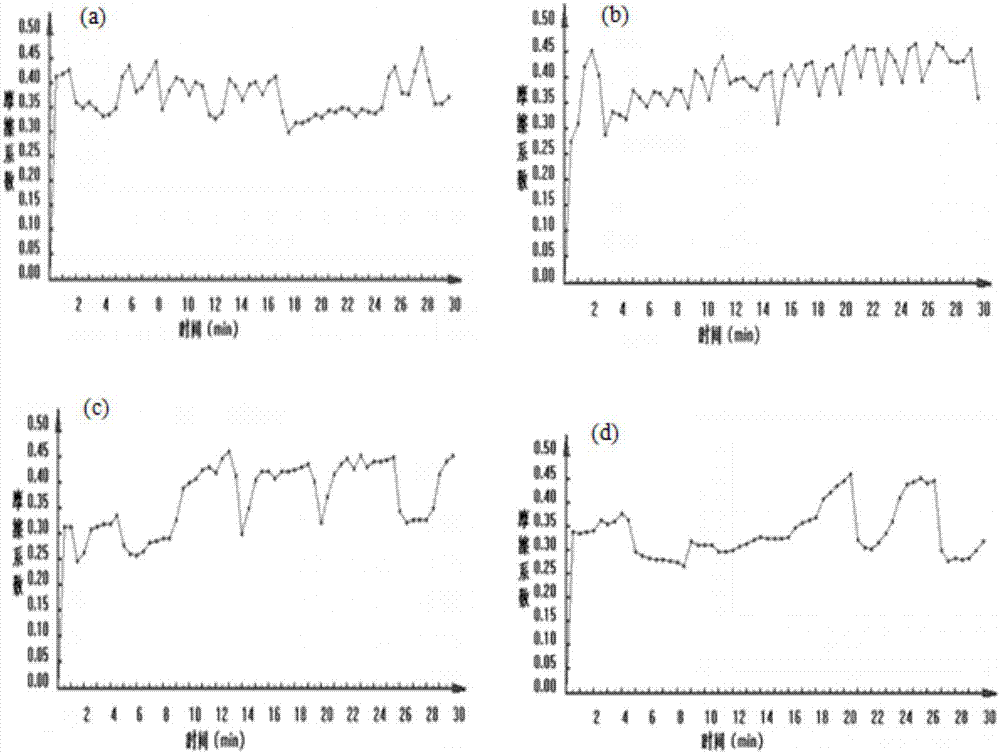
本發(fā)明屬于輪軌潤滑領(lǐng)域,具體涉及一種用于火車車輪踏面的摩擦控制劑及其制備工藝。
背景技術(shù):
:現(xiàn)代軌道交通運(yùn)輸領(lǐng)域中,輪軌摩擦與潤滑關(guān)系到機(jī)車牽引能量消耗、行車安全、輪軌材料消耗及維修成本等,因此受到各國鐵路部門重視。隨著列車運(yùn)行速度的進(jìn)一步提高,機(jī)車車輛的重載不斷增大,輪軌相互動(dòng)作用力不斷增大,與此同時(shí),鋼軌損傷(龜裂和剝離)、“噪聲”曲線、鋼軌磨耗等問題愈加突出。特別是處于小半徑曲線上的鋼軌,由于存在曲線鋼軌對(duì)列車輪軸的導(dǎo)向作用,車輪與鋼軌產(chǎn)生相互間的黏著、蠕滑和滑動(dòng),車輪輪緣、踏面和鋼軌軌側(cè)、軌頂磨耗和損傷十分嚴(yán)重。20世紀(jì)后,輪緣與鋼軌側(cè)面的潤滑技術(shù)得到長足發(fā)展,然而,為了保證輪軌粘著,潤滑僅限于輪緣和鋼軌側(cè)面,一般用于曲線區(qū)段,傳統(tǒng)觀念認(rèn)為滾動(dòng)面是潤滑的禁區(qū)。隨著科學(xué)研究的深入,和軌頂?shù)哪Σ量刂埔驳玫桨l(fā)展,根據(jù)德國hy-power公司研究結(jié)果,實(shí)施踏面摩擦控制可降低噪音35db、鋼軌磨耗減少2/3和列車脫軌系數(shù)降低67%。然而,對(duì)于火車車輪踏面的摩擦系數(shù)的控制,有些路局開始使用,但國內(nèi)尚沒有成熟產(chǎn)品在所有路局推廣,尤其在曲線半徑大、坡度大的線路,減磨效果不夠理想,成本高;存在固體潤滑粘結(jié)膜與輪軌表面附著力附著力不夠,且材料脆而受熱時(shí)易碎裂等問題。技術(shù)實(shí)現(xiàn)要素:本發(fā)明的目的是提供一種用于火車車輪踏面的摩擦控制劑,它具有耐熱性高、硬度高、機(jī)械強(qiáng)度高和耐磨性好的特點(diǎn),并可有效控制摩擦系數(shù)、成膜性,具有正摩擦特性并可降低行駛噪音,能有效減少鋼軌和車輪磨損,確保行車安全;且涉及的制備方法簡單、使用方便,適合推廣應(yīng)用。為實(shí)現(xiàn)上述目的,本發(fā)明采用的技術(shù)方案為:一種用于火車車輪踏面的摩擦控制劑,各組分及其所占質(zhì)量百分比包括:各組分及其所占質(zhì)量百分比包括:復(fù)合粘接劑25-50%,潤滑劑30-50%,增摩劑5-15%,摩擦改良劑10~30%,固化劑1-3%,促進(jìn)劑0-1.5%,脫模劑1~3%。優(yōu)選的,各組分及其所占質(zhì)量百分比包括:復(fù)合粘接劑30-40%,潤滑劑35-45%,增摩劑8-10%,摩擦改良劑10-15%,固化劑2%,促進(jìn)劑1%,脫模劑2%。上述方案中,所述復(fù)合粘接基體由無機(jī)粘接劑和有機(jī)樹脂粘接劑組成,且質(zhì)量比為(1~3):1,所述無機(jī)粘接劑為磷酸鋁鉻或磷酸二氫鋁,所述有機(jī)粘接劑為不飽和聚酯樹脂、熱固性丙烯酸樹脂或熱固性酚醛樹脂。上述方案中,所述潤滑劑為石墨、二硫化鉬中的一種或兩種,其細(xì)度為800目。上述方案中,所述摩擦改良劑為滑石粉、碳酸鈣、膨潤土或硅藻土,其細(xì)度為800目。所述摩擦改良劑可為所得摩擦控制劑賦予正摩擦特性,改善蠕滑和噪音,同時(shí)可作為空間填料在所得摩擦控制劑中起到改善材料的物理與機(jī)械性能、調(diào)節(jié)摩擦性能及降低成本的作用。上述方案中,所述增摩劑為氟化鈣、氧化鋁、硅酸鋯或鉀長石,莫氏硬度為5~6,其細(xì)度為325目。上述方案中,所述促進(jìn)劑劑為環(huán)烷酸鈷、二甲基苯胺或氧化鎂。上述方案中,所述固化劑為:當(dāng)所述樹脂粘結(jié)劑為不飽和聚酯樹脂、熱固性丙烯酸樹脂時(shí),固化劑選用過氧化環(huán)己酮;當(dāng)所述樹脂粘結(jié)劑為熱固性酚醛樹脂時(shí),固化劑選用石油磺酸。上述方案中,所述脫模劑為石蠟、聚乙烯蠟或硬脂酸鋅;本申請(qǐng)采用的脫模劑除具有脫模性能外,還具有耐化學(xué)性,在與上述不同熱固性樹脂粘結(jié)劑中的化學(xué)成份(特別是苯乙烯)接觸時(shí)不被溶解,同時(shí)還具有耐熱及應(yīng)力性能,不易分解或磨損。上述一種用于火車車輪踏面的摩擦控制劑的制備方法,包括如下步驟:1)混料工藝:首先按比例稱取各組分,各組分及其所占質(zhì)量百分比包括:復(fù)合粘接劑25%-50%,潤滑劑30%-50%,摩擦改良劑10%~30%,增摩劑5%-15%,固化劑1%-3%,促進(jìn)劑0%-1.5%,脫模劑1%~3%;將稱取的復(fù)合粘接劑和促進(jìn)劑攪拌均勻備用得液體混合料;將稱取的潤滑劑、增摩劑、摩擦改良劑和脫模劑混合后置于高速粉碎機(jī)中粉碎混勻得固體混合料;將所得液體混合料和固體混合料混合后,再加入稱取的固化劑,攪拌均勻,再次置于高速粉碎機(jī)中,得混合原料;2)真空抽氣工藝:將混合原料加入到模具內(nèi),合模后放入真空干燥箱中,在0.01~0.1mpa下,保壓8~10min,抽出物料中的空氣;3)熱壓工藝:將經(jīng)步驟2)處理的模具置于平板硫化機(jī)內(nèi)進(jìn)行熱壓,熱壓溫度為150~200℃、壓力為20~50mpa和保壓時(shí)間為2~4h;4)后固化工藝:先脫模,將摩擦控制劑從模具中取出放入到干燥箱中,進(jìn)行熱處理,加熱到150~200℃、保溫2~4h,即得用于火車車輪踏面的摩擦控制劑。優(yōu)選的,將步驟4)所得用于火車車輪踏面的摩擦控制劑以石蠟為浸漬劑進(jìn)行真空浸漬,工藝參數(shù)為浸漬溫度100~150℃,壓力0.01~0.1mpa,時(shí)間為1~2h;選用具有潤滑性的石蠟作為浸漬液,可進(jìn)一步提升所得摩擦控制劑的密實(shí)性能,優(yōu)化其摩擦控制效果。本發(fā)明的原理為:本發(fā)明采用熱壓成型技術(shù)制備出固體踏面摩擦控制劑,復(fù)合粘接劑采用磷酸鹽無機(jī)粘接劑和熱固性有機(jī)樹脂粘接劑,在熱壓成型時(shí)無機(jī)粘接劑受熱發(fā)生一次脫水,其自身的網(wǎng)絡(luò)結(jié)構(gòu)形成,同時(shí)利用熱固性樹脂固化過程中形成三維網(wǎng)狀立體聚合物,將所述潤滑劑、增摩劑和摩擦改良劑等骨材包絡(luò)在網(wǎng)狀體之中,形成堅(jiān)韌的體型復(fù)合物,其中占主要部分的潤滑劑起到潤滑減摩效果,而加入適量的微米級(jí)摩擦改良劑,與聚合物樹脂以化學(xué)鍵、物理吸附等方式結(jié)合,表現(xiàn)出增韌與增強(qiáng)的同步效應(yīng),有效提升耐磨性;在上述摩擦體系中引入尺寸較大的增摩劑可進(jìn)一步保證摩擦系數(shù)控制在0.3~0.4之間,有效保證火車車輪踏面的摩擦控制效果,并可進(jìn)一步改善顆粒間的粘結(jié)強(qiáng)度和耐熱性能。此外,在實(shí)際使用過程中,由于摩擦作用的存在使溫度升高,無機(jī)粘接劑受熱部分分解,出現(xiàn)二次脫水交聯(lián),使所得體型復(fù)合物的網(wǎng)絡(luò)結(jié)構(gòu)進(jìn)一步密實(shí),熱固性有機(jī)粘接劑的多孔結(jié)構(gòu)和無機(jī)粘接劑的高溫網(wǎng)絡(luò)結(jié)構(gòu),使所得摩擦控制劑在有效保證火車車輪踏面的摩擦控制效果的基礎(chǔ)上,改善了單一無機(jī)粘接劑的脆性,并可表現(xiàn)出優(yōu)異的耐高溫性能和降噪性能,有效改善曲線半徑大、坡度大的線路,減磨效果不夠理想、成本高、且受熱易碎裂等問題,具有重要的推廣應(yīng)用價(jià)值。本發(fā)明的有益效果為:1)本發(fā)明采用磷酸鹽無機(jī)粘接劑和熱固性有機(jī)樹脂粘接劑制備復(fù)合粘接劑,二者形成的網(wǎng)絡(luò)結(jié)構(gòu)協(xié)同作用,將潤滑劑、增摩劑和摩擦改良劑等骨材包絡(luò)在網(wǎng)狀體之中,形成堅(jiān)韌的體型復(fù)合物,改善了單一無機(jī)粘接劑的脆性和使用時(shí)摩擦生熱溫度升高強(qiáng)度下降過大;摩擦改良劑可進(jìn)一步與聚合物樹脂以化學(xué)鍵、物理吸附等方式結(jié)合,發(fā)揮增韌和增強(qiáng)效應(yīng),并可抑制復(fù)合粘結(jié)劑的固化收縮問題;使所得摩擦控制劑表現(xiàn)出耐熱性好,機(jī)械強(qiáng)度高,硬度高,耐磨性好等優(yōu)點(diǎn);此外摩擦改良劑還可賦予摩擦控制劑正摩擦特性,有效抑制輪軌之間的磨損和減少噪音的產(chǎn)生。2)本發(fā)明添加的一定細(xì)度的硬質(zhì)增摩劑能夠有效控制摩擦控制劑材料的摩擦系數(shù),并能改善顆粒間的粘結(jié)強(qiáng)度和耐熱性能。3)本發(fā)明采用分步混料工藝,使所得材料表現(xiàn)出較高的強(qiáng)度和成膜性能。4)本發(fā)明所述摩擦控制劑可以有效地均勻涂覆,并形成一層固體膜,其在保證具有良好粘結(jié)強(qiáng)度和耐熱性能的同時(shí),能使得輪軌間達(dá)到中等摩擦因數(shù)(0.35左右),可有效延長鋼軌的使用壽命,減緩鋼軌表面疲勞和損耗。5)本發(fā)明涉及的制備工藝簡單、生產(chǎn)效率高、成本低,且所述摩擦控制劑比傳統(tǒng)的液體摩擦控制劑使用簡單,配套裝置成本也較低,具有重要的經(jīng)濟(jì)和環(huán)境效益。附圖說明圖1為實(shí)施例1~2和對(duì)比例1~2所得摩擦控制劑的摩擦系數(shù)圖。圖2為對(duì)比例1(a)和實(shí)施例2(b)所得摩擦控制劑經(jīng)摩擦試驗(yàn)后在圓盤上的固體干膜的三維超景深3d顯示效果圖。圖3為實(shí)施例2(a)和對(duì)比例1(b)所得摩擦控制劑的tg-dsc曲線圖。具體實(shí)施方式為了更好地理解本發(fā)明,下面結(jié)合實(shí)施例進(jìn)一步闡明本發(fā)明的內(nèi)容,但本發(fā)明的內(nèi)容不僅僅局限于下面的實(shí)施例。實(shí)施例1一種用于火車車輪踏面的摩擦控制劑,其配方用量見下表1,其制備方法包括如下步驟:1)混料工藝:按表3所述配方稱取各原料;稱取磷酸鋁鉻,熱固性丙烯酸聚酯樹脂和促進(jìn)劑(環(huán)烷酸鈷),攪拌均勻,得液體混合料;將稱取的潤滑劑(石墨、二硫化鉬,800目)、增磨劑(硅酸鋯,325目)摩擦改良劑(碳酸鈣,800目)和脫模劑(硬脂酸鋅)混合后置于高速粉碎機(jī)中粉碎混勻得固體混合料;將所得液體混合料和固體混合料混合后,再加入稱取的固化劑(過氧化環(huán)己酮),攪拌均勻,得混合原料;2)真空抽氣工藝:將混合原料加入到模具內(nèi),合模后放入真空干燥箱中,在壓力為0.01mpa的添加下保壓10min,抽出物料中的空氣;3)熱壓工藝:將經(jīng)步驟2)處理的模具置于平板硫化機(jī)內(nèi)進(jìn)行熱壓(輥壓溫度為150℃、壓力為50mpa、保壓時(shí)間為2h);4)后固化工藝:將熱壓產(chǎn)物從模具中取出放入到真空干燥箱中,加熱到160℃保溫4h,即得用于火車車輪踏面的摩擦控制劑;5)浸漬工藝:將步驟4)所得用于火車車輪踏面的摩擦控制劑以石蠟為浸漬劑進(jìn)行真空浸漬備用,工藝參數(shù)為浸漬溫度120℃,壓力為0.01mpa,時(shí)間為1h。表1實(shí)施例1所述摩擦控制劑中各組分的用量組分質(zhì)量百分?jǐn)?shù)(wt%)磷酸鋁鉻15熱固性丙烯酸樹脂15石墨22二硫化鉬22碳酸鈣13硅酸鋯8過氧化環(huán)己酮2環(huán)烷酸鈷1硬脂酸鋅2經(jīng)測(cè)試,本實(shí)施例制備的摩擦控制劑的使用溫度范圍為-40℃~400℃;在載荷20n,轉(zhuǎn)速400rpm,室溫,空氣中,進(jìn)行銷-盤式摩擦試驗(yàn),摩擦?xí)r間30min,其摩擦系數(shù)為0.376(摩擦系數(shù)圖見圖1(a)),體積磨損量為10.02mg·cm-3,成膜厚度11.6μm,密度為2.11g·cm-3,邵氏硬度(d型)為61.2,壓縮強(qiáng)度為29.41mpa,彎曲強(qiáng)度為19.88mpa。實(shí)施例2一種用于火車車輪踏面的摩擦控制劑,其配方用量見下表2,其制備方法包括如下步驟:1)混料工藝:按表3所述配方稱取各原料;稱取磷酸鎂二氫鋁,熱固性丙烯酸樹脂和促進(jìn)劑(環(huán)烷酸鈷),攪拌均勻,得液體混合料;將稱取的潤滑劑(石墨、二硫化鉬,800目)、摩擦改良劑(碳酸鈣,800目)、增摩劑(硅酸鋯,325目)和脫模劑(硬脂酸鋅)混合后置于高速粉碎機(jī)中粉碎混勻得固體混合料;將所得液體混合料和固體混合料混合后,再加入稱取的固化劑(過氧化環(huán)己酮),攪拌均勻,得混合原料;2)真空抽氣工藝:將混合原料加入到模具內(nèi),合模后放入真空干燥箱中,壓力為0.01mpa,保壓10min,抽出物料中的空氣;3)熱壓工藝:將經(jīng)步驟2)處理的模具置于平板硫化機(jī)內(nèi)進(jìn)行熱壓(輥壓溫度為180℃、壓力為30mpa、保壓時(shí)間為2h);4)后固化工藝:將熱壓產(chǎn)物從模具中取出放入到真空干燥箱中,加熱到160℃保溫4h,即得用于火車車輪踏面的摩擦控制劑;5)浸漬工藝:將步驟4)所得用于火車車輪踏面的摩擦控制劑以石蠟為浸漬劑進(jìn)行真空浸漬,工藝參數(shù)為浸漬溫度120℃,壓力0.01mpa,時(shí)間為1h。表2實(shí)施例2所述摩擦控制劑中各組分的用量組分質(zhì)量百分?jǐn)?shù)(wt%)磷酸二氫鋁20熱固性丙烯酸樹脂10石墨22二硫化鉬22碳酸鈣13鉀長石8過氧化環(huán)己酮2環(huán)烷酸鈷1硬脂酸鋅2經(jīng)測(cè)試,本實(shí)施例制備的摩擦控制劑的使用溫度范圍為-40℃~400℃;在載荷20n,轉(zhuǎn)速400rpm,室溫,空氣中,進(jìn)行銷-盤式摩擦試驗(yàn),摩擦?xí)r間30min,摩擦系數(shù)為0.399(摩擦系數(shù)圖見圖1(b)),體積磨損量為10.35mg·cm-3,成膜厚度4.9μm,密度為2.18g·cm-3,邵氏硬度(d型)為61.2,壓縮強(qiáng)度為26.50mpa,彎曲強(qiáng)度為17.18mpa。本實(shí)施例所得摩擦控制劑的經(jīng)摩擦試驗(yàn)后在圓盤上的固體干膜的三維超景深3d顯示效果圖見圖2(a),可以看出摩擦控制材料在鋼表面形成了一層均勻分布的摩擦控制膜,厚度也較為均勻,其平均厚度為4.9μm;本實(shí)施例所得摩擦控制劑的tg-dsc曲線圖見圖3(a),結(jié)果表明在空氣氣氛中,摩擦控制劑在200℃時(shí)開始失重,300℃時(shí)已經(jīng)失重11.79%,主要是有機(jī)樹脂的分解,在600℃以后才再次失重,說明無機(jī)粘接劑在250~400℃仍起粘接作用。對(duì)比例1一種摩擦控制劑,其配方用量見下表3,其制備方法包括如下步驟:1)混料工藝:按表1所述配方稱取各原料;稱取不飽和聚酯樹脂,促進(jìn)劑(環(huán)烷酸鈷)攪拌均勻,得液體混合料;將稱取的潤滑劑(石墨、二硫化鉬)、增摩劑(鉀長石)、摩擦改良劑(滑石粉)和脫模劑(硬脂酸鋅)混合后置于高速粉碎機(jī)中粉碎混勻得固體混合料;將所得液體混合料和固體混合料混合后,再加入稱取的固化劑(過氧化環(huán)己酮),攪拌均勻,再置于高速粉碎機(jī)中進(jìn)行粉碎,得混合原料;2)真空抽氣工藝:將所得混合原料加入模具內(nèi),合模后放入真空干燥箱中,在壓力為0.01mpa的條件下保壓10min,抽出物料中的空氣;3)熱壓工藝:將經(jīng)步驟2)處理的模具置于平板硫化機(jī)內(nèi)進(jìn)行熱壓(輥壓溫度為160℃、壓力為30mpa、保壓時(shí)間為2h;4)后固化工藝:將熱壓產(chǎn)物從模具中取出放入到真空干燥箱中,加熱到150℃保溫4h,冷卻,即得用于火車車輪踏面的摩擦控制劑。表3對(duì)比例1所述摩擦控制劑中各組分的用量組分質(zhì)量百分?jǐn)?shù)(wt%)不飽和聚酯樹脂30石墨21二硫化鉬21滑石粉17鉀長石6過氧化環(huán)己酮2環(huán)烷酸鈷1硬脂酸鋅2經(jīng)測(cè)試,本對(duì)比例制備的摩擦控制劑,其使用溫度范圍為-40℃~250℃;在載荷20n,轉(zhuǎn)速400rpm,室溫,空氣中,進(jìn)行銷-盤式摩擦試驗(yàn),摩擦?xí)r間30min,其摩擦系數(shù)為0.374(摩擦系數(shù)圖見圖1(c)),體積磨損量為12.3mg·cm-3,成膜厚度10.3μm;密度為2.24g·cm-3,邵氏硬度(d型)為70,壓縮強(qiáng)度為27.91mpa,彎曲強(qiáng)度為19.21mpa,350℃馬弗爐燒結(jié)1h后,壓縮強(qiáng)度為13.78mpa,彎曲強(qiáng)度為8.52mpa。本對(duì)比例所得摩擦控制劑的經(jīng)摩擦試驗(yàn)后在圓盤上的固體干膜的三維超景深3d顯示效果圖見圖2(b),可以看出摩擦控制材料在鋼表面形成了一層較為均勻的摩擦控制膜,厚度有高有低,其平均厚度為10.3μm;本對(duì)比例所得摩擦控制劑的tg-dsc曲線圖見圖3(b),結(jié)果表明在空氣氣氛中,摩擦控制劑在200℃時(shí)開始失重,350℃時(shí)已經(jīng)失重18.75%,在450℃失重率達(dá)到27.19%,表面摩擦控制劑體系中有機(jī)樹脂已經(jīng)分解,表明粘接性減弱。對(duì)比例2一種摩擦控制劑,其配方用量見下表4,其制備方法包括如下步驟:1)混料工藝:按表2所述配方稱取各原料;熱固性丙烯酸樹脂和促進(jìn)劑(環(huán)烷酸鈷),攪拌均勻,得液體混合料;將稱取的潤滑劑(石墨、二硫化鉬)、增摩劑(硅酸鋯)、摩擦改良劑(碳酸鈣)和脫模劑(硬脂酸鋅)混合后置于高速粉碎機(jī)中粉碎混勻得固體混合料;將所得液體混合料和固體混合料混合后,再加入稱取的固化劑(過氧化環(huán)己酮),攪拌均勻,得混合原料;2)真空抽氣工藝:將混合原料加入到模具內(nèi),合模后放入真空干燥箱中,在壓力為0.01mpa的條件下保壓10min,抽出物料中的空氣;3)熱壓工藝:將經(jīng)步驟2)處理的模具置于平板硫化機(jī)內(nèi)進(jìn)行熱壓(輥壓溫度為160℃、壓力為30mpa、保壓時(shí)間為2h);4)后固化工藝:將熱壓產(chǎn)物從模具中取出放入到真空干燥箱中,加熱到150℃保溫4h,即得用于火車車輪踏面的摩擦控制劑;表4對(duì)比例2所述摩擦控制劑中各組分的用量經(jīng)測(cè)試,本對(duì)比例所得摩擦控制劑的使用溫度范圍為-40℃~400℃;在載荷20n,轉(zhuǎn)速400rpm,室溫,空氣中,進(jìn)行銷-盤式摩擦試驗(yàn),摩擦?xí)r間30min,其摩擦系數(shù)為0.342(摩擦系數(shù)圖見圖1(d)),體積磨損量為12.3mg·cm-3(除與摩擦系數(shù)有關(guān)外,還與摩擦控制劑中各組分之間的粘結(jié)性能有關(guān)),成膜厚度8.1μm,密度為2.13g·cm-3邵氏硬度(d型)為66.5,壓縮強(qiáng)度為25.73mpa,彎曲強(qiáng)度為17.73mpa,350℃馬弗爐燒結(jié)1h后,壓縮強(qiáng)度為17.88mpa,彎曲強(qiáng)度為11.68mpa。以上實(shí)施例僅為本發(fā)明的優(yōu)選實(shí)施方式,應(yīng)當(dāng)指出,對(duì)于本領(lǐng)域技術(shù)人員來說,在不脫離本發(fā)明原料前提下,所作出的若干改進(jìn),也應(yīng)視為本發(fā)明的保護(hù)范圍。當(dāng)前第1頁12