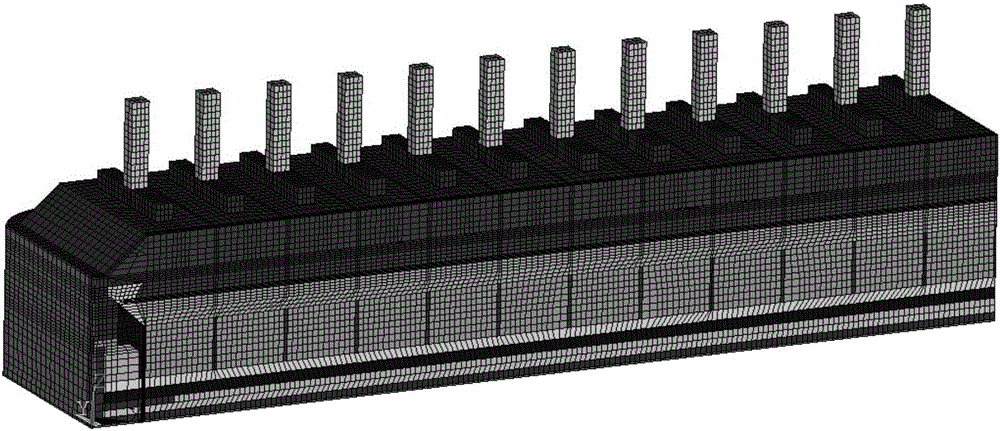
本發(fā)明涉及一種基于熱-流耦合的鋁電解槽三維爐幫的評估方法;屬于鋁電解槽設(shè)計
技術(shù)領(lǐng)域:
。
背景技術(shù):
:鋁電解槽內(nèi),高溫熔融電解質(zhì)在側(cè)部發(fā)生凝固,稱為爐幫。鋁電解槽的爐幫位于槽膛內(nèi)壁上,可保護側(cè)部炭塊免受電解質(zhì)和鋁液等高溫熔體的侵蝕,同時,適當(dāng)?shù)臓t幫厚度能夠保持電解過程的熱平衡和物料平衡,通過爐幫的溶解與生成,降低鋁電解生產(chǎn)的溫度波動和濃度波動。當(dāng)槽溫升高時,爐幫減薄增強散熱,阻止槽溫的升高;當(dāng)槽溫降低時,爐幫增厚,阻止熱量散失。良好的鋁電解槽保溫結(jié)構(gòu)設(shè)計是形成理想爐幫形狀的前提條件。頂部、側(cè)部和底部的保溫情況決定了鋁電解槽的溫度分布以及爐幫厚度和伸腿長度。因此,研究爐幫形狀受這些參數(shù)的影響程度,對于鋁電解槽的結(jié)構(gòu)設(shè)計以及處理生產(chǎn)過程中出現(xiàn)的各種問題,具有重要的指導(dǎo)作用。而不斷優(yōu)化的鋁電解槽爐幫形狀計算方法,對于這些研究具有非常重要的意義。對鋁電解槽爐幫形狀的計算,工業(yè)界和學(xué)術(shù)界提出了多種計算方法,主要是基于熱場計算的一維、二維和偽三維模型。然而,現(xiàn)有對于爐幫形狀的計算方法,均沒有反映出熔體流動對爐幫形成的影響,計算中也僅僅是賦予熔體一個較高的均一等效導(dǎo)熱系數(shù),由傳遞原理可知,流速大的區(qū)域傳熱也較快,上述均一簡化與實際情況有較大的偏差。這就導(dǎo)致了根據(jù)上述計算結(jié)果所做出的評估是存在一定的偏差的。除此之外,鋁電解槽在大型化的方向迅猛發(fā)展,目前400kA及以上的槽型已占全部電解槽的一半以上,因此現(xiàn)有爐幫計算以及由該類計算方法所得的評估已經(jīng)不能滿足現(xiàn)代大型電解槽的設(shè)計、生產(chǎn)需求。技術(shù)實現(xiàn)要素:本發(fā)明針對現(xiàn)有技術(shù)的不足,提供一種基于熱-流耦合的鋁電解槽三維爐幫的評估方法。本發(fā)明一種基于熱-流耦合的鋁電解槽三維爐幫的評估方法:包括下述步驟:步驟(1):獲得鋁電解槽的結(jié)構(gòu)參數(shù)及鋁電解槽運行工藝條件所述鋁電解槽結(jié)構(gòu)參數(shù)包括槽體各部分的尺寸和槽體各部分的材料屬性參數(shù),其中,槽體各部分的尺寸是指陽極、陰極、爐膛以及內(nèi)襯材料的長度、寬度以及高度或厚度;槽體各部分的材料屬性參數(shù)是指槽體各部分的導(dǎo)熱率、導(dǎo)電率、磁導(dǎo)率、密度和比熱容,以及熔體的粘度和熔化潛熱;上述參數(shù)均為固有屬性參數(shù);所述鋁電解槽運行工藝條件包括極距、電解質(zhì)水平、鋁水平及槽系列電流值;步驟(2):建立鋁電解槽電熱場模型和電磁場模型依據(jù)步驟(1)獲得的數(shù)據(jù),并使用假設(shè)的初始爐幫形狀,根據(jù)有限元理論及方法建立鋁電解槽電熱場模型和電磁場模型;步驟(3):提取電熱場模型中槽膛區(qū)域的焦耳生熱率分布、提取電磁場模型中槽膛區(qū)域的電磁力密度分布設(shè)定步驟(2)得到的電熱場模型和電磁場模型的邊界條件,并求解電熱場模型和電磁場模型,根據(jù)運算結(jié)果提取電熱場模型中槽膛區(qū)域的焦耳生熱率分布、提取電磁場模型中槽膛區(qū)域的電磁力密度分布;步驟(4):求解爐幫形狀的理論分布建立起鋁電解槽凝固傳熱仿真計算數(shù)學(xué)模型與鋁電解槽流動耦合仿真計算數(shù)學(xué)模型,并導(dǎo)入步驟(3)得到的焦耳生熱率分布作為熱源St,導(dǎo)入電磁力密度分布作為動量源項Sv,利用有限體積法求解數(shù)學(xué)模型得到爐幫形狀的理論分布;步驟(5):校準(zhǔn)和驗證數(shù)學(xué)模型以已有的鋁電解槽為對象,通過步驟1-4求解所得的爐幫形狀的理論分布計算得到該已有的鋁電解槽n個位置的爐幫形狀;然后測量該已有的鋁電解槽n個位置的實際爐幫形狀;根據(jù)實際爐幫形狀校準(zhǔn)邊界條件;得到校準(zhǔn)后的邊界條件;步驟(6):電解槽的運行效果的評估利用步驟(5)所得校準(zhǔn)后的邊界條件以及步驟四所得鋁電解槽凝固傳熱仿真計算數(shù)學(xué)模型與鋁電解槽流動耦合仿真計算數(shù)學(xué)模型;設(shè)定不同的槽結(jié)構(gòu)設(shè)計參數(shù)與運行參數(shù),根據(jù)設(shè)定的槽結(jié)構(gòu)設(shè)計參數(shù)以及運行參數(shù)計算出該條件下爐幫形狀;并根據(jù)爐幫的厚度對不同條件下電解槽的運行效果作出評估。在實際應(yīng)用過程中,所述鋁電解槽結(jié)構(gòu)參數(shù)包括槽體各部分的尺寸和槽體各部分的材料屬性參數(shù),其中,槽體各部分的尺寸是指陽極、陰極、爐膛以及內(nèi)襯材料的長度、寬度以及高度或厚度;槽體各部分的材料屬性參數(shù)是指槽體各部分的導(dǎo)熱率、密度和比熱容,以及熔體的粘度和熔化潛熱;上述參數(shù)均為固有屬性參數(shù);所述鋁電解槽運行工藝條件包括極距、電解質(zhì)水平、鋁水平及槽系列電流值。在本發(fā)明所述電解質(zhì)水平是指熔融電解質(zhì)層的高度、所述鋁水平是指熔融鋁液層的高度、所述槽系列電流值是指加載在電解槽。本發(fā)明一種基于熱-流耦合的鋁電解槽三維爐幫的評估方法;步驟(2)中所述假設(shè)的初始爐幫形狀優(yōu)選為崔喜風(fēng),鄒忠,張紅亮,等人在《預(yù)焙鋁電解槽三維槽幫形狀的模擬計算》中所提供的爐幫形狀。本發(fā)明一種基于熱-流耦合的鋁電解槽三維爐幫的評估方法;步驟(2)中根據(jù)有限元理論及方法建立的鋁電解槽電熱場模型的表達式如下方程組(3):∂∂x(kx∂T∂x)+∂∂y(ky∂T∂y)+∂∂z(kz∂T∂z)+qS=0qs=σ|▿φ|2---(3)]]>方程組(3)中,kx,ky,kz分別為x、y、z軸方向的導(dǎo)熱系數(shù),ρ為密度,均由步驟(1)收集得到;T為溫度;qs為電流產(chǎn)生的焦耳熱;σ為材料的電導(dǎo)率;φ為電勢。在工業(yè)化應(yīng)用時φ可為實際加載的電邊界條件(如電流的大小等)。本發(fā)明一種基于熱-流耦合的鋁電解槽三維爐幫的評估方法;步驟(2)中根據(jù)有限元理論及方法建立的電磁場模型的表達式為方程組(4):▿·J=0J=-σ▿φ▿×H=JB=μH▿·B=0---(4)]]>方程組(4)中,J為電流密度;σ為材料電導(dǎo)率;μ為材料磁導(dǎo)率;φ為電勢,來源于計算前加載的電邊界條件;H為磁場強度,B是磁感應(yīng)強度,通過求解電磁場模型后可得到。本發(fā)明一種基于熱-流耦合的鋁電解槽三維爐幫的評估方法;步驟(3)中設(shè)定步驟(2)得到的電熱場模型和電磁場模型的邊界條件;所述邊界條件為:電熱場模型中的槽系列電流大小、外界空氣溫度、與外界空氣的對流換熱系數(shù),電磁場模型中的槽系列電流大小。作為優(yōu)選,為了減少計算量,步驟(3)中設(shè)定步驟(2)得到的電熱場模型和電磁場模型的邊界條件;所述邊界條件為:電熱場模型中的槽系列電流大小、外界空氣溫度、與外界空氣的對流換熱系數(shù),電磁場模型中的槽系列電流大小。當(dāng)選定電解槽后,其電流一般也就確定了下來。并且槽殼與空氣的對流換熱系數(shù)取決于槽殼幾何結(jié)構(gòu)、槽殼材料光滑度、廠房內(nèi)部通風(fēng),對于確定的槽結(jié)構(gòu),該系數(shù)一般為確定的函數(shù)關(guān)系式。那么此時只需考慮外界空氣溫度。在求解模型時,可采用賦值的方式確定邊界條件,所謂賦值一般是賦予工業(yè)應(yīng)用時,電解槽所在空間的平均溫度。一般為40℃。作為優(yōu)選,本發(fā)明一種基于熱-流耦合的鋁電解槽三維爐幫的評估方法:步驟(3)中,設(shè)定步驟(2)得到的電熱場模型和電磁場模型的邊界條件,并采用伽遼金法求解電熱場模型、采用全標(biāo)量法求解電磁場模型。本發(fā)明一種基于熱-流耦合的鋁電解槽三維爐幫的評估方法:步驟(4)中所述的鋁電解槽凝固傳熱仿真數(shù)學(xué)模型為方程組(1):∂∂t(ρH)+▿·(ρv→H)=▿·(keff▿T)+StH=h+ΔHh=href+∫TrefTcpdTΔH=βLkeff=k0+kt---(1)]]>方程組(1)中,ρ為熔體密度;H為總焓;t為時間;為熔體流速,通過計算流場控制方程得到;keff為有效導(dǎo)熱系數(shù),由各種材料的導(dǎo)熱系數(shù)k0和湍流導(dǎo)熱系數(shù)kt相加得到,其中湍流導(dǎo)熱系數(shù)kt為標(biāo)準(zhǔn)k-ε模型計算所得;T為溫度;St為熱源;h為顯焓;Tref為參考溫度;href為參考溫度下的參考焓,可由熱力學(xué)手冊查到;ΔH為潛熱;Cp為熔體的比熱容;β為熔體的液相分數(shù);L為熔體的熔化潛熱。本發(fā)明一種基于熱-流耦合的鋁電解槽三維爐幫的評估方法:步驟(4)中鋁電解槽流動耦合仿真計算數(shù)學(xué)模型為流場控制方程;所述流場控制方程為方程組(2):∂ρ∂t+▿·(ρv→)=0∂∂t(ρv→)+v→·▿v→=μeff·▿2v→+SS=Sv-(1-β)2(β3+ϵ)Amush·v→μeff=μ0+μt---(2)]]>方程組(2)中,ρ為熔體密度;為熔體流速,通過方程組(2)可求得;μeff為熔體的有效粘度,由熔體粘度μ0和湍流粘度μt相加得到,其中湍流粘度μt為標(biāo)準(zhǔn)k-ε模型計算所得;S為源項;Sv為動量源項;β為熔體的液相分數(shù);ε為小于0.0001的常數(shù);Amush為糊狀區(qū)常數(shù),取104~107。本發(fā)明一種基于熱-流耦合的鋁電解槽三維爐幫的評估方法:液相分數(shù)β的計算方法為:式中,Tsolidus為熔體的固相點溫度,Tliquidus為熔體的液相點溫度。本發(fā)明一種基于熱-流耦合的鋁電解槽三維爐幫的評估方法:步驟(5)中所述n大于等于10,優(yōu)選為10-100。有益效果:本發(fā)明方法與現(xiàn)行的爐幫形狀計算方法相比具備如下優(yōu)點:(1)本發(fā)明利用熱場-流場耦合的方法計算鋁電解槽爐幫形狀,可充分考慮各區(qū)域熔體流動對爐幫凝固的影響,相比現(xiàn)有方法僅僅直接用測試溫度來判斷爐幫形狀,使用本方法校準(zhǔn)后計算出來的爐幫形狀更加貼近實際生產(chǎn)情況。(2)在熱-流耦合計算中,預(yù)先使用電熱場和電磁場模型計算得到焦耳生熱率和電磁力分布,并導(dǎo)入成能量源項與動量源項,可以大幅提高凝固模型計算的速度。(3)利用實際測試數(shù)據(jù)對建立的熱流耦合凝固模型進行校準(zhǔn)和驗證,可提高理論計算結(jié)果與實際爐幫形狀的相符度,增強后續(xù)計算的可信度。附圖說明圖1本發(fā)明方法的流程圖;圖2為應(yīng)用本發(fā)明方法建立的鋁電解槽電熱場模型的示意圖;圖3為應(yīng)用本發(fā)明方法建立的鋁電解槽電磁場模型的示意圖;圖4為實施例1電熱場模型計算得到的槽膛區(qū)域焦耳生熱率分布/J·m-3;圖5為實施例1電磁場模型計算得到的槽膛區(qū)域電磁力密度分布/N·m-3;圖6為應(yīng)用本發(fā)明方法計算得到的420kA鋁電解槽爐幫形狀;圖7為應(yīng)用本發(fā)明方法計算得到的420kA鋁電解槽流場分布圖;圖8為應(yīng)用本發(fā)明方法計算得到的420kA鋁電解槽爐幫形狀局部放大圖;圖9為應(yīng)用本發(fā)明方法計算得到的420kA鋁電解槽局部爐幫形狀與流速分布對比圖。從圖1中可以看出本發(fā)明方法整體的步驟流程圖。從圖2中可以看出應(yīng)用本發(fā)明方法建立的鋁電解槽電熱場模型的結(jié)構(gòu)包括了導(dǎo)電部分和周圍的各內(nèi)襯保溫結(jié)構(gòu)。從圖3中可以看出應(yīng)用本發(fā)明方法建立的鋁電解槽電磁場模型的結(jié)構(gòu)包括了槽內(nèi)導(dǎo)電部分和連接槽與槽之間的母線結(jié)構(gòu)。從圖4中可以看出槽膛區(qū)域焦耳生熱率分布主要是集中在陽極投影的下方,即陽極下方熔體的發(fā)熱量是最高的。從圖5中可以看出槽膛區(qū)域電磁力密度的分布不均勻,這導(dǎo)致了熔體以多個旋渦的形式在槽內(nèi)流動。從圖6中可以看出所得到的爐幫形狀較為理想,角部爐幫較厚,可以保護槽內(nèi)襯不受高溫熔體的侵蝕,同時伸腿部分長度合適,沒有生長到陽極投影區(qū)域下。從圖7中可以看出熔體流場主要是呈兩個大漩渦形態(tài),熔體在角部流速較小,傳熱作用較弱,使得角部爐幫變厚,這與圖6的爐幫形狀分布相吻合。從圖8中可以看出計算爐幫形狀并不是非常平滑,由于受到熔體流動的影響,某些部位的爐幫厚度出現(xiàn)了明顯的凹凸差異。從圖9中可以看出在流動形態(tài)變化較大的地方,熔體流動對凝固界面形狀產(chǎn)生了明顯影響。尤其在陽極底掌高度以上的區(qū)域,由于受到陽極側(cè)面的阻擋,電解質(zhì)在平行于間縫方向的速度分量得到增強,與之正對著的爐幫受到?jīng)_刷形成明顯的凹槽。具體實施方式下面結(jié)合附圖對本發(fā)明作進一步說明,但本發(fā)明的保護范圍不受實施例所限。實施例1一種基于熱-流耦合的鋁電解槽三維爐幫計算方法,基于鋁電解槽的結(jié)構(gòu)及運行工藝條件,采用有限元計算理論及方法建立鋁電解槽熱-流場模型,計算得到鋁電解槽的爐幫形狀,進而對模型進行校準(zhǔn)驗證。具體步驟如下:步驟(1):獲得鋁電解槽的結(jié)構(gòu)參數(shù)及運行工藝條件;所述鋁電解槽結(jié)構(gòu)參數(shù)包括槽體各部分的尺寸和槽體各部分的材料屬性參數(shù),其中,槽體各部分的尺寸是指陽極、陰極、爐膛和各種內(nèi)襯材料的長度、寬度以及高度或厚度;槽體各部分的材料屬性參數(shù)是指槽體各部分的導(dǎo)熱率、導(dǎo)電率、磁導(dǎo)率、密度和比熱容,以及熔體的粘度和熔化潛熱;上述參數(shù)均為固有屬性參數(shù);所述鋁電解槽運行工藝條件包括極距、電解質(zhì)水平、鋁水平及槽系列電流值。例如,某420kA電解槽的結(jié)構(gòu)參數(shù)、材料屬性、運行參數(shù)如下表:表1某420kA電解槽關(guān)鍵參數(shù)步驟(2):依據(jù)步驟(1)獲得的數(shù)據(jù),并使用假設(shè)的初始爐幫形狀,根據(jù)有限元理論及方法建立鋁電解槽電熱場模型如圖2,和電磁場模型如圖3所示;(初始爐幫形狀參見崔喜風(fēng),鄒忠,張紅亮等所發(fā)表的《預(yù)焙鋁電解槽三維槽幫形狀的模擬計算》中的爐幫形狀)步驟(2)中根據(jù)有限元理論及方法建立的鋁電解槽電熱場模型的表達式如下:穩(wěn)態(tài)熱傳導(dǎo)方程:∂∂x(kx∂T∂x)+∂∂y(ky∂T∂y)+∂∂z(kz∂T∂z)+qS=0qs=σ|▿φ|2]]>kx,ky,kz為導(dǎo)熱系數(shù),ρ為密度,均由步驟(1)收集得到;T為溫度;qs為電流產(chǎn)生的焦耳熱;σ為材料的電導(dǎo)率;φ為電勢,來源于計算前加載的電邊界條件。步驟(2)中根據(jù)有限元理論及方法建立的電磁場模型的表達式如下:▿·J=0J=-σ▿φ▿×H=JB=μH▿·B=0]]>J為電流密度;σ為材料電導(dǎo)率;μ為材料磁導(dǎo)率;φ為電勢,來源于計算前加載的電邊界條件;H為磁場強度,B是磁感應(yīng)強度,通過求解方程后可得到。步驟(3):設(shè)定步驟(2)得到的電熱場模型和電磁場模型的相關(guān)邊界條件、所述邊界條件為:流經(jīng)電解槽的電流大小為420kA,外界空氣溫度為40℃(實際測量平均溫度),與外界空氣的對流換熱系數(shù)隨溫度變化,為α=0.0719T+5.7149,并進行計算,提取電熱場模型中槽膛區(qū)域的焦耳生熱率分布,其中部分位置的生熱率值列于表1,全域生熱率分布如圖4所示,提取電磁場模型中槽膛區(qū)域的電磁力密度分布,其中部分位置的生熱率值列于表2,全域生熱率分布如圖5所示;表1部分位置的生熱率表2部分位置的電磁力密度步驟(4):建立起鋁電解槽凝固傳熱與流動耦合仿真計算數(shù)學(xué)模型。建立鋁電解槽凝固傳熱仿真數(shù)學(xué)模型的具體方法如下:能量控制方程:∂∂t(ρH)+▿·(ρv→H)=▿·(k▿T)+StH=h+ΔHh=href+∫TrefTcpdTΔH=βLkeff=k0+kt]]>式(1)中,ρ為熔體密度,取值為2130kg/m3;H為總焓;t為時間;為熔體流速,通過計算流場控制方程得到;keff為有效導(dǎo)熱系數(shù),由各種材料的導(dǎo)熱系數(shù)k0和湍流導(dǎo)熱系數(shù)kt相加得到,其中湍流導(dǎo)熱系數(shù)kt為標(biāo)準(zhǔn)k-ε模型計算所得;T為溫度;St為熱源;h為顯焓;Tref為參考溫度;href為參考溫度下的參考焓,可由熱力學(xué)手冊查到;ΔH為潛熱;Cp為熔體的比熱容,取值為1660J/(kg·K);β為熔體的液相分數(shù);L為熔體的熔化潛熱,取值1.6×105J·kg-1。鋁電解槽內(nèi)部熔體流場的函數(shù)表達式為:流場控制方程:∂ρ∂t+▿·(ρv→)=0∂∂t(ρv→)+v→·▿v→=μeff·▿2v→+SS=Sv-(1-β)2(β3+ϵ)Amush·v→μeff=μ0+μt]]>式中,ρ為熔體密度,取2130kg/m-3;為熔體流速;μeff為熔體的有效粘度,由熔體粘度μ0和湍流粘度μt相加得到,其中湍流粘度μt為標(biāo)準(zhǔn)k-ε模型計算所得;S為源項;Sv為動量源項;β為熔體的液相分數(shù);ε為小于0.0001的常數(shù);Amush為糊狀區(qū)常數(shù),取106。上式中液相分數(shù)β的計算方法為:式中,Tsolidus為熔體的固相點溫度,取值為940℃,Tliquidus為熔體的液相點溫度,取值為945℃。并導(dǎo)入步驟(3)得到的焦耳生熱率分布作為熱源,導(dǎo)入電磁力密度分布作為動量源項,利用數(shù)學(xué)模型計算得到爐幫形狀分布。步驟(5):校準(zhǔn)和驗證數(shù)學(xué)模型以已有的420kA鋁電解槽為對象,通過步驟求解所得的爐幫形狀的理論分布計算得到該已有的鋁電解槽20個位置的爐幫形狀;然后測量該已有的鋁電解槽20個位置的實際爐幫形狀;根據(jù)實際爐幫形狀校準(zhǔn)邊界條件;得到校準(zhǔn)后的邊界條件;校準(zhǔn)后的邊界條件為:底部槽殼外界空氣溫度為40℃,中部槽殼外界溫度為70℃,頂部槽殼外界溫度為160℃,與外界空氣的對流換熱系數(shù)隨溫度變化,為α=0.0719T+5.7149。步驟(6):利用步驟(5)所得校準(zhǔn)后的邊界條件以及步驟四所得鋁電解槽凝固傳熱仿真計算數(shù)學(xué)模型與鋁電解槽流動耦合仿真計算數(shù)學(xué)模型;設(shè)定不同的槽結(jié)構(gòu)設(shè)計參數(shù)與運行參數(shù),根據(jù)設(shè)定的槽結(jié)構(gòu)設(shè)計參數(shù)以及運行參數(shù)計算出該條件下爐幫形狀;并根據(jù)爐幫的厚度對不同條件下電解槽的運行效果作出評估。對凝固傳熱與流動耦合仿真模型先進行初始的邊界條件賦值求解,計算該參數(shù)條件下的爐幫形狀;進而將計算結(jié)果與實際測量的爐幫形狀數(shù)據(jù)比較,來校準(zhǔn)原先的邊界條件,以得到更合適的校準(zhǔn)后的邊界條件參數(shù);通過校準(zhǔn)后的邊界條件,就可以對電解槽的待評價參數(shù)(如槽結(jié)構(gòu)、運行工藝參數(shù))進行合理的評估,判斷這些待評估參數(shù)應(yīng)用在電解槽上的效果。圖6是本實施例計算420kA鋁電解槽得到的爐幫形狀,圖7是本實施例計算420kA鋁電解槽對應(yīng)的熔體流場分布,圖8和圖9是爐幫形狀的局部放大圖。由圖8-圖9可知,該420kA鋁電解槽在鋁水平220cm,電解質(zhì)水平180cm,極距45cm條件下所生成的爐幫形狀較為理想,可以保護槽內(nèi)襯不受高溫熔體的侵蝕,同時伸腿部分長度合適,沒有生長到陽極投影區(qū)域下。同時,觀察局部的爐幫形狀可以看出熔體流動對爐幫形狀的影響。在流動形態(tài)變化較大的地方,熔體流動對凝固界面形狀產(chǎn)生了明顯影響。尤其在陽極底掌高度以上的區(qū)域,由于受到陽極側(cè)面的阻擋,電解質(zhì)在平行于間縫方向的速度分量得到增強,與之正對著的爐幫受到?jīng)_刷形成明顯的凹槽。當(dāng)前第1頁1 2 3