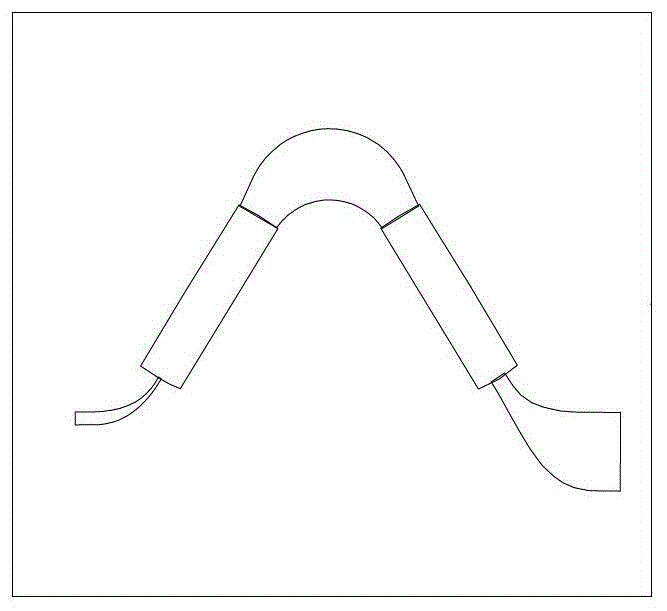
本發(fā)明涉及光通信用波分復(fù)用/解復(fù)用器的切割方法,更具體地是涉及一種曲線型陣列波導(dǎo)光柵芯片的分割方法以及切割用夾具,本發(fā)明屬于通信領(lǐng)域。
背景技術(shù):陣列波導(dǎo)光柵(AWG)是實(shí)現(xiàn)多通道密集波分復(fù)用(DWDM)光網(wǎng)絡(luò)的最理想器件。1988年,荷蘭Delft大學(xué)的Smit首先提出AWG的概念,它的基本功能是進(jìn)行波長的合波/分波,憑借其通道數(shù)多、體積小、易于與其它器件集成、價(jià)格低的優(yōu)勢已經(jīng)取代傳統(tǒng)的TFF的密集波分復(fù)用/解復(fù)用器,在骨干網(wǎng)和城域網(wǎng)中得到了廣泛的商用多年;另外,AWG能靈活地與其它光器件構(gòu)成多功能器件和模塊,如波長路由器、光分插復(fù)用器、多波長光源、光波長選擇器(OWS)、多波長接收器、多信道均衡器等。AWG器件是以光集成技術(shù)為基礎(chǔ)的平面波導(dǎo)型器件,具有高穩(wěn)定性及好的性價(jià)比,適宜于批量生產(chǎn),重復(fù)性好,尺寸小,插入損耗均勻性較好,易于與其它器件集成等特點(diǎn),是目前DWDM系統(tǒng)中商用的主流復(fù)用/解復(fù)用器。AWG的波導(dǎo)制作材料主要有SiO2、InGaAsP、Polymer和Si,其中硅基二氧化硅光波導(dǎo)集成技術(shù)由于具有成熟的半導(dǎo)體工藝技術(shù)基礎(chǔ)、與光纖耦合效率好、成本低廉等優(yōu)勢,已經(jīng)成為AWG芯片生產(chǎn)廠家普遍采用的主流技術(shù)。光通信用器件的價(jià)格每年約降低10%,成本是每個(gè)器件供應(yīng)商必須考慮的重要因素。尤其對(duì)已經(jīng)商用多年的AWG芯片,許多研究者已經(jīng)提出了多種方案來降低成本,其中,減小芯片尺寸是一種有效的降低成本的手段。目前已報(bào)道的專利文獻(xiàn),減小芯片尺寸的方案主要有兩種:提高波導(dǎo)的折射率差、優(yōu)化AWG結(jié)構(gòu)本身圖案。優(yōu)化結(jié)構(gòu)圖案有個(gè)極限、提高折射率差對(duì)設(shè)計(jì)及工藝都需要重大技術(shù)突破。目前AWG芯片的外形輪廓都是方形,針對(duì)這種問題,本發(fā)明提出了一種簡單的曲線切割方案來減小AWG芯片的尺寸,切割后的AWG芯片的外形輪廓為曲線型,并且芯片的性能指標(biāo)、穩(wěn)定性與方形芯片完全相同。如圖1所示,陣列波導(dǎo)光柵由N個(gè)輸入波導(dǎo)、M個(gè)輸出波導(dǎo)和兩個(gè)波導(dǎo)星形耦合器及一個(gè)相鄰波導(dǎo)間具有恒定路徑長度差的波導(dǎo)陣列組成。輸入光從第一個(gè)星形耦合器的輸入端同一輸入波導(dǎo)輸入,該耦合器把光功率分配到每一個(gè)陣列波導(dǎo)中,由于波導(dǎo)陣列中的波導(dǎo)長度不等,產(chǎn)生不同的相位延遲,在輸出星型耦合波導(dǎo)中相干疊加,從而表現(xiàn)出光柵的功能和特性,輸出端口與波長有一一對(duì)應(yīng)的關(guān)系。不同光波長組成的入射光束經(jīng)陣列波導(dǎo)光柵傳輸后,依波長的不同出現(xiàn)在不同的波導(dǎo)端口上。精確設(shè)計(jì)陣列波導(dǎo)的長度差,可以使不同波長的信號(hào)從不同的輸出端口輸出,從而起到解復(fù)用器的作用。以圓形的陣列波導(dǎo)光柵晶圓片為基底,在其上依次通過熱氧化、下包層沉積、波導(dǎo)芯層沉積、光刻、刻蝕和上包層沉積、表面鈍化、退火等工藝,在整個(gè)陣列波導(dǎo)光柵晶圓片上一次性制作出多個(gè)AWG芯片;然后將包含有多個(gè)AWG的陣列波導(dǎo)光柵晶圓片用切割設(shè)備切割成單個(gè)的芯片。受限于采用的切割技術(shù),目前已知的切割技術(shù)是采用機(jī)械運(yùn)動(dòng)的方式進(jìn)行切割,只能進(jìn)行直線切割,因此陣列波導(dǎo)光柵晶圓片上的多個(gè)AWG只能低密度地分開排放,見圖1,AWG芯片包括輸入波導(dǎo)2、陣列波導(dǎo)3、輸出波導(dǎo)4、平板波導(dǎo)5。直線切割后的AWG芯片只能是方形的輪廓,見圖2,如果AWG芯片的外形輪廓為方形,那么單個(gè)襯底基片可以排放的芯片總個(gè)數(shù)有限,這種直線切割技術(shù)浪費(fèi)了大量可用空間。
技術(shù)實(shí)現(xiàn)要素:本發(fā)明的目的克服現(xiàn)有技術(shù)存在的技術(shù)缺陷,提供一種曲線型陣列波導(dǎo)光柵芯片的分割方法以及切割用夾具,采用本發(fā)明方法可以能大大減小芯片尺寸,進(jìn)一步降低芯片成本。本發(fā)明所采用的技術(shù)方案是:一種曲線型陣列波導(dǎo)光柵芯片的切割方法,陣列波導(dǎo)光柵芯片位于陣列波導(dǎo)光柵圓晶,包括如下步驟:步驟1:沿陣列波導(dǎo)光柵芯片輸入端和輸出端側(cè)面將陣列波導(dǎo)光柵晶圓分切成條狀硅晶芯片;步驟2:在條狀硅晶芯片中的單個(gè)陣列光柵芯片表面外圍制作凹槽,該凹槽是一個(gè)連接整體凹槽體,或者是由多個(gè)排列緊密的凹槽單體組成的凹槽體;步驟3:對(duì)暴露在外的條狀硅晶芯片表面進(jìn)行保護(hù)處理;步驟4:采用夾具將條狀硅晶芯片固定于切割臺(tái);步驟5:沿著條狀硅晶芯片的陣列光柵芯片外圍凹槽的曲線方向進(jìn)行激光劃片。所述步驟1和步驟2之間有步驟A:在條狀硅晶芯片有圖形一面沿步驟1切割后的邊沿,將蓋片平行對(duì)齊粘貼在條狀硅晶芯片的輸入以及輸出端兩側(cè);所述步驟A中蓋片粘接位置需要考慮蓋片8°角或15°角的拋光距離,且蓋片突出于條狀硅晶芯片邊緣表面1~2mm。所述步驟2中的凹槽的槽體是U槽或者V槽或者矩形槽。所述凹槽槽體寬度為100-600um,其深度<500um。所述步驟3的保護(hù)處理方式采用在條狀硅晶芯片表面表面涂膠的化學(xué)方式處理。所述步驟3的保護(hù)處理方式可以采用在條狀硅晶芯片正表面粘貼耐熱膠帶紙,耐熱膠帶紙覆蓋蓋片之外的區(qū)域。所述步驟5中激光劃片采用紅外光頻段波長進(jìn)行切割,功率為80~120W,脈沖釋放時(shí)間控制在2~8us之間。所述方法使用的夾具,所述夾具包括上底板夾具和基板夾具,所述基板夾具上設(shè)置有一個(gè)凸臺(tái),上底板夾具上表面開有凹臺(tái),該凹臺(tái)區(qū)域包括中部凹臺(tái)區(qū)域和邊緣凹臺(tái)區(qū)域,中部凹臺(tái)區(qū)域同條狀硅晶芯片的形狀相匹配,邊緣凹臺(tái)區(qū)域是上底板夾具的邊緣且同中部凹臺(tái)區(qū)域相通的相隔設(shè)置的第二凹槽,上底板夾具底部間隔設(shè)置有多個(gè)第一凹槽,基板夾具的凸臺(tái)寬度因與第一凹槽尺寸相匹配。所述第二凹槽寬度小于上底板夾具底部的第一凹槽之間距離。所述中部凹臺(tái)區(qū)域由間隔分布的凹臺(tái)組成。本發(fā)明具有如下特點(diǎn):1、本發(fā)明的曲線型陣列波導(dǎo)光柵芯片及其切割方法,是采用激光切割、Water-Jet水切割或線切割的曲線切割技術(shù),而激光切割方案又根據(jù)激光器不同又分為光纖激光切割方案,半導(dǎo)體固體激光切割方案以及LED激光方案等等,本發(fā)明采用激光切割中的半導(dǎo)體固體激光切割方案將含有多個(gè)陣列波導(dǎo)光柵芯片切割成單個(gè)的芯片,從而實(shí)現(xiàn)切割后的陣列波導(dǎo)光柵芯片具有曲線型的外形輪廓,減小芯片尺寸,降低成本;2、本發(fā)明采用激光切割、Water-Jet水切割或線切割的曲線切割技術(shù),實(shí)現(xiàn)針對(duì)陣列波導(dǎo)光柵芯片種類多樣化的低成本,高效率的實(shí)施方案;3、本發(fā)明采用預(yù)切割的方式,可以最大程度減少傳統(tǒng)固體激光切割過程中高溫氣化以及熱應(yīng)力帶來對(duì)芯片指標(biāo)的影響。附圖說明圖1是現(xiàn)有技術(shù)采用直線切割技術(shù)AWG芯片排放示意圖;圖2是現(xiàn)有技術(shù)的直線切割后的方形AWG芯片示意圖;圖3是本發(fā)明陣列波導(dǎo)光柵晶圓片上AWG的密集排放示意圖;圖4是本發(fā)明采用直線切割處理后的條狀硅晶片示意圖;圖5-1A是本發(fā)明條狀硅晶片上覆蓋第一種結(jié)構(gòu)蓋板的示意圖;圖5-1B是本發(fā)明條狀硅晶片上覆蓋第一種結(jié)構(gòu)蓋板的放大圖;圖5-2A是本發(fā)明本發(fā)明條狀硅晶片上覆蓋第二種結(jié)構(gòu)蓋板的示意圖;圖5-2B是本發(fā)明本發(fā)明條狀硅晶片上覆蓋第二種結(jié)構(gòu)蓋板的示意圖;圖6是本發(fā)明處理之后的條狀硅晶片側(cè)視圖;圖7-1是本發(fā)明采用的夾具的上底俯視示意圖;圖7-2是本發(fā)明采用的夾具的第二種上底俯視示意圖;圖8是是本發(fā)明采用的上底板夾具側(cè)視視示意圖。圖9是本發(fā)明采用的基板夾具的俯視示意圖;圖10是本發(fā)明采用的基板夾具的側(cè)視示意圖。圖11是本發(fā)明采用的夾具裝配示意圖圖12是根據(jù)不同制作要求部分沿著陣列波導(dǎo)光柵圖案的邊緣切割后的曲線型芯片示意圖。其中:1:陣列波導(dǎo)光柵晶圓片;2:輸入波導(dǎo);3:陣列波導(dǎo);4:輸出波導(dǎo);5:平板波導(dǎo);6:條狀硅晶芯片7:蓋片;8:凹槽;9:耐熱膠帶紙;10:中部凹臺(tái)區(qū)域;11:邊緣凹臺(tái)區(qū)域;12:夾具;13:上底板夾具;14:基板夾具;15:第一凹槽;16:凸臺(tái);17:第二凹槽;A:上底板夾具底部的第一凹槽15之間的距離;B:第二凹槽17的寬度;具體實(shí)施方式下面結(jié)合實(shí)施例對(duì)本發(fā)明的曲線型陣列波導(dǎo)光柵芯片及其切割方法做出詳細(xì)說明。步驟1:采用傳統(tǒng)機(jī)械切片設(shè)備沿芯片輸入端和輸出端側(cè)面將如圖3所示的陣列波導(dǎo)光柵晶圓片1分切成條狀的條狀硅晶芯片6,一般分切為2條到3條,這樣處理后的條狀硅晶芯片可以方便于之后的陣列波導(dǎo)光柵芯片條的芯片指標(biāo)測試以及激光外型曲線切割。經(jīng)過該步驟處理后的條狀硅晶芯片結(jié)構(gòu)如圖4所示;步驟2、粘貼條狀蓋片7。在條狀硅晶芯片有圖形一面,沿步驟1切割后的邊沿,將蓋片7平行對(duì)齊粘貼在條狀硅晶芯片的正表面之上,位于條狀硅晶芯片的輸入以及輸出端兩側(cè)。蓋片粘接位置需要考慮蓋片8°角或15°角或其他特殊角度的拋光距離,蓋片7一般突出于條狀硅晶芯片邊緣表面1~2mm。蓋片7可采用高硼硅玻璃、石英以及硅材料等。預(yù)先粘貼蓋片工藝,便于芯片在之后工藝過程中起到更好的對(duì)準(zhǔn)定位,也起到了保護(hù)輸入輸出波導(dǎo)端,減少芯片切割過程中清洗清潔的步驟。所述蓋片7粘接用于陣列波導(dǎo)光柵芯片與光纖陣列的芯片指標(biāo)測試以及之后的耦合工藝步驟,同時(shí)便于曲線切割后的單個(gè)陣列波導(dǎo)光柵芯片與熱敏電阻或者金屬底板或者其他材料的粘接定位。如圖5-1A、圖5-1B中蓋片7覆蓋波導(dǎo)圖形部分。蓋片7寬度尺寸根據(jù)拋光工藝決定。厚度尺寸一般為1~1.5mm。若使用多段等長度短條蓋片7,蓋片與蓋片之間留有一定距離,跟據(jù)蓋片7尺寸大小,距離可為500~1500um。如圖5-2A、圖5-2B所示,也可采用粘接整條蓋片7的工藝完全覆蓋條狀硅晶芯片邊緣,但需要采用傳統(tǒng)機(jī)械切片設(shè)備在單個(gè)陣列波導(dǎo)光柵芯片之間位置開出一定寬度以及深度的凹槽,凹槽不宜太淺,否則之后所用的激光切割方式無法將其切透。步驟3、凹槽8處理:在條狀硅晶芯片表面,沿著條狀硅晶芯片上單個(gè)陣列波導(dǎo)光柵芯片波導(dǎo)圖形外圍制造一個(gè)的凹槽8輪廓,凹槽的形狀可以是U槽,V槽或者是矩形槽。槽體為一連續(xù)整體,但考慮到固體激光器采用脈沖模式對(duì)硅晶芯片表面進(jìn)行切割,也可以制作為由小段凹槽體組成的凹槽8,用于定位激光切割路徑以及達(dá)到芯片減薄??梢栽谇肮に嚕谀ぐ逯谱鞯倪^程中,通過光刻,刻蝕的方法完成;也可以通過激光器、金剛石刀片或其他切割方式完成。所述凹槽8的深度、寬度可以根據(jù)芯片之間相互擺放的不同而設(shè)定,為保證在條狀硅晶芯片上最大限度的擺放陣列波導(dǎo)光柵芯片,凹槽8不宜太寬,最佳寬度是L,100<L<600um,凹槽8的深度為D,最佳深度控制在D<500um。凹槽8的寬度過寬或過窄都可能導(dǎo)致芯片在正表面激光切割過程中造成芯片劃傷。凹槽8的深度過深容易在正表面激光切割過程中出現(xiàn)崩裂或者崩壞。步驟4、對(duì)條狀硅晶芯片6表面進(jìn)行保護(hù)處理。如圖6所示在條狀硅晶芯片6正表面粘貼耐熱膠帶紙9,并確保耐熱膠帶紙覆蓋到除蓋片7之外的所有陣列波導(dǎo)光柵芯片正表面。耐熱膠帶紙9用以防止激光切割過程中,材料部分熔融體硅屑附著在芯片邊緣以及表面而難以清除。在清洗工藝環(huán)節(jié)中,容易造成對(duì)芯片正表面劃傷。另一方面在一定程度上耐熱膠帶紙9起到隔熱效果,降低芯片在瞬時(shí)高溫下發(fā)生的物理化學(xué)性質(zhì)的變化而導(dǎo)致的指標(biāo)影響。所述耐熱膠帶紙9厚度為N,厚度根據(jù)芯片本身厚度有所調(diào)整。對(duì)于0.5~0.7mm厚度芯片,選取N1=0.06mm;對(duì)于0.7~1.0mm厚度芯片,選取N2=0.08mm;對(duì)于1.0~1.5mm厚度芯片,選取N3=0.1mm。貼耐膠帶紙尺寸厚度過薄,容易過薄或者過厚都容易對(duì)芯片切割質(zhì)量造成影響。并可以在激光切割完畢后采用紫外燈照射、酒精浸泡超聲等方式去除耐熱膠帶紙。本步驟也可以通過在條狀硅晶芯片表面涂膠的化學(xué)方式處理完成。步驟5、將如圖4所示的條狀硅晶芯片6使用夾具固定于切割臺(tái)。本發(fā)明一種曲線型陣列波導(dǎo)光柵芯片的切割方法使用的夾具12總體分為上底板夾具13以及基板夾具14兩部分。夾具12的裝配結(jié)構(gòu)如圖11所示?;鍔A具14如圖7-1、圖7-2、圖8所示,基板夾具14是平板上設(shè)置有一個(gè)凸臺(tái)16,基板夾具14固定于激光設(shè)備切割工作平臺(tái)上,并需確保基板夾具本身不與平臺(tái)發(fā)生相對(duì)的位置變化。上底板夾具13如圖7-1所示,上底板夾具的上表面開有凹臺(tái),凹臺(tái)區(qū)域包括中部凹臺(tái)區(qū)域10和邊緣凹臺(tái)區(qū)域11,中部凹臺(tái)區(qū)域10同條狀硅晶芯片6的形狀相匹配,條狀硅晶芯片6可以放置并且固定于上底板夾具上表面的中部凹臺(tái)區(qū)域10內(nèi),邊緣凹臺(tái)區(qū)域11是中部凹臺(tái)區(qū)域10相通的相隔凹槽區(qū)域,位于上底板夾具的邊緣,邊緣凹臺(tái)區(qū)域11中的凹槽寬度為條狀硅晶芯片6上的單個(gè)陣列波導(dǎo)光柵芯片的寬度。圖7-1和圖7-2中的上底板夾具的邊緣凹臺(tái)區(qū)域11是用于切割前后陣列波導(dǎo)光柵芯片取放以及條狀硅晶芯片6的定位。上底板夾具上的邊緣凹臺(tái)區(qū)域11中的第二凹槽17的寬度B,應(yīng)保證B<A,并確保有足夠位置便于左右施力同時(shí)拿取激光切割完后的單個(gè)曲線型陣列波導(dǎo)光柵芯片。上底板夾具中部凹臺(tái)區(qū)域10內(nèi)與條狀硅晶芯片6之間需要有較高的匹配程度,并確保條狀硅晶芯片6一側(cè)與上底板夾具一邊對(duì)齊,穩(wěn)定的固定于上底板夾具13的中部凹臺(tái)區(qū)域10內(nèi)。針對(duì)于不同大小尺寸的條狀硅晶芯片來設(shè)計(jì)夾具上的中部凹臺(tái)區(qū)域10的尺寸外型。并可以根據(jù)要求,在上底板夾具上放置多條條狀硅晶芯片,如圖7-2中夾具上的中部凹臺(tái)區(qū)域10由間隔分布的凹臺(tái)組成,不同尺寸的條狀硅晶芯片分布對(duì)應(yīng)固定放置于各自匹配凹臺(tái)內(nèi)。上底板夾具的底部間隔設(shè)置有多個(gè)第一凹槽15,基板夾具14的凸臺(tái)16寬度因與上底板夾具底部的第一凹槽15尺寸一致,并能完美的放置在一起,再將表面處理好后的條狀硅晶芯片正表面朝上的放置在圖7-1、圖7-2的上底板夾具的中部凹臺(tái)區(qū)域10的凹臺(tái)位置,也可以通過吸附等其他的方式對(duì)條狀硅晶芯片6進(jìn)行固定。夾具本身也需要有較好的熱傳導(dǎo)性能,材料可以是硅片或者玻璃片或者陶瓷片或者金屬片。圖7-1和圖7-2中上底板夾具底部的第一凹槽15之間的距離A為條狀硅晶芯片中各陣列波導(dǎo)光柵芯片之間的距離,這樣確保了通過紅外光源校準(zhǔn)第一條激光切割路徑,即:沿著凹槽8的路途位置之后,僅通過平移上底板夾具,達(dá)到快速找尋下條凹槽8位置切割路徑的方法。若條狀硅晶芯片上含有多種類型芯片,而帶來的芯片間距有差異的情況,也可以根據(jù)其要求改變上底板第一凹槽15間隔A的尺寸,由于曲線切割采用脈沖高溫氣化材料的方式,而且芯片材料可能與上底板材料不一致,因而熱傳導(dǎo)能力不同,很容易引起切割后的單個(gè)芯片粘合在夾具表面。所示芯片固定的夾具如圖7-1、圖7-2、圖8所示,目前使用的陣列波導(dǎo)光柵芯片是利用掩膜版通過光刻方法進(jìn)行制作,故可以實(shí)現(xiàn)切割的陣列波導(dǎo)光柵芯片尺寸的規(guī)范性。在掩模版前工藝時(shí)可以根據(jù)要求來調(diào)節(jié)芯片與芯片之間的間距,也可以配合采用微調(diào)架或電機(jī)控制步進(jìn)長度來達(dá)到高效快速批量生產(chǎn)。步驟6、芯片曲線切割:將激光起始聚焦點(diǎn),調(diào)節(jié)至芯片上表面凹槽8的位置上,并調(diào)節(jié)激光光束,采用連續(xù)脈沖激光切割方式沿芯片凹槽的曲線方向進(jìn)行激光劃片。激光劃片采用紅外光頻段波長進(jìn)行切割,功率一般在80~120W之間,脈沖釋放時(shí)間在控制在2~8us之間。功率過大以及脈沖時(shí)間過長會(huì)產(chǎn)生大量熱應(yīng)力并很容易導(dǎo)致硅晶芯片斷裂,功率過小以及脈沖時(shí)間過短會(huì)無法切斷或達(dá)到切割目的。采用激光切割、Water-Jet水切割或線切割的曲線切割技術(shù),切割后的單個(gè)陣列波導(dǎo)芯片具有曲線型的切割邊緣輪廓,具有最小的外形尺寸,切割后的芯片外形輪廓具有“∧”形。曲線型的切割邊緣輪廓可以是全部沿著沿陣列波導(dǎo)光柵圖案的邊緣,也可以是部分地沿著陣列波導(dǎo)光柵圖案的邊緣。本步驟可以采用激光切割、Water-Jet水切割或線切割的曲線切割方法,切割邊緣位于凹槽8之上,并與陣列波導(dǎo)光柵芯片圖案邊緣保留有大于200微米的安全距離,保證切割后不會(huì)破壞波導(dǎo)部分。由于采用凹槽8的特殊處理后,硅晶芯片局部厚度減薄,同時(shí)提高了切割后的芯片邊緣平滑度,另外采用了表面處理后的芯片。本發(fā)明實(shí)施例中以硅基二氧化硅材料為例來說明,但不只局限于此材料,還包括InGaAsP、Polymer和Si等本領(lǐng)域技術(shù)人員公知的其它波導(dǎo)材料。激光切割模式采用連續(xù)切割模式,降低一般采用分段切割模式帶來的熱應(yīng)力影響,減少降低原本采用分段切割模式帶來的激光與芯片接觸面可能發(fā)生的特性變化。減少由于局部溫度過高而帶來的熱量分散不均勻帶來的應(yīng)力影響。AWG陣列波導(dǎo)光柵結(jié)構(gòu)圖案本身具有彎曲的輪廓,因此,為了進(jìn)一步減小芯片尺寸,降低成本,本發(fā)明提出通過激光光束、水注、電流注可以沿任意路徑進(jìn)行切割的特點(diǎn),采用激光切割、Water-Jet水切割或線切割的方法進(jìn)行陣列波導(dǎo)光柵晶圓片的切割,來取代傳統(tǒng)機(jī)械切割法。采用曲線切割技術(shù),陣列波導(dǎo)光柵晶圓片上的多個(gè)AWG可以密集排放,見圖3,曲線切割后的AWG陣列波導(dǎo)光柵芯片為曲線型的外形輪廓,這種曲線型的外形輪廓可以是全部沿著沿陣列波導(dǎo)光柵圖案的邊緣,也可以是部分地沿著陣列波導(dǎo)光柵圖案的邊緣,見圖12所示,這種非接觸式的曲線切割技術(shù)最大程度地利用了可用空間,極大增加了陣列波導(dǎo)光柵晶圓片上可排放的陣列波導(dǎo)光柵芯片個(gè)數(shù),從而大降低了陣列波導(dǎo)光柵芯片成本。以上所述實(shí)施例僅表達(dá)了本發(fā)明的幾種實(shí)施方式,其描述較為具體和詳細(xì),但并不能因此而理解為對(duì)本發(fā)明專利范圍的限制。應(yīng)當(dāng)指出的是,對(duì)于本領(lǐng)域的普通技術(shù)人員來說,在不脫離本發(fā)明構(gòu)思的前提下,還可以做出若干變形和改進(jìn),這些都屬于本發(fā)明的保護(hù)范圍。因此,本發(fā)明專利的保護(hù)范圍應(yīng)以所附權(quán)利要求為準(zhǔn)。