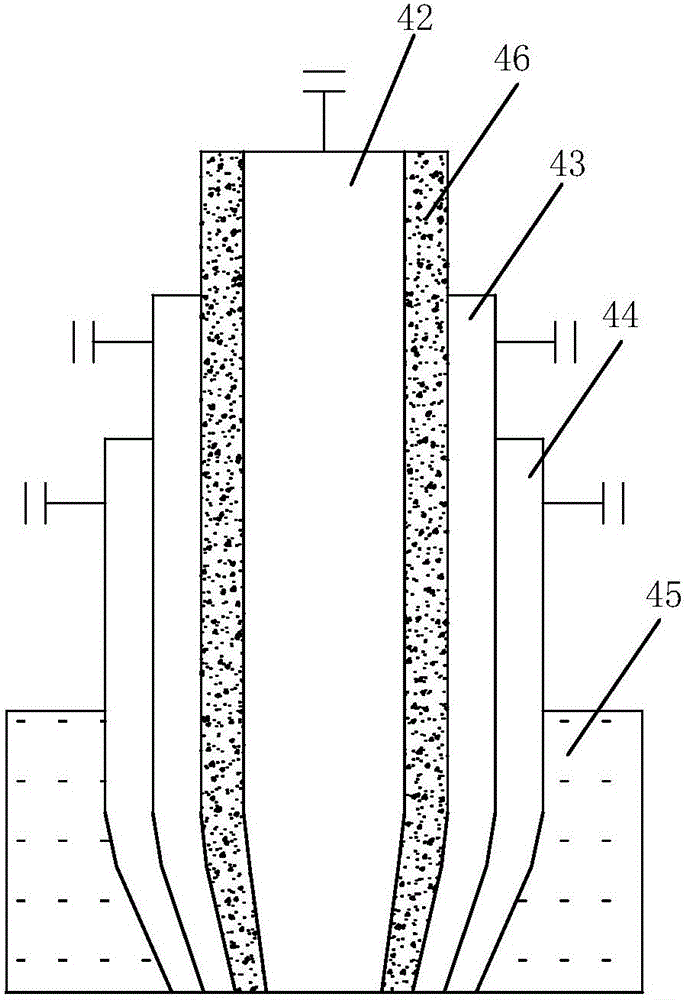
本發(fā)明涉及一種化工設(shè)備及反應(yīng)方法,具體指一種煤加氫反應(yīng)裝置及反應(yīng)方法。
背景技術(shù):
:煤直接加氫工藝過程主要包括煤的破碎與干燥、煤漿制備、加氫液化、固液分離、氣體凈化、液體產(chǎn)品分餾和精制以及制氫等部分。主要流程為:在高溫高壓下,高濃度煤漿中的煤發(fā)生熱解,在催化劑作用下進(jìn)行加氫和分解,最終成為穩(wěn)定的液體分子。液化過程中,將煤、催化劑和循環(huán)油制成的煤漿,與制得的氫氣混合送入反應(yīng)器。在液化反應(yīng)器內(nèi),煤首先發(fā)生熱解反應(yīng),生成自由基“碎片”,不穩(wěn)定的自由基“碎片”再與氫在催化劑存在條件下結(jié)合,形成分子量比煤低得多的初級加氫產(chǎn)物。出反應(yīng)器的產(chǎn)物構(gòu)成十分復(fù)雜,包括氣、液、固三相。氣相的主要成分是氫氣,分離后循環(huán)返回反應(yīng)器重新參加反應(yīng);固相為未反應(yīng)的煤、礦物質(zhì)及催化劑;液相則為輕油(粗汽油)、中油等餾份油及重油。液相餾份油經(jīng)提質(zhì)加工(如加氫精制、加氫裂化和重整等)得到合格的汽油、柴油和航空煤油等產(chǎn)品。重質(zhì)的液固淤漿經(jīng)進(jìn)一步分離得到重油和殘?jiān)赜妥鳛檠h(huán)溶劑用于煤漿制備?,F(xiàn)有的煤直接液化技術(shù)中,反應(yīng)器反應(yīng)壓力高達(dá)17MPa-30Mpa,氫耗量高達(dá)6%-10%,流程復(fù)雜,投資成本高。工藝過程中不僅要補(bǔ)充大量新氫,還需要循環(huán)油作供氫溶劑,裝置生產(chǎn)能力降低,出液化反應(yīng)器的產(chǎn)物組成復(fù)雜,固液兩相分離困難,產(chǎn)油率低。技術(shù)實(shí)現(xiàn)要素:本發(fā)明所要解決的技術(shù)問題是針對現(xiàn)有技術(shù)的現(xiàn)狀提供一種反應(yīng)條件溫和且氫耗量小、產(chǎn)油率高的煤加氫反應(yīng)裝置。本發(fā)明所要解決的另一個(gè)技術(shù)問題是針對現(xiàn)有技術(shù)的現(xiàn)狀提供一種反應(yīng)條件溫和且氫耗量小、產(chǎn)油率高的煤直接加氫反應(yīng)方法。本發(fā)明解決上述技術(shù)問題所采用的技術(shù)方案為:該煤加氫反應(yīng)裝置,其特征在于包括氣化室,所述氣化室的側(cè)壁上設(shè)有用于向所述氣化室內(nèi)加料的氣化噴嘴;所述氣化室的頂部通過管道連接旋風(fēng)反應(yīng)器,所述管道的側(cè)壁上設(shè)有蒸汽噴嘴;所述旋風(fēng)反應(yīng)器的側(cè)壁上設(shè)有用于向所述旋風(fēng)反應(yīng)器內(nèi)加料的粉煤噴嘴,所述旋風(fēng)反應(yīng)器的頂部設(shè)有油氣出口,所述旋風(fēng)反應(yīng)器的底部設(shè)有煤焦出口;所述氣化室的底部出口連接下降管,所述下降管連通冷卻室,所述冷卻室的底部設(shè)有煤渣出口;所述下降管連接激冷裝置,所述激冷裝置連接設(shè)置在殼體側(cè)壁上的激冷水入口。所述氣化噴嘴包括第一本體,第一本體上由內(nèi)而外依次設(shè)有燃料通道、氧氣通道、蒸汽通道和第一冷卻通道;燃料通道與氧氣通道之間的隔層采用耐磨材料制備;所述煤焦出口通過氣相輸送裝置連接所述燃料通道。所述氣相輸送裝置包括依次連接的第一管道、放料罐、第二管道、給料罐和連接所述氣化噴嘴的第三管道;所述第一管道連接所述旋風(fēng)分離器的底部出口;所述第一管道和所述第二管道上分別設(shè)有第一控制閥和第二控制閥;所述放料罐、給料罐和所述第三管道均連接輸送氣源。所述粉煤燒嘴包括第二本體,所述第二本體上設(shè)有粉煤通道,所述粉煤通道外設(shè)有第二冷卻通道。所述旋風(fēng)反應(yīng)器的下部設(shè)有用于儲(chǔ)存煤焦的儲(chǔ)焦室,所述煤焦出口設(shè)置在所述儲(chǔ)焦室的底部。所述的煤加氫反應(yīng)裝置的煤加氫反應(yīng)方法,其特征在于包括下述步驟:燃料、氧氣和水蒸汽自所述氣化噴嘴進(jìn)入所述氣化室,在1000~1700℃、1~9MPa下進(jìn)行反應(yīng),生成以CO+H2為主要組成的高溫高壓合成氣;溫度為1000~1700℃、壓力為1~9MPa的高溫高壓合成氣從所述氣化室的頂部出口進(jìn)入所述管道,與來自所述蒸汽噴嘴的蒸汽反應(yīng),進(jìn)一步增加合成氣中的氫含量;煤粉通過所述粉煤噴嘴進(jìn)入所述旋風(fēng)反應(yīng)器,與來自所述管道的溫度為1000~1700℃、壓力為1~9MPa高溫高壓合成氣在600~1500℃、1~9MPa下進(jìn)行煤加氫反應(yīng),生成油氣和煤焦;油氣從所述油氣出口排出,煤焦儲(chǔ)存在所述煤焦室內(nèi),定期從所述煤焦出口排出,煤焦通過氣相輸送裝置加壓后送入氣化噴嘴4;控制所述進(jìn)入氣化噴嘴的煤焦與進(jìn)入粉煤噴嘴的煤粉質(zhì)量比例為0.4~0.7:1;進(jìn)入所述氣化室的合成氣流速為0.5~1.5m/s;進(jìn)入所述旋風(fēng)分離器內(nèi)的氫氣占干基煤粉的質(zhì)量比為4~10%;控制所述旋風(fēng)分離器內(nèi)氣速為1~3m/s。所述燃料選自甲烷、液化石油氣或生物質(zhì)燃料。與現(xiàn)有技術(shù)相比,本發(fā)明所提供的煤加氫反應(yīng)裝置及反應(yīng)方法能夠在相對溫和的條件下對煤粉進(jìn)行分級利用;將煤中的輕組分直接熱解加氫,無需催化劑和制漿,得到的揮發(fā)份用來制備合成油,煤中的重組分即煤焦進(jìn)行燃燒為裝置提供熱量和氫;本發(fā)明將煤制氫和加氫集成在一起,系統(tǒng)不需要外設(shè)煤制氫裝置,簡化了反應(yīng)流程,煤的利用充分、合理,能耗低,減少環(huán)境污染,工藝流程簡單,煤加氫反應(yīng)是通過氣相反應(yīng)實(shí)現(xiàn)的,反應(yīng)速率快,轉(zhuǎn)化率高,油收率高。附圖說明圖1為本發(fā)明實(shí)施例示意圖;圖2為本發(fā)明實(shí)施例中氣化噴嘴的剖視示意圖;圖3為本發(fā)明實(shí)施例中粉煤噴嘴的剖視示意圖。具體實(shí)施方式以下結(jié)合附圖實(shí)施例對本發(fā)明作進(jìn)一步詳細(xì)描述。如圖1至圖3所示,該一種煤加氫反應(yīng)裝置包括氣化室1,氣化室1的側(cè)壁上設(shè)有用于向氣化室內(nèi)加料的氣化噴嘴4;氣化噴嘴可以是一個(gè),也可以是多個(gè)。氣化室1的頂部通過管道2連接旋風(fēng)反應(yīng)器3,管道2的側(cè)壁上設(shè)有蒸汽噴嘴6;旋風(fēng)反應(yīng)器3的側(cè)壁上設(shè)有用于向旋風(fēng)反應(yīng)器3內(nèi)加料的粉煤噴嘴5,旋風(fēng)反應(yīng)器3的頂部設(shè)有油氣出口31,旋風(fēng)反應(yīng)器3的底部設(shè)有煤焦出口32;氣化室1的底部出口連接下降管7,下降管7連通冷卻室8,冷卻室8的底部設(shè)有煤渣出口81;殼體的側(cè)壁上設(shè)有激冷水入口12激冷水入口連接激冷裝置9,通過激冷裝置9向下降管7的側(cè)壁通激冷水,保護(hù)下降管,同時(shí)控制激冷室內(nèi)溫度(殼體為何表示出兩層:殼體為常規(guī)水冷壁結(jié)構(gòu)。內(nèi)層是指水冷壁,外層是指外殼)。氣化噴嘴4包括第一本體,第一本體上由內(nèi)而外依次設(shè)有燃料通道42、氧氣通道43、蒸汽通道44和第一冷卻通道45;燃料通道42與氧氣通道43之間的隔層46采用耐磨材料制備;所述煤焦出口32通過氣相輸送裝置8連接燃料通道42。氣相輸送裝置8包括按煤焦輸送方向依次連接第一管道81、放料罐84、第二管道82、給料罐85和連接所述氣化噴嘴4的第三管道83;第一管道81連接旋風(fēng)分離器1的底部出口;所述第一管道81和所述第二管道82上分別設(shè)有第一控制閥86和第二控制閥87;放料罐84、給料罐85和第三管道83均連接輸送氣源。粉煤燒嘴5包括第二本體51,所述第二本體51上設(shè)有粉煤通道52,所述粉煤通道52外設(shè)有第二冷卻通道53。所述旋風(fēng)反應(yīng)器3的下部設(shè)有用于儲(chǔ)存煤焦的儲(chǔ)焦室33,所述煤焦出口32設(shè)置在所述儲(chǔ)焦室33的底部。使用上述煤加氫反應(yīng)裝置的煤加氫反應(yīng)方法,包括下述步驟:燃料、氧氣和水蒸汽自所述氣化噴嘴4進(jìn)入所述氣化室1,在1300℃、4MPa下進(jìn)行反應(yīng),生成以CO+H2為主要組成的高溫高壓合成氣;溫度為1300℃、壓力為4MPa的高溫高壓合成氣從氣化室1的頂部出口進(jìn)入所述管道2,與來自蒸汽噴嘴6的蒸汽在1500℃、4MPaG下反應(yīng):CO+H2O=CO2+H2;進(jìn)一步增加合成氣中的氫含量;煤粉通過所述粉煤噴嘴5進(jìn)入所述旋風(fēng)反應(yīng)器3,與來自管道2的溫度為1000~1700℃、壓力為3.8MPa高溫高壓合成氣在1300℃、3.8MPa下進(jìn)行煤加氫反應(yīng),生成油氣和煤焦;油氣從所述油氣出口31排出,煤焦儲(chǔ)存在煤焦室33內(nèi),定期從煤焦出口排出。當(dāng)旋風(fēng)式反應(yīng)器下部的煤焦儲(chǔ)存到焦放料罐容積的85%左右后,將放料罐84泄壓至與旋風(fēng)式反應(yīng)器壓力相同,打開第一閥門86將煤焦排放至放料罐84,放料完畢后關(guān)閉第一閥門86。然后用氮?dú)饣蚨趸枷蚍帕瞎?4內(nèi)充壓至與給料罐85內(nèi)壓力相同;打開第二閥門87,煤焦進(jìn)入給料罐85。給料罐85內(nèi)的煤焦通過惰性輸送氣氣相輸送至氣化燒嘴4,給料罐85內(nèi)壓力比氣化室1內(nèi)的壓力高1.0MPa。放料罐下部、給料罐下部和輸焦管線均連接氣體輸入裝置(圖中未示出)。正常情況下不需要添加燃料,進(jìn)入氣化室的燃料僅僅是煤焦;裝置開車時(shí)可以根據(jù)需要添加其它燃料;燃料選自甲烷、液化石油氣、生物質(zhì)燃料等。進(jìn)入氣化噴嘴4的煤焦與進(jìn)入粉煤噴嘴5的干基煤粉的質(zhì)量比例為0.6??刂茪饣?合成氣流速為1m/s,溫度為1500℃,壓力4MPa;旋風(fēng)分離器3內(nèi)氣速2m/s,溫度1300℃,壓力3.8MPa。本實(shí)施例和現(xiàn)有技術(shù)的對比如表1所示。表1煤炭直接液化煤炭間接液化煤炭干餾實(shí)施例耗煤量3.5噸/噸油品4噸/噸油品25噸/噸油品3.34噸/噸油品氫氣來源制氫裝置制氫裝置-------不需外加氫氣當(dāng)前第1頁1 2 3