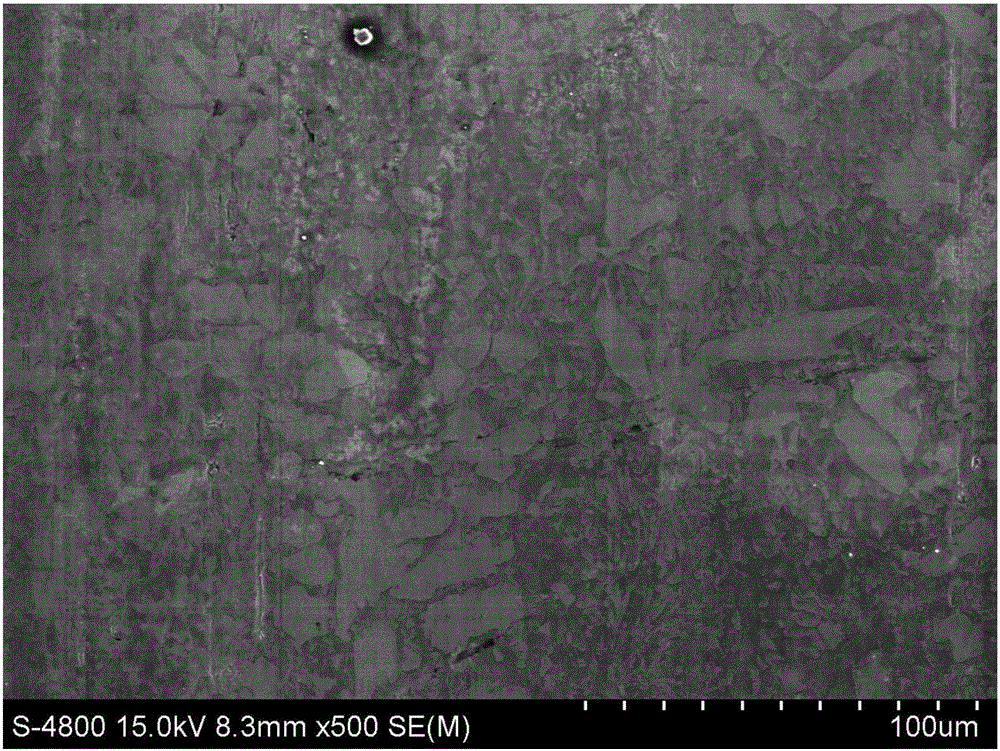
本發(fā)明屬于表面工程、冶金領(lǐng)域,涉及一種用于等離子弧堆焊鈷基合金粉末,特別是涉及一種等離子弧堆焊用耐高溫腐蝕及磨損涂層鈷基合金粉末。
背景技術(shù):
:在能源化工及熱電廠高溫及腐蝕介質(zhì)工況下,零部件表面磨損和腐蝕其的主要形式。目前采用表面工程技術(shù)如表面改性、表面堆焊等技術(shù)在基體表面沉積一層幾微米至幾毫米的涂層,從而賦予基體材料優(yōu)異的耐熱、耐蝕、耐磨和抗高溫氧化等性能。采用熱噴涂、埋弧堆焊、激光熔敷等工藝獲得的涂層存在一些質(zhì)量問題,如:涂層中存在致密度低、氣孔、氧化物夾雜等缺陷;焊接熱輸入不易控制,導(dǎo)致涂層成分稀釋率過大,涂層耐磨耐蝕性能下降;涂層厚度小和基體結(jié)合強度低、制備過程復(fù)雜、生產(chǎn)效率低等問題。采用等離子弧堆焊技術(shù)制造高溫耐磨耐蝕涂層,可以有效的解決上述問題,并擁有生產(chǎn)工藝條件易調(diào)節(jié)、操作簡單、易實現(xiàn)自動化生產(chǎn),并有效的降低生產(chǎn)成本。等離子弧堆焊技術(shù)是表面工程及再制造領(lǐng)域的一個分支,自上世紀(jì)六十年代人們在掌握獲得大功率、長壽命的等離子體發(fā)生器后,等離子電弧作為一種具有較高能量密度、電弧挺度的新型熱源廣泛地用在表面熔敷領(lǐng)域。等離子弧堆焊采用聯(lián)合弧或轉(zhuǎn)移弧熔化零件表面耐磨損耐腐蝕粉末,對零件表面進行改性,使零件表面獲得優(yōu)異的性能。其具有高效、低稀釋率、自動化程度高、堆焊用材料范圍廣等優(yōu)點,在國內(nèi)外已獲得迅速發(fā)展和廣泛使用。鈷基合金在高溫腐蝕介質(zhì)工況仍具有優(yōu)異的耐磨、耐腐蝕、抗氧化等性能。特別是其紅硬性好,抗摩擦磨損和腐蝕磨損性能好,可以在惡劣的環(huán)境下使用。常用的鈷基合金粉末為Co-Cr-W系和Co-Cr-Mo系,堆焊這些合金粉末獲得熔敷層,雖然可以在一定程度上改善基體金屬耐熱、耐磨損能,但其高溫抗腐蝕能仍待提高,在Na2SO4-K2SO4混合鹽900℃保溫200h后,涂層的發(fā)生嚴重的硫化其內(nèi)硫化物深度可達55um并生成大量的氧化物。有研究表明Co-25Cr-10Ni-4Al-5Ta-0.5Y具有很好的耐高溫腐蝕性能,但是其顯微硬度最佳僅為650~700HV0.5,耐磨損性能不足。堆焊層的耐磨損和耐腐蝕性不足均使涂層的使用持久性能降低,從而使粉末的使用范圍受到了一定的局限性。技術(shù)實現(xiàn)要素:本發(fā)明為了解決上述現(xiàn)有的鈷基合金存在的不足,提供一種等離子弧堆焊用耐高溫腐蝕及磨損鈷基粉末。該粉末通過在合金粉末中加入Al和稀土元素,并采用機械合金化方法獲得一種具有良好的高溫耐磨損、耐腐蝕性能且性能穩(wěn)定的等離子弧堆焊用耐高溫腐蝕及磨損鈷基合金粉末。本發(fā)明采用合理的粉末配比和行星式球磨機機械合金化方法制得成分混合均勻、粒度適中、活性較高的鈷基合金粉末,較霧化制粉簡單易行、節(jié)約成本,復(fù)合國家節(jié)能減排的環(huán)保理念。本發(fā)明的技術(shù)方案為:一種等離子弧堆焊用耐高溫腐蝕及磨損鈷基粉末,包含Cr、Mo、Si、Al、Ta、氧化釔、氧化鈰,粉末各組分質(zhì)量百分數(shù)如下:Cr:12~14%;Mo:20~24%;Si:2.5~3.2%;Al:3~6%;Ta:1~3%;氧化釔:0.3~0.8%;氧化鈰:0.1~0.2%;余量為Co,原始粉末的粒徑范圍為200~350目。所述的耐高溫腐蝕及磨損鈷基粉末的制備方法,包括以下步驟:1)配料:將初始粉末按照以上比例進行配料,初始粉末為99.99wt%的鈷粉,99.99wt%的鉻粉,99.99wt%鉬粉,99.95wt%硅粉,99.99wt%鋁粉,99.95wt%鉭粉,99.95wt%氧化釔,99.95wt%氧化鈰;2)球墨:采用行星式球磨機,將步驟1)配比好的粉末和磨球按照10:1的比例一起放到球磨罐中,并加入步驟1)配比好的粉末質(zhì)量的0.5~0.7%的硬脂酸作為過程控制劑,并在Ar氣氛圍下,以轉(zhuǎn)速150~200r/min球墨10~15h,最后冷卻到室溫;3)出粉:用150目和300目粒徑的篩子對步驟2)獲得的粉末進行篩分,獲得粒徑為150~300目的混合粉末。上述耐高溫腐蝕及磨損鈷基粉末的制備方法中,所涉及的原材料及實驗設(shè)備均通過公知的途徑獲得,所采用的操作工藝是本領(lǐng)域技術(shù)人員所掌握的。所述的等離子弧堆焊用耐高溫腐蝕及磨損鈷基粉末的應(yīng)用,用作等離子轉(zhuǎn)移弧同步送粉堆焊時的原料,在工件表面堆焊涂層。本發(fā)明的有益效果為:本發(fā)明通過對Cr、Mo、Si、Al以及氧化釔、氧化鈰等稀土氧化物進行合理的成分配比,在保證鈷基合金強度、耐磨性的同時又能保持其高的抗氧化、抗硫化能力。具體體現(xiàn)在:(1)本發(fā)明制備等離子弧用鈷基合金粉末工藝簡單,原材料來源廣泛,設(shè)備要求低,降低了等離子弧焊用鈷基合金粉末的生產(chǎn)成本。(2)本發(fā)明的高溫耐腐蝕鈷基合金粉末,將其等離子弧堆焊制得的涂層浸入75%Na2SO4+25%K2SO4混合鹽中,在900℃條件下保溫120h后取出試樣,觀察其截面金相形貌,在靠近外表面層區(qū)域有完整的析出物層,進行35S放射性同位素示蹤技術(shù),S侵入基體的深度為22um左右,而一般鈷基合金S元素的侵入深度可以達到55um左右,本發(fā)明的高溫抗腐蝕鈷基合金有優(yōu)異的抗氧化、抗硫化能力,使涂層在高溫硫化環(huán)境中持久性得到了提升。(3)本發(fā)明的高溫耐腐蝕鈷基合金粉末,對其等離子弧堆焊制得的涂層進行600℃高溫銷-盤滑行磨損試驗,在載荷32N滑行900m測得失重量為65mg,而一般的鈷基合金失重量在128~150mg,耐磨損性能提升了2~2.5倍,充分提高了工件的使用效率,提高了生產(chǎn)效率、節(jié)約能源,響應(yīng)國家綠色再制造的號召。附圖說明下面結(jié)合附圖和實施例對本發(fā)明進一步說明。圖1為本發(fā)明實施例1處理后典型顯微組織200倍金相照片;圖2為本發(fā)明實施例1取試樣進行高溫磨損后的表面形貌的SEM照片;具體實施方式下面為本發(fā)明的較佳實施例進行詳細闡述,便于本領(lǐng)域的技術(shù)人員理解,明確本發(fā)明的保護范圍并做出明確的界定,下面的實例均在本發(fā)明的技術(shù)方案前提下進行。本發(fā)明所述一種耐高溫磨損及腐蝕鈷基粉末,所述鈷基粉末由Co、Cr、Mo、Si、Al、Ta、氧化釔、氧化鈰八種成分組合而成,純度為:99.99wt%的鈷粉,99.99wt%的鉻粉,99.99wt%鉬粉,99.95wt%硅粉,99.99wt%鋁粉,99.95wt%鉭粉,99.95wt%氧化釔,99.95wt%氧化鈰,粒徑范圍為200~350目。所述鈷基粉末中各成分中所占百分比均為重量比。表一為各實施例中鈷基粉末的成分重量百分比(其余為Co)實施例CrMoSiAlTa氧化釔氧化鈰112202.531.50.30.1213232.541.50.30.15313233.2520.50.15414233.2620.50.2514243.2530.80.2實施例1第一步,配料使用精度為0.01g的天平對各組分按表一實例1各組分重量百分比進行配料1000g,并按總重量的0.5wt%稱量5g的硬脂酸。第二步:球墨按照球磨比為1:10,稱量所需要磨球的重量,需要注意的是,磨球要求不同直徑的混合球,將磨球、混合粉及硬脂酸末放到球磨罐中,其中硬脂酸作為過程控制劑防止球磨過程中粉末出現(xiàn)粘合現(xiàn)象,后用Ar氣對密封好的球磨罐進行6次充放氣,保證球磨罐中為Ar環(huán)境,避免球磨過程中合金組分被氧化,設(shè)定行星式球磨機轉(zhuǎn)速為150r/min時間為10h,球墨結(jié)束后,將球磨罐放到冰箱里,使球磨罐溫度冷卻到室溫。第三步:出粉將300目的篩子置于150目的篩子下面,將球磨罐中的磨球和粉末導(dǎo)入到篩子上面,進行篩分,獲得粒度范圍為150~300目的鈷基粉末。實施例2目標(biāo)成分為表一實例2,配料、出粉如實施例一所示,不同之處為:在球墨時,設(shè)定轉(zhuǎn)速為150r/min,球磨時間為15h得到鈷基粉末。實施例3目標(biāo)成分為表一實例3,配料、出粉如實施例一所示,不同之處為:在球墨時,設(shè)定轉(zhuǎn)速為180r/min,球磨時間為12h,得到鈷基粉末。實施例4目標(biāo)成分為表一實例4,配料、出粉如實施例一所示,不同之處為:在球墨時,設(shè)定轉(zhuǎn)速為180r/min,球磨時間為15h,得到鈷基粉末。實施例5目標(biāo)成分為表一實例5,配料、出粉如實施例一所示,不同之處為:在球墨時,設(shè)定轉(zhuǎn)速為200r/min,球磨時間為12h,得到鈷基粉末。將上述五種實例得到的鈷基粉末,按照表二的工藝參數(shù)在長寬高為100mm*100mm*25mm的316L不銹鋼板材上面分別進行等離子弧堆焊表二等離子弧焊接工藝參數(shù)按照MG-2000型高溫高速摩擦磨損試驗機試樣要求分別從各實例對應(yīng)的堆焊板材上面取下尺寸為φ6mm*12mm的試樣3個,將上面取得試樣分為三組,分別進行下面的測試。(1)分別觀察各實例堆焊得到的涂層金相組織,并根據(jù)顯微維氏硬度計參考GBT4340.1-2009國家標(biāo)準(zhǔn)測定各實施例試樣的顯微硬度;其硬度、抗拉強度、密度如表4所示。(2)高溫摩擦磨損實驗,在600℃下載荷為32N滑行900m,利用精密天平分別測試各實例試樣的磨損失重量,并對其磨損形貌進行觀察;(3)高溫硫酸鹽腐蝕實驗,將樣品鈷基涂層浸入75%Na2SO4+25%K2SO4混合鹽里,在900℃高溫下保溫120h,對試樣進行35S放射性示蹤試驗,并對其斷面腐蝕形貌進行觀察,測定S元素侵蝕深度;各實例測得顯微硬度、磨損失重量、S元素侵蝕深度如表三表三實施例顯微硬度(HV0.5)磨損失重量(mg)S元素侵蝕深度(um)1950713029807027311006422411506424511003223本發(fā)明等離子弧堆焊用鈷基合金粉末,在保證鈷基合金高硬度的同時使其高溫耐磨損能力和抗腐蝕能力提高一倍以上,有效的增加了工件的使用壽命,節(jié)約了金屬資源,復(fù)合國家節(jié)約能源的理念。本發(fā)明Cr含量設(shè)計為12~14%。鈷基合金中Cr元素用來提高耐腐蝕性和增強固溶體,其可以促進富鈷固溶體在高溫時的fcc結(jié)構(gòu)向室溫富鈷固溶體hcp結(jié)構(gòu)的轉(zhuǎn)變。本發(fā)明Mo的含量設(shè)計為20~24%,Si元素含量為2.5~3.2%,Mo元素和Si元素可以通過形成Co3Mo2Si這種Laves相,來提高鈷基合金的硬度和耐磨損性能,Mo元素可以使α-Co在室溫下穩(wěn)定,進而也可以增強固溶體。合理的搭配Mo元素和Si元素的含量,使鈷基合金為過共晶組織,在保證鈷基合金韌性的同時,生成盡可能多的Laves相。從圖1金相圖中可以看出在鈷基體上均勻分布著Laves相,有效的提高了堆焊層的硬度和耐磨損性能。圖2顯示堆焊層經(jīng)過高溫磨損后堆焊層無脫落、劃痕等,展示了堆焊層的高溫耐磨損性能。本發(fā)明Al的含量設(shè)計為3~6%,Ta元素含量設(shè)計為1~3%。Al元素和Ta元素是活性較強的元素,可以在高溫環(huán)境中,優(yōu)先和O、S等元素發(fā)生反應(yīng),微量的Ta元素優(yōu)先反應(yīng)生成Ta2O5,作為形核質(zhì)點促進Al2O3氧化膜的形成,由于Al2O3氧化膜非常致密,可以阻止S元素的侵蝕,提高鈷基合金的高溫耐腐蝕能力。本發(fā)明氧化釔含量設(shè)計為0.3~0.8%,氧化鈰含量設(shè)計為0.1~0.2。添加微量的稀土氧化物提高了鈷基合金的耐氧化能力并較少Cr的含量,一般鈷基合金Cr含量在25%以上才能形成連續(xù)的Cr2O3氧化膜。稀土氧化物可以作為CoCr2O4、Cr2O3等氧化物的形核質(zhì)點,從而可以在合金表面形成以Cr2O3、CoO·Cr2O3為主的含有Cr2O3(Y2O3)、CrY2S4、Ce2O3的氧化膜,提高了氧化膜和基體的粘著性,并且在鉻氧化膜中氧化釔和氧化鈰往往在晶界及位錯缺陷處,阻礙了原子的擴散通道。所以它們既阻礙氧、硫向內(nèi)部的擴散侵入,又阻礙了鉻的短程遷移,減緩氧化腐蝕速度。另外,通過調(diào)節(jié)合金成分中的不同質(zhì)量百分比,使得到的鈷基合金性能高低不一。本發(fā)明所述的是一種耐高溫腐蝕及磨損的鈷基合金,通過向鈷基合金中添加Cr、Mo、Si、Al、Ta合金元素及氧化釔、氧化鈰稀土氧化物,提高鈷基合金的高溫強度、耐腐蝕及耐磨能力,改善了持久強度,提升了穩(wěn)定性,改善了高溫鈷基合金的品質(zhì)。以上是本發(fā)明的具體實施方式,但是本發(fā)明的保護范圍不局限于此,任何熟悉本領(lǐng)域的相關(guān)技術(shù)人員在本發(fā)明所揭露的技術(shù)范圍內(nèi),不經(jīng)創(chuàng)造性想到的變化或替換,都應(yīng)該涵蓋在本發(fā)明的本發(fā)明的保護范圍之內(nèi),因此,本發(fā)明的保護范圍應(yīng)該以權(quán)利要求書所限定的保護范圍為準(zhǔn)。本發(fā)明未盡事宜為公知技術(shù)。當(dāng)前第1頁1 2 3