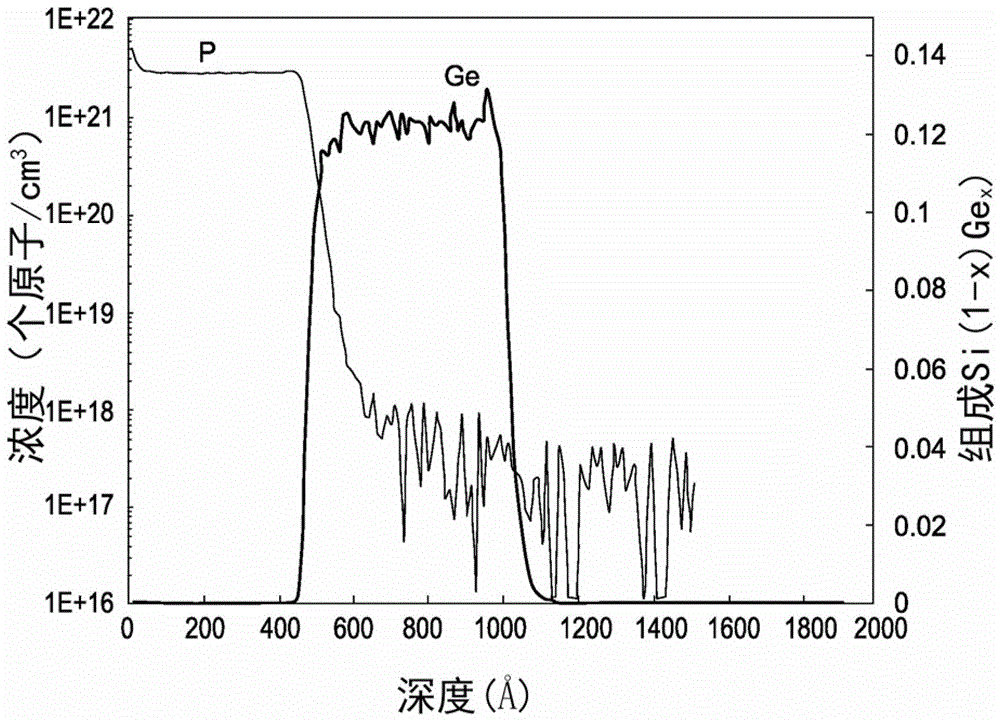
用于拉伸應(yīng)變應(yīng)用上的高拉伸硅合金的外延法發(fā)明背景發(fā)明領(lǐng)域本發(fā)明的實施例大體上涉及半導(dǎo)體制造工藝與半導(dǎo)體器件的領(lǐng)域,更具體地說,本發(fā)明的實施例涉及沉積含硅膜以供形成半導(dǎo)體器件的方法。相關(guān)技術(shù)的描述金氧半導(dǎo)體場效晶體管(MOSFET)的尺寸減少已使集成電路的每單元功能上的速度性能、密度、成本有持續(xù)的改善。一項改善晶體管性能的方法是通過對晶體管溝道區(qū)域施加應(yīng)力。應(yīng)力扭曲半導(dǎo)體晶格(例如,使半導(dǎo)體晶格產(chǎn)生應(yīng)變),且所述扭曲進而影響半導(dǎo)體的能帶排列(bandalignment)與電荷傳輸性質(zhì)。通過控制完成的器件中的應(yīng)力量級,制造商能夠增加載流子遷移率(carriermobility)并且改善器件性能。有數(shù)種既存的將應(yīng)力導(dǎo)進晶體管溝道區(qū)域的途徑。一項此類將應(yīng)力導(dǎo)進晶體管溝道區(qū)域的途徑是將碳在所述區(qū)域形成期間并入所述區(qū)域。存在于所述區(qū)域的碳影響半導(dǎo)體晶格,因而引起應(yīng)力。然而,外延沉積膜的質(zhì)量隨著膜內(nèi)碳濃度增加而降低。因此,對于在膜質(zhì)量變得無法接受之前能引起的拉伸應(yīng)力的量有所限制。大體而言,高于約1原子百分比的碳濃度嚴重地降低膜質(zhì)量并且增加膜生長問題的可能性。例如,諸如非期望的多晶硅或非晶硅生長(而非外延式生長)之類的膜生長的問題可能發(fā)生,這是由于大于1原子百分比的碳濃度存在的緣故。因此,通過并入碳而增加膜的拉伸應(yīng)力所能獲得的益處受限于膜的碳濃度在1原子百分比或更低。再者,甚至連含有低于1原子百分比的碳的膜都仍會經(jīng)歷一些膜質(zhì)量的問題。因此,需要生產(chǎn)實質(zhì)上無碳的高拉伸應(yīng)力的外延膜。
技術(shù)實現(xiàn)要素:本發(fā)明的實施例大體上涉及用于在半導(dǎo)體器件上形成硅外延層的方法。這些方法包括在增加的壓力與降低的溫度下在襯底上形成硅外延層。所述硅外延層具有每立方厘米約1x1021個原子或更大的磷濃度,并且不添加碳而形成所述硅外延層。每立方厘米約1x1021個原子或更大的磷濃度增加沉積層的拉伸應(yīng)變,而因此所述磷濃度改善溝道遷移率。因為外延層實質(zhì)上無碳,因此外延層不會遭受通常與含碳外延層有所關(guān)聯(lián)的膜形成與質(zhì)量問題。在一個實施例中,在襯底上形成膜的方法包含將襯底定位于處理腔室內(nèi),以及加熱所述襯底達一溫度,所述溫度是在從約550攝氏度至約700攝氏度的范圍內(nèi)。一或多種工藝氣體隨后導(dǎo)進處理腔室。所述一或多種工藝氣體包含硅源以及磷源。實質(zhì)上無碳的硅外延層隨后沉積在襯底上。所述實質(zhì)上無碳的硅外延層具有磷濃度,所述磷濃度為每立方厘米約1x1021個原子或更大。實質(zhì)上無碳的硅外延層在約300托(Torr)或更大的腔室壓力下沉積。另一實施例中,在襯底上形成膜的方法包含將襯底定位于處理腔室內(nèi),以及加熱所述襯底達一溫度,所述溫度是在從約600攝氏度至約650攝氏度的范圍內(nèi)。一或多種工藝氣體隨后導(dǎo)進處理腔室。所述一或多種工藝氣體包含硅源以及磷源。實質(zhì)上無碳的硅外延層隨后沉積在襯底上。所述實質(zhì)上無碳的硅外延層具有每立方厘米約1x1021個原子或更大的磷濃度,且所述實質(zhì)上無碳的硅外延層在約300托(Torr)或更大的腔室壓力下沉積。另一實施例中,在襯底上形成膜的方法包含將襯底定位于處理腔室內(nèi),以及加熱所述襯底達一溫度,所述溫度是在從約550攝氏度至約750攝氏度的范圍內(nèi)。膦與甲硅烷(silane)或乙硅烷(disilane)的至少一種隨后導(dǎo)入處理腔室,并且將實質(zhì)上無碳的硅外延層沉積在襯底上。所述實質(zhì)上無碳的硅外延層具有每立方厘米約1x1021個原子或更大的磷濃度,且所述實質(zhì)上無碳的硅外延層在約150托(Torr)或更大的腔室壓力下沉積。附圖簡單說明通過參考實施例(一些實施例說明于附圖中),可得到發(fā)明內(nèi)容中簡要總結(jié)的本發(fā)明的更特定的描述,而詳細理解本發(fā)明于發(fā)明內(nèi)容所記載的特征。然而,應(yīng)注意,附圖僅說明此發(fā)明的典型實施例,而因此不應(yīng)將附圖視為限制本發(fā)明的范圍,因本發(fā)明可容許其它等效實施例。圖1是流程圖,所述流程圖說明形成含磷的硅外延層的方法。圖2是圖表,所述圖表說明根據(jù)本發(fā)明實施例形成的膜的摻雜分布曲線。圖3是圖表,所述圖表說明圖2的膜的拉伸應(yīng)力。為了助于理解,如可能則使用相同元件符號指定各圖共有的相同元件。應(yīng)考慮一個實施例的元件可有利地用于其它實施例而無須特別記敘。具體描述本發(fā)明的實施例大體上涉及用于在半導(dǎo)體器件上形成硅外延層的方法。這些方法包括在增加的壓力與降低的溫度下在襯底上形成硅外延層。所述硅外延層具有每立方厘米約1x1021個原子或更大的磷濃度,并且不添加碳而形成所述硅外延層。每立方厘米約1x1021個原子或更大的磷濃度增加沉積層的拉伸應(yīng)變,而因此所述磷濃度改善溝道遷移率。因為外延層實質(zhì)上無碳,所以外延層不會遭受通常與含碳外延層有所關(guān)聯(lián)的膜形成與質(zhì)量問題。在此所用的“實質(zhì)上無碳”是指不使用含碳前驅(qū)物形成的膜;然而,應(yīng)考慮到,痕量的碳可能由于污染而存在于所述膜中。本發(fā)明的實施例可在RPEpi腔室中實施,所述腔室可購自美國加州SantaClara的應(yīng)用材料公司。應(yīng)考慮其它腔室(包括可購自其它制造商的腔室)可用于實施本發(fā)明的實施例。圖1是流程圖100,所述流程圖說明形成含磷的硅外延層的方法。在步驟102,單晶硅襯底定位在處理腔室內(nèi)。在步驟104,襯底被加熱到預(yù)定溫度。所述襯底一般被加熱到從約550攝氏度到約700攝氏度的范圍內(nèi)的溫度。期望通過將襯底加熱到足以熱分解處理試劑(reagent)并且在襯底上沉積外延膜的最低溫度,而使最終器件的熱預(yù)算減至最小。然而,因為增加溫度一般導(dǎo)致處理量增加,應(yīng)考慮可依生產(chǎn)需要所指定使用較高的溫度。在步驟106中,含有一或多個處理試劑的工藝氣體導(dǎo)進處理腔室中。所述工藝氣體包括硅源與磷源以供在襯底上沉積含磷的硅外延層。視情況任選,所述一或多種工藝氣體可包括載氣以便將硅源與磷源輸送至處理腔室,在執(zhí)行選擇性沉積工藝時,所述一或多種工藝氣體也可包括蝕刻劑。示例性磷源包括膦,可以約2sccm至約30sccm的流量(或更大的流量)將膦輸送到處理腔室。例如,膦的流量可為約12sccm至約15sccm。適合的 載氣包括氮、氫或其它相對于沉積工藝為惰性的氣體。可用范圍從約3slm至約30slm的流量提供所述載氣到處理腔室。適合的硅源包括二氯硅烷、甲硅烷與乙硅烷??捎媒橛诩s300sccm至400sccm之間的流量將硅源輸送到處理腔室。雖考慮其它的硅源與磷源,一般仍期望盡量減少碳添加到處理氣氛,因此,應(yīng)避免含碳前驅(qū)物。在步驟108中,試劑的混合物受熱驅(qū)動而反應(yīng)并且在襯底表面上沉積含磷的硅外延層。在沉積工藝期間,處理腔室內(nèi)的壓力維持在約150托或更大,例如約300托至約600托。應(yīng)考慮,在不利用低壓沉積腔室時,可使用超過約600托的壓力。相較下,在低壓沉積腔室中典型的外延生長工藝維持約10托到約100托的處理壓力以及超過700攝氏度的處理溫度。然而,通過增加壓力到約150托或更大,沉積的外延膜形成為具有相較于低壓外延生長工藝而言更高的磷濃度(例如,每立方厘米約1x1021個原子到每立方厘米約5x1021個原子)。再者,低壓沉積期間提供的高流量的磷源氣體經(jīng)常造成襯底的表面毒害(surfacepoisoning),表面毒害會抑制外延形成。在大于300托的壓力下處理時,一般不會經(jīng)歷表面毒害,這是由于硅源通量克服毒害效應(yīng)的緣故。因此,對于利用高摻雜劑流量的外延工藝而言,期望增加處理壓力。當提供膦流量為約3sccm至約5sccm時,在低于100托的壓力下形成的外延膜的磷濃度大約是每立方厘米3x1020個原子。因此,相較于在低于約100托或更低的壓力形成的外延膜,在較高壓力(例如300托或更大)形成的外延層在磷濃度上會經(jīng)歷大約十倍的增加。相信在每立方厘米約1x1021個原子或更大的磷濃度下,沉積的外延膜并非純粹是以磷摻雜的硅膜,所述膜反而是介于硅與磷化硅(例如類立方體Si3P4)之間的合金(alloy)。相信硅/磷化硅合金對外延膜的拉伸應(yīng)力增加有所貢獻。形成硅/磷化硅合金的可能性隨著磷濃度增加而增加,因為相鄰磷原子交互作用的概率增加。在約550攝氏度至約750攝氏度之間的處理溫度及大于300托的壓力下形成的外延膜在被摻雜至足夠的磷濃度(例如每立方厘米約1x1021個原子或更大)時會經(jīng)歷增加的拉伸應(yīng)力。在此類條件下形成的無碳外延膜經(jīng)歷約1GPa(十億帕斯卡)至約1.5GPa的拉伸應(yīng)力,前述拉伸應(yīng)力與含有約1.5原子百分比的碳的低壓硅外延膜等效。然而,如前文所述,含有超過約1原子百分比的碳的外延膜遭受膜質(zhì)量降低而因此是不期望的。再者,碳摻雜的硅外延工藝 一般利用循環(huán)沉積蝕刻工藝,所述工藝增加了工藝的復(fù)雜度與成本。根據(jù)本文的實施例生產(chǎn)外延膜不僅造成膜具有比含1.5原子百分比的碳的外延膜更高或相等的拉伸應(yīng)力,且無碳膜的電阻率也較低(例如,相較于約0.9毫歐姆厘米,無碳膜的電阻率為約0.6毫歐姆厘米)。因此實質(zhì)上無碳的外延膜相較于含碳外延膜呈現(xiàn)更高的膜質(zhì)量、較低的電阻率以及等效的拉伸應(yīng)力。外延生長膜的拉伸應(yīng)變能進一步增加,這是通過降低外延生長工藝期間的沉積溫度而實現(xiàn)的。在第一實例中,磷摻雜的硅外延膜是在700托的腔室壓力與約750攝氏度的溫度下沉積。生長工藝期間,將含有300sccm的二氯硅烷及5sccm的膦的工藝氣體提供到處理腔室。所述沉積膜含有磷濃度約每立方厘米3x1020個原子并且呈現(xiàn)與具有碳濃度約0.5原子百分比的硅外延膜相等的拉伸應(yīng)變。第二實例中,磷摻雜硅外延膜是在另一襯底上于類似工藝條件下沉積;然而,處理溫度降低到約650攝氏度,而膦流量增加到20sccm。磷摻雜的硅外延膜的拉伸應(yīng)變與含有1.8原子百分比的碳的膜等效。因此,當處理溫度降低而摻雜劑濃度增加時,沉積的外延膜內(nèi)的拉伸應(yīng)變增加。然而應(yīng)注意,降低的溫度造成的拉伸應(yīng)變的益處可能有所限制,因為存在反應(yīng)與沉積處理試劑所需的最小溫度。第三實例中,磷摻雜硅外延膜在與第一實例類似的工藝條件下形成;然而,處理期間的膦流量降低到約2sccm。所得的磷摻雜硅外延膜的拉伸應(yīng)變與具有約0.2原子百分比的碳的膜等效。此外,相較于第一實例的膜的電阻率為0.60毫歐姆厘米,所得的膜具有約0.45毫歐姆厘米的電阻率。因此,不僅外延膜的拉伸應(yīng)變可通過在沉積工藝期間變化溫度及/或壓力而調(diào)整,連電阻率也能通過變化提供至處理腔室的摻雜劑的量而調(diào)整。圖2是圖表,所述圖表說明根據(jù)本發(fā)明實施例形成的膜的摻雜劑分布曲線。圖2中所分析的膜是通過將硅襯底(在所述硅襯底上具有硅鍺層)加熱到約650攝氏度的溫度而形成。大約300sccm的二氯硅烷與30sccm的膦輸送到維持在約600托的壓力下的處理腔室。450埃的硅外延膜形成于硅鍺層上。如二次離子質(zhì)譜儀所測定,磷摻雜的外延膜具有均勻的磷濃度且實質(zhì)上無碳,所述磷濃度為每立方厘米約3x1021個原子。相較于圖2所分析的膜,在較低壓力下(諸如低于300托)形成的外延膜具有每立方厘米約3x1020個原子的磷濃度。因此,根據(jù)本文描述實施例所形成的外延膜相較于較低壓力下形成的外延膜在 磷濃度上呈現(xiàn)十倍的增加。圖3是說明如高分辨率X光繞射法測定的圖2的膜的拉伸應(yīng)力的圖表。峰A對應(yīng)到單晶硅襯底的拉伸應(yīng)力,而峰B對應(yīng)硅鍺層的拉伸應(yīng)力。峰C對應(yīng)含磷外延層的拉伸應(yīng)力。明確界定的峰B與峰C的邊緣指出具有均勻組成的高質(zhì)量外延膜。峰B對應(yīng)硅鍺外延層,所述硅鍺外延層含有約12.3原子百分比的鍺。峰B具有約-1000弧秒至約-1500弧秒之間的偏移(例如壓縮的應(yīng)力)以及約1000a.u.的強度。峰C具有約1700弧秒至約2400弧秒之間的峰偏移(例如拉伸應(yīng)力)與約800a.u.的強度。對應(yīng)峰C的應(yīng)力類似于碳濃度約1.8原子百分比的外延膜的應(yīng)力。如前文所討論,含有超過約1原子百分比的碳的外延膜具有無法接受的膜質(zhì)量。因此,雖然高磷摻雜的外延膜的拉伸強度大約等于含1.8原子百分比的碳的外延膜,所述高磷摻雜的外延膜呈現(xiàn)比相當拉伸應(yīng)變的碳摻雜外延膜更高的膜品質(zhì)。本發(fā)明的益處包括呈現(xiàn)高拉伸應(yīng)變的高質(zhì)量硅外延膜。增加的處理壓力結(jié)合降低的處理溫度容許形成磷濃度為每立方厘米3x1021個原子或更大的硅外延膜而不經(jīng)歷表面毒害。高磷濃度引起沉積的外延膜內(nèi)的應(yīng)力,因而增加拉伸應(yīng)變,導(dǎo)致載流子遷移率增加并且改善器件性能。高磷摻雜外延硅獲得的拉伸應(yīng)變與含有高達1.8原子百分比的碳的外延膜相當。然而,本發(fā)明的高磷摻雜的外延硅避免了與碳摻雜膜相關(guān)聯(lián)的質(zhì)量問題。前述內(nèi)容關(guān)于本發(fā)明的實施例,可不背離本發(fā)明的基本范圍而設(shè)計其它與進一步的本發(fā)明實施例,本發(fā)明的范圍由隨后的權(quán)利要求書所決定。