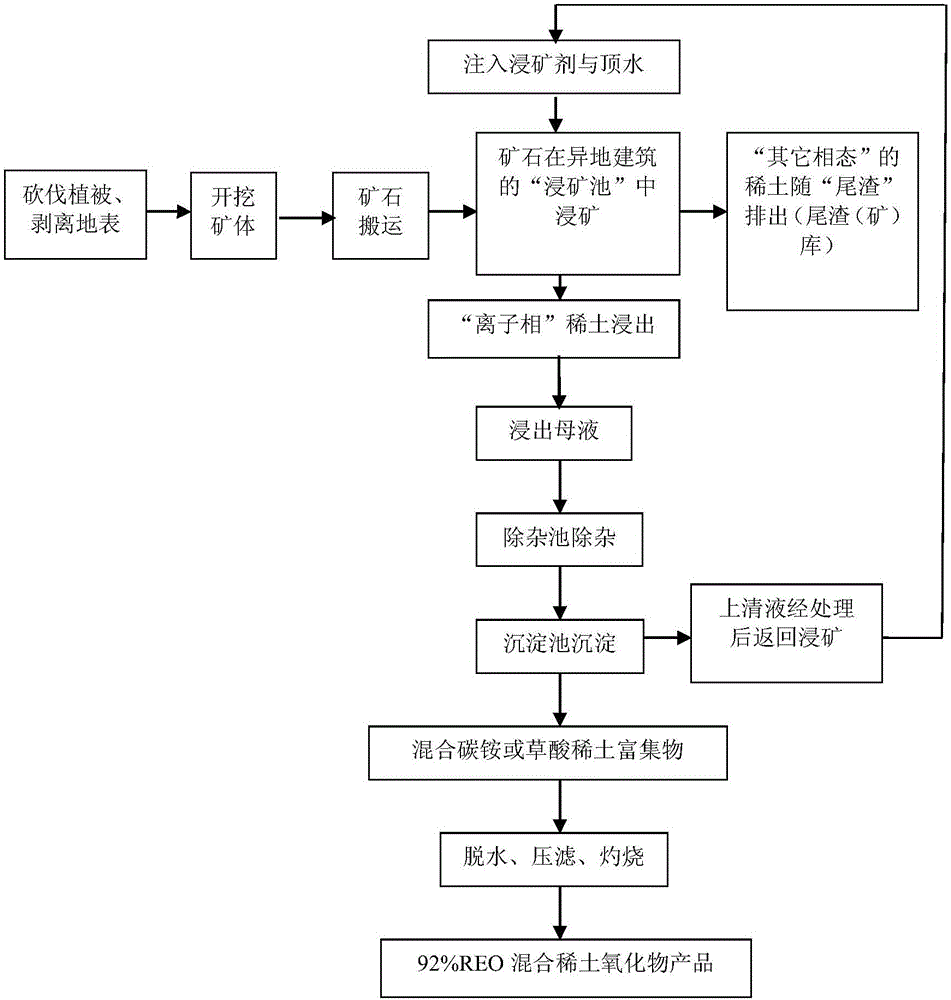
本發(fā)明涉及采礦工藝
技術(shù)領(lǐng)域:
,具體涉及一種離子型稀土礦的稀土原地浸出及富集工藝。
背景技術(shù):
:迄今,“離子型稀土礦”的浸出與富集工藝主要有兩種,一種為“池浸”,一種為“原地浸礦”。因“池浸”對生態(tài)環(huán)境帶來的破壞與影響很大,我國對“離子型稀土礦”開采實(shí)行的采掘技術(shù)政策已將其淘汰,現(xiàn)推行的是“原地浸礦”工藝。這兩種采掘工藝的流程示意圖分別如圖1和圖2所示。以上兩種工藝的核心和首先要解決的問題,就是如何將以“離子”狀態(tài)的稀土礦物,從礦石(體)中“浸出”(或“解吸”)出來,這就需要采用將離子型稀土“浸出”的“浸礦劑”。我國離子型稀土礦使用的“浸礦劑”,初期采用的是氯化鈉,爾后普遍采用硫酸銨。而對其除雜的藥劑,一般為碳銨;沉淀富集的藥劑,普遍采用碳銨或草酸。對“離子型稀土”的“原地浸礦”工藝,是針對“池浸”工藝對環(huán)境破壞嚴(yán)重的主要弊端,而研發(fā)的新一代離子型稀土礦山開采工藝。它在不破壞礦區(qū)地表植被、不開挖表土的情況下,對含礦山體內(nèi)部,按規(guī)定的方式和要求,開掘到達(dá)礦體內(nèi)部的注液井(或孔),將浸礦劑溶液(含電解質(zhì)溶液)通過注液井(孔)直接注入礦體。電解質(zhì)中化學(xué)性質(zhì)更為活潑的陽離子,將吸附在“載體礦物”表面和晶層間的化學(xué)性質(zhì)活潑性較前者更差的稀土陽離子,交換解吸下來。然后通過收液系統(tǒng)將浸出母液收集,使其進(jìn)入后續(xù)加工處理系統(tǒng)。根據(jù)浸礦原理,電解質(zhì)溶液在礦體內(nèi)的運(yùn)動,是一個“滲透→擴(kuò)散→交換→再擴(kuò)散→再滲透”的過程。顯而易見,電解質(zhì)溶液的整個運(yùn)動過程,也就是稀土離子不斷地被交換和解吸的過程。擴(kuò)散動力是電解質(zhì)溶液的濃度差,不斷注入礦體的溶液(或頂水)擠出已發(fā)生交換作用的稀土浸礦液。在這不斷地“浸礦”過程中,注入礦體內(nèi)部的液體,業(yè)已逐步地演變成含稀土的“母液”(簡稱“母液”),或稱之為“浸出母液”?!霸亟V”工藝,客觀上雖然解決了“池浸”工藝中地表剝離、礦體露天開采、異地浸礦等對生態(tài)環(huán)境帶來重大影響與破壞的問題,但主觀上仍存在一些突出的問題。主要是:(1)因該工藝應(yīng)用的藥劑,其組份含氨氮,故在工藝實(shí)施過程中,在諸多的環(huán)節(jié)里,氨氮嚴(yán)重超標(biāo),污染環(huán)境,制約了工藝的使用,許多礦山已因此停產(chǎn)整頓多年,至今未復(fù)產(chǎn);(2)對稀土的浸出過程缺乏系統(tǒng)的研究,不能實(shí)現(xiàn)對稀土進(jìn)行系統(tǒng)、科學(xué)、人為地“控制浸出”;(3)浸出母液濃度低、液量大、處理成本較高,不能直接進(jìn)槽萃取分離;(4)整個工藝生產(chǎn)過程中,稀土浸出周期較長,整個生產(chǎn)周期較久;(5)開發(fā)工程技術(shù)人員若對技術(shù)掌握不夠,工程布置與管理不當(dāng),易于引發(fā)“地質(zhì)問題”;(6)該工藝主要適用于“全相”稀土中“離子相”稀土的浸出,對包含“四相八態(tài)”中的“其它相態(tài)”稀土的回收缺乏研究,導(dǎo)致該工藝對“其它相態(tài)”稀土資源的利用率很差;(7)現(xiàn)有工藝的碳銨沉淀法富集稀土獲得的混合碳銨稀土,產(chǎn)品中非稀土雜質(zhì)(如Fe、Al、Si、Ca等)含量較高,不利于后續(xù)加工;而以草酸沉淀法獲得的混合草酸稀土,雖然雜質(zhì)含量較低,但其廢水中草酸根與H+根離子含量較高,需中和處理,同時產(chǎn)生氨氮或COD對環(huán)境的影響;(8)現(xiàn)生產(chǎn)工藝所獲固態(tài)稀土產(chǎn)品,進(jìn)入分離廠后,首先需將其制備成合格的料液,這就需經(jīng)鹽酸分解、除雜等工序,除處理成本高外,因酸霧的影響,環(huán)保壓力也很大;(9)產(chǎn)品單一。技術(shù)實(shí)現(xiàn)要素:有鑒于此,本發(fā)明的目的是提供一種全新的離子型稀土礦的稀土原地浸出及富集工藝,從而解決前述現(xiàn)有技術(shù)中存在的至少一項(xiàng)技術(shù)問題。本發(fā)明提供的離子型稀土礦的稀土原地浸出及富集工藝,包括:步驟一:向礦體內(nèi)部注入浸礦劑和收縮劑,原地原位浸礦使“離子相”及部分“其它相態(tài)”稀土浸出,得到浸出母液;步驟二:向濃度≥1g/L的中、高濃度浸出母液中通入除雜劑I進(jìn)行除雜,除雜后經(jīng)沉淀劑沉淀,再經(jīng)清水洗滌、過濾、灼燒得到固態(tài)稀土產(chǎn)品;其中,所述除雜劑I為碳酸氫鈉溶液和碳酸鈉溶液的混合液,所述沉淀劑為碳酸氫鈉溶液;和向濃度<1g/L的低濃度浸出母液中通入除雜劑II中和去除鋁雜質(zhì),然后將除鋁后母液(即浸出母液經(jīng)除鋁后所得稀土上清液)通入離子交換柱中進(jìn)行稀土離子的吸附富集,再用酸進(jìn)行解吸,得到液態(tài)稀土產(chǎn)品;其中,所述除雜劑II為石灰乳。在本領(lǐng)域,“離子型”稀土礦稀土的賦存性狀,是由“四相八態(tài)”稀土礦物組成,包括:①離子吸附相(含可交換性吸附態(tài)、專性吸附態(tài);②膠體分散相(含膠體吸附態(tài)、凝膠態(tài));③獨(dú)立礦物相(含表生礦物態(tài)、殘留礦物態(tài));④晶格雜質(zhì)相(含類質(zhì)同象態(tài)、內(nèi)潛同晶態(tài))。由這“四相八態(tài)”的稀土礦物,即構(gòu)成離子吸附型稀土礦中,所謂的“全相”稀土礦物。有關(guān)于“四相八態(tài)”其命名資料的來源為:《贛南花崗巖類風(fēng)化殼離子吸附型稀土成礦規(guī)律研究》報告,贛南地質(zhì)調(diào)查大隊(duì),1986。在本發(fā)明中,所述的“其它相態(tài)”稀土是指離子型稀土礦中,除“離子相”稀土礦物之外的、其余“相態(tài)”的稀土礦物。步驟一中,所述浸礦劑由含鐵、錳和鈣的菱鎂礦制得,所述浸礦劑的制備過程為:礦石經(jīng)粉碎后用水調(diào)漿,然后加入酸分解至呈弱酸性,即得液態(tài)的浸礦劑。本發(fā)明得到的浸礦劑含有鎂、鐵、錳和鈣等復(fù)合陽離子。優(yōu)選地,所述浸礦劑的制備過程還包括:將所得液態(tài)的浸礦劑經(jīng)過濾、洗滌后,將所得母液進(jìn)行蒸發(fā)結(jié)晶,即得固體浸礦劑。在浸礦過程中,將固體浸礦劑加水或酸復(fù)溶,得到液態(tài)的浸礦劑后使用。優(yōu)選地,所述菱鎂礦中鐵<10%、錳<3%、鈣<10%,所述百分比為質(zhì)量百分比。所述收縮劑是氯化鈣溶液。優(yōu)選地,所述收縮劑還可以進(jìn)一步由氯化鈣溶液結(jié)晶得到固體產(chǎn)品,即固體收縮劑。在浸礦過程中,可以將固體收縮劑加水或酸復(fù)溶,得到液態(tài)的收縮劑后使用,也可以直接將收縮劑加入頂水使用。在本發(fā)明中,所述收縮劑是在頂水注入階段與頂水配合使用的,即將收縮劑加入到頂水中,并與頂水一起注入。更優(yōu)選地,所述收縮劑是以石灰為原料,經(jīng)酸解得到氯化鈣溶液,再經(jīng)結(jié)晶得到固體產(chǎn)品,即為所述固體收縮劑。步驟一中,在浸礦劑注入階段(即浸礦的初、中期)注入浸礦劑;在頂水注入階段(即浸礦的后期)注入頂水,注入頂水時,將收縮劑加入在頂水中與頂水一并注入。這是由于在浸礦劑中含有與收縮劑相關(guān)的離子,在浸礦時注入浸礦劑相當(dāng)于一并注入了收縮劑,不需另外添加收縮劑;而在浸礦的后期(即頂水注入階段),由于頂水中沒有與收縮劑相關(guān)的離子,因此需在頂水中加入收縮劑。在此,本領(lǐng)域技術(shù)人員應(yīng)當(dāng)理解,作為在浸礦過程中使用的浸礦劑,可以是液態(tài)的,也可以是固態(tài)的浸礦劑經(jīng)加水或酸復(fù)溶得到的液態(tài)浸礦劑,并根據(jù)現(xiàn)場使用需要適時作一定的pH調(diào)節(jié)。步驟一中,稀土浸出周期的時間受礦體滲透性好壞的影響,一般來說其滲透性均較差。在浸出過程中,需分區(qū)域設(shè)定控制點(diǎn),對控制點(diǎn)的浸出母液的流量、稀土含量進(jìn)行監(jiān)控。優(yōu)選地,當(dāng)浸出母液中的稀土含量越過峰值并處在下降的過程中,停止浸礦劑注入,改為注入頂水(內(nèi)含收縮劑);當(dāng)浸出母液中的稀土含量下降至0.1克/升時,停止注入頂水(內(nèi)含收縮劑)并收液,結(jié)束浸礦。更優(yōu)選地,當(dāng)浸出母液中的稀土含量越過峰值并下降至(所述峰值的)80%~50%時,停止浸礦劑注入,改為注入頂水。步驟二中,所述通入除雜劑I進(jìn)行除雜時優(yōu)選控制pH≤5.2。步驟二中,所述除雜劑II為石灰乳,但此處也可以用除雜劑I(即碳酸氫鈉溶液和碳酸鈉溶液的混合液)替代石灰乳進(jìn)行除雜。步驟二中,所述離子交換柱優(yōu)選丙烯酸系陽離子交換樹脂。步驟二中,所述用酸進(jìn)行解吸優(yōu)選使用鹽酸進(jìn)行解吸。本發(fā)明取得了下述有益效果:(1)本發(fā)明研發(fā)和應(yīng)用不含氨氮的新型浸礦劑、除雜劑、沉淀劑,從源頭上解決氨氮污染問題,從而更為有效地浸出稀土。(2)本發(fā)明研究和應(yīng)用新的除雜劑、沉淀劑和母液的除雜、富集工藝技術(shù),降低產(chǎn)品中非稀土雜質(zhì)含量,提高母液濃度,減少母液量和后續(xù)處理工序的加工量,縮短浸礦周期;所得新型液態(tài)稀土富集產(chǎn)品能直接進(jìn)槽。(3)本發(fā)明中使用的各種藥劑,不產(chǎn)生影響環(huán)保參數(shù)的問題,確保它們將不導(dǎo)致環(huán)保問題,從而使整個工藝環(huán)保整體達(dá)標(biāo),對“離子型稀土”實(shí)現(xiàn)綠色開采。(4)本發(fā)明的工藝可以實(shí)現(xiàn)對稀土系統(tǒng)、科學(xué)、人為地“控制浸出”,引入和應(yīng)用“收縮劑”藥劑與技術(shù),能改善和提高礦體結(jié)構(gòu)的穩(wěn)定性,減少山體坍塌、滑坡的發(fā)生率。(5)本發(fā)明提高了對“其它相態(tài)”稀土的資源利用率。(6)本發(fā)明創(chuàng)新性地對母液進(jìn)行“分類分流”處理,從而使各部分產(chǎn)品能得到更合理的應(yīng)用,且節(jié)省了成本。附圖說明圖1是稀土礦“池浸”工藝的流程示意圖。圖2是現(xiàn)有技術(shù)稀土礦“原地浸礦”工藝的流程示意圖。圖3為本發(fā)明的離子型稀土礦的稀土原地浸出及富集工藝的流程示意圖。具體實(shí)施方式為使本發(fā)明的目的、技術(shù)方案和優(yōu)點(diǎn)更加清楚明白,以下結(jié)合具體實(shí)施例,并參照附圖,對本發(fā)明作進(jìn)一步的詳細(xì)說明。如圖3所示,其為本發(fā)明的離子型稀土礦的稀土原地浸出及富集工藝的流程示意圖。本發(fā)明的離子型稀土礦的稀土原地浸出及富集工藝包括:步驟一:向礦體內(nèi)部注入浸礦劑和收縮劑,原地原位浸礦使“離子相”及部分“其它相態(tài)”稀土浸出,得到浸出母液;步驟二:向濃度≥1g/L的中、高濃度浸出母液中通入除雜劑I進(jìn)行除雜,除雜后經(jīng)沉淀劑沉淀,再經(jīng)清水洗滌、過濾、灼燒得到固態(tài)稀土產(chǎn)品;其中,所述除雜劑I為碳酸氫鈉溶液和碳酸鈉溶液的混合液,所述沉淀劑為碳酸氫鈉溶液;和向濃度<1g/L的低濃度浸出母液中通入除雜劑II中和去除鋁雜質(zhì),然后將除鋁后母液(即浸出母液經(jīng)除鋁后所得稀土上清液)通入離子交換柱中進(jìn)行稀土離子的吸附富集,再用酸進(jìn)行解吸,得到液態(tài)稀土產(chǎn)品;其中,所述除雜劑II為石灰乳。本發(fā)明中使用的各種藥劑均與現(xiàn)有技術(shù)完全不同,均為完全自主研發(fā)的新產(chǎn)品。本發(fā)明中使用的新型浸礦劑、除雜劑、沉淀劑均不含氨氮,因此能夠從源頭上解決氨氮污染問題,更為有效地浸出稀土。不僅如此,本發(fā)明還開創(chuàng)性地對所得到的浸出母液進(jìn)行分類處理,通過針對不同濃度的浸出母液分別采取不同的除雜、沉淀和富集工藝,從而得到不同形態(tài)的產(chǎn)品。在正式開始浸礦開采工作之前,一般來說,還包括如下準(zhǔn)備工作:1、補(bǔ)充地質(zhì)勘查;2、工程設(shè)計與施工;3、建設(shè)主要工程:(1)注液體系;(2)供水體系;(3)地下、地面收液體系;(4)濕法冶金體系;(5)供配電體系;(6)其它輔助體系;(7)離子吸附除雜、富集體系及儲罐(車)。本發(fā)明的離子型稀土礦的稀土原地浸出及富集工藝與現(xiàn)有的稀土原地浸出工藝相比較,能夠?qū)崿F(xiàn)原地浸礦無氨氮化作業(yè)、綠色開采、環(huán)保達(dá)標(biāo)、優(yōu)化流程、控制浸出、防止山體滑移、富集母液直接進(jìn)槽分離、提高“其它相態(tài)”的資源利用率,從而實(shí)現(xiàn)離子型稀土提取工藝重大變革、技術(shù)經(jīng)濟(jì)指標(biāo)全面優(yōu)化、生態(tài)環(huán)境友好的目的。具體地,相比現(xiàn)有技術(shù),本發(fā)明取得的積極進(jìn)步效果包括:(1)本發(fā)明的浸礦劑所采用的生產(chǎn)原料豐富低廉,生產(chǎn)工藝簡單,產(chǎn)品可結(jié)晶為固體,便于運(yùn)輸、儲存。本發(fā)明浸礦劑中含有的復(fù)合陽離子成分,使其對稀土離子的浸出,具有良好的協(xié)同作用,從而更有利于對“其它相態(tài)”稀土的浸出?!半x子相”稀土浸出可達(dá)到99.4%以上,部分“其它相態(tài)”稀土的浸出達(dá)到22.5%以上,“全相”稀土浸出率達(dá)到83%以上。與現(xiàn)有技術(shù)工藝采用的硫酸銨浸礦劑相比,對“其它相態(tài)”的稀土浸取效果尤為突出,“其它相態(tài)”稀土浸出率提高15%,“全相”稀土浸出率提高3%。同樣藥劑用量的情況下,本發(fā)明的浸礦劑可以縮短浸礦周期20~40%以上。(2)使用本發(fā)明的浸礦劑,得到的浸出母液中,主要的非稀土雜質(zhì)Fe、Al、Si浸出率分別為0.73%、0.37%、1.93%,各占現(xiàn)有技術(shù)硫酸銨浸礦劑浸出稀土母液中的8.81%、77.08%、51.60%。本發(fā)明的浸礦劑對鐵的浸出大大降低,鋁、硅的浸出也有不小幅度的降低。優(yōu)質(zhì)的、雜質(zhì)含量更低的浸出母液,將大大有利于后續(xù)濕法冶金的加工處理。(3)本發(fā)明中應(yīng)用的收縮劑及其技術(shù),其主要物質(zhì)為鈣,它發(fā)揮的重要作用是提高了山(礦)體結(jié)構(gòu)的穩(wěn)定性,使其不易沿結(jié)構(gòu)面發(fā)生滑移。同時,有利于提高浸出速度,縮短浸礦周期。(4)在本發(fā)明的工藝流程中,沉淀上清液及其它涉及外排的液體,各項(xiàng)環(huán)保指標(biāo),尤其是氨氮≤8mg/L、化學(xué)需氧量(COD)≤100mg/L、P≤1mg/l,都符合環(huán)保的相關(guān)要求。應(yīng)用本發(fā)明的浸礦劑浸礦,完全可以避免氨氮及其它因素污染環(huán)境的問題,替代現(xiàn)有技術(shù)的硫酸銨具有極大的優(yōu)勢。(5)選用碳酸氫鈉和碳酸鈉混合液進(jìn)行沉淀除雜,用碳酸氫鈉進(jìn)行稀土沉淀,所得稀土氧化物符合產(chǎn)品要求規(guī)范。選用的新型除雜劑、沉淀劑使用效果與現(xiàn)有技術(shù)工藝傳統(tǒng)藥劑相當(dāng),但是取得了比原工藝更為優(yōu)異的環(huán)保指標(biāo)。(6)本發(fā)明以石灰乳除鋁雜質(zhì),因稀土母液中含有鈣、鎂,因此其工藝步驟不引入新的雜質(zhì)。在除鋁工藝過程中,控制適當(dāng)?shù)膒H值更可達(dá)到非常優(yōu)異的除鋁雜質(zhì)效果,稀土損失率低。其中,石灰乳除鋁的工藝步驟可由以碳酸氫鈉和碳酸鈉的混合液進(jìn)行沉淀除雜代替。本發(fā)明的Al雜質(zhì)除去率達(dá)93.94%,稀土損失率低至3.63%。(7)利用本發(fā)明的丙烯酸系陽離子交換樹脂的分離富集方法和工藝,對稀土母液進(jìn)行除雜和富集,可以得到一種能夠滿足稀土分離廠萃取料液要求的、潔凈的高濃度稀土富集液。富集液中稀土濃度≥196g/L,富集比約200倍,稀土解析回收率99.07%。主要雜質(zhì)Fe≤100mg/L,Al≤800mg/L,Si≤100mg/L,Ca≤1.2g/L,Mg≤1.2g/L。本發(fā)明試驗(yàn)室獲得的Fe、Al、Si等非稀土雜質(zhì)含量極低(Fe0.36mg/L、Al19.71mg/L、Si6.04mg/L)的優(yōu)質(zhì)液態(tài)稀土富集液,是目前稀土分離廠都難以達(dá)到的指標(biāo)。針對稀土母液的除雜與富集問題,本發(fā)明采用的技術(shù)路線為“離子吸附”,與相關(guān)單位采用的“離心萃取”技術(shù)路線完全不同,兩者互不相干。(8)本發(fā)明提出和建立的“控制浸出”技術(shù)概念及其技術(shù)體系,對浸出母液采取“分類分流”措施,是本發(fā)明中的重大特色之一。對“截高取低”合理地進(jìn)行控制,可以達(dá)到對浸出稀土母液的除雜、富集工藝優(yōu)化的效果,其截高的點(diǎn)(中、高稀土濃度)1g/L,今后可進(jìn)一步根據(jù)生產(chǎn)實(shí)踐的情況進(jìn)行調(diào)整。(9)本發(fā)明應(yīng)用的新型浸礦劑及綜合的新的工藝技術(shù),使“其它相態(tài)”稀土得到部分地浸出,平均浸出率15~30%,為“其它相態(tài)”稀土資源的利用,探索了方法和途徑。(10)本發(fā)明研發(fā)了“液態(tài)稀土富集液”全套的生產(chǎn)工藝和產(chǎn)品,可為分離廠提供優(yōu)質(zhì)、直接進(jìn)槽使用的合格料液。(11)本發(fā)明試驗(yàn)室獲得浸出母液平均濃度5.6~6.4g/L,而現(xiàn)有技術(shù)工藝僅4.4~4.6g/L,比現(xiàn)有工藝提高了21.7~45.5%。按浸出液平均濃度計,本發(fā)明獲得的母液量3.7~4.2L,而現(xiàn)有工藝為4.99~5.0L,比現(xiàn)有工藝減少液量16~26%。本發(fā)明工藝比現(xiàn)有工藝浸出母液濃度提高,液量減少,既縮短浸礦周期,又減少了后續(xù)工序的處理量,使得綜合成本大為降低。(12)本發(fā)明研究和應(yīng)用的多種新型藥劑及全套的新型稀土浸出與富集工藝,廢水達(dá)標(biāo)排放,廢渣無危害、排入渣庫,極少量廢氣可自然排放,環(huán)保整體達(dá)標(biāo)。全新的藥劑與工藝技術(shù),確保了企業(yè)實(shí)現(xiàn)綠色生產(chǎn),達(dá)到企業(yè)、生產(chǎn)、環(huán)境相互友好的目的,從根本上解決了現(xiàn)有技術(shù)工藝中存在的環(huán)保問題。(13)本發(fā)明的工藝與現(xiàn)有工藝相比,技術(shù)、經(jīng)濟(jì)指標(biāo)全面提高,單位成本降低,相同條件下,產(chǎn)量增加20%,綜合經(jīng)濟(jì)效益提高25%。綜上所述,本發(fā)明有效地克服了現(xiàn)有技術(shù)工藝存在的主要問題:一是采用了全新的藥劑和研發(fā)了整套的全新工藝技術(shù);二是環(huán)保整體達(dá)標(biāo),企業(yè)可真正地實(shí)現(xiàn)綠色生產(chǎn);三是提高了浸出母液濃度,減少了液量及后續(xù)工序處理量,浸礦周期可縮短20~40%以上,降低成本,提高產(chǎn)量;四是對“其它相態(tài)”稀土利用問題摸索了途徑和方法,本發(fā)明對“其它相態(tài)”稀土資源利用平均可達(dá)15~30%以上;五是比現(xiàn)有技術(shù)工藝全面地提高了技術(shù)、經(jīng)濟(jì)指標(biāo),“全相”稀土回收率提高3~6%,單位直接成本降低,綜合效益提高25%;六是首次提出和建立稀土“控制浸出”的概念及其技術(shù)思想、措施、方法,創(chuàng)新研發(fā)對不同濃度稀土母液的處理工藝,獲得不同形態(tài)的稀土產(chǎn)品;七是本發(fā)明的“液態(tài)稀土富集液產(chǎn)品及其工藝技術(shù)”,完全能滿足現(xiàn)行分離廠對合格料液的要求,可直接進(jìn)槽分離;八是對“收縮劑”的研發(fā)和應(yīng)用,有利于改善和提高礦體結(jié)構(gòu)的穩(wěn)定性,減少“地質(zhì)災(zāi)害”事故的發(fā)生;九是本發(fā)明生產(chǎn)的稀土產(chǎn)品,非稀土雜質(zhì)含量低,為分離廠提供更為優(yōu)質(zhì)的原料。由此可見,現(xiàn)有技術(shù)工藝存在的一些突出問題,在本發(fā)明中都得到了很好的解決。本發(fā)明為現(xiàn)行離子型稀土礦山的生產(chǎn),提供了一整套全新的、有效的、先進(jìn)的、各項(xiàng)技術(shù)經(jīng)濟(jì)指標(biāo)優(yōu)異的生產(chǎn)工藝。以下是應(yīng)用本發(fā)明工藝的幾個具體實(shí)施例,通過具體的實(shí)施例來詳細(xì)地了解本發(fā)明的實(shí)現(xiàn)及其技術(shù)效果。其中,REO是指稀土氧化物(rareearthoxide),RE是指稀土(rareearth)。下述實(shí)施例中使用的浸礦劑由含鐵、錳和鈣的菱鎂礦制得,所述浸礦劑的制備過程為:礦石經(jīng)粉碎后用水調(diào)漿,然后加入酸分解至呈弱酸性,即得所述浸礦劑,得到的浸礦劑含有鎂、鐵、錳和鈣等復(fù)合陽離子。其中,所述菱鎂礦中鐵<10%、錳<3%、鈣<10%,所述百分比為質(zhì)量百分比。下述實(shí)施例中使用的收縮劑是由氯化鈣溶液結(jié)晶得到的固體產(chǎn)品,其是以石灰為原料,經(jīng)酸解得到氯化鈣溶液,再經(jīng)結(jié)晶所得。實(shí)施例1本實(shí)施例中的離子型稀土礦來自于贛州尋烏某稀土礦山,礦樣主要化學(xué)成分如表1所示。表1尋烏某離子型稀土礦主要成分表首先,進(jìn)行前期的準(zhǔn)備工作:1、補(bǔ)充地質(zhì)勘查;2、工程設(shè)計與施工;3、建設(shè)主要工程:(1)注液體系;(2)供水體系;(3)地下、地面收液體系;(4)濕法冶金體系;(5)供配電體系;(6)其它輔助體系;(7)離子吸附除雜、富集體系及儲罐(車)。然后,開始浸礦富集工作:步驟一:向礦體內(nèi)部注入浸礦劑和收縮劑,原地原位浸礦使“離子相”及部分“其它相態(tài)”稀土浸出,得到浸出母液;步驟二:向濃度≥1g/L的中、高濃度浸出母液中通入除雜劑I進(jìn)行除雜,除雜時控制pH≤5.2,除雜后經(jīng)沉淀劑沉淀,再經(jīng)清水洗滌、過濾、灼燒得到固態(tài)稀土產(chǎn)品;其中,所述除雜劑I為碳酸氫鈉溶液和碳酸鈉溶液的混合液,所述沉淀劑為碳酸氫鈉溶液;和向濃度<1g/L的低濃度浸出母液中通入除雜劑II中和去除鋁雜質(zhì),然后將除鋁后母液(即浸出母液經(jīng)除鋁后所得稀土上清液)通入離子交換柱中進(jìn)行稀土離子的吸附富集,再用酸進(jìn)行解吸,得到液態(tài)稀土產(chǎn)品;其中,所述除雜劑II為石灰乳。具體地,在浸礦的初、中期注入浸礦劑;當(dāng)浸出母液中的稀土含量越過峰值并下降至60%時,停止浸礦劑注入,改為注入頂水,在頂水中加入收縮劑一并注入,當(dāng)浸出母液中的稀土含量下降至0.1克/升時,停止注入頂水并收液,結(jié)束浸礦。結(jié)束浸礦后,對于濃度≥1g/L的中、高濃度浸出母液用碳酸氫鈉和碳酸鈉混合液除雜后,直接用碳酸氫鈉溶液沉淀,經(jīng)清水洗滌、過濾、灼燒得到“固態(tài)”稀土產(chǎn)品后送檢;對于濃度<1g/L的低濃度浸出母液用石灰乳除鋁后,上清液通入裝有大孔丙烯酸系陽離子交換樹脂的交換柱進(jìn)行吸附富集、除雜,經(jīng)鹽酸解析得到“液態(tài)”稀土產(chǎn)品后送檢。稀土礦樣經(jīng)浸礦劑浸出后所得中、高濃度混合稀土浸出母液主要化學(xué)成分如表2所示。表2中、高濃度混合稀土浸出母液的主要化學(xué)成分表名稱RE(g/l)Al(g/l)Mn+(g/l)中、高濃度混合稀土母液8.991.122.75稀土礦樣經(jīng)浸礦劑浸出后所得低濃度混合稀土浸出母液主要化學(xué)成分如表3所示。表3低濃度混合稀土浸出母液主要化學(xué)成分表元素REOAlFeCaMgSipH含量g/L0.980.33<0.010.051.830.033.7低濃度稀土浸出母液經(jīng)除鋁后所得稀土上清液主要化學(xué)成分如表4所示。表4除鋁后液主要化學(xué)成分表元素REAlFeCaMgSi除鋁上清液0.890.02<0.010.051.770.03實(shí)施例2稱取稀土礦樣(如表1所示)18kg放入浸出柱中,將配置好的浸礦劑對稀土礦樣進(jìn)行浸出。浸出的試驗(yàn)條件為原礦重量18kg,浸出劑濃度4wt%,浸出劑流速3ml/min,液固比(即浸礦劑與稀土礦樣的體積比)1:3.25。在上述試驗(yàn)條件下,離子相稀土浸出率為99.45%,“其它相態(tài)”稀土浸出率為30.02%,浸出母液中Fe、Al、Si雜質(zhì)相應(yīng)浸出率分別為0.73%、0.37%、1.93%。實(shí)施例3稱取稀土礦樣(如表1所示)18kg放入浸出柱中,將配置好的浸礦劑對稀土礦樣進(jìn)行浸出。浸出的試驗(yàn)條件為原礦重量18kg,浸出劑濃度2.5wt%,浸出劑流速3ml/min,液固比1:2.5。在上述試驗(yàn)條件下,離子相稀土浸出率為91.04%,“其它相態(tài)”稀土浸出率為12.5%,浸出母液中Fe、Al、Si雜質(zhì)相應(yīng)浸出率分別為0.68%、0.32%、1.86%。實(shí)施例4稱取稀土礦樣(如表1所示)18kg放入浸出柱中,將配置好的浸礦劑對稀土礦樣進(jìn)行浸出。浸出的試驗(yàn)條件為原礦重量18kg,浸出劑濃度3.5wt%,浸出劑流速2.5ml/min,液固比1:3.5。在上述試驗(yàn)條件下,離子相稀土浸出率為99.17%,“其它相態(tài)”稀土浸出率為22.51%,浸出母液中Fe、Al、Si雜質(zhì)相應(yīng)浸出率分別為0.85%、0.41%、1.89%。實(shí)施例5稱取稀土礦樣(如表1所示)18kg放入浸出柱中,將配置好的浸礦劑對稀土礦樣進(jìn)行浸出。浸出的試驗(yàn)條件為原礦重量18kg,浸出劑濃度4.5wt%,浸出劑流速2.5ml/min,液固比1:4.5。在上述試驗(yàn)條件下,離子相稀土浸出率為99.81%,“其它相態(tài)”稀土浸出率為27.51%,浸出母液中Fe、Al、Si雜質(zhì)相應(yīng)浸出率分別為0.91%、0.47%、2.04%。實(shí)施例6量取中、高濃度混合稀土浸出母液(如表2所示)1L,采用8%的碳酸氫鈉和10%的碳酸鈉1:1混合液進(jìn)行除雜、過濾,除雜試驗(yàn)條件為控制pH值為4.7,在上述試驗(yàn)條件下,稀土損失率為1.21%,所得稀土氧化物鋁含量為1.0%;過濾后上清液采用8%碳酸氫鈉進(jìn)行清水洗滌、過濾、灼燒,在上述試驗(yàn)條件下,稀土沉淀率為97.4%。實(shí)施例7量取中、高濃度混合稀土浸出母液(如表2所示)1L,采用8%的碳酸氫鈉和10%的碳酸鈉1:1混合液進(jìn)行除雜、過濾,除雜試驗(yàn)條件為控制pH值為4.7,在上述試驗(yàn)條件下,稀土損失率為1.81%,所得稀土氧化物鋁含量為0.42%;過濾后上清液采用8%碳酸氫鈉進(jìn)行清水洗滌、過濾、灼燒,在上述試驗(yàn)條件下,稀土沉淀率為97.19%。實(shí)施例8量取中、高濃度混合稀土浸出母液(如表2所示)4L,采用8%的碳酸氫鈉和10%的碳酸鈉1:1混合液進(jìn)行除雜、過濾,除雜試驗(yàn)條件為控制pH值為4.85,在上述試驗(yàn)條件下,稀土損失率為1.93%,所得稀土氧化物鋁含量為0.35%;過濾后上清液采用8%碳酸氫鈉進(jìn)行清水洗滌、過濾、灼燒,在上述試驗(yàn)條件下,稀土沉淀率為97.07%。實(shí)施例9量取低濃度混合稀土浸出母液(如表3所示)4L,加入燒杯中,開啟攪拌,不斷滴加石灰乳,用pH計監(jiān)控pH值,調(diào)pH值到5.0,繼續(xù)攪拌30min后并使pH值保持不變,終點(diǎn)后過濾,濾餅洗滌、干燥。在上述試驗(yàn)條件下,除鋁后液(即浸出母液經(jīng)除鋁后所得稀土上清液)中Fe<0.01g/L、Al為0.07g/L、Ca為0.05g/L、Mg為1.80g/L、Si為0.03g/L,稀土濃度為0.962g/L,稀土收率為99.39%。實(shí)施例10量取低濃度混合稀土浸出母液(如表3所示)4L,加入燒杯中,開啟攪拌,不斷滴加石灰乳,用pH計監(jiān)控pH值,調(diào)pH值到5.15,繼續(xù)攪拌30min后并使pH值保持不變,終點(diǎn)后過濾,濾餅洗滌、干燥。在上述試驗(yàn)條件下,除鋁后液(即浸出母液經(jīng)除鋁后所得稀土上清液)中Fe<0.01g/L、Al為0.02g/L、Ca為0.05g/L、Mg為1.75g/L、Si為0.03g/L,稀土濃度為0.941g/L,稀土收率為98.90%。實(shí)施例11量取低濃度混合稀土浸出母液(如表3所示)4L,加入燒杯中,開啟攪拌,不斷滴加石灰乳,用pH計監(jiān)控pH值,調(diào)pH值到5.3,繼續(xù)攪拌30min后并使pH值保持不變,終點(diǎn)后過濾,濾餅洗滌、干燥。在上述試驗(yàn)條件下,除鋁后液(即浸出母液經(jīng)除鋁后所得稀土上清液)中Fe<0.01g/L、Al為0.01g/L、Ca為0.05g/L、Mg為1.70g/L、Si為0.03g/L,稀土濃度為0.895g/L,稀土收率為96.59%。實(shí)施例12將其中裝有H型大孔丙烯酸系陽離子交換樹脂(以134克干重樹脂裝柱)的單級吸附柱(柱徑比8:1)進(jìn)行預(yù)處理,以600ml/h的流速、下進(jìn)上出的方式進(jìn)料(表4中所示料液),出口液體為吸附余液。初始階段,吸附余液無稀土,隨著吸附繼續(xù)進(jìn)行,吸附柱吸附的稀土越來越多,樹脂顏色由淺變深,32h后,出口吸附余液用草酸水檢測出稀土,繼續(xù)進(jìn)液,每1h取一個樣用EDTA溶液檢測稀土濃度,23h后出液稀土與進(jìn)液稀土濃度相等,樹脂飽和,用清水洗滌樹脂,直至出口無稀土,停止進(jìn)水,測稀土吸附余液。吸附飽和后采用4.5N鹽酸進(jìn)行解吸,解析速度控制為100ml/h,將吸附余液與解吸液分析檢測。在上述試驗(yàn)條件下,測得單柱樹脂總吸附量為21.35g稀土,飽和吸附容量為157.41mg/g;稀土解析率為99%,解析液最高濃度為RE=75g/L,Ca=0.8g/L,Mg=0.12g/L,Al=0.65g/L。實(shí)施例13準(zhǔn)備8根多級串聯(lián)已預(yù)處理的樹脂柱(同實(shí)施例12),以1000ml/h的流速、下進(jìn)上出(試驗(yàn)柱1底部進(jìn)料,試驗(yàn)柱8頂部流出)的方式進(jìn)料(表4中所示料液),實(shí)時檢測各吸附柱出口的液體稀土濃度,當(dāng)試驗(yàn)柱1出口有稀土后,每1h檢測第一根出口稀土濃度,41h后稀土濃度等于0.94g/L,試驗(yàn)柱1飽和,檢測試驗(yàn)柱3出口有稀土,試驗(yàn)柱4出口無稀土。一直進(jìn)料直到檢測試驗(yàn)柱8出口有稀土,繼續(xù)進(jìn)料,并收集出口稀土料液,直至試驗(yàn)柱8出口稀土濃度等于0.94g/L,停止進(jìn)料。用清水洗滌,洗至試驗(yàn)柱8出口無稀土,采用4.5N鹽酸解析,分段截取解析液,直至試驗(yàn)柱8出口無稀土停止進(jìn)鹽酸。在上述試驗(yàn)條件下,總共進(jìn)料260L,試驗(yàn)柱8出口液體(穿透液)37L,含稀土0.65g/L,8柱串聯(lián)吸附柱對稀土總吸附量為220.35g;解析液最高稀土濃度為183g/L,解析液稀土總量為218.45g,稀土解析率為99.14%,從最高稀土濃度解析液分析非稀土雜質(zhì)濃度為:Al=0.82g/L,Mg=0.62g/L,Ca=1.1g/L,F(xiàn)e=0.03g/L。實(shí)施例14準(zhǔn)備8根多級串聯(lián)已預(yù)處理的樹脂柱(同實(shí)施例12),以600ml/h的流速、下進(jìn)上出(試驗(yàn)柱1底部進(jìn)料,試驗(yàn)柱8頂部流出)的方式進(jìn)料(表4中所示料液),實(shí)時檢測各吸附柱出口液體稀土濃度,當(dāng)試驗(yàn)柱1出口有稀土后,每1h檢測第一根出口稀土濃度,65h后稀土濃度等于0.94g/L,第一根飽和,檢測試驗(yàn)柱3出口有稀土,試驗(yàn)柱4出口無稀土。一直進(jìn)料直至檢測試驗(yàn)柱8出口有稀土,繼續(xù)進(jìn)料,并收集出口稀土料液,直至試驗(yàn)柱8稀土濃度等于0.94g/L,停止進(jìn)料。用清水洗滌,直至試驗(yàn)柱8出口無稀土,采用5.5N鹽酸解析,分段截取解析液,直至試驗(yàn)柱8出口無稀土停止進(jìn)鹽酸。在上述試驗(yàn)條件下,總共進(jìn)料260.5L,試驗(yàn)柱8出口液體(穿透液)37L,含稀土0.58g/L,8柱串聯(lián)吸附柱對稀土總吸附量為220.83g;解析液最高稀土濃度215g/L,解析液稀土總量為219.51g,稀土解析率為99.40%,從最高稀土濃度解析液分析非稀土雜質(zhì)濃度為:Al=0.31g/L,Mg=0.52g/L,Ca=1.03g/L,F(xiàn)e=0.02g/L。從上述各實(shí)施例可以看出,相比現(xiàn)有技術(shù),本發(fā)明具有下述優(yōu)勢:第一、剔除了現(xiàn)有技術(shù)工藝采用的全部藥劑,本發(fā)明研發(fā)和采用了多種全新的藥劑;本發(fā)明還首次研究和引入了“收縮劑”藥劑與應(yīng)用技術(shù)。第二、現(xiàn)有技術(shù)工藝基本上只有“離子相”稀土的浸出,而本發(fā)明除了“離子相”稀土的浸出之外,還有部分“其它相態(tài)”稀土的浸出。第三、現(xiàn)有技術(shù)工藝對“浸出母液”的處理方法只有一種方法,即生產(chǎn)“固態(tài)”混合稀土的方法。而本發(fā)明中,對“浸出母液”有兩種處理方法,即把≥1g/L的中、高濃度稀土母液,進(jìn)入“固態(tài)”產(chǎn)品生產(chǎn)體系處理;把<1g/L的低濃度稀土母液,進(jìn)入“液態(tài)”產(chǎn)品生產(chǎn)體系處理。第四、本發(fā)明中研發(fā)的新型“液態(tài)稀土富集產(chǎn)品”生產(chǎn)工藝,其產(chǎn)品無論從稀土濃度或從非稀土雜質(zhì)含量來衡量,全部都能滿足現(xiàn)有分離廠對合格料液的要求,該產(chǎn)品能直接進(jìn)槽分離。第五、“液態(tài)稀土富集產(chǎn)品”生產(chǎn)工藝,革除了現(xiàn)生產(chǎn)礦山中,除雜、沉淀、脫水、壓濾、灼燒等生產(chǎn)過程,同時還革除了現(xiàn)分離廠的鹽酸分解、除雜等生產(chǎn)工藝過程。經(jīng)離子吸附、富集處理后,一次性地全面達(dá)到除雜與富集的效果,直接進(jìn)槽分離。大大縮短了加工工序,綜合成本降低,解決了固體稀土物料需再經(jīng)酸分解與分解中的酸霧污染問題。第六、本發(fā)明提出和建立了對稀土的浸出,實(shí)行“控制浸出”的概念與技術(shù)措施、方法。對不同濃度的浸出母液,實(shí)行“分類分流”處理,從而獲得不同形態(tài)的產(chǎn)品。創(chuàng)新的全套工藝與現(xiàn)行工藝相比,發(fā)生了革命性的變化,將極大地推動本領(lǐng)域內(nèi)的技術(shù)創(chuàng)新和發(fā)展。以上所述的具體實(shí)施例,對本發(fā)明的目的、技術(shù)方案和有益效果進(jìn)行了進(jìn)一步詳細(xì)說明,應(yīng)理解的是,以上所述僅為本發(fā)明的具體實(shí)施例而已,并不用于限制本發(fā)明,凡在本發(fā)明的精神和原則之內(nèi),所做的任何修改、等同替換、改進(jìn)等,均應(yīng)包含在本發(fā)明的保護(hù)范圍之內(nèi)。當(dāng)前第1頁1 2 3