對平面共軛凸輪的內外輪廓分別同步磨削和在線檢測的連續(xù)作業(yè)的控制方法。實現(xiàn)本發(fā)明目的的基本技術方案是:一種平面共軛凸輪輪廓檢測和磨削加工裝置的精確控制方法,其特點是:采用的平面共軛凸輪輪廓檢測和磨削加工裝置包括控制系統(tǒng)、機身、設置在機身上的可沿X軸Y軸運動的工作臺機構、固定設置在工作臺機構上的凸輪旋轉機構和固定設置在機身上的檢測磨削裝置。所述控制系統(tǒng)控制工作臺機構、凸輪旋轉機構和檢測磨削裝置的動作。檢測磨削裝置包括磨削機構和在線檢測裝置。上述磨削機構包括磨削工作臺和砂輪磨頭。磨削工作臺固定設置在機身上。在線檢測裝置包括凸輪外輪廓在線檢測裝置和凸輪內輪廓在線檢測裝置。凸輪外輪廓在線檢測裝置包括第一激光測量頭、第一直線電機和第一直線電機驅動器。第一直線電機由其定子固定設置在磨削機構的磨削工作臺的后側上。第一激光測量頭通過第一連接測量桿固定設置在第一直線電機的動子上,由控制系統(tǒng)通過第一直線電機驅動器控制第一直線電機的動子帶動第一激光測量頭進行X向移動測量平面共軛凸輪的外輪廓尺寸。凸輪內輪廓在線檢測裝置包括第二激光測量頭、第二直線電機和第二直線電機驅動器。第二直線電機由其定子固定設置在磨削機構的磨削工作臺的前側上。第二激光測量頭通過第二連接測量桿固定設置在第二直線電機的動子上,由控制系統(tǒng)通過第二直線電機驅動器控制第二直線電機的動子帶動第二激光測量頭進行X向移動測量平面共軛凸輪的內輪廓尺寸。第一激光測量頭、第二激光測量頭與磨削機構的砂輪磨頭處于同一X-Y平面上,且三者的軸線相互平行,并且平面共軛凸輪的軸線位于X-Y平面上。上述第一激光測量頭與砂輪磨頭的軸線的基準間距為Lw,第二激光測量頭與砂輪磨頭的軸線的基準間距為Ls,在所述平面共軛凸輪的旋轉角度為θi時,平面共軛凸輪的安裝軸線與砂輪磨頭的軸線的間距為lui,平面共軛凸輪端面與磨削工作臺Y軸線的間距為lvi,在線測量的平面共軛凸輪的外輪廓與第一激光測量頭的間距測量值為l1i,在線測量的平面共軛凸輪內輪廓與第二激光測量頭的間距測量值為l2i,00≤θi≤3600,θi=360/n,i=1,2,3......,n。n為平面共軛凸輪旋轉一周的過程中同時檢測θi、l1i和l2i測量值的次數(shù)。上述平面共軛凸輪輪廓檢測和磨削加工裝置的精確控制方法具有以下步驟:①、由檢測磨削裝置的在線檢測裝置對平面共軛凸輪內外輪廓尺寸在線測量。在線測量分為平面共軛凸輪磨削前和磨削結束后以及磨削工作中測量。在平面共軛凸輪磨削前和磨削結束后狀態(tài),使平面共軛凸輪旋轉1周以每個θi角度均分做“間歇旋轉”運動,在每個間歇旋轉周期,第一激光測量頭與第二激光測量頭分別也可同時在平面共軛凸輪的軸向輪廓線上做快速往復運動進行測量。在平面共軛凸輪磨削中在線測量,使平面共軛凸輪旋轉1周以每個θi角度均分做緩慢連續(xù)旋轉運動,第一激光測量頭與第二激光測量頭分別在平面共軛凸輪的軸向內外輪廓線上做快速往復運動進行測量。平面共軛凸輪的旋轉速度為1轉/60分至1轉/20分。第一激光測量頭與第二激光測量頭的往復直線運動的速度為3000毫米/分至10000毫米/分。②、根據(jù)測得的平面共軛凸輪的內外輪廓尺寸計算出平面共軛凸輪的外輪廓極坐標徑向尺寸和內輪廓極坐標徑向尺寸并與要加工的平面共軛凸輪的外內輪廓極坐標徑向尺寸進行比較,得出加工誤差和加工余量。然后將平面共軛凸輪外輪廓極坐標徑向尺寸最大值作為平面共軛凸輪磨削的加工零點。然后通過工作臺帶動平面共軛凸輪使外輪廓移向砂輪磨頭處,完成平面共軛凸輪加工零點自動定位。并根據(jù)測量數(shù)據(jù)自動確定粗磨平面共軛凸輪外輪廓的加工進給量。③、根據(jù)步驟②確定的加工進給量由檢測磨削裝置的磨削機構對平面共軛凸輪的外輪廓進行粗磨磨削加工,同時由在線檢測裝置的凸輪內輪廓在線檢測裝置對平面共軛凸輪的內輪廓進行測量。④、完成平面共軛凸輪的外輪廓進行粗磨磨削加工后,回到加工零點,由檢測磨削裝置的磨削機構對平面共軛凸輪的內輪廓進行粗磨磨削加工,同時由在線檢測裝置的凸輪外輪廓在線檢測裝置對平面共軛凸輪的外輪廓進行測量。根據(jù)測量的數(shù)據(jù)計算出下一步精磨平面共軛凸輪外輪廓的加工進給量。⑤、完成平面共軛凸輪的內輪廓的粗磨磨削加工后,回到加工零點,根據(jù)步驟④中的精磨平面共軛凸輪外輪廓的加工進給量由檢測磨削裝置的磨削機構對平面共軛凸輪的外輪廓進行精磨磨削加工,同時由在線檢測裝置的凸輪內輪廓在線檢測裝置對平面共軛凸輪的內輪廓進行測量。根據(jù)測量的數(shù)據(jù)計算出下一步精磨平面共軛凸輪內輪廓的加工進給量。⑥、完成平面共軛凸輪的外輪廓的精磨磨削加工后,回到加工零點,根據(jù)步驟⑤中的精磨平面共軛凸輪內輪廓的加工進給量由檢測磨削裝置的磨削機構對平面共軛凸輪的外輪廓進行精磨磨削加工,同時由在線檢測裝置的凸輪外輪廓在線檢測裝置對平面共軛凸輪的外輪廓進行測量。⑦、完成平面共軛凸輪的內輪廓的精磨磨削加工后,由在線檢測裝置的凸輪內輪廓在線檢測裝置對平面共軛凸輪的內輪廓進行測量并計算出平面共軛凸輪內輪廓極坐標徑向尺寸。根據(jù)步驟⑥中測得的平面共軛凸輪的外輪廓數(shù)據(jù)計算出外輪廓極坐標徑向尺寸。將上述平面共軛凸輪外、內輪廓極坐標徑向尺寸與要加工的平面共軛凸輪外、內輪廓極坐標徑向尺寸進行比較,得出平面共軛凸輪外、內輪廓極坐標徑向尺寸加工誤差判斷加工平面共軛凸輪是否合格,如果需要修復補償可以自動重復上述相應步驟對平面共軛凸輪輪廓進行進一步磨削加工。以上述基本技術方案為基礎的技術方案是:所述步驟①中的第一激光測量頭與第二激光測量頭在平面共軛凸輪的軸向輪廓線上測量一次的時間為0.12秒至2秒。以上述相應技術方案為基礎的技術方案是:所述步驟①中的平面共軛凸輪內外輪廓尺寸在線測量,第一激光測量頭與第二激光測量頭的初始位置在X軸方向各自直線電機定子x1處,并且使第一激光測量頭與第二激光測量頭處于同一沿前后向設置的鉛垂面上。通過工作臺機構沿X軸Y軸運動帶動凸輪旋轉機構使待加工的平面共軛凸輪進入測量位置lui>Ls,lvi=x1且lvi<x2進行測量。以上述技術方案為基礎的技術方案是:所述步驟②測量時以平面共軛凸輪任意位置θi為測量零點,測量使平面共軛凸輪旋轉1周以每個θi角度均分做旋轉運動,在每個凸輪旋轉過程,第一激光測量頭與第二激光測量頭分別在平面共軛凸輪的軸向輪廓線上做快速往復運動進行測量。第一激光測量頭測得此θi位置的1組l1xj軸向外輪廓線數(shù)據(jù),第二激光測量頭測得此θi位置的1組l2xj軸向內輪廓線數(shù)據(jù),其中j為激光測量頭在軸向輪廓線的采樣次數(shù),通過對每組數(shù)據(jù)“去極值”和“平均值”數(shù)據(jù)濾波最終得出該θi位置的l1i和l2i。通過上述方法測得平面共軛凸輪外輪廓和內輪廓的每個θi角度位置的l1i和l2i,以及平面共軛凸輪的安裝軸線與砂輪磨頭軸線的間距坐標lui,可計算得出平面共軛凸輪的外輪廓極坐標徑向尺寸ρ1(θi)=lui+Lw-l1i。平面共軛凸輪的內輪廓極坐標徑向尺寸ρ2(θi)=lui-Ls+l2i。將所述的ρ1(θi)和ρ2(θi)與要加工的平面共軛凸輪的外內輪廓極坐標徑向尺寸ρ1=ρ(θ)和ρ2=ρ(θ)相比較,得出加工誤差和加工余量。將測得的平面共軛凸輪外輪廓極坐標徑向尺寸最大值ρ1max(θi)點作為平面共軛凸輪磨削的加工零點,此時重新定義此處的加工零點尺寸θi=θ0,外輪廓l1i=l10,內輪廓l2i=l20,控制平面共軛凸輪旋轉定位于平面共軛凸輪轉角θ0、外輪廓l10和內輪廓l20,則平面共軛凸輪位于加工零點。上述控制工作臺移動使得平面共軛凸輪端面基準尺寸lvi=x0??刂频谝恢本€電機由其動子帶動第一激光測量頭位于lvi=x1處,控制第二直線電機由其動子帶動第二激光測量頭位于lvi=x1處,同時控制工作臺移動使得平面共軛凸輪的端面位于x0處,完成平面共軛凸輪加工零點自動定位。以上述技術方案為基礎的技術方案是:所述步驟③通過待加工毛坯平面共軛凸輪加工零點定位后,工作臺帶動平面共軛凸輪使外輪廓移向砂輪磨頭處,磨削加工采用控制平面共軛凸輪二軸聯(lián)動數(shù)控插補運動與砂輪磨頭相對旋轉運動實現(xiàn)平面共軛凸輪外輪廓粗磨削。加工進給量根據(jù)上述在線測量平面共軛凸輪毛坯的加工余量確定。在磨削內輪廓的同時,第二激光測量頭在平面共軛凸輪的軸向輪廓線上做往復運動進行測量,測得平面共軛凸輪的軸向內輪廓線數(shù)據(jù)。以上述技術方案為基礎的技術方案是:所述步驟④在完成上述毛坯平面共軛凸輪外輪廓粗磨削后,工作臺帶動平面共軛凸輪回到加工零點θ0處,采用上述平面共軛凸輪外輪廓粗磨削的方法進行平面共軛凸輪內輪廓粗磨削。在磨削平面共軛凸輪內輪廓粗磨削的同時,通過第一激光測量頭完成平面共軛凸輪外輪廓尺寸的測量,即第一激光測量頭在平面共軛凸輪的軸向輪廓線上做往復運動進行測量,測得1組l1xj軸向輪廓線數(shù)據(jù),通過對每組數(shù)據(jù)“去極值”和“平均值”數(shù)據(jù)濾波最終得出該位置的l1i,通過上述公式計算得出ρ1(θi),進而確定下一步精磨外輪廓的加工進給量。以上述技術方案為基礎的技術方案是:所述步驟⑤完成上述毛坯平面共軛凸輪內輪廓粗磨削后,根據(jù)上述確定的精磨外輪廓的加工進給量采用上述平面共軛凸輪外輪廓粗磨削的方法進行平面共軛凸輪外輪廓精磨削。同時通過第二激光測量頭完成內輪廓尺寸的測量,即第二激光測量頭在平面共軛凸輪的軸向輪廓線上做往復運動進行測量,測得1組l2xj軸向輪廓線數(shù)據(jù),通過對每組數(shù)據(jù)“去極值”和“平均值”數(shù)據(jù)濾波最終得出該位置的l2i,通過上述公式計算得出ρ2(θi),進而確定下一步精磨內輪廓的加工進給量。以上述技術方案為基礎的技術方案是:所述步驟⑥根據(jù)上述測得的精磨內輪廓的加工進給量采用步驟④所述的方法進行平面共軛凸輪內輪廓精磨削的同時進行平面共軛凸輪外輪廓尺寸的測量。以上述技術方案為基礎的技術方案是:所述步驟⑦完成精磨平面共軛凸輪的內輪廓后,采取上述的檢測方法檢測平面共軛凸輪的外輪廓尺寸ρ1(θi)和內輪廓尺寸ρ2(θi)。同時將所述的ρ1(θi)和ρ2(θi)與要加工的平面共軛凸輪外內輪廓極坐標徑向尺寸ρ1=ρ(θ)和ρ2=ρ(θ)相比較,得出平面共軛凸輪外內輪廓極坐標徑向尺寸加工誤差判斷加工平面共軛凸輪是否合格,如果需要修復補償可以自動重復上述相應的加工步驟。本發(fā)明具有積極的效果:(1)、本發(fā)明的這種對平面共軛凸輪的每個輪廓交替進行在線測量和磨削的連續(xù)作業(yè)方法,工作時,先可由人工將平面共軛凸輪安裝固定在凸輪旋轉機構上,再由相應的在線檢測裝置對平面共軛凸輪的內外輪廓依次或同時進行初始的在線檢測,或者對內外輪廓的一個輪廓進行初始的在線檢測。然后,即可由控制系統(tǒng)對照預先設定的與相應的測量值所對應的加工余量控制磨削機構對平面共軛凸輪的已測輪廓進行磨削加工??刂葡到y(tǒng)在控制磨削加工某個輪廓的同時,還控制在線檢測裝置對平面共軛凸輪的另一個輪廓進行相應的在線檢測,從而為下一步對該另一個輪廓的磨削加工提供依據(jù)。不需要將平面共軛凸輪從凸輪旋轉機構上卸下即可完成檢測,不僅提高了工作效率,而且能充分保證平面共軛凸輪內外輪廓尺寸的共軛性,同時也有效地提高了測量精度以及加工精度和表面粗糙度等級。(2)、本發(fā)明的在線檢測裝置采用“激光掃描線測”的方法來測量平面共軛凸輪輪廓尺寸,也即分別通過第一激光測量頭和第二激光測量頭對平面共軛凸輪的周向內外側表面在做左右向(也即X方向)的往復運動的同時進行測量,而得到相應的θi位置的2組l1xj和l2xj軸向輪廓線數(shù)據(jù),通過對每組數(shù)據(jù)“去極值”和“平均值”數(shù)據(jù)濾波最終得出該θi位置的l1i和l2i,有效避免了傳統(tǒng)“點測”的測量誤差,進一步提高了測量精度。(3)、平面共軛凸輪的內外輪廓各自由多個不同升程曲線組成,必須在磨削加工前確定一個恰當?shù)哪ハ鞫ㄎ黄瘘c(加工零點)才保證加工精度。另外,還需根據(jù)毛坯尺寸大小的不同確定相應的加工余量,以及根據(jù)加工余量的分布確定平面共軛凸輪輪廓的各個部位的磨削加工進給量。本發(fā)明的方法采用平面共軛凸輪加工零點自動定位和自動檢測平面共軛凸輪的內外輪廓尺寸,在線自動確定平面共軛凸輪粗精磨加工進給量,并能在線測量平面共軛凸輪加工后的加工誤差,實現(xiàn)修復以及刀具磨損診斷功能,改變傳統(tǒng)“靠經(jīng)驗確定加工進給量”和“手工離線檢測”方法,大大提高平面共軛凸輪磨削加工的效率,并能有效地提高加工精度和表面粗糙度等級。附圖說明圖1為采用本發(fā)明的方法的平面共軛凸輪輪廓檢測和磨削加工裝置的結構示意圖;圖2為圖1中的工作臺機構的俯視示意圖;圖3為本發(fā)明的檢測磨削裝置在同時測量平面共軛凸輪毛坯內外輪廓時的測量原理示意圖,圖中的第一激光測量頭和第二激光測量頭在X方向上均位于測量的一個設定的起始位置;圖3的觀察方向與圖1的A向相同;圖4為圖3中的第一激光測量頭測量平面共軛凸輪外輪廓的示意圖,圖中的第一激光測量頭位于測量的一個設定的終止位置;圖5為圖3所示的檢測磨削裝置在對平面共軛凸輪的外輪廓進行磨削的同時還在線測量其內輪廓的示意圖;圖6為圖3所示的檢測磨削裝置在對平面共軛凸輪的內輪廓進行磨削的同時還在線測量其外輪廓的示意圖;圖7為本發(fā)明的控制系統(tǒng)的示意圖;圖8為從圖1的右方觀察時加工好的平面共軛凸輪的示意圖;圖9為控制方法流程圖。上述附圖中的標記如下:平面共軛凸輪輪廓檢測和磨削加工裝置1,機身11,工作臺機構12,X軸底座12-1,Y軸底座12-2,連接座12-3,工作臺12-4,X軸直線電機12-5,定子12-5-1,動子12-5-2,Y軸直線電機12-6,定子12-6-1,動子12-6-2,X軸直線導軌12-7,Y軸直線導軌12-8,X軸直線導軌滑塊12-9,Y軸直線導軌滑塊12-10,X軸移動檢測光柵12-11,Y軸移動檢測光柵12-12,凸輪旋轉機構13,主立柱13-1,第一交流伺服電機13-2,減速箱13-3,角度編碼器13-4,固定螺母13-5,檢測磨削裝置10,磨削機構14,磨削工作臺14-1,第二交流伺服電機14-2,調速箱14-3,砂輪磨頭14-4,在線檢測裝置15,凸輪外輪廓在線檢測裝置15a,第一激光測量頭15-1,第一直線電機15-3,定子15-3-1,動子15-3-2,第一直線電機驅動器15-5,第一連接測量桿15-7,凸輪內輪廓在線檢測裝置15b,第二激光測量頭15-2,第二直線電機15-4,定子15-4-1,動子15-4-2,第二直線電機驅動器15-6,第二連接測量桿15-9,平面共軛凸輪100。具體實施方式本發(fā)明的方位的描述按照圖1所示的方位進行,也即圖1所示的上下左右方向即為描述的上下左右方向,圖1所朝的一方為前方,背離圖1的一方為后方。(實施例1)見圖1和圖2,本實施例的平面共軛凸輪輪廓檢測和磨削的控制方法采用的平面共軛凸輪輪廓檢測和磨削加工裝置1包括控制系統(tǒng)、檢測磨削裝置10、機身11、移動工作臺機構12和凸輪旋轉機構13。移動工作臺機構12設置在機身11上能相對于機身11在X-Y平面上運動,所述X-Y平面為與水平面呈任意夾角的平面(本實施例為水平面,即與水平面的夾角為0度),并且所進行的運動由控制系統(tǒng)控制。凸輪旋轉機構13固定設置在工作臺機構12上且其動作由控制系統(tǒng)控制、檢測磨削裝置10固定設置在機身11上且其動作由控制系統(tǒng)控制。見圖1和圖2,工作臺機構12包括X軸底座12-1、Y軸底座12-2、連接座12-3、工作臺12-4、X軸直線電機12-5、Y軸直線電機12-6、X軸直線導軌12-7、Y軸直線導軌12-8、X軸直線導軌滑塊12-9、Y軸直線導軌滑塊12-10、X軸移動檢測光柵12-11和Y軸移動檢測光柵12-12。X軸底座12-1設置在機身11上,Y軸底座12-2通過連接座12-3與X軸底座12-1呈相互垂直設置。X軸直線導軌滑塊12-9設置在連接座12-3的下側上,X軸直線導軌12-7沿X向設置在X軸底座12-1上側上,X軸直線導軌滑塊12-9從上方向下滑動配合設置在X軸直線導軌12-7上。X軸直線電機12-5的動子12-5-2固定設置在X軸底座12-1上側上,X軸直線電機12-5的定子12-5-1固定設置在連接座12-3的下側上。通過X軸直線電機12-5驅動連接座12-3沿X向水平運動。X軸移動檢測光柵12-11設置在X軸直線導軌12-7的相應部位上與X軸直線電機12-5構成閉環(huán)控制,用來檢測連接座12-3的X軸位移。本實施例的X軸移動檢測光柵12-11采用長春光機數(shù)顯公司SGC系列封閉式光柵。Y軸直線導軌12-8沿Y向設置在Y軸底座12-2下側上,Y軸直線導軌滑塊12-10設置在連接座12-3的上側上,Y軸直線導軌滑塊12-10從下向上滑動配合設置在Y軸直線導軌12-8上。Y軸直線電機12-6的動子12-6-2固定設置在連接座12-3的上側上,Y軸直線電機12-6的定子12-6-1固定設置在Y軸底座12-2的下側上。通過Y軸直線電機12-6驅動Y軸底座12-2沿Y向水平運動。工作臺12-4固定設置在Y軸底座12-2上側上。Y軸移動檢測光柵12-12設置在Y軸直線導軌12-8的相應部位上與Y軸直線電機12-6構成閉環(huán)控制,用來檢測Y軸底座12-2的Y軸位移。本實施例的Y軸移動檢測光柵12-12采用長春光機數(shù)顯公司SGC系列封閉式光柵。本實施例的X軸移動檢測光柵12-11和Y軸移動檢測光柵12-12均采用長春光機數(shù)顯公司SGC系列封閉式光柵。本實施例中X軸直線電機12-5和Y軸直線電機12-6均采用科爾摩根公司的直接驅動直線電機(DDL)系列。見圖1,凸輪旋轉機構13包括主立柱13-1、第一交流伺服電機13-2、減速箱13-3、角度編碼器13-4和固定螺母13-5。主立柱13-1鉛垂固定設置在工作臺機構12的工作臺12-4上。第一交流伺服電機13-2固定設置在主立柱13-1上。減速箱13-3固定設置在主立柱13-1上。減速箱13-3的輸出軸沿X向設置,且朝向右方。角度編碼器13-4同軸設置在輸出軸的左端上,本實施例的角度編碼器13-4采用無錫瑞普ZKT11系列光電編碼器。固定螺母13-5旋合在輸出軸的右端上,并將平面共軛凸輪100夾緊固定在輸出軸右端相應部位上。由第一交流伺服電機13-2驅動減速箱13-3并通過減速箱13-3的輸出軸帶動平面共軛凸輪100繞C軸旋轉,由角度編碼器13-4測量平面共軛凸輪100的旋轉角度。見圖1、圖3、圖5和圖6,檢測磨削裝置10包括磨削機構14和在線檢測裝置15。磨削機構14包括磨削工作臺14-1、第二交流伺服電機14-2、調速箱14-3和砂輪磨頭14-4。磨削工作臺14-1固定設置在機身11上。調速箱14-3固定在磨削工作臺14-1上,調速箱14-3的輸出軸沿X向設置,且朝向左方。砂輪磨頭14-4固定設置在調速箱14-3的輸出軸的左端上。第二交流伺服電機14-2固定設置在磨削工作臺14-1上,第二交流伺服電機14-2與調速箱14-3的輸入軸連接,由第二交流伺服電機14-2驅動調速箱14-3并通過調速箱14-3的輸出軸帶動砂輪磨頭14-4轉動,并由控制系統(tǒng)控制第二交流伺服電機14-2的轉速來調節(jié)砂輪磨頭14-4的磨削加工速度。本實施例中的第一交流伺服電機和第二交流伺服電機均采用施耐德公司的Lexium23D系列交流伺服電機。見圖1、圖3、圖5和圖6,在線檢測裝置15包括凸輪外輪廓在線檢測裝置15a和凸輪內輪廓在線檢測裝置15b。凸輪外輪廓在線檢測裝置15a包括第一激光測量頭15-1、第一直線電機15-3和第一直線電機驅動器15-5。第一直線電機15-3由其定子15-3-1固定設置在磨削機構14的磨削工作臺14-1的后側上。第一激光測量頭15-1通過第一連接測量桿15-7固定設置在第一直線電機15-3的動子15-3-2上,由控制系統(tǒng)通過第一直線電機驅動器15-5控制第一直線電機15-3的動子15-3-2帶動第一激光測量頭15-1進行X向移動測量平面共軛凸輪的外輪廓尺寸。凸輪內輪廓在線檢測裝置15b包括第二激光測量頭15-2、第二直線電機15-4和第二直線電機驅動器15-6。第二直線電機15-4由其定子15-4-1固定設置在磨削機構14的磨削工作臺14-1的前側上。第二激光測量頭15-2通過第二連接測量桿15-9固定設置在第二直線電機15-4的動子15-4-2上,由控制系統(tǒng)通過第二直線電機驅動器15-6控制第二直線電機15-4的動子15-4-2帶動第二激光測量頭15-2進行X向移動測量平面共軛凸輪的內輪廓尺寸。第一激光測量頭15-1、第二激光測量頭15-2與磨削機構14的砂輪磨頭14-4處于同一X-Y平面上,且三者的軸線相互平行,并且平面共軛凸輪的軸線位于X-Y平面上。本實施例的第一激光測量頭15-1和第二激光測量頭15-2均采用美國Banner公司L-GAGELH系列激光測距位移傳感器,該傳感器測量精度最小能達到1μm。本實施例中的第一直線電機和第二直線電機均采用科爾摩根公司的直接驅動直線電機(DDL)系列。當平面共軛凸輪輪廓檢測和磨削加工裝置1由其檢測磨削裝置10的磨削機構14的砂輪磨頭14-4對平面共軛凸輪100的外輪廓進行磨削加工時,由凸輪內輪廓檢測裝置15b的第二激光測量頭15-2沿平面共軛凸輪100的軸向做往復運動并對平面共軛凸輪100內輪廓軸向上的輪廓線進行測量;當平面共軛凸輪輪廓檢測和磨削加工裝置1由其檢測磨削裝置10的磨削機構14的砂輪磨頭14-4對平面共軛凸輪100的內輪廓進行磨削加工時,由凸輪外輪廓檢測裝置15a的第一激光測量頭15-1在平面共軛凸輪100的軸向上做往復運動并對平面共軛凸輪100外輪廓軸向上的輪廓線進行測量,當凸輪旋轉一周,則檢測磨削裝置10能同時對平面共軛凸輪100的內外輪廓中的一個輪廓的尺寸在周向上進行在線檢測和對平面共軛凸輪100的內外輪廓中的另一個輪廓進行磨削。見圖7,控制系統(tǒng)包括高速計數(shù)卡、激光位移傳感器采集卡、運動控制卡、工控機、PLC、開關量檢測控制模塊、故障檢測模塊和觸摸屏人機接口。本實施例的高速計數(shù)卡采用研華公司PCI-1784U,激光位移傳感器采集卡采用研華公司PCI-1710HGU,運動控制卡采用研華公司PCI-1245,工控機采用研華ARK系列嵌入式工控機,PLC采用施耐德公司的M258高性能PLC。X軸移動檢測光柵12-11、Y軸移動檢測光柵12-12和角度編碼器13-4與高速計數(shù)卡信號電連接,高速計數(shù)卡與工控機信號電連接。高速計數(shù)卡用于采集X軸移動檢測光柵12-11和Y軸移動檢測光柵12-12檢測的XY軸位移信號和角度編碼器13-4檢測的平面共軛凸輪100旋轉角度信號,再把采集的信號輸入到工控機。第一激光測量頭21和第二激光測量頭22與激光位移傳感器采集卡信號電連接,激光位移傳感器采集卡與工控機信號電連接。激光位移傳感器采集卡用于采集第一激光測量頭15-1實時檢測的第一激光測量頭21與平面共軛凸輪100外輪廓之間的距離信號和第二激光測量頭15-2實時檢測的第二激光測量頭22與平面共軛凸輪100內輪廓之間的距離信號,并將信號輸入到工控機。X軸直線電機驅動器、Y軸直線電機驅動器、第一交流伺服電機13-2、第二交流伺服電機14-2、第一直線電機驅動器15-5和第二直線電機驅動器15-6與運動控制卡信號電連接。運動控制卡通過X軸直線電機驅動器控制X軸直線電機12-5的動作,進而控制工作臺12-4在X向上的動作;運動控制卡通過Y軸直線電機驅動器控制Y軸直線電機12-6的動作,進而控制工作臺12-4在Y向上的動作。運動控制卡通過第一交流伺服電機驅動器控制第一交流伺服電機13-2的動作,進而控制平面共軛凸輪100繞C軸旋轉動作。運動控制卡通過第二交流伺服電機驅動器控制第二交流伺服電機14-2的動作,進而控制砂輪磨頭14-4的動作。運動控制卡通過第一直線電機驅動器15-5控制第一直線電機15-3動作,進而控制第一激光測量頭15-1在X向上的動作。運動控制卡通過第二直線電機驅動器26控制第二直線電機15-4動作,進而控制第二激光測量頭15-2在X向上的動作。運動控制卡與工控機信號電連接。工控機通過通訊接口與PLC相連。故障檢測模塊與PLC信號電連接;開關量檢測控制模塊與PLC雙向信號電連接;觸摸屏人機接口與PLC雙向信號電連接。見圖3和圖4,第一激光測量頭15-1與砂輪磨頭14-4的軸線的基準間距為Lw,第二激光測量頭15-6與砂輪磨頭14-4的軸線的基準間距為Ls,在所述平面共軛凸輪100的旋轉角度為θi時,平面共軛凸輪100的安裝軸線與砂輪磨頭14-4的軸線的間距為lui,平面共軛凸輪100端面與磨削工作臺14-1Y軸線的間距為lvi,在線測量的平面共軛凸輪100的外輪廓與第一激光測量頭15-1的間距測量值為l1i,在線測量的平面共軛凸輪100內輪廓與第二激光測量頭15-2的間距測量值為l2i,00≤θi≤3600,θi=360/n,i=1,2,3......,n;n為平面共軛凸輪100旋轉一周的過程中同時檢測θi、l1i和l2i測量值的次數(shù),n的值越大,測得的平面共軛凸輪100內外輪廓的極坐標徑向尺寸數(shù)據(jù)越精確。見圖3至圖9,上述平面共軛凸輪輪廓檢測和磨削加工裝置的精確控制方法包括以下步驟:①、平面共軛凸輪內外輪廓尺寸在線測量:在線測量分為平面共軛凸輪100磨削前和磨削結束后以及磨削工作中測量;在平面共軛凸輪100磨削前和磨削結束后狀態(tài),使平面共軛凸輪100旋轉1周以每個θi角度均分做“間歇旋轉”運動,在每個間歇旋轉周期,第一激光測量頭15-1與第二激光測量頭15-2分別也可同時在平面共軛凸輪100的軸向輪廓線上做快速往復運動進行測量;在平面共軛凸輪100磨削中在線測量,使平面共軛凸輪100旋轉1周以每個θi角度均分做緩慢連續(xù)旋轉運動,第一激光測量頭15-1與第二激光測量頭15-2分別在平面共軛凸輪100的軸向內外輪廓線上做快速往復運動進行測量;平面共軛凸輪100的旋轉速度為1轉/60分至1轉/20分;第一激光測量頭15-1與第二激光測量頭15-2的往復直線運動的速度為3000毫米/分至10000毫米/分;第一激光測量頭15-1與第二激光測量頭15-2在平面共軛凸輪100的軸向輪廓線上測量一次的時間為0.12秒至2秒。第一激光測量頭15-1與第二激光測量頭15-2的初始位置在X軸方向各自直線電機定子x1處,并且使第一激光測量頭15-1與第二激光測量頭15-2處于同一沿前后向設置的鉛垂面上。通過工作臺機構12沿X軸Y軸運動帶動凸輪旋轉機構13使待加工的毛坯平面共軛凸輪100進入測量位置lui>Ls,lvi=x1且lvi<x2進行測量。②、平面共軛凸輪加工零點自動定位:測量時以平面共軛凸輪100任意位置θi為測量零點,測量使平面共軛凸輪100旋轉1周以每個θi角度均分做旋轉運動(凸輪磨削前后做間歇旋轉運動,凸輪磨削中做緩慢旋轉運動),在每個凸輪旋轉過程,第一激光測量頭15-1與第二激光測量頭15-2分別在平面共軛凸輪100的軸向輪廓線上做快速往復運動進行測量。第一激光測量頭15-1測得此θi位置的1組l1xj軸向外輪廓線數(shù)據(jù),第二激光測量頭15-2測得此θi位置的1組l2xj軸向內輪廓線數(shù)據(jù),其中j為激光測量頭在軸向輪廓線的采樣次數(shù),通過對每組數(shù)據(jù)“去極值”和“平均值”數(shù)據(jù)濾波最終得出該θi位置的l1i和l2i。這種“激光掃描線測”平面共軛凸輪輪廓尺寸的測量方法可避免傳統(tǒng)“點測”的測量誤差,有效提高測量精度。通過上述方法測得平面共軛凸輪100外輪廓和內輪廓的每個θi角度位置的l1i和l2i,以及平面共軛凸輪100的安裝軸線與砂輪磨頭14-4軸線的間距坐標lui,可計算得出平面共軛凸輪100的外輪廓極坐標徑向尺寸ρ1(θi)=lui+Lw-l1i;平面共軛凸輪100的內輪廓極坐標徑向尺寸ρ2(θi)=lui-Ls+l2i。將所述的ρ1(θi)和ρ2(θi)與要加工的平面共軛凸輪100的外內輪廓極坐標徑向尺寸ρ1=ρ(θ)和ρ2=ρ(θ)相比較,得出加工誤差和加工余量。將測得的平面共軛凸輪100外輪廓極坐標徑向尺寸最大值ρ1max(θi)點作為平面共軛凸輪100磨削的加工零點,此時重新定義此處的加工零點尺寸θi=θ0,外輪廓l1i=l10,內輪廓l2i=l20,控制平面共軛凸輪100旋轉定位于平面共軛凸輪100轉角θ0、外輪廓l10和內輪廓l20,則平面共軛凸輪100位于加工零點;控制工作臺12-4移動使得平面共軛凸輪100端面基準尺寸lvi=x0。控制第一直線電機15-3由其動子帶動第一激光測量頭15-1位于lvi=x1處,控制第二直線電機15-4由其動子帶動第二激光測量頭15-2位于lvi=x1處,同時控制工作臺12-4移動使得平面共軛凸輪100的端面位于x0處,完成平面共軛凸輪100加工零點自動定位。③、平面共軛凸輪外輪廓粗磨及自動確定平面共軛凸輪內輪廓粗磨加工余量:通過上述毛坯平面共軛凸輪100加工零點定位后,工作臺12-4帶動平面共軛凸輪100使外輪廓移向砂輪磨頭14-4處,磨削加工采用控制平面共軛凸輪100二軸聯(lián)動數(shù)控插補運動(也即工作臺Y軸移動和凸輪旋轉軸C軸轉動)與砂輪磨頭11相對旋轉運動實現(xiàn)平面共軛凸輪100外輪廓粗磨削。加工進給量根據(jù)上述在線測量平面共軛凸輪100毛坯的加工余量確定。同時采用“輪廓同步磨削和在線檢測連續(xù)作業(yè)加工工藝”即在磨削平面共軛凸輪100外輪廓的同時,第二激光測量頭15-2在平面共軛凸輪100的軸向輪廓線上做往復運動進行測量,測得平面共軛凸輪100的軸向內輪廓線數(shù)據(jù)。④、平面共軛凸輪內輪廓粗磨及自動確定平面共軛凸輪外輪廓精磨加工余量:完成上述毛坯平面共軛凸輪100外輪廓粗磨削后,工作臺12-4帶動平面共軛凸輪100回到加工零點θ0處,采用上述平面共軛凸輪100外輪廓粗磨削的方法進行平面共軛凸輪100內輪廓粗磨削。同時采用“輪廓同步磨削和在線檢測連續(xù)作業(yè)加工工藝”,即在磨削平面共軛凸輪100內輪廓粗磨削的同時,通過第一激光測量頭15-1完成平面共軛凸輪100外輪廓尺寸的測量,即第一激光測量頭15-1在平面共軛凸輪100的軸向輪廓線上做往復運動進行測量,測得1組l1xj軸向輪廓線數(shù)據(jù),通過對每組數(shù)據(jù)“去極值”和“平均值”數(shù)據(jù)濾波最終得出該位置的l1i,通過上述公式計算得出ρ1(θi),進而確定下一步精磨外輪廓的加工進給量。⑤、平面共軛凸輪外輪廓精磨及自動確定平面共軛凸輪內輪廓精磨加工余量:完成上述毛坯平面共軛凸輪100內輪廓粗磨削后,根據(jù)上述確定的精磨外輪廓的加工進給量采用上述平面共軛凸輪100外輪廓粗磨削的方法進行平面共軛凸輪100外輪廓精磨削。同時通過第二激光測量頭15-2完成內輪廓尺寸的測量,即第二激光測量頭15-2在平面共軛凸輪100的軸向輪廓線上做往復運動進行測量,測得1組l2xj軸向輪廓線數(shù)據(jù),通過對每組數(shù)據(jù)“去極值”和“平均值”數(shù)據(jù)濾波最終得出該位置的l2i,通過上述公式計算得出ρ2(θi),進而確定下一步精磨內輪廓的加工進給量。⑥、平面共軛凸輪內輪廓精磨及自動檢測平面共軛凸輪外輪廓尺寸:根據(jù)上述測得的精磨內輪廓的加工進給量采用步驟④所述的方法進行平面共軛凸輪100內輪廓精磨削的同時進行平面共軛凸輪100外輪廓尺寸的測量。⑦、平面共軛凸輪內外輪廓尺寸在線誤差測量及修復補償:完成精磨平面共軛凸輪(100)的內輪廓后,采取上述的檢測方法檢測平面共軛凸輪100外輪廓尺寸ρ1(θi)和內輪廓尺寸ρ2(θi)。同時將所述的ρ1(θi)和ρ2(θi)與要加工的平面共軛凸輪100外內輪廓極坐標徑向尺寸ρ1=ρ(θ)和ρ2=ρ(θ)相比較,得出平面共軛凸輪100外內輪廓極坐標徑向尺寸加工誤差判斷加工平面共軛凸輪100是否合格,如果需要修復補償可以自動重復上述相應的加工步驟。如果在批量平面共軛凸輪加工后檢測都出現(xiàn)誤差過大,說明此時砂輪磨頭磨損嚴重,可以針對加工誤差的余量,對砂輪磨頭進行適量的進給補償。如果補償后還出現(xiàn)明顯的加工誤差,系統(tǒng)提示砂輪磨頭磨損嚴重,需要更換砂輪磨頭刀具。以上實施例僅供說明本發(fā)明之用,而非對本發(fā)明的限制,有關技術領域的技術人員在不脫離本發(fā)明的精神和范圍的情況下,還可以作出各種變換和變化,具體應用過程中還可以根據(jù)上述實施例的啟發(fā)進行相應的改造,因此所有等同的技術方案均應該歸入本發(fā)明的專利保護范圍之內。