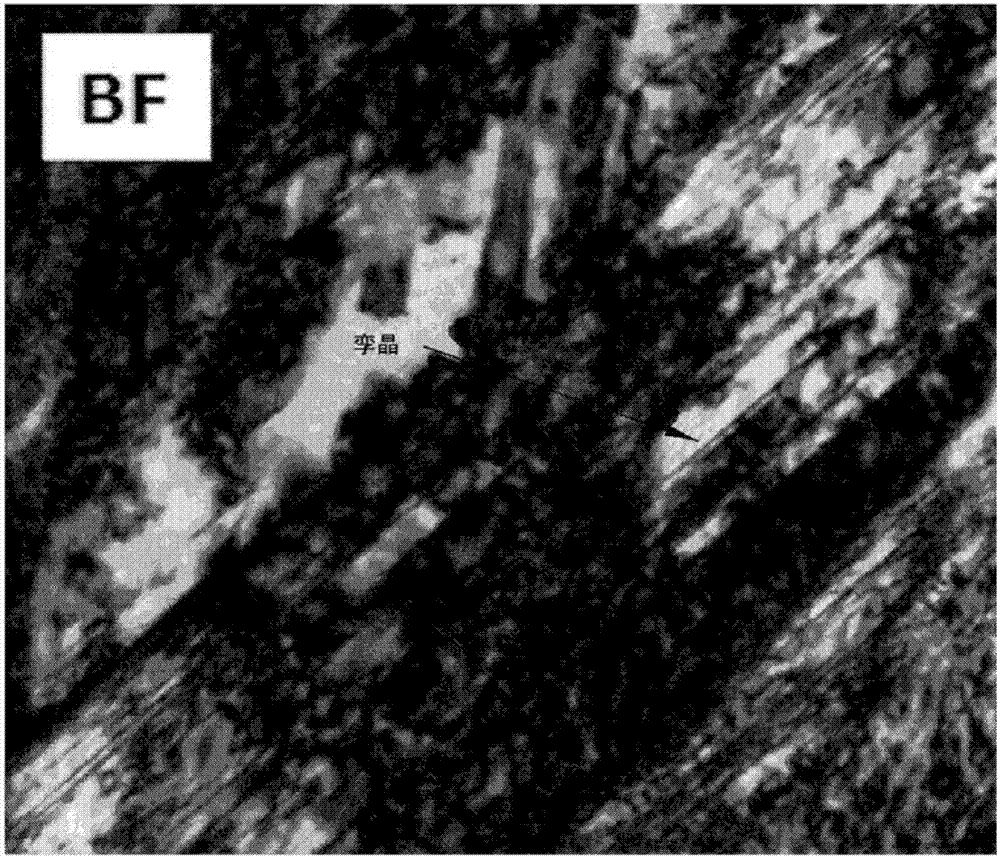
本發(fā)明涉及具有鐵素體-奧氏體組織的經(jīng)濟(jì)型雙相不銹鋼及其制造方法。
背景技術(shù):
:通常,加工性和耐蝕性良好的奧氏體系不銹鋼以鐵(fe)作為基體金屬,主要原料含有鉻(cr)和鎳(ni),并通過添加鉬(mo)和銅(cu)等其它金屬,開發(fā)成滿足各種用途的各種鋼種。耐蝕性及加工性優(yōu)異的300系列不銹鋼含有昂貴的ni、mo等原料,作為替代方案,也對(duì)使用200系列及400系列不銹鋼進(jìn)行了討論,但200系列及400系列不銹鋼具有以下缺點(diǎn),即,它們各自的成型性及耐蝕性達(dá)不到300系列不銹鋼。另外,混合奧氏體相和鐵素體相的雙相不銹鋼具有奧氏體系和鐵素體系所具有的所有優(yōu)點(diǎn),至今為止,開發(fā)出了多種類的雙相不銹鋼。此外,最近為了彌補(bǔ)價(jià)格競(jìng)爭(zhēng)力方面的缺陷,對(duì)排除雙相不銹鋼中所含有的ni及mo等高價(jià)合金元素并添加低價(jià)的合金元素的在費(fèi)用上更加突顯優(yōu)勢(shì)的雙相不銹鋼的關(guān)注越來越大。但是,這種經(jīng)濟(jì)型雙相不銹鋼根據(jù)鐵素體系和奧氏體系相間的強(qiáng)度差異而熱加工性脆弱,從而具有大量產(chǎn)生表面裂紋及邊緣裂紋的缺點(diǎn)。此外,對(duì)成分被調(diào)整為經(jīng)濟(jì)型雙相不銹鋼用的合金元素通過現(xiàn)有的普通連續(xù)鑄造法進(jìn)行加工時(shí),在從液態(tài)凝固為固態(tài)時(shí),根據(jù)氮固溶度的差異,會(huì)在板坯內(nèi)部產(chǎn)生大量的氣孔(porosity)。這種內(nèi)部氣孔在作為后續(xù)工序的再加熱及熱軋過程中,顯然會(huì)成為在產(chǎn)品表面產(chǎn)生大量缺陷的原因,并且導(dǎo)致在熱軋的鋼卷的邊緣產(chǎn)生大量裂紋的缺陷。以上在
背景技術(shù):
中進(jìn)行說明的事項(xiàng)是為了促進(jìn)對(duì)本發(fā)明
背景技術(shù):
的理解,不應(yīng)認(rèn)為是本領(lǐng)域技術(shù)人員已知的現(xiàn)有技術(shù)。技術(shù)實(shí)現(xiàn)要素:要解決的技術(shù)問題本發(fā)明通過調(diào)整合金成分的含量來降低成本的同時(shí),對(duì)其進(jìn)行控制,以滿足雙相不銹鋼中存在的堆垛層錯(cuò)能值,從而提供能夠確保優(yōu)異的延伸率和耐蝕性的經(jīng)濟(jì)型雙相不銹鋼及其制造方法。此外,通過進(jìn)行控制,以滿足形成應(yīng)變誘發(fā)馬氏體相的臨界應(yīng)變(criticalstrainforstraininducedmartensiteformation)值,從而提供能夠確保優(yōu)異的延伸率和耐蝕性的經(jīng)濟(jì)型雙相不銹鋼及其制造方法。此外,提供經(jīng)濟(jì)型雙相不銹鋼及其制造方法,其可以解決鑄造時(shí)從液態(tài)凝固為固態(tài)期間,由于氮固溶度急劇減少而引起的氮?dú)獾拇罅颗懦龅膯栴}。技術(shù)方案根據(jù)本發(fā)明一實(shí)施方式的經(jīng)濟(jì)型雙相不銹鋼為鐵素體-奧氏體系不銹鋼,其為鐵素體-奧氏體系的經(jīng)濟(jì)型雙相不銹鋼,優(yōu)選地,由下述[式2]表示的奧氏體相的堆垛層錯(cuò)能(sfe)值為19~37,形成應(yīng)變誘發(fā)馬氏體相的臨界應(yīng)變值范圍為0.1~0.25,sfe=25.7+1.59×ni/[k(ni)-k(ni)×v(γ)+v(γ)]+0.795×cu/[k(cu)-k(cu)×v(γ)+v(γ)]-0.85×cr/[k(cr)-k(cr)×v(γ)+v(γ)]+0.001×(cr/[k(cr)-k(cr)×v(γ)+v(γ)])2+38.2×(n/[k(n)-k(n)×v(γ)+v(γ)])0.5-2.8×si/[k(si)-k(si)×v(γ)+v(γ)]-1.34×mn/[k(mn)-k(mn)×v(γ)+v(γ)]+0.06×(mn/[k(mn)-k(mn)×v(γ)+v(γ)])2………………[式2],在[式2]中,ni、cu、cr、n、si、mn表示各元素成分的總含量(wt%),k(x)是各元素成分(x)的分配系數(shù),且由下述[式3]表示,v(γ)是奧氏體的相分率(0.45~0.75范圍),k(x)=[鐵素體相中的x元素的含量]/[奧氏體相中的x元素的含量]………………[式3]。此時(shí),所述k(x)中的k(cr)=1.16,k(ni)=0.57,k(mn)=0.73,k(cu)=0.64,根據(jù)n和si的含量(wt%),k(n)和k(si)可以為以下值。n:0.2~0.32%時(shí),k(n)=0.15,n<0.2%時(shí),k(n)=0.25,si≤1.5%時(shí),k(si)=2.76-0.96×si,si>1.5%時(shí),k(si)=1.4。所述不銹鋼的延伸率優(yōu)選為45%以上。所述不銹鋼以重量%計(jì),優(yōu)選包含c:0.08%以下且0%除外、si:0.2~3.0%、mn:2~4%、cr:18~24%、ni:0.2~2.5%、n:0.15~0.32%、cu:0.2~2.5%、余量的fe及其它不可避免的雜質(zhì)。所述不銹鋼以重量%計(jì),可以進(jìn)一步包含w:0.1~1.0%及mo:0.1~1.0%中的至少一種以上。所述不銹鋼以重量%計(jì),可以進(jìn)一步包含ti:0.001~0.1%、nb:0.001~0.05%及v:0.001~0.15%中的至少一種以上。另外外,根據(jù)本發(fā)明一實(shí)施例的經(jīng)濟(jì)型雙相不銹鋼的制造方法為制造鐵素體-奧氏體系經(jīng)濟(jì)型雙相不銹鋼的方法,其可以包括以下步驟:準(zhǔn)備鋼水;將所述鋼水處理成不銹鋼,從而使得由下述[式2]表示的奧氏體相的堆垛層錯(cuò)能(sfe)值為19~37,形成應(yīng)變誘發(fā)馬氏體相的臨界應(yīng)變值范圍為0.1~0.25;sfe=25.7+1.59×ni/[k(ni)-k(ni)×v(γ)+v(γ)]+0.795×cu/[k(cu)-k(cu)×v(γ)+v(γ)]-0.85×cr/[k(cr)-k(cr)×v(γ)+v(γ)]+0.001×(cr/[k(cr)-k(cr)×v(γ)+v(γ)])2+38.2×(n/[k(n)-k(n)×v(γ)+v(γ)])0.5-2.8×si/[k(si)-k(si)×v(γ)+v(γ)]-1.34×mn/[k(mn)-k(mn)×v(γ)+v(γ)]+0.06×(mn/[k(mn)-k(mn)×v(γ)+v(γ)])2………………[式2];在[式2]中,ni、cu、cr、n、si、mn表示各元素成分的總含量(wt%),k(x)是各元素成分(x)的分配系數(shù),且由下述[式3]表示,v(γ)是奧氏體的相分率(0.45~0.75范圍)。k(x)=[鐵素體相中的x元素的含量]/[奧氏體相中的x元素的含量]………………[式3]。尤其,將所述鋼水處理成不銹鋼的過程可以包括以下步驟:使所述鋼水維持在比理論凝固溫度高10~50℃的溫度,并臨時(shí)儲(chǔ)存到中間包中;一次冷卻,將鋼水從中間包注入到鑄膜中,并維持500~1500℃/分鐘的冷卻速度通過鑄膜;二次冷卻,使經(jīng)過一次冷卻而形成凝固殼的鋼水拉拔并通過扇形體。此時(shí),在所述二次冷卻步驟中,優(yōu)選向形成凝固殼的鋼水噴射0.25~0.35l/kg的冷卻水。此外,可以進(jìn)一步包括三次冷卻步驟,所述三次冷卻步驟為,在所述二次冷卻步驟之后被拉拔的鑄坯的表面溫度在1100~1200℃范圍內(nèi),以空氣和冷卻水的比例(空氣/冷卻水)為1.0~1.2的方式,將100~125l/kg·分鐘的冷卻水與空氣進(jìn)行混合并向鑄坯的表面進(jìn)行噴射。另外,將所述鋼水處理成不銹鋼的過程包括使所述鋼水通過一對(duì)鑄輥之間的同時(shí)凝固,從而制造帶鋼的步驟,在制造所述帶鋼的步驟中,鋼水中所包含的超過氮固溶極限的量的氮可以通過所述鑄輥向凝固殼外部排出。此時(shí),優(yōu)選地,在制造所述帶鋼的步驟中,在所述一對(duì)鑄輥中的至少任意一個(gè)鑄輥中使用外周面上沿著圓周方向形成有氣體排出通道的鑄輥。此外,在制造所述帶鋼的步驟中所使用的鑄輥上形成的氣體排出通道以50~500μm的寬度、50~300μm的深度形成多個(gè),并且相鄰的氣體排出通道之間的間隔為100~1000μm,所述鑄輥的表面上形成有15~25μm的凹凸。此外,在準(zhǔn)備所述鋼水的過程中,所述鋼水以重量%計(jì),包含c:0.08%以下且0%除外、si:0.2~3.0%、mn:2~4%、cr:18~24%、ni:0.2~2.5%、n:0.15~0.32%、cu:0.2~2.5%、余量的fe及其它不可避免的雜質(zhì)。另外,在準(zhǔn)備所述鋼水的過程中,所述鋼水以重量%計(jì),可以進(jìn)一步包含w:0.1~1.0%及mo:0.1~1.0%中的至少一種以上。此外,在準(zhǔn)備所述鋼水的過程中,所述鋼水以重量%計(jì),可以進(jìn)一步包含ti:0.001~0.1%、nb:0.001~0.05%及v:0.001~0.15%中的至少一種以上。有益效果根據(jù)本發(fā)明的實(shí)施例,通過調(diào)整高價(jià)元素ni、si及cu合金成分的含量,能夠節(jié)約資源且顯著降低原料費(fèi)用,尤其是通過確保與sts304相比具有同等水平以上的耐蝕性及優(yōu)異的延伸率,能夠充分代替用于成型的200系列、300系列(sts304、316)。并且,連續(xù)鑄造根據(jù)本發(fā)明的實(shí)施例的合金元素時(shí),通過控制鋼水溫度及冷卻速度,能夠抑制鑄坯內(nèi)部產(chǎn)生的針孔(pinhole)。此外,對(duì)根據(jù)本發(fā)明實(shí)施例的合金元素進(jìn)行薄帶連鑄時(shí),通過改善鑄輥,從而使由液態(tài)凝固為固態(tài)時(shí)所產(chǎn)生的氮?dú)饽軌蝽槙车嘏懦?,以能夠防止?nèi)部氣孔的產(chǎn)生及表面缺陷的產(chǎn)生。附圖說明圖1為以根據(jù)本發(fā)明實(shí)施例的發(fā)明鋼和比較鋼的應(yīng)力變形曲線來示出形成應(yīng)變誘發(fā)馬氏體相的臨界應(yīng)變值的圖。圖2a及圖2b作為根據(jù)本發(fā)明實(shí)施例的比較鋼和發(fā)明鋼的代表性透射電子顯微鏡組織的照片,示出是否形成了應(yīng)變誘發(fā)馬氏體相。圖3為示出延伸率和形成應(yīng)變誘發(fā)馬氏體相的臨界應(yīng)變值的關(guān)系的圖表。圖4為概略地示出根據(jù)本發(fā)明一實(shí)施例的經(jīng)濟(jì)型雙相不銹鋼的連鑄方式的制造工序的圖。圖5為概略地示出本發(fā)明一實(shí)施例的經(jīng)濟(jì)型雙相不銹鋼的薄帶連鑄方式制造工序的圖。圖6為概略地示出本發(fā)明一實(shí)施例的經(jīng)濟(jì)型雙相不銹鋼的薄帶連鑄方式制造工序中所需的鑄輥的圖。圖7為比較材料i和發(fā)明材料a的組織照片。圖8為比較材料h的表面缺陷照片。圖9為比較材料f的表面缺陷照片。具體實(shí)施方式下面,參照附圖對(duì)本發(fā)明的實(shí)施例進(jìn)行更詳細(xì)的說明。但是,本發(fā)明并不限定于下述的實(shí)施例,可以以相互不同的多種形態(tài)體現(xiàn),本實(shí)施例僅是為了使本發(fā)明公開完整,且使本領(lǐng)域技術(shù)人員完全知曉本發(fā)明的范圍而提供的。首先,本發(fā)明涉及具有鐵素體-奧氏體系組織的經(jīng)濟(jì)型雙相不銹鋼,本發(fā)明所涉及的鐵素體-奧氏體系組織是指鐵素體相和奧氏體相占據(jù)大部分組織,而不是指不銹鋼僅由鐵素體相和奧氏體相形成。例如,鐵素體相和奧氏體相占據(jù)大部分的組織,是指形成不銹鋼的組織中,鐵素體相和奧氏體相之合為90%以上,除去鐵素體相和奧氏體相的剩余的部分可以為由奧氏體相相變形成的馬氏體相。圖1為以根據(jù)本發(fā)明實(shí)施例的發(fā)明鋼和比較鋼的應(yīng)力變形曲線來示出形成應(yīng)變誘發(fā)馬氏體相的臨界應(yīng)變值的圖。本發(fā)明的對(duì)象可以為經(jīng)濟(jì)型雙相不銹鋼,以重量%(以下在未特別提及時(shí),成分的含量為重量%)計(jì),包含c:0.08%以下且0%除外、si:0.2~3.0%、mn:2~4%、cr:18~24%、ni:0.2~2.5%、n:0.15~0.32%、cu:0.2~2.5%、余量的fe及其它不可避免的雜質(zhì),并且具有由鐵素體相和奧氏體相形成的雙相組織。所述經(jīng)濟(jì)型雙相不銹鋼可以進(jìn)一步包含w:0.1~1.0%、mo:0.1~1.0%、ti:0.001~0.1%、nb:0.001~0.05%、v:0.001~0.15%中的至少一種以上。c作為形成奧氏體相的元素,是通過固溶強(qiáng)化而增強(qiáng)材料強(qiáng)度的有效元素。但是,添加過量的c時(shí),由于在鐵素體-奧氏體相的邊界容易與對(duì)耐蝕性有效的cr等形成碳化物的元素進(jìn)行結(jié)合,降低晶界周圍的cr含量,從而降低耐蝕性,因此,為了極大化耐蝕性,優(yōu)選以大于0且0.08%以下的范圍添加c。si是為了脫氧效果而部分添加的元素,si作為形成鐵素體相的元素,是在退火熱處理時(shí)濃縮在鐵素體相上的元素。因此,為了確保適當(dāng)?shù)蔫F素體相分率,應(yīng)添加0.2%以上的si。但是,超過3.0%的過量添加會(huì)急劇增加鐵素體相的硬度,對(duì)降低雙相鋼的延伸率產(chǎn)生影響,從而使用于充分確保延伸率的奧氏體相難以得到確保。此外,過多的情況下,降低煉鋼時(shí)的熔渣的流動(dòng)性,并與氧結(jié)合而形成夾雜物,從而降低耐蝕性。因此,優(yōu)選將si含量控制為0.2~3.0%。mn是為脫氧劑及增加氮的固溶度的元素,其為形成奧氏體相的元素,可以代替高價(jià)的ni而使用。當(dāng)大量添加mn時(shí),雖然對(duì)氮的固溶度有效果,但是與鋼中的s結(jié)合而形成mns,從而會(huì)使耐蝕性變差。因此,以大于4%的含量添加mn時(shí),難以確保304鋼水平的耐蝕性。此外,當(dāng)mn的含量小于2%時(shí),即使調(diào)整形成奧氏體相的元素ni、cu、n等,也難以確保適當(dāng)?shù)膴W氏體相分率,并且所添加的n的固溶度低,從而在常壓下難以得到氮的充分的固溶。因此,優(yōu)選將mn的含量控制為2~4%。cr為與si一起作為鐵素體相的穩(wěn)定化元素,不僅在確保雙相不銹鋼的鐵素體相方面起到主要作用,而且還是確保耐蝕性的必需元素。增加cr含量雖然會(huì)增加耐蝕性,但是為了維持相分率,需要增加高價(jià)的ni或其它形成奧氏體相的元素的含量。由此,為了在維持雙相不銹鋼的相分率的同時(shí),確保與304鋼同等水平以上的耐蝕性,優(yōu)選將cr的含量控制在18~24%。ni為與mn、cu及n一起是奧氏體相穩(wěn)定化的的元素,對(duì)確保雙相不銹鋼的奧氏體相起到主要作用。為了節(jié)約成本,可以最大限度地減少價(jià)格昂貴的ni含量,且相對(duì)地增加其他作為奧氏體相形成元素的mn和n,從而可以充分維持因ni的減少所帶來的相分率的均衡。但是,為了能夠抑制在冷加工時(shí)形成過多的應(yīng)變誘發(fā)馬氏體相,并且為了確保充分的奧氏體相的穩(wěn)定度,應(yīng)添加0.2%以上的ni。當(dāng)大量添加ni時(shí),會(huì)增加奧氏體相分率,從而難以確保合適的奧氏體相分率,尤其,由于高價(jià)的ni而導(dǎo)致產(chǎn)品的制備費(fèi)用上升,從而相比于304鋼,難以確保競(jìng)爭(zhēng)力。因此,優(yōu)選將ni的含量控制在0.2~2.5%。n在雙相不銹鋼中與ni一起對(duì)奧氏體相的穩(wěn)定化起到很大作用的元素,在退火熱處理時(shí),由于在固相中的擴(kuò)散速度快,從而大部分會(huì)濃縮在奧氏體相上的元素之一。因此,增加n含量會(huì)附帶地誘發(fā)耐蝕性的增加及高強(qiáng)度化。但是n的固溶度會(huì)隨著添加的mn的含量而發(fā)生變化。在本發(fā)明的mn范圍內(nèi),當(dāng)n含量超過0.32%時(shí),在鑄造時(shí),由于超過氮的固溶度而產(chǎn)生氣孔(blowhole)、針孔(pinhole)等,誘發(fā)表面缺陷,從而難以穩(wěn)定地制造鋼。另外,為了確保304鋼水平的耐蝕性,添加0.15%以上的n,當(dāng)n含量過低時(shí),難以確保適當(dāng)?shù)南喾致?。因此,?yōu)選將n含量控制在0.15~0.32%。cu為與mn、ni及n一起是奧氏體相穩(wěn)定化的元素,為了節(jié)約成分,優(yōu)選以最小限度地降低與ni起到相同作用的cu的含量。但是,為了能夠抑制在冷加工時(shí)形成過多的塑性誘發(fā)馬氏體,并為了確保充分的奧氏體相的穩(wěn)定度,優(yōu)選添加0.2%以上的cu。另一方面,當(dāng)cu含量超過2.5%時(shí),由于熱脆性而會(huì)使產(chǎn)品加工變得困難,因此,優(yōu)選將cu含量調(diào)整為0.2~2.5%。w及mo為形成奧氏體相的元素,同時(shí)還是提高耐蝕性的元素,在進(jìn)行熱處理時(shí),在700~1000℃溫度下,由于促進(jìn)金屬間化合物的形成,從而是劣化耐蝕性及機(jī)械性質(zhì)的元素。當(dāng)w及mo的含量超過1%時(shí),由于金屬間化合物的形成,會(huì)導(dǎo)致耐蝕性的急劇下降,尤其會(huì)導(dǎo)致延伸率的急劇下降。此外,為了顯示出耐蝕性的改善效果,可以添加0.1%以上的w及mo。因此,優(yōu)選將w及mo的含量控制在0.1~1.0%,并且可以含有w及mo中的至少一種以上。ti、nb、v為與氮反應(yīng)而形成氮化物的元素,在鋼水中結(jié)晶為tin、nbn、vn等,在凝固時(shí)作為鐵素體相的成核位點(diǎn),即使增加冷卻速度也能夠充分地進(jìn)行凝固,從而抑制板坯的斷裂。此外,這些元素在制造過程中,即在再加熱或熱軋時(shí)充分固溶,并且在冷卻時(shí)與碳及氮進(jìn)行反應(yīng),從而形成碳氮化物,隨著抑制cr碳化物的形成,有助于提高耐蝕性。尤其是在焊接時(shí),抑制熱影響部中cr碳化物的形成。當(dāng)分別過多地添加這些元素時(shí),即ti超過0.1%,nb超過0.05%,v超過0.15%時(shí),在凝固時(shí)它們的結(jié)晶物會(huì)形成大型集群(cluster),從而會(huì)導(dǎo)致堵塞鑄造噴嘴的現(xiàn)象,此外,它們存在于板坯表層部時(shí),會(huì)成為軋制時(shí)產(chǎn)生缺陷、加工時(shí)引起斷裂的原因。此外,大部分為昂貴的合金元素,當(dāng)大量添加時(shí),會(huì)導(dǎo)致制造成分的上升。因此,優(yōu)選地分別控制為以下范圍,ti:0.001~0.1%,nb:0.001~0.05%,v:0.001~0.15%,并且可以含有ti、nb及v中的至少一種以上。另外,本發(fā)明通過調(diào)整合金元素的含量、分配系數(shù)及相分率來控制堆垛層錯(cuò)能,從而能夠保持優(yōu)異的延伸率和耐蝕性。例如,下述[式1]為利用合金中全部成分的含量來導(dǎo)出堆垛層錯(cuò)能的式。sfe=25.7+1.59(ni+0.5cu)-0.85cr+0.001×cr2+38.2n0.5-2.8si-1.34mn+0.06mn2….[式1]所述[式1]中的cr、ni、cu、si、mn、n表示各個(gè)成分元素的總含量(wt%)。但是,本申請(qǐng)人以多種方法測(cè)定并計(jì)算本發(fā)明鋼的堆垛層錯(cuò)能的結(jié)果,發(fā)現(xiàn)對(duì)于預(yù)測(cè)合金的物理性質(zhì)方面,與如同[式1]僅利用整體合金組合物的成分含量來計(jì)算堆垛層錯(cuò)能相比,利用奧氏體組織的成分含量來計(jì)算時(shí)更為準(zhǔn)確。為此,發(fā)現(xiàn)了與僅利用整體合金組合物的成分含量來計(jì)算堆垛層錯(cuò)能相比,考慮合金元素的組織間分配系數(shù)來計(jì)算堆垛層錯(cuò)能時(shí),與實(shí)際測(cè)定的堆垛層錯(cuò)能值更加接近。因此,本申請(qǐng)人為了能夠通過利用奧氏體相的分配系數(shù)來推導(dǎo)出奧氏體相的堆垛層錯(cuò)能,對(duì)所述[式1]進(jìn)行了補(bǔ)充,從而獲得了下述[式2]。sfe=25.7+1.59×ni/[k(ni)-k(ni)×v(γ)+v(γ)]+0.795×cu/[k(cu)-k(cu)×v(γ)+v(γ)]-0.85×cr/[k(cr)-k(cr)×v(γ)+v(γ)]+0.001×(cr/[k(cr)-k(cr)×v(γ)+v(γ)])2+38.2×(n/[k(n)-k(n)×v(γ)+v(γ)])0.5-2.8×si/[k(si)-k(si)×v(γ)+v(γ)]-1.34×mn/[k(mn)-k(mn)×v(γ)+v(γ)]+0.06×(mn/[k(mn)-k(mn)×v(γ)+v(γ)])2………………[式2]。在[式2]中,ni、cu、cr、n、si、mn表示各元素成分的總含量(wt%)。并且,在所述[式2]中,k(x)是各元素成分(x)的分配系數(shù),由下述[式3]表示。k(x)=[鐵素體相中的x元素的含量]/[奧氏體相中的x元素的含量]………………[式3]。本申請(qǐng)人利用了與常規(guī)的掃描電子顯微鏡進(jìn)行的能量彌散的x線分析(edax)相比更準(zhǔn)確的fe-電子微探針分析(epma)及fe-透射電子顯微鏡(tem)來測(cè)定了多種退火條件及合金系中的各個(gè)合金元素的分配系數(shù)。確認(rèn)了所測(cè)定的大部分合金元素的分配系數(shù)在作為熱退火或冷退火的溫度范圍的900~1200℃溫度下不隨的溫度變化而變化。即,確認(rèn)到所述k(x)中的k(cr)=1.16,k(ni)=0.57,k(mn)=0.73,k(cu)=0.64,并且k(n)和k(si)隨著n和si的含量(wt%)而變。但是,n:0.2~0.32%時(shí),k(n)=0.15,n<0.2%時(shí),k(n)=0.25,si≤1.5%時(shí),k(si)=2.76-0.96×si,si>1.5%時(shí),k(si)=1.4。此時(shí),合金元素n、si表示不銹鋼的總成分。但是,在本實(shí)施例中,由于n:0.15~0.32%,因此,n為0.15%以上且小于0.2%時(shí),適用k(n)=0.25,n:0.2~0.32時(shí),適用k(n)=0.15,由于si為0.2~3.0%,因此,si為0.2~1.5%時(shí),適用k(si)=2.76-0.96×si,si大于1.5%且小于3.0%時(shí),適用k(si)=1.4。并且,所述[式2]中,v(γ)為奧氏體相分率,奧氏體相分率被定義為下述關(guān)系式。1=v(α)+v(γ)在此,v(α)為鐵素體相分率,v(γ)具有0.45~0.75的范圍值。另外,對(duì)于將奧氏體相的堆垛層錯(cuò)能值限定為19~37的理由進(jìn)行說明。已知奧氏體相的堆垛層錯(cuò)能控制奧氏體相的變形機(jī)理。通常,就單相的奧氏體系不銹鋼而言,奧氏體相的堆垛層錯(cuò)能是指外部施加的塑性變形能對(duì)奧氏體相的變形起到作用的程度。通常,堆垛層錯(cuò)能越低,在奧氏體相中形成ε馬氏體相后,會(huì)增加對(duì)鋼的加工固化起到作用的應(yīng)變誘發(fā)馬氏體相的形成程度。在中間程度的堆垛層錯(cuò)能的情況下,在它們孿晶的交叉點(diǎn)會(huì)形成應(yīng)變誘發(fā)馬氏體相,因此,施加的塑性變形能會(huì)機(jī)械性地導(dǎo)致相變化,從而引起從奧氏體相相變?yōu)轳R氏體相。因此,就不銹鋼而言,已知在相當(dāng)廣泛的范圍中,除了中間相(ε馬氏體相或機(jī)械性孿晶)的差異之外,形成應(yīng)變誘發(fā)馬氏體相。因此,當(dāng)堆垛層錯(cuò)能小于50mj/m2時(shí),在奧氏體相中形成ε馬氏體相后,形成應(yīng)變誘發(fā)馬氏體相,或者在奧氏體相中形成機(jī)械性孿晶后,形成應(yīng)變誘發(fā)馬氏體相。但是,已知當(dāng)堆垛層錯(cuò)能為50mj/m2以上時(shí),在不形成機(jī)械孿晶或ε馬氏體相的前提下,根據(jù)位錯(cuò)移動(dòng)而進(jìn)行變形,因此不能很好地形成從奧氏體相到馬氏體相的相變。此外,確認(rèn)到當(dāng)使用[式1]并僅利用合金的總成分來推出堆垛層錯(cuò)能時(shí),在11以下容易形成應(yīng)變誘發(fā)馬氏體相,因此,在變形的初期發(fā)生急劇的加工固化,即形成應(yīng)變誘發(fā)馬氏體相,從而導(dǎo)致延伸率的急劇降低,還確認(rèn)了,根據(jù)熱處理或制造工序,隨著被分配到奧氏體相中的合金元素的變化,在部分成分系中形成應(yīng)變誘發(fā)馬氏體相的舉動(dòng)會(huì)有所不同。對(duì)此,本申請(qǐng)人考慮到多種制造工序及熱處理后的奧氏體相中分配的合金元素的分配系數(shù),如同所述[式2]補(bǔ)充了計(jì)算式。其結(jié)果,當(dāng)計(jì)算的奧氏體相的堆垛層錯(cuò)能小于19時(shí),首先形成作為中間相的ε馬氏體相,并在所形成的ε馬氏體相的交叉點(diǎn)上形成了馬氏體相。但是,這些馬氏體相在變形的初期急劇形成,從而由于急劇的加工固化而顯示出降低延伸率的現(xiàn)象。另外,當(dāng)利用補(bǔ)正的計(jì)算式計(jì)算得出的奧氏體相的堆垛層錯(cuò)能超過37時(shí),利用透射電子顯微鏡進(jìn)行調(diào)查的結(jié)果,確認(rèn)到在塑性變形后未觀察到馬氏體相的形成。因此,可知奧氏體相的堆垛層錯(cuò)能的優(yōu)選范圍為19~37。另外,根據(jù)本發(fā)明的經(jīng)濟(jì)型雙相不銹鋼,以體積分?jǐn)?shù)計(jì),優(yōu)選形成45~75%的奧氏體相和25~55%的鐵素體相。其原因在于,當(dāng)奧氏體相分率小于45%時(shí),在退火中,奧氏體相上會(huì)發(fā)生奧氏體相形成元素過度濃縮的現(xiàn)象。由此,奧氏體相得到充分的穩(wěn)定,從而抑制變形中所產(chǎn)生的應(yīng)變誘發(fā)馬氏體相的相變,并且由于合金元素的充分固溶而增加奧氏體相的含量,從而也可以充分確保材料的拉伸強(qiáng)度。但是,由于產(chǎn)生延展性降低的現(xiàn)象,從而難以充分獲得所需的延伸率及強(qiáng)度。因此,從高延展性的觀點(diǎn)來看,奧氏體的相分率優(yōu)選為45%以上。但是,當(dāng)奧氏體相分率超過75%時(shí),在熱軋時(shí)產(chǎn)生表面裂紋等,從而會(huì)導(dǎo)致熱加工性的降低,并喪失作為雙相組織鋼的特性。因此,奧氏體相分率優(yōu)選為75%以下。此外,就本發(fā)明而言,在冷加工或拉伸變形時(shí),形成應(yīng)變誘發(fā)馬氏體相的臨界應(yīng)變值的范圍優(yōu)選維持在0.1~0.25。從應(yīng)力-變形曲線的拐點(diǎn)處開始測(cè)定形成應(yīng)變誘發(fā)馬氏體相的臨界應(yīng)變量,其通常示出在形成應(yīng)變誘發(fā)馬氏體相的鋼中,對(duì)馬氏體相的加工固化起作用的時(shí)間點(diǎn)的變形值。詳細(xì)地,對(duì)獲得形成應(yīng)變誘發(fā)馬氏體相的臨界應(yīng)變值的方法進(jìn)行如下說明。首先,在經(jīng)過冷軋退火的材料中,以美國(guó)材料與試驗(yàn)協(xié)會(huì)(astm)小尺寸(sub-size)的規(guī)格與軋制方向平行地截取試片并進(jìn)行加工后,使用拉伸試驗(yàn)機(jī)在常溫(例如20~25℃)下以1.0×10-3/s的應(yīng)變速率(strainrate)進(jìn)行拉伸試驗(yàn),直至材料斷裂。此時(shí)所獲得的真應(yīng)變-真應(yīng)力曲線的斜率變化為加工固化速度。加工固化速度的變化與應(yīng)變誘發(fā)馬氏體相的形成具有密切的關(guān)系。就加工固化速度而言,在發(fā)生屈服后,隨著拉伸變形的進(jìn)行而逐漸減小,直到形成應(yīng)變誘發(fā)馬氏體相而開始對(duì)加工固化起作用的時(shí)間點(diǎn),即在臨界應(yīng)變中形成拐點(diǎn)。并且,以拐點(diǎn)以上的變形進(jìn)行拉伸變形,同時(shí)當(dāng)增加應(yīng)變誘發(fā)馬氏體相的形成時(shí),再次增加加工固化速度。因此,臨界應(yīng)變值為,形成應(yīng)變誘發(fā)馬氏體相而對(duì)加工固化開始起作用的時(shí)間點(diǎn)的應(yīng)變值,是指在通過拉伸實(shí)驗(yàn)而獲得的應(yīng)力-應(yīng)變曲線(stress-straincurve)中的相當(dāng)于拐點(diǎn)的應(yīng)變值,在數(shù)學(xué)上為對(duì)曲線進(jìn)行二次微分的值為“0”的點(diǎn)。因此,當(dāng)臨界應(yīng)變值小于0.1時(shí),在變形時(shí)會(huì)過于容易地形成應(yīng)變誘發(fā)馬氏體相,在變形初期由于急劇的加工固化而急劇降低材料的延展性。此外,當(dāng)應(yīng)變誘發(fā)馬氏體相形成過晚時(shí),即臨界應(yīng)變值超過0.25時(shí),由于材料的加工固化不足而會(huì)產(chǎn)生局部應(yīng)力集中而發(fā)生頸縮現(xiàn)象,從而會(huì)引起延伸率的降低。因此,加工固化速度應(yīng)具有合適的范圍。因此,本發(fā)明中形成應(yīng)變誘發(fā)馬氏體相的臨界應(yīng)變值的范圍優(yōu)選為0.1~0.25。此外,在本發(fā)明的經(jīng)濟(jì)型雙相不銹鋼中,控制奧氏體相的穩(wěn)定度非常重要。通常,應(yīng)變誘發(fā)馬氏體相是在不穩(wěn)定的奧氏體相變形時(shí)形成的硬的相,會(huì)引起加工固化而對(duì)增加鋼的延伸率起作用。就由奧氏體相及鐵素體相形成的雙相不銹鋼的本發(fā)明鋼而言,可以利用適當(dāng)?shù)胤峙浜辖鹪貋碚{(diào)整奧氏體相的穩(wěn)定度。本發(fā)明中,用于使合金元素得到合適的分配的方法,使用了急速凝固法。就急速凝固而言,由于在固相中發(fā)生擴(kuò)散的時(shí)間不足,因此,形成的奧氏體相及鐵素體相會(huì)非平衡地形成凝固。對(duì)這些非平衡的凝固相進(jìn)行短時(shí)間的熱軋退火熱處理時(shí),利用所產(chǎn)生的合金元素的分配,可以使奧氏體相的穩(wěn)定度充分地控制在所需范圍內(nèi)。作為用于形成其的方法,可以以以下方式設(shè)計(jì)合金,即,通過將在固相中的擴(kuò)散速度快的氮的含量維持在高于常規(guī)情況,從而使大部分的氮偏析到奧氏體相上。[實(shí)施例]下面,通過本發(fā)明的經(jīng)濟(jì)型雙相不銹鋼的多種實(shí)施例來對(duì)延伸率及耐蝕性進(jìn)行詳細(xì)說明。利用調(diào)整為如下述表1的成分含量的鋼水來準(zhǔn)備試片后,在熱軋、熱軋退火、冷軋后進(jìn)行冷軋退火,調(diào)整材料的相分率,從而測(cè)定延伸率及耐蝕性。對(duì)于拉伸試驗(yàn)片,與軋制方向平行地對(duì)astm-subsize的試片進(jìn)行加工后,在常溫下將拉伸變形率速度調(diào)節(jié)為1.0×10-3/s并進(jìn)行測(cè)定。下述[表1]示出了對(duì)于實(shí)驗(yàn)鋼種的合金組成(重量%)。此外,下述[表2]中示出了將上述[表1]中部分實(shí)驗(yàn)鋼種在1100℃下進(jìn)行退火熱處理后所測(cè)定的鐵素體相和奧氏體相的相分率。此外,下述[表3]中示出了,對(duì)使用在本發(fā)明的說明中的比較鋼及發(fā)明鋼,不考慮分配系數(shù)而通過[式1]計(jì)算的堆垛層錯(cuò)能值,考慮分配系數(shù)及相分率,并利用[式2]計(jì)算的堆垛層錯(cuò)能值、吉布斯自由能(gibbsfreeenegy)差異、是否形成應(yīng)變誘發(fā)馬氏體相、臨界應(yīng)變值、延伸率的結(jié)果。此時(shí),使用吉布斯自由能(gibbsfreeenegy)的原因在于,計(jì)算具有相同成分的相的結(jié)晶結(jié)構(gòu)為fcc的奧氏體時(shí),其為bcc的馬氏體時(shí)的熱力學(xué)吉布斯自由能的差異,并滿足δg=gm-gγ≤0(馬氏體相的吉布斯能-奧氏體相的吉布斯能)的條件才能形成應(yīng)變誘發(fā)馬氏體相。如上所述,吉布斯自由能差異和應(yīng)變誘發(fā)馬氏體相的形成具有密切的關(guān)系,例如,吉布斯自由能差異(δg)為正數(shù)時(shí),可以表示不形成應(yīng)變誘發(fā)馬氏體相,吉布斯自由能差異(δg)為負(fù)數(shù)時(shí),可以表示形成應(yīng)變誘發(fā)馬氏體相。在本實(shí)施例中,為了計(jì)算奧氏體相和馬氏體相的吉布斯自由能,利用商用軟件factsage6.4(thermfact和gtt-技術(shù)(thermfactandgtt-technologies))來進(jìn)行計(jì)算。尤其,為了計(jì)算吉布斯自由能,首先,需要知道以鐵素體相-奧氏體相的雙相存在的鋼中的奧氏體相中存在的合金成分,奧氏體相中存在的合金成分的含量可以利用本發(fā)明中公開的分配系數(shù)和相分率來進(jìn)行計(jì)算。例如,可以利用奧氏體相中存在的x成分=x/[k(x)-k(x)×v(γ)+v(γ)](x:總x成分,k(x):分配系數(shù),v(γ):奧氏體相分率)來進(jìn)行計(jì)算。此外,是否形成應(yīng)變誘發(fā)馬氏體相是利用鐵素體范圍(商用產(chǎn)品)在拉伸變形時(shí)發(fā)生頸縮之前的裂紋拉伸區(qū)間進(jìn)行了測(cè)定。表1表2鋼種鐵素體相分率,%奧氏體相分率,%比較鋼15149比較鋼28317比較鋼33565比較鋼45446比較鋼54159發(fā)明鋼14555發(fā)明鋼23763發(fā)明鋼34060發(fā)明鋼43850發(fā)明鋼52853發(fā)明鋼63367發(fā)明鋼74258發(fā)明鋼84753發(fā)明鋼94258發(fā)明鋼104852表3就經(jīng)濟(jì)型雙相不銹鋼而言,相分率隨著合金成分及熱處理溫度而變化。由此,[表2]中示出了分別以1100℃的溫度對(duì)比較鋼1~比較鋼5及發(fā)明鋼1~發(fā)明鋼10進(jìn)行熱處理時(shí)的鐵素體和奧氏體相分率。就發(fā)明鋼1~發(fā)明鋼10而言,可知鐵素體的相分率包含在約25~55%的范圍內(nèi),奧氏體的相分率包含在約45~75%的范圍內(nèi)。此外,比較鋼2在1100℃溫度下處理時(shí),分別示出了鐵素體的相分率為83%,此時(shí),奧氏體相分率也分別示出為17%。即,可知比較鋼2未包含在本發(fā)明的鐵素體及奧氏體的相分率范圍內(nèi)。此外,可知比較鋼4為考慮分配的奧氏體相的堆垛層錯(cuò)能為17.88mj/m2,未包含在奧氏體相的堆垛層錯(cuò)能(sfe)值的合適范圍內(nèi)。另外,圖1為本發(fā)明中所獲得的具有代表性的公稱應(yīng)變-公稱應(yīng)力比較曲線,是在1100℃下對(duì)各個(gè)材料進(jìn)行熱處理后實(shí)施拉伸實(shí)驗(yàn)的結(jié)果。就比較鋼1而言,在均勻應(yīng)變中未形成應(yīng)變誘發(fā)馬氏體相。其結(jié)果,由于在塑性變形時(shí),不存在能夠抑制因加工固化導(dǎo)致的局部頸縮的應(yīng)變誘發(fā)馬氏體相,從而預(yù)測(cè)了延伸率的下降,且實(shí)際上比較鋼1的延伸率為31%左右,非常差。并且,可以確認(rèn)比較鋼3在塑性變形時(shí)形成應(yīng)變誘發(fā)馬氏體相的臨界應(yīng)變值為0.1以下(拐點(diǎn);用箭頭表示),由此由于應(yīng)變誘發(fā)馬氏體相急劇形成而導(dǎo)致急劇的加工固化,從而可以預(yù)測(cè)會(huì)產(chǎn)生延伸率降低。實(shí)際上比較例3雖然是由鐵素體相和奧氏體相構(gòu)成的雙相不銹鋼,但延伸率為35%左右非常差。另外,本發(fā)明鋼表明了,當(dāng)應(yīng)力-變形曲線中形成應(yīng)變誘發(fā)馬氏體相的臨界應(yīng)變范圍為0.1~0.25時(shí),通過適當(dāng)?shù)乜刂萍庸r(shí)形成的應(yīng)變誘發(fā)馬氏體相的形成速度,從而能夠得到多種值的延伸率。即將發(fā)明鋼8和發(fā)明鋼1進(jìn)行比較可知,形成應(yīng)變誘發(fā)馬氏體相的臨界應(yīng)變?cè)酱螅冃温蕰?huì)得到增加。這是由于控制冷加工時(shí)奧氏體相相變?yōu)閼?yīng)變誘發(fā)馬氏體相,因此延伸率大部分為45%以上。其與本發(fā)明鋼所要代替的通常的經(jīng)濟(jì)型雙相鋼的比較鋼1相比,顯示出非常優(yōu)異的延伸率,還顯示出了能夠與本發(fā)明中所要替代的304鋼的延伸率匹敵的優(yōu)異的延伸率。詳細(xì)而言,當(dāng)臨界應(yīng)變值小于0.1時(shí),由于急劇形成應(yīng)變誘發(fā)馬氏體相的同時(shí),急劇的加工固化導(dǎo)致的材料的固化,從而導(dǎo)致急劇降低延伸率。此外,當(dāng)臨界應(yīng)變值超過0.25時(shí),由于應(yīng)變誘發(fā)馬氏體相形成得過慢,無法抑制根據(jù)變形的材料的局部頸縮。因此,就由本合金系的奧氏體相-鐵素體相形成的經(jīng)濟(jì)型雙相不銹鋼而言,當(dāng)形成應(yīng)變誘發(fā)馬氏體相的臨界應(yīng)變值的范圍為0.1~0.25時(shí),可以確保比現(xiàn)有的雙相鋼所具的30%以下的延伸率更為優(yōu)異的45%以上的延伸率,并且在部分應(yīng)變條件下,可以確保能夠與304鋼匹敵的45%以上的延伸率。由此,在進(jìn)行冷加工時(shí),形成應(yīng)變誘發(fā)馬氏體相的臨界應(yīng)變值優(yōu)選為0.1~0.25。并且,如[表3]中的比較鋼1及比較鋼5所示,能夠確認(rèn)即使根據(jù)[式2]的堆垛層錯(cuò)能在19~37的范圍內(nèi),奧氏體相中形成馬氏體相的吉布斯自由能值也顯示為正數(shù)值,且在利用透射電子顯微鏡觀察的微細(xì)組織中未觀察到應(yīng)變誘發(fā)馬氏體相的形成,在這種情況下,觀察到延伸率降低。此外,如[表3]的比較鋼2及比較鋼3所示,即使由于吉布斯自由能值顯示為負(fù)值而形成應(yīng)變誘發(fā)馬氏體相,臨界應(yīng)變值不在0.1~0.25的范圍時(shí),也觀察到延伸率降低。圖2a及圖2b分別示出比較鋼1和發(fā)明鋼1的透射電子顯微鏡觀察的微細(xì)組織。就比較鋼1而言,如圖2a所示,可知雖然觀察到由于變形導(dǎo)致的變形帶或機(jī)械孿晶,但未觀察到應(yīng)變誘發(fā)馬氏體相。就發(fā)明鋼1而言,如圖2b所示,可知變形帶或機(jī)械孿晶的交叉點(diǎn)上形成了應(yīng)變誘發(fā)馬氏體相(應(yīng)變誘發(fā)馬氏體相用箭頭表示)。另外,圖3為示出延伸率和形成應(yīng)變誘發(fā)馬氏體相的臨界應(yīng)變值之間的關(guān)系的圖表,參照[圖1]的應(yīng)力-變形曲線,將形成馬氏體相的臨界應(yīng)變的測(cè)定結(jié)果示于圖3中。從圖3所述,能夠確認(rèn)臨界應(yīng)變值小于0.1和超過0.25的情況下,不能確保45%的延伸率,而另一方面,臨界應(yīng)變值的范圍具有0.1~0.25值的情況下,能夠確保45%以上的延伸率。另外,根據(jù)本發(fā)明的經(jīng)濟(jì)型雙相不銹鋼從液態(tài)凝固成固態(tài)時(shí),根據(jù)氮固溶度的差異,根據(jù)解決氮?dú)馍苫蚺懦龅膯栴},均可使用連鑄方式及薄帶連鑄方式來制造。首先,對(duì)使用連鑄法來制造經(jīng)濟(jì)型雙相不銹鋼的方法進(jìn)行說明。圖4為概略地示出本發(fā)明一實(shí)施例的經(jīng)濟(jì)型雙相不銹鋼的連鑄方式制造工序的圖。根據(jù)本發(fā)明一實(shí)施例的經(jīng)濟(jì)型雙相不銹鋼在依次配置有鋼包(ladle)(110)、中間包(120)、鑄膜(130)、多個(gè)扇形體(segment)(140)的常規(guī)的連鑄設(shè)備(100)中制造。但是,在扇形體(140)的后段部進(jìn)一步具備混合空氣和冷卻水并進(jìn)行噴射的噴射裝置(150)。為了通過連鑄方式來制造經(jīng)濟(jì)型雙相不銹鋼,首先準(zhǔn)備具有上述公開的合金成分的鋼水,使其移動(dòng)到鋼包(110)后,利用套管噴嘴(shroudingnozzle)(111)使其臨時(shí)儲(chǔ)存到中間包(120)中。此時(shí),臨時(shí)儲(chǔ)存在中間包(120)中的鋼水優(yōu)選維持在比理論凝固溫度高出10~50℃的溫度。詳細(xì)而言,中間包(120)中的鋼水溫度與理論凝固溫度的溫差δt(℃)的下限值為10℃,上限值為50℃,當(dāng)δt小于下限值10℃時(shí),鋼水(m)會(huì)在中間包(120)中進(jìn)行凝固,從而在連鑄中會(huì)產(chǎn)生問題,當(dāng)δt超過上限值50℃時(shí),在凝固中凝固速度會(huì)變慢,使凝固組織變得粗大,從而在連鑄鑄坯上容易產(chǎn)生凝固裂紋和在熱軋時(shí)容易引起線狀缺陷。并且,在中間包(120)中利用浸漬噴嘴(121)向鑄膜(130)中注入鋼水。此時(shí),在鑄膜(130)中使鋼水(m)的冷卻速度維持在500~1500℃/分鐘,并使鋼水通過鑄膜(130)進(jìn)行一次冷卻。此時(shí),當(dāng)冷卻速度小于500℃/分鐘時(shí),由于初期形成的δ鐵素體凝固導(dǎo)致的氮溶解度差異而產(chǎn)生的氮?dú)馔ㄟ^鑄膜(130)的凝固殼排出,由此會(huì)產(chǎn)生粗大的氮針孔,因此,連鑄的板坯產(chǎn)生大量的粗大的氮針孔。并且,在初期形成的δ鐵素體發(fā)生粗大化,從而會(huì)對(duì)外部應(yīng)力較為脆弱。此外,當(dāng)冷卻速度小于500℃/分鐘時(shí),連鑄時(shí)鑄膜(130)中的冷卻(一次冷卻)及扇形體(140)中的冷卻(二次冷卻)的量減少,由此在鑄造中鑄坯(s)的熱傳遞變慢,從而降低鑄坯凝固層的強(qiáng)度,發(fā)生鑄坯膨脹(bulging)的現(xiàn)象,導(dǎo)致操作及質(zhì)量的惡化。并且,將冷卻速度控制為超過1500℃/分鐘,從氮針孔的方面是非常有利的,但是因目前的連鑄設(shè)備存在限制,無法進(jìn)行連鑄,在連鑄時(shí)由于枝狀晶體(dendrite)之間殘留的溶質(zhì)元素的偏析擴(kuò)散的時(shí)間變少,從而會(huì)發(fā)生鑄坯表面裂紋。由于這種現(xiàn)象,具有在鑄膜(130)內(nèi)部產(chǎn)生鑄坯殼(外形,殼(shell))一時(shí)斷裂的重疊現(xiàn)象的問題。因此,在鑄膜(130)內(nèi)進(jìn)行一次冷卻時(shí),優(yōu)選將冷卻速度設(shè)定為500~1500℃/分鐘。鑄膜(130)中形成凝固殼的鋼水(m),即鑄坯(s)向扇形體(140)進(jìn)行拉拔,從而進(jìn)行二次冷卻,此時(shí),優(yōu)選向鑄坯(s)噴射0.25~0.35l/kg的冷卻水。這樣限定扇形體(140)中的噴水量的原因如下。扇形體(140),即將二次冷卻帶的噴水量設(shè)置得相對(duì)較大時(shí),雖然可以微細(xì)地形成凝固組織,但當(dāng)噴水量超過0.35l/kg時(shí),在連續(xù)鑄造工序時(shí),偏析到凝固組織之間的雜質(zhì)擴(kuò)散的時(shí)間會(huì)變少,會(huì)以σ相存在,從而會(huì)在鑄坯表面產(chǎn)生裂紋。此外,不僅會(huì)產(chǎn)生熱應(yīng)力所導(dǎo)致的裂紋,還會(huì)在表面過度產(chǎn)生殘留應(yīng)力,因此,在進(jìn)行鑄坯研磨(grinding)時(shí)會(huì)在表面產(chǎn)生裂紋。并且,當(dāng)噴水量小于0.25l/kg時(shí),凝固組織會(huì)變得過大,從而由于晶界上生成的σ相而具有產(chǎn)生凝固裂紋的問題點(diǎn),并且在連鑄中鑄坯凝固殼(shell)的強(qiáng)度會(huì)降低,從而會(huì)引起因鑄坯膨脹(bulging)所導(dǎo)致的裂紋的問題。因此,在扇形體(140)中的噴水量范圍優(yōu)選為0.25~0.35l/kg。并且,對(duì)向扇形體(140)拉拔的而進(jìn)行二次冷卻的鑄坯進(jìn)行三次冷卻。三次冷卻時(shí)繼續(xù)向扇形體(140)拉拔,同時(shí)在鑄坯的表面溫度為1100~1200℃范圍內(nèi),以空氣和冷卻水的比例(空氣/冷卻水)為1.0~1.2方式,將100~125l/kg·分鐘的冷卻水與空氣進(jìn)行混合而向鑄坯(s)表面整體進(jìn)行噴射,以進(jìn)行冷卻。三次冷卻是為了使鑄坯(s)的表面確保均勻的氧化皮而進(jìn)行控制。其原因在于,就經(jīng)濟(jì)型雙相不銹鋼而言,由于其在加熱爐中的氧化量非常少,從而在熱軋時(shí)因氧化皮帶來的潤(rùn)滑效果小,從而難以降低表面裂紋。因此,為了在軋制中避免因輥和鋼板的接觸而導(dǎo)致的溫度下降,并且為了減少輥和鋼板之間的摩擦力來防止表面裂紋,應(yīng)在鋼板表面形成致密且厚的氧化皮,此外還需在軋制中不易發(fā)生剝離。如上所述,限定鑄坯(s)的表面溫度、冷卻水的噴水量及冷卻水和空氣的比例(空氣/冷卻水)的原因在于,在不滿足上述條件的情況下,在鑄坯(s)的表面不能以所需水平(大約為35μm±2μm)的厚度形成氧化皮,并且所生成的氧化皮不能均勻地形成。下面,按照[表4],將具有本發(fā)明組成的經(jīng)濟(jì)型雙相不銹鋼在中間包中的鋼水溫度、在鑄膜中的冷卻速度、在二次冷卻帶(coolingzone)中的噴水量進(jìn)行變更,從而生產(chǎn)鑄坯,并將作為其結(jié)果的針孔及鑄坯表面產(chǎn)生裂紋的程度也示于[表4]中。此時(shí),將板坯的表面約研磨0.5mm左右后,通過觀察被研磨的表面來確認(rèn)鑄坯是否產(chǎn)生針孔。表4從[表4]可知,滿足本發(fā)明的所有控制條件的發(fā)明例的發(fā)明材料a~發(fā)明材料e在連鑄的鑄坯中均沒有產(chǎn)生因氮引起的針孔,并且,未產(chǎn)生膨脹且在熱軋鋼卷表面未產(chǎn)生缺陷。并且,比較材料f及比較材料g在鑄膜中的冷卻速度均在本發(fā)明的范圍內(nèi),因此,在鑄坯的內(nèi)部未產(chǎn)生因氮?dú)庖鸬尼樋?。但是,比較材料f的噴水量大于本發(fā)明的范圍,雖然在鑄造中未產(chǎn)生膨脹,但鑄造表面形成很強(qiáng)的熱應(yīng)力作用,從而誘發(fā)了裂紋的產(chǎn)生。此外,比較材料g的二次冷卻帶的噴水量的范圍小于本發(fā)明的范圍,因此隨著在鑄坯上產(chǎn)生膨脹,在鑄坯表面產(chǎn)生了裂紋。因此,在熱軋時(shí)由于形成局部過多的氧化皮,從而在熱軋鋼卷表面產(chǎn)生了線狀缺陷。并且,比較材料i及比較材料j在鑄膜中的冷卻速度低于本發(fā)明的范圍,因此在鑄坯上產(chǎn)生了嚴(yán)重的針孔。但是,雖然由于二次冷卻帶的噴水量在本發(fā)明的范圍內(nèi),從而連鑄鑄坯的表面良好,但是由于鑄坯上存在的針孔導(dǎo)致熱軋時(shí)產(chǎn)生大量的線狀缺陷。此外,圖7為根據(jù)本發(fā)明的連鑄方式而制造的比較材料i和發(fā)明材料a的組織照片,圖8為根據(jù)本發(fā)明的連鑄方式制造的比較材料h的表面缺陷照片,圖9為根據(jù)本發(fā)明的連鑄方式制造的比較材料f的表面缺陷照片。此時(shí),圖8及圖9為在比較材料h及比較材料f進(jìn)行熱軋后發(fā)現(xiàn)的熱軋鋼圈表面的缺陷照片。由圖7可以確認(rèn),在發(fā)明材料a的鑄坯在表面上沒有發(fā)現(xiàn)針孔,但比較材料i上產(chǎn)生了大量的針孔。此外,由圖8可知,對(duì)針孔產(chǎn)生良好的比較材料h進(jìn)行熱軋后,觀察了熱軋鋼卷的表面,觀察到沿軋制方向產(chǎn)生了大量的被延伸的針孔性缺陷。此外,圖9是將比較材料f進(jìn)行熱軋后,對(duì)熱軋鋼卷的表面進(jìn)行觀察,從而觀察到產(chǎn)生了大量的鑄坯裂紋性表面缺陷。因此,通過多種實(shí)施例確認(rèn)了以下內(nèi)容,根據(jù)本發(fā)明通過適當(dāng)?shù)乜刂七B鑄時(shí)鑄膜內(nèi)的冷卻速度和二次冷卻帶的噴水量,從而能夠獲得抑制了針孔、鑄造時(shí)的裂紋及膨脹的發(fā)生的由奧氏體相和鐵素體相構(gòu)成的經(jīng)濟(jì)型雙相不銹鋼的優(yōu)異的鑄坯品質(zhì),不僅如此,還確認(rèn)了能夠進(jìn)行穩(wěn)定的連鑄操作。此外,按照[表5],將對(duì)具有本發(fā)明的組成且經(jīng)過一次冷卻和二次冷卻的雙相不銹鋼進(jìn)行三次冷卻時(shí),變更冷卻時(shí)的冷卻水量、噴射時(shí)間、空氣/冷卻水比例、鑄坯表面溫度,從而生產(chǎn)鑄坯,并將作為其結(jié)果的氧化皮的厚度及均勻程度也示于[表5]中。表5如發(fā)明材料1~發(fā)明材料4可知,在鑄坯表面溫度為1000~1200℃時(shí),使空氣/冷卻水的比例維持在1.0~1.2,同時(shí)以100~120l/㎏·分鐘的冷卻水量噴射20~30分鐘冷卻水時(shí),氧化皮非常均勻且變厚。但是,如比較材料1及比較材料2,以50l/kg·分鐘或80l/kg·分鐘的冷卻水量進(jìn)行噴射時(shí),因冷卻水的量不充分,從而未能促進(jìn)氧化皮的生成,也未能獲得均勻的氧化皮。并且,如比較材料3~比較材料5,變更空氣與冷卻水的比例(空氣/冷卻水)來調(diào)查氧化皮,可以確認(rèn)空氣的量越充分,越增加氧化皮的厚度。由此,為了形成所需厚度的氧化皮層,優(yōu)選將空氣與冷卻水的比例(空氣/冷卻水)控制為1.0以上。但是,當(dāng)空氣的比例超過上限值1.2時(shí),雖然能獲得充分的氧化皮層,但會(huì)存在對(duì)整體冷卻水系統(tǒng)產(chǎn)生影響的擔(dān)憂。如比較材料6及比較材料7,以15分鐘及10分鐘的噴射時(shí)間噴射冷卻水時(shí),雖然冷卻水噴射時(shí)的溫度和空氣/冷卻水比例等接近發(fā)明材料的條件,但由于噴射時(shí)間不足而難以獲得均勻且厚度充分的氧化皮層。因此,可以確認(rèn),為了獲得均勻且厚度厚的氧化皮層,需要用于板坯和空氣反應(yīng)的充分的噴射時(shí)間。但是,當(dāng)冷卻水的噴射時(shí)間超過一定時(shí)間以上時(shí),鑄坯會(huì)停滯,從而存在降低生成量的擔(dān)憂。此外,如比較材料8及比較材料9,在鑄坯的表面溫度為932℃、1062℃時(shí)噴射冷卻水時(shí),氧化皮的厚度為15μm、26μm,顯示出了不均勻的氧化皮。但是,可以預(yù)測(cè)出鑄坯的溫度越高,會(huì)越促進(jìn)氧化皮的生成,從而能夠獲得均勻的氧化皮。此外,可以預(yù)測(cè)在連鑄的鑄坯中的鑄坯溫度越高,能夠獲得均勻的氧化皮。如上所述,在連鑄工序結(jié)束后,在冷卻噴射工序中,在最佳的噴射位置上噴射最佳的冷卻水及空氣的比和最佳的冷卻水水量,能夠優(yōu)化氧化皮的形成,并且能夠提高表面品質(zhì),可以最小化用在去除缺陷的工序等中的費(fèi)用,從而可以提高附加價(jià)值。然后,對(duì)使用薄帶連鑄方式制造經(jīng)濟(jì)型雙相不銹鋼的方法進(jìn)行說明。圖5為概略地示出根據(jù)本發(fā)明一實(shí)施例的經(jīng)濟(jì)型雙相不銹鋼的薄帶連鑄方式制造工序的圖,圖6為示出形成在本發(fā)明的鑄輥上的氮排出通道的模式圖。根據(jù)本發(fā)明一實(shí)施例的經(jīng)濟(jì)型雙相不銹鋼在依次配置有鋼包(210)、中間包(220)、一對(duì)鑄輥(230)、內(nèi)聯(lián)輥(260)、收卷輥(270)的常規(guī)連鑄設(shè)備(200)中制造。但是,在鑄輥(230)的表面形成有氣體排出通道(231)。為了通過薄帶連鑄方式制造經(jīng)濟(jì)型雙相不銹鋼,首先準(zhǔn)備具有上述公開的合金成分的鋼水(m),使其移動(dòng)到鋼包(210)后,利用套管噴嘴(shroudingnozzle)(211)臨時(shí)儲(chǔ)存到中間包(220)中。然后,通過注入噴嘴(221)使其通過一對(duì)鑄輥(230)之間的同時(shí)凝固,從而制成帶鋼(s),制得的帶鋼(s)在鑄輥(230)和連續(xù)配置的內(nèi)聯(lián)輥(260)中被軋制,從而收卷到收卷輥(270)上。另外,鑄輥(230)上部安裝有歧管防護(hù)罩(manifoldshield)(250),以能夠防止熔融金屬表面與空氣接觸而被氧化,這種歧管防護(hù)罩(250)內(nèi)部注入了適當(dāng)?shù)臍怏w,從而形成合適的防止氧化的氛圍。如上所述,鋼水(m)從一對(duì)鑄輥(230)相遇的輥距中脫離出來,經(jīng)過內(nèi)聯(lián)輥(260)被軋制后,經(jīng)過熱處理過程及冷間軋制等工序來制成10mm以下的帶鋼(s)。如上所述的直接制造10mm以下的帶鋼(s)的雙輥式帶鋼連鑄機(jī)中最為重要的技術(shù)要素之一為,通過注入噴嘴(250)快速地向相反方的向旋轉(zhuǎn)的內(nèi)部水冷式鑄輥(twin-drumrolls)(230)和側(cè)封板(240)(sidedam)之間供給鋼水(m),從而通過被水冷的鑄輥(230)的表面釋放大量的熱量,從而使鋼水急速冷卻,不產(chǎn)生裂紋地制成具有所需厚度的薄板,以提高實(shí)際產(chǎn)率。本發(fā)明的高延展性經(jīng)濟(jì)型雙相不銹鋼制造方法中,解決了成為邊緣(edge)裂紋及表面裂紋原因的包含在鋼水中的固溶限度以上的氮的問題,及因含氮而引起的熱加工性降低的問題。即,通過鑄輥(230)凝固鋼水(m)時(shí),排出固溶限度以上的氮的同時(shí)完成急速鑄造,在鑄造后利用連續(xù)進(jìn)行的內(nèi)聯(lián)輥(260)來完成了急速鑄造,從而制造約為2~5mm的薄的帶鋼(s),由此解決了上述問題。在薄帶連鑄過程中,為了去除包含在鋼水(m)中的固溶限度以上的氮,可以提供多種方法,在本發(fā)明的高延展性經(jīng)濟(jì)型雙相不銹鋼的制造方法中,作為其中的一例,通過在鑄輥(230)表面形成氮排出通道(231),從而在凝固鋼水時(shí)排出了固溶限度以上的氮。根據(jù)氮的內(nèi)部氣孔問題,大部分是在鋼水通過一對(duì)鑄輥(230)之間并急速被冷卻的過程中產(chǎn)生。因此,鋼水(m)中的固溶限度以上的氮,需要在使鋼水(m)通過鑄輥(230)的同時(shí)進(jìn)行。為此,為了在鑄造中使能夠排出氮,優(yōu)選在鑄輥(230)的表面形成氣體排出通道(231)。氣體排出通道(231)為不能通過鋼水(m)僅能夠排出氮?dú)獬潭鹊奈⒓?xì)的通道。這種氣體排出通道(231)可以以多種方式形成在鑄輥(230)上,在鑄輥(230)的表面沿圓周方向形成,從而隨著鑄輥(230)的旋轉(zhuǎn),能夠向鑄輥(230)的外側(cè)方向引導(dǎo)并排出氮?dú)?。氣體排出通道(231)相當(dāng)于寬度為50~500μm深度為50~300μm的微細(xì)通道,在鑄輥(230)的圓周方向上形成有多個(gè),且相鄰的氣體排出通道(231)之間的間距優(yōu)選以100~1000μm左右形成。氣體排出通道(231)的形狀、結(jié)構(gòu)及其使用位置只要是能夠?qū)崿F(xiàn)其功能,則可以進(jìn)行多種變形。另外,形成多個(gè)這種氣體排出通道(231)時(shí),會(huì)減少鑄輥(230)和通過該鑄輥(230)的鋼水(m)之間的接觸面積,為了防止該現(xiàn)象,優(yōu)選在鑄輥表面突出地形成凹凸。這種凹凸具有15~25μm的平均尺寸。下面,為了確認(rèn)鋼水中的固溶限度以上的氮對(duì)薄板產(chǎn)生的影響,如下述[表6],變更鋼水的組成及鑄造法來制造經(jīng)濟(jì)型雙相鋼。此時(shí),比較例1為利用普通的連續(xù)鑄造法對(duì)具有特定組成的鋼水進(jìn)行鑄造的,比較例2為利用普通的薄帶連鑄方式(急速鑄造)對(duì)具有特定組成的鋼水進(jìn)行鑄造的,實(shí)施例1~實(shí)施例5為根據(jù)本發(fā)明,利用鑄輥將鋼水中的固溶限度以上的氮?dú)膺M(jìn)行排出,并通過薄帶連鑄方式鑄造的。表6如[表6]所示,可以確認(rèn)比較例1在連續(xù)鑄造工序中未排出氮,從而在鑄坯內(nèi)部產(chǎn)生了氣孔。此外,可以確認(rèn)比較例2在普通方式的薄帶連鑄工序中未排出氮,從而在帶鋼內(nèi)部產(chǎn)生了氣孔。其原因在于,鋼水在通過鑄膜或鑄輥并進(jìn)行凝固而產(chǎn)生的氮溶解度的差異所致。本發(fā)明的高延展性經(jīng)濟(jì)型雙相不銹鋼的氮組成在1500~3200ppm范圍。另外,鋼水從液相凝固成固相的過程以液相→液相+δ相(deltaphase)→δ相→δ相+奧氏體相的順序進(jìn)行,液相變?yōu)棣南鄷r(shí),氮固溶度約為1164ppm,產(chǎn)生約836~1836ppm的固溶度差異。因此,在液相中過飽和的氮中的一部分凝固時(shí),顯然被氣(gas)化而凝固的材料的內(nèi)部形成多種氣孔,并且在材料表面形成的凝固殼中也形成多數(shù)氣孔。如此,實(shí)際凝固的材料的內(nèi)部存在大量的氣孔,這些氣孔的一部分也會(huì)在熱軋時(shí)被壓縮,而未被壓縮的氣孔會(huì)成為內(nèi)部缺陷,在利用加熱爐進(jìn)行加熱時(shí),向外部露出時(shí)會(huì)發(fā)展成多種表面缺陷。另一方面,實(shí)施例1~實(shí)施例5為利用本發(fā)明的薄帶連鑄工序的實(shí)施例,在工序中可以確認(rèn)因排出了氮,從而在帶鋼內(nèi)部沒有產(chǎn)生氣孔。參照附圖和前述的優(yōu)選實(shí)施例對(duì)本發(fā)明進(jìn)行了說明,但本發(fā)明并不限定于此,而是由權(quán)利要求書范圍所限定。因此,本領(lǐng)域技術(shù)人員在不脫離本發(fā)明的權(quán)利要求書的范圍的技術(shù)思想的范圍內(nèi),可以對(duì)本發(fā)明進(jìn)行多種變形及修改。附圖標(biāo)記說明100:連鑄設(shè)備110:鋼包120:中間包130:鑄膜140:扇形體150:噴射手段200:薄帶連鑄設(shè)備210:鋼包220:中間包230:鑄輥260:內(nèi)聯(lián)輥270:收卷輥當(dāng)前第1頁12