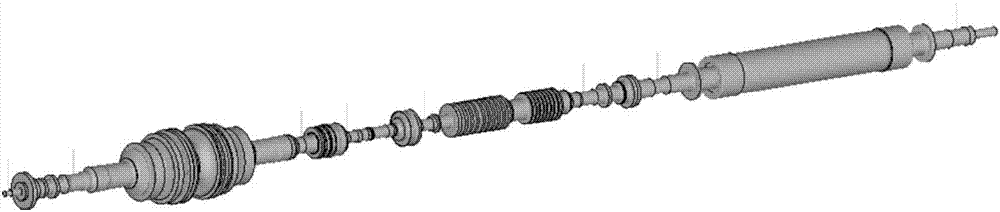
本發(fā)明屬于透平機械轉(zhuǎn)子軸承系統(tǒng)的數(shù)值模擬
技術(shù)領域:
,具體涉及一種通過調(diào)整軸承標高控制聯(lián)合循環(huán)機組振動的優(yōu)化方法。
背景技術(shù):
:在燃氣-蒸汽聯(lián)合循環(huán)供熱機組中,為了使機組供熱最大化,可采用sss離合器技術(shù),將其置于中壓轉(zhuǎn)子和低壓轉(zhuǎn)子之間。通過控制sss離合器的嚙合與分離,可以使機組在抽凝供熱工況和被壓供熱工況間進行轉(zhuǎn)換,其中sss離合器分離對應凝氣供熱工況轉(zhuǎn)背壓供熱工況,嚙合對應背壓供熱工況轉(zhuǎn)凝氣供熱工況。理論分析和試驗研究表明,sss離合器的存在會對燃氣-蒸汽聯(lián)合循環(huán)的軸系振動產(chǎn)生很大影響,軸系設計缺陷將會導致振動加劇,甚至損傷設備。因此,針對聯(lián)合循環(huán)機組軸系,研究安裝參數(shù)對軸系動力特性的影響,進而達到通過調(diào)整安裝參數(shù)來抑制振動的目的,對燃氣-蒸汽聯(lián)合循環(huán)機組的振動安全性有著重要的影響。傳統(tǒng)的軸系動力特性模擬方法基于有限元計算方法,建立軸系有限元分析模型獲得軸系振動響應曲線。由于非線性軸承油膜力的存在,傳統(tǒng)的軸系計算方法無法模擬軸承標高對軸系振動特性的影響。此外,由于非對稱電機轉(zhuǎn)子的存在,有限元法必須建立三維整機模型,同時為了研究不同軸承標高下的多轉(zhuǎn)速下的響應,需進行大量工況的計算才能獲得軸承標高對機組的影響規(guī)律,這樣的反復計算會加大對計算時間和計算機資源的需求。技術(shù)實現(xiàn)要素:針對上述缺陷和不足,本發(fā)明的目的在于提供一種通過調(diào)整軸承標高控制聯(lián)合循環(huán)機組振動的優(yōu)化方法。本發(fā)明首先采用三維有限元模型對軸系進行建模,然后根據(jù)攝動原理將油膜力線性化,采用差分模型計算軸承的剛度和阻尼;其次采用模態(tài)綜合法對建立軸系的等效縮減模型;最后進行不同軸承標高下的軸系動力特性計算,獲得軸承標高對軸系動力特性的影響,為控制燃氣-蒸汽聯(lián)合循環(huán)供熱機組的振動提供解決方案。為了實現(xiàn)上述目的,本發(fā)明采用如下技術(shù)方案:一種通過調(diào)整軸承標高控制聯(lián)合循環(huán)機組振動的優(yōu)化方法,包括以下步驟:1)以sss離合器為界將軸系分為兩部分并進行編號,靠近發(fā)電機的部分為第一子結(jié)構(gòu),遠離發(fā)電機的部分為第二子結(jié)構(gòu);2)依次抬高每個軸承,獲得軸承標高變化前后的軸承載荷,計算標高變化后的軸承的剛度矩陣k和阻尼矩陣c;3)分別建立第一子結(jié)構(gòu)和第二子結(jié)構(gòu)的三維有限元模型,分別獲得其質(zhì)量矩陣、阻尼矩陣和剛度矩陣,記為m1,m2,c1,c2,k1,k2;4)采用模態(tài)綜合法對第一子結(jié)構(gòu)和第二子結(jié)構(gòu)進行縮減,獲得縮減后的質(zhì)量矩陣、阻尼矩陣和剛度矩陣,記為5)對縮減后的第一子結(jié)構(gòu)和第二子結(jié)構(gòu)進行綜合,建立軸系等效縮減模型,綜合后的質(zhì)量矩陣、阻尼矩陣和剛度矩陣,記為6)針對縮減系統(tǒng)進行多轉(zhuǎn)速下振動響應求解,獲得穩(wěn)態(tài)響應;7)以軸承標高配置方案為設計變量,建立約束條件,然后基于步驟5)和步驟6)所求的振動響應建立目標函數(shù);8)使用優(yōu)化算法,對步驟7)中的目標函數(shù)進行優(yōu)化,不斷迭代得到最優(yōu)解,即求出使得步驟6)中所求振動響應最小的軸承標高配置方案。本發(fā)明進一步的改進在于,所述步驟2)中,計算軸承標高變化后的軸承參數(shù),具體過程如下:定義具有n個軸承的軸系的標高配置方案為[δ1,δ2,…,δn],不失一般性,以第一軸承的標高變化來說明軸承參數(shù)的求解過程:其中,δx1和δy1分別為x方向和y方向的位移擾動;x′1和y′1分別為x方向和y方向的速度擾動;δf1,dij為位移擾動引起的第一軸承油膜力的變化;δf1,vij為速度擾動引起的第一軸承油膜力的變化;k1,ij為軸承剛度;c1,ij為軸承阻尼;i、j表示x、y中的某一個;將以上八個系數(shù)用矩陣形式表達為:本發(fā)明進一步的改進在于,所述步驟3)中,建立聯(lián)合循環(huán)機組軸系的有限元模型,獲得其系統(tǒng)矩陣,具體過程如下:在忽略阻尼的情況下,第一子結(jié)構(gòu)的運動學方程為:式中,m1為質(zhì)量矩陣,ω為轉(zhuǎn)速,c1,cor為單位轉(zhuǎn)速陀螺矩陣,k1,s為剛度矩陣,m1,d為單位轉(zhuǎn)速旋轉(zhuǎn)軟化矩陣,f1為載荷向量;為簡化表達,將上式記為在分析前計算零轉(zhuǎn)速和最高轉(zhuǎn)速下的剛度矩陣和阻尼矩陣,記為k1,0,k1,max,c1,0,c1,max,根據(jù)式1)中的比例關系,得到任意轉(zhuǎn)速ω下的剛度矩陣和阻尼矩陣:k1,ω=k1,0+(k1,max-k1,0)·(ω/ωmax)2(5)c1,ω=c1,0+(c1,max-c1,0)·ω/ωmax(6)將以上過程應用到第二子結(jié)構(gòu)的分析中能夠得到同樣的結(jié)果。本發(fā)明進一步的改進在于,所述步驟3)中,在系統(tǒng)矩陣中添加軸承系數(shù)矩陣,具體過程如下:利用各個軸承中心點的自由度信息,在系統(tǒng)矩陣中找到對應的位置,將2維的軸承系數(shù)矩陣拓展成與系統(tǒng)矩陣維度相同的矩陣:將和添加到系統(tǒng)方程中去:本發(fā)明進一步的改進在于,所述步驟4)中,采用固定界面模態(tài)綜合法對軸系進行自由度縮減,該方法對應的自由度變換方程為:式中,xi和xj分別對應系統(tǒng)內(nèi)部和界面自由度,pk和pj分別為保留的前k階模態(tài)所對應的模態(tài)坐標和界面自由度,φk和φc分別為保留的正則模態(tài)集和約束模態(tài),φfix為自由度變換矩陣;利用φfix可對第一子結(jié)構(gòu)和第二子結(jié)構(gòu)進行模態(tài)縮減,縮減后的運動方程為:其中經(jīng)過以上縮減過程,將自由度為(i+j)的問題縮減為了(k+j),對于軸系這種大型結(jié)構(gòu),k<<j,自由度得到了縮減。本發(fā)明進一步的改進在于,所述步驟5)中,對第一子結(jié)構(gòu)和第二子結(jié)構(gòu)進行綜合,具體過程如下:對界面自由度xj進行進一步區(qū)分其中xsss對應sss離合器連接處的界面自由度,xb對應轉(zhuǎn)子軸承中心點處的界面自由度;sss離合器連接處的界面自由度采用間接對接的模態(tài)綜合法來對接,連接子結(jié)構(gòu)采用matrix27單元,其中matrix27單元的系數(shù)通過等效剛度法來確定;轉(zhuǎn)子軸承中心點處的界面自由度是為了添加軸承參數(shù)的需求而保留,綜合后的軸系運動方程為:本發(fā)明進一步的改進在于,所述步驟7)中,確定優(yōu)化的設計變量,建立約束條件,然后基于步驟6)中所求的振動響應為建立目標函數(shù),具體過程如下:設計變量:各軸承標高的配置方案,即δ=[δ1,δ2,…,δn];約束條件:各軸承標高的約束條件一般來自安裝環(huán)境、軸承結(jié)構(gòu)等的限制,可表示為:δc∈(lc,uc),c=1,2,…,n(14)其中,lc和uc分別表示軸承c的標高的上下限;目標函數(shù):優(yōu)化目標是使軸系振動響應峰值最小化,振動響應峰值u由步驟5)和步驟6)求得,因此,目標函數(shù)u表示為設計變量δ的函數(shù):u=f(δ)(15)在滿足約束條件的前提下使得目標函數(shù)值最優(yōu),即完成優(yōu)化模型的求解。本發(fā)明進一步的改進在于,所述步驟8)中采用遺傳算法進行優(yōu)化,具體過程為:801)通過二進制編碼隨機組成初始種群,記當前種群代數(shù)count=1;802)基于步驟2)至步驟6)分別求出種群中每個個體對應的目標函數(shù)值,即為每個個體的適應度值u;803)選擇操作:按照適應大小對個體排序,采用輪盤賭法從種群中以一定概率選擇優(yōu)良個體,以繁殖得到下一代個體;804)交叉操作:從種群中隨機選擇兩個個體,通過編碼交換組合,把優(yōu)秀的特征傳遞到下一代個體;805)變異操作:從種群中隨機選擇一個個體,對個體中的編碼進行變異以產(chǎn)生下一代個體;806)判斷是否結(jié)束優(yōu)化過程:當?shù)螖?shù)count達到最大迭代次數(shù)或最優(yōu)值滿足收斂條件后,停止優(yōu)化過程,獲得最優(yōu)個體,即最優(yōu)的軸承標高配置方案;若不滿足以上條件,則重復進行步驟802)-步驟806)過程,直到滿足結(jié)束條件為止。與現(xiàn)有技術(shù)相比,本發(fā)明具有以下優(yōu)點:本發(fā)明基于三維有限元模型建立了燃氣-蒸汽聯(lián)合循環(huán)供熱機組軸系的振動響應優(yōu)化模型,在計算振動響應時考慮了旋轉(zhuǎn)軟化效應和陀螺效應等因素,更符合實際工況。本發(fā)明建立了計算任意轉(zhuǎn)速下的系統(tǒng)矩陣的快速算法;引入差分模型以獲得軸承標高變化后的軸承參數(shù);對模態(tài)綜合法進行改進以進行自由度縮減;在計算過程中采用matrix27單元以計入sss離合器的影響;采用遺傳算法對優(yōu)化模型進行優(yōu)化。綜合以上方法的優(yōu)點,本發(fā)明能夠大大縮減計算時間,節(jié)省計算機資源,便于工程應用,可得到使得軸系振動響應峰值最小的最優(yōu)軸承標高配置方案。進一步,本發(fā)明結(jié)合差分模型,提供了一種計算軸承標高變化后的軸承參數(shù)的方法,能夠方便快速地計入軸承標高的影響,便于工程應用。進一步,本發(fā)明根據(jù)聯(lián)合循環(huán)機組軸系的剛度矩陣和阻尼矩陣隨轉(zhuǎn)速變化的特點,提供了一種用于快速計算不同轉(zhuǎn)速下的剛度矩陣和阻尼矩陣的方法,可以避免在計算時重復組裝矩陣,提高計算速度。進一步本發(fā)明提供了一種根據(jù)軸承中心點的自由度信息將求得的軸承參數(shù)拓展成與系統(tǒng)矩陣維度相同的軸承矩陣的方法,便于將軸承矩陣添加到系統(tǒng)矩陣中去。進一步,本發(fā)明對固定界面模態(tài)綜合法進行了改進,提供了一種對系統(tǒng)矩陣進行自由度縮減的方法,可以縮減系統(tǒng)矩陣的自由度,縮減計算時間,減小對計算資源的需求。進一步,本發(fā)明提供了一種處理固定界面模態(tài)綜合法的界面自由度的方法,具體來說是,將界面自由度分為兩部分,一部分對應軸承中心點處的界面自由度,一部分對應sss離合器連接處的界面自由度,以完成第一子結(jié)構(gòu)和第二子結(jié)構(gòu)的模態(tài)綜合過程,以用于軸系振動響應的計算。進一步,本發(fā)明提供了建立通過調(diào)整軸承標高控制聯(lián)合循環(huán)機組振動的優(yōu)化模型的方法,確定了設計變量、約束條件和目標函數(shù),可用于聯(lián)合循環(huán)機組的振動控制的優(yōu)化。進一步,本發(fā)明提供了通過遺傳算法對優(yōu)化模型進行優(yōu)化的方法,以快速有效地獲得使軸系振動響應峰值達到最小的最優(yōu)軸承標高配置方案。附圖說明圖1為本發(fā)明一種通過調(diào)整軸承標高控制聯(lián)合循環(huán)機組振動的優(yōu)化方法的總體流程圖;圖2為聯(lián)合循環(huán)機組的三維模型圖;圖3為子結(jié)構(gòu)劃分示意圖;圖4為軸承的八參數(shù)模型;圖5為遺傳算法的流程圖。具體實施方式下面將結(jié)合附圖和實施例詳細說明本方法的實施方式。請參閱圖1所示,本發(fā)明為一種通過調(diào)整軸承標高控制聯(lián)合循環(huán)機組振動的優(yōu)化方法,包括以下7個步驟:1)本發(fā)明實施例采用如圖2所示的燃氣-蒸汽聯(lián)合循環(huán)供熱機組軸系,該模型具有8個軸承,模型的密度為7810kg/m3,彈性模量為200gpa,泊松比為0.3。以sss離合器為界將軸系分為第一子結(jié)構(gòu)和第二子結(jié)構(gòu),將各子結(jié)構(gòu)的自由度分為3類:xi表示內(nèi)部自由度,xsss表示sss離合器連接處自由度,xbrg表示軸承處自由度。2)、依次抬高每個軸承,計算8個軸承標高變化后的軸承參數(shù)。以第一軸承的標高變化為例來說明軸承參數(shù)的求解過程。其中,δx1和δy1分別為x方向和y方向的位移擾動;x′1和y′1分別為x方向和y方向的速度擾動;δf1,dij為位移擾動引起的第一軸承油膜力的變化;δf1,vij為速度擾動引起的第一軸承油膜力的變化,k1,ij為軸承剛度;c1,ij為軸承阻尼;i、j表示x、y中的某一個。如圖3所示,采用八系數(shù)軸承單元模擬軸承,將以上八個系數(shù)用矩陣形式表達為:2)、根據(jù)剛度矩陣和阻尼矩陣的快速算法計算任意轉(zhuǎn)速下的系統(tǒng)矩陣,分別建立第一子結(jié)構(gòu)和第二子結(jié)構(gòu)的三維有限元模型,任意轉(zhuǎn)速下的剛度矩陣和阻尼矩陣快速算法為:k1,ω=k1,0+(k1,max-k1,0)·(ω/ωmax)2(5)c1,ω=c1,0+(c1,max-c1,0)·ω/ωmax(6)式中,k1,0,k1,ω,k1,max,c1,0,c1,ω,c1,max,分別為零轉(zhuǎn)速,任意轉(zhuǎn)速和最高轉(zhuǎn)速下的剛度矩陣和阻尼矩陣。將以上過程應用到第二子結(jié)構(gòu)的分析中能夠得到同樣的結(jié)果。因此,只需進行兩次系統(tǒng)矩陣的組裝便可獲得任意轉(zhuǎn)速ω下的系統(tǒng)矩陣,避免了重復組裝系統(tǒng)矩陣的問題,節(jié)省計算時間。建立子結(jié)構(gòu)的運動學方程為:同時在系統(tǒng)方程中添加軸承系數(shù):利用各個軸承中心點的自由度信息,在系統(tǒng)矩陣中找到對應的位置,將2維矩陣拓展成與系統(tǒng)矩陣維度相同的矩陣:添加軸承系數(shù)矩陣后的系統(tǒng)運動學方程為:4)、采用固定界面模態(tài)綜合法對子結(jié)構(gòu)進行縮減,該方法選用的自由度變換方程為:式中,和分別對應系統(tǒng)內(nèi)部、sss離合器連接處界面自由度和軸承處界面自由度;和分別為保留的正則模態(tài)自由度、sss離合器處自由度和軸承處自由度;和分別為保留的正則模態(tài)集、對應于sss離合器連接處界面自由度的約束模態(tài)和對應于軸承處界面自由度的約束模態(tài);φfix為自由度變換矩陣??s減后的子結(jié)構(gòu)運動學方程為:5)對縮減后的子結(jié)構(gòu)進行綜合。sss離合器連接處的界面自由度采用間接對接的模態(tài)綜合法來對接,連接子結(jié)構(gòu)采用matrix27單元,其中matrix27單元的系數(shù)通過等效剛度法來確定。綜合后的軸系運動學方程為:對實施例進行縮減后,系統(tǒng)矩陣的自由度1176531由變?yōu)?28,大大降低了系統(tǒng)的自由度,降低了對計算資源的需求。6)、針對縮減系統(tǒng)進行多轉(zhuǎn)速下振動響應求解,獲得穩(wěn)態(tài)響應。7)、確定優(yōu)化的設計變量,建立約束條件,然后建立起目標函數(shù)。設計變量:由圖1可知,軸系包含8個軸承,故設計變量為δ=[δ1,δ2,…,δ8]。約束條件:考慮安裝環(huán)境,軸承結(jié)構(gòu)等的限制,可表示為:表1約束條件(μm)目標函數(shù):優(yōu)化目標是使軸系振動響應峰值最小化,振動響應峰值u由步驟5)和步驟6)求得,因此,目標函數(shù)u表示為設計變量δ的函數(shù):u=f(δ)(15)8)、使用采用遺傳算法進行優(yōu)化,對步驟7)中的目標函數(shù)進行優(yōu)化,實施方法如圖4所示。本節(jié)設定優(yōu)化過程中總的優(yōu)化代數(shù)為100,種群大小為20,目標函數(shù)殘差為1×10-4。801)通過二進制編碼隨機組成個體數(shù)為100的初始種群,記當前種群代數(shù)count=1;802)基于步驟5)和步驟6)分別求出種群中每個個體對應的目標函數(shù)值,即為每個個體的適應度值u;803)選擇操作:按照適應大小對個體排序,采用輪盤賭法從種群中以一定概率選擇優(yōu)良個體,以繁殖得到下一代個體;804)交叉操作:從種群中隨機選擇兩個個體,通過編碼交換組合,把優(yōu)秀的特征傳遞到下一代個體;805)變異操作:從種群中隨機選擇一個個體,對個體中的編碼進行變異以產(chǎn)生下一代個體;806)判斷是否結(jié)束優(yōu)化過程:當?shù)螖?shù)count滿足迭代次數(shù)大于100,或目標函數(shù)殘差小于1×10-4中任一條件時,停止優(yōu)化過程,獲得最優(yōu)個體,即最優(yōu)的軸承標高配置方案;若不滿足以上條件,則重復進行步驟802)-步驟806)過程,直到滿足結(jié)束條件為止。采用以上優(yōu)化對實例中的聯(lián)合循環(huán)機組進行優(yōu)化后,表1和表2分別為優(yōu)化前后的標高和優(yōu)化前后響應幅值的變化。表1為優(yōu)化前后的標高組合(mm)第一軸承第二軸承第三軸承第四軸承第五軸承第六軸承第七軸承第八軸承優(yōu)化前19.244.522.630.27002.954.8優(yōu)化后19.244.522.630.270.050.12.9554.8表2位優(yōu)化前后的響應(幅值μm/角度°)軸承4x軸承4y軸承5x軸承5y軸承6x軸承6y軸承7x軸承7y優(yōu)化前30.6/30618.7/6636.5/9517/19163.7/11248.4/21084.1/24160.3/54優(yōu)化后28.9/32927.2/8441.6/6228.9/16444.2/7343.3/19856.1/23039.9/338從表中可以看出,優(yōu)化前后,最大響應幅值降低了33.3%,說明本發(fā)明所提供的優(yōu)化方法在實踐中是可行的。當前第1頁12