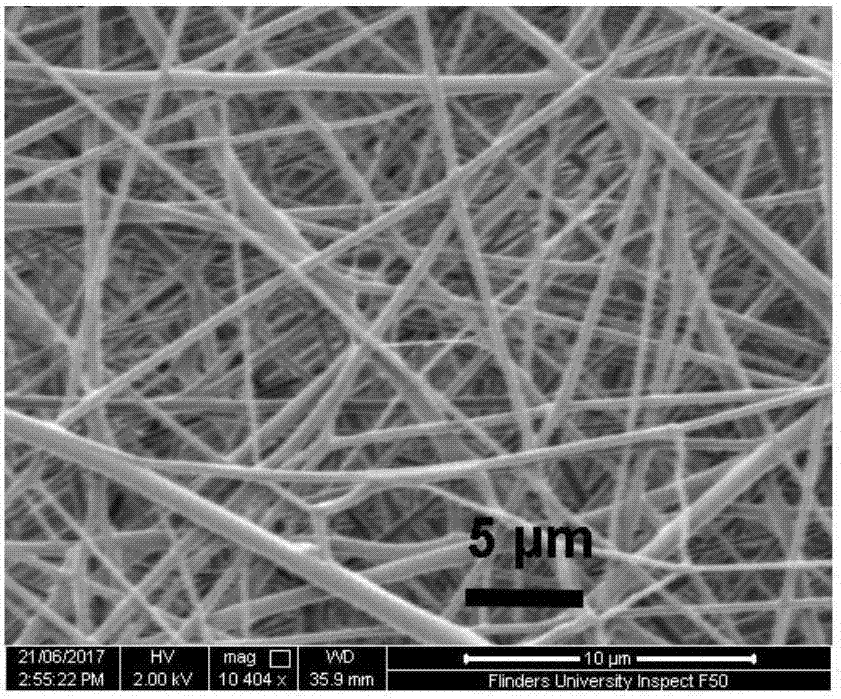
本發(fā)明涉及一種薄膜纖維的制備方法,具體涉及一種聚苯乙烯-聚多巴氨復(fù)合薄膜纖維的制備方法。
背景技術(shù):
:科技是一把雙刃劍,20世紀以來科學(xué)技術(shù)迅猛發(fā)展,促進了經(jīng)濟的發(fā)展,提高了人民的生活水平,然而,與此同時,人類也付出了慘重的代價。由于工業(yè)“三廢”機動車尾氣的排放、污水灌溉和農(nóng)藥、除草劑、化肥等的使用以及礦業(yè)的發(fā)展,嚴重地污染了土壤、水質(zhì)和大氣。其中重金屬和油品對環(huán)境的污染尤為嚴重。重金屬離子主要來源有礦冶行業(yè)、機械加工、電鍍行業(yè)、廢舊電池垃圾等,這些行業(yè)產(chǎn)生的廢水很多都被直接排放或簡單處理后直接排放到附近的河流、湖泊中。對自然環(huán)境和水源都是極大的威脅,嚴重危害了人類及各類生物的生存。重金屬污染對人類生存環(huán)境的威脅已經(jīng)引起各國政府及科學(xué)界的廣泛關(guān)注,重金屬廢水處理技術(shù)得到了快速發(fā)展。處理重金屬廢水的方法多樣,大體可以歸納為:膜處理法、離子交換法和吸附法。前兩種方法由于處理效果不理想、費用昂貴等原因,在實際應(yīng)用中受到很大的限制。相對于前兩種的諸多弊端,吸附法憑其對低濃度的重金屬廢水良好的處理效果、費用低廉、廢料易處理等特點,成為重金屬廢水處理研究的熱點。在石油開采、運輸、加工和使用過程中,通常會面臨由于石油泄漏造成的水體污染問題,不僅是資源的嚴重浪費,還破壞了人類生活環(huán)境,威脅了生態(tài)環(huán)境平衡。目前處理溢油的方法,主要有物理法、化學(xué)法和生物法。在物理法中,采用吸附劑處理是最經(jīng)濟有效的方法。人們發(fā)現(xiàn)直徑在亞微米或納米級的聚合物超細纖維具有獨特的性能,比如大的比表面積、超強的力學(xué)性能等,在重金屬吸附處理和油品吸附處理領(lǐng)域具有廣闊的應(yīng)用前景。靜電紡絲技術(shù)作為制備聚合物超細纖維的一種簡單易行的方法,近年來發(fā)展迅速。本發(fā)明提供一種通過靜電紡絲法制備聚苯乙烯-聚多巴氨復(fù)合薄膜纖維的方法,通過聚苯乙烯與聚多巴氨的復(fù)合,并通過靜電紡絲得到的薄膜纖維具有比表面積大、孔隙小、且孔隙率高等優(yōu)點,對重金屬廢水和油品吸附處理方面取得了有益的技術(shù)效果,具有較大的實用價值。技術(shù)實現(xiàn)要素:本發(fā)明的一個目的是解決至少上述問題和/或缺陷,并提供至少后面將說明的優(yōu)點。為了實現(xiàn)根據(jù)本發(fā)明的這些目的和其它優(yōu)點,提供了一種聚苯乙烯-聚多巴氨復(fù)合薄膜纖維的制備方法,包括以下步驟:步驟一、將濃度為12~17wt%的聚苯乙烯溶液和濃度為20~40mg/ml的多巴胺溶液攪拌混合,超聲,得到混合溶液;所述聚苯乙烯溶液與多巴胺溶液的體積比為5~20:1;步驟二、將混合溶液進行靜電紡絲,接收板上包覆鋁箔,得到聚苯乙烯-多巴氨復(fù)合薄膜纖維;步驟三、將得到的聚苯乙烯-多巴氨復(fù)合薄膜纖維加入ph為8~8.5的0.05~0.08mol/l的三羥甲基氨基甲烷溶液中,密封反應(yīng),取出后用蒸餾水洗滌至ph值為中性,干燥,得到聚苯乙烯-聚多巴氨復(fù)合薄膜纖維。優(yōu)選的是,所述聚苯乙烯溶液和多巴胺溶液的溶劑均為n,n-二甲基甲酰胺。優(yōu)選的是,所述靜電紡絲采用的參數(shù)為:環(huán)境溫度為40~60℃、高壓電源的輸出電壓為10~20kv、接收板與噴絲口之間距離為10~15cm、流速為0.5~2.5ml/h,噴絲口的內(nèi)徑為0.5~1.2mm。優(yōu)選的是,還包括,將混合溶液加入不銹鋼球形容器中,同時加入分散劑和助溶劑,將球形容器置于四軸研磨儀上,開啟四軸研磨儀,帶動不銹鋼球形容器無規(guī)旋轉(zhuǎn)60~90min;所述不銹鋼球形容器的進料口通過螺紋蓋密封,螺紋蓋密封連接后與不銹鋼球形容器的表面齊平;所述分散劑占聚苯乙烯重量的0.5~1.5%;所述助溶劑占聚苯乙烯重量的0.5~1.5%;所述混合溶液占不銹鋼球形容器容積的2/3。優(yōu)選的是,所述分散劑為1,3-二甲基咪唑四氟硼酸鹽、1-乙基-3-甲基咪唑六氟磷酸鹽、1-乙基-3-甲基咪唑高氯酸鹽、1-乙基-3-甲基咪唑乳酸、三乙基己基磷酸、十二烷基硫酸鈉、甲基戊醇中的一種或幾種。優(yōu)選的是,所述助溶劑為烷基酚聚氧乙烯醚、聚氧乙烯酰胺、聚乙二醇、水楊酸鈉、聚氧乙烯、聚乙烯吡咯烷酮、聚ε-己內(nèi)酯、聚芐基谷氨酸中的一種或幾種。優(yōu)選的是,所述四軸研磨儀的主動軸轉(zhuǎn)速為100~150rpm,隨機轉(zhuǎn)變頻率為30~60s。優(yōu)選的是,所述超聲的頻率為30~45khz,超聲波功率密度為500~1000w/l,超聲波采用間歇輻照,間歇輻照時的間歇時間為15~20s/5~10s。優(yōu)選的是,所述步驟三中,將得到的聚苯乙烯-多巴氨復(fù)合薄膜纖維加入ph為8~8.5的0.05~0.08mol/l的三羥甲基氨基甲烷溶液中,然后置于密封容器中,將該密封容器置于2.5mev、40ma的電子加速器中進行輻照攪拌處理,輻照劑量率為100~200kgy/h,輻照劑量為100~800kgy。優(yōu)選的是,所述干燥采用微波輻射干燥,其過程為:將洗滌后的薄膜纖維放入石英干燥器中,然后置于微波輻射反應(yīng)爐內(nèi);以50~100ml/min的速度通入氮氣,對沉淀進行微波輻射干燥處理;所述微波輻射干燥處理的條件為:微波輻射頻率為2450±50mhz,微波輻射單位功率為0.10~1.00w/g,微波輻射時間為30~60min,微波輻射溫度為50~60℃。本發(fā)明至少包括以下有益效果:本發(fā)明采用廉價的聚苯乙烯為原料,通過靜電紡絲法制備聚苯乙烯-聚多巴氨復(fù)合薄膜纖維吸附材料,其拉伸強度高于單純的聚苯乙烯纖維,力學(xué)性能優(yōu)異。本發(fā)明的吸附材料具有比表面積大、孔隙小、且孔隙率高等優(yōu)點,并對重金屬和油吸附效果好、選擇性高;本發(fā)明制備得到的聚苯乙烯-聚多巴氨復(fù)合薄膜纖維吸附材料,可以廣泛應(yīng)用于重金屬廢水、海洋溢油處理、工業(yè)污水凈化、食品廢油處理等方面,分離速度快,吸附效率高。本發(fā)明實驗方案可行性高,原材料來源豐富,操作工藝簡單,資金投入少,制備周期短,反應(yīng)條件溫和,不需要大型儀器設(shè)備,可以實現(xiàn)大規(guī)模的工業(yè)化生產(chǎn)加工,具有很廣泛的應(yīng)用前景。本發(fā)明的其它優(yōu)點、目標和特征將部分通過下面的說明體現(xiàn),部分還將通過對本發(fā)明的研究和實踐而為本領(lǐng)域的技術(shù)人員所理解。附圖說明:圖1為本發(fā)明實施例3制備的聚苯乙烯-聚多巴氨復(fù)合薄膜纖維的sem圖;圖2為本發(fā)明實施例3制備的聚苯乙烯-聚多巴氨復(fù)合薄膜纖維的sem圖;圖3為本發(fā)明實施例3制備的聚苯乙烯-聚多巴氨復(fù)合薄膜纖維的sem圖。具體實施方式:下面結(jié)合附圖對本發(fā)明做進一步的詳細說明,以令本領(lǐng)域技術(shù)人員參照說明書文字能夠據(jù)以實施。應(yīng)當理解,本文所使用的諸如“具有”、“包含”以及“包括”術(shù)語并不配出一個或多個其它元件或其組合的存在或添加。實施例1:一種聚苯乙烯-聚多巴氨復(fù)合薄膜纖維的制備方法,包括以下步驟:步驟一、將濃度為12wt%的聚苯乙烯溶液和濃度為20mg/ml的多巴胺溶液攪拌混合,超聲,得到混合溶液;所述聚苯乙烯溶液與多巴胺溶液的體積比為5:1;所述聚苯乙烯溶液和多巴胺溶液的溶劑均為n,n-二甲基甲酰胺;所述超聲的頻率為30khz,超聲波功率密度為500w/l,超聲波采用間歇輻照,間歇輻照時的間歇時間為15s/5s(輻照時間/間歇時間);步驟二、將混合溶液進行靜電紡絲,接收板上包覆鋁箔,得到聚苯乙烯-多巴氨復(fù)合薄膜纖維;所述靜電紡絲采用的參數(shù)為:環(huán)境溫度為40℃、高壓電源的輸出電壓為10kv、接收板與噴絲口之間距離為10cm、流速為0.5ml/h,噴絲口的內(nèi)徑為0.5mm;步驟三、將得到的聚苯乙烯-多巴氨復(fù)合薄膜纖維加入ph為8的0.05mol/l的三羥甲基氨基甲烷溶液中,密封反應(yīng),取出后用蒸餾水洗滌至ph值為中性,干燥,得到聚苯乙烯-聚多巴氨復(fù)合薄膜纖維。實施例2:一種聚苯乙烯-聚多巴氨復(fù)合薄膜纖維的制備方法,包括以下步驟:步驟一、將濃度為17wt%的聚苯乙烯溶液和濃度為40mg/ml的多巴胺溶液攪拌混合,超聲,得到混合溶液;所述聚苯乙烯溶液與多巴胺溶液的體積比為20:1;所述聚苯乙烯溶液和多巴胺溶液的溶劑均為n,n-二甲基甲酰胺;所述超聲的頻率為45khz,超聲波功率密度為1000w/l,超聲波采用間歇輻照,間歇輻照時的間歇時間為20s/10s(輻照時間/間歇時間);步驟二、將混合溶液進行靜電紡絲,接收板上包覆鋁箔,得到聚苯乙烯-多巴氨復(fù)合薄膜纖維;所述靜電紡絲采用的參數(shù)為:環(huán)境溫度為60℃、高壓電源的輸出電壓為20kv、接收板與噴絲口之間距離為15cm、流速為2.5ml/h,噴絲口的內(nèi)徑為1.2mm;步驟三、將得到的聚苯乙烯-多巴氨復(fù)合薄膜纖維加入ph為8.5的0.08mol/l的三羥甲基氨基甲烷溶液中,密封反應(yīng),取出后用蒸餾水洗滌至ph值為中性,干燥,得到聚苯乙烯-聚多巴氨復(fù)合薄膜纖維。實施例3:一種聚苯乙烯-聚多巴氨復(fù)合薄膜纖維的制備方法,包括以下步驟:步驟一、將濃度為15wt%的聚苯乙烯溶液和濃度為30mg/ml的多巴胺溶液攪拌混合,超聲,得到混合溶液;所述聚苯乙烯溶液與多巴胺溶液的體積比為12:1;所述聚苯乙烯溶液和多巴胺溶液的溶劑均為n,n-二甲基甲酰胺;所述超聲的頻率為40khz,超聲波功率密度為800w/l,超聲波采用間歇輻照,間歇輻照時的間歇時間為15s/10s(輻照時間/間歇時間);步驟二、將混合溶液進行靜電紡絲,接收板上包覆鋁箔,得到聚苯乙烯-多巴氨復(fù)合薄膜纖維;所述靜電紡絲采用的參數(shù)為:環(huán)境溫度為50℃、高壓電源的輸出電壓為15kv、接收板與噴絲口之間距離為12cm、流速為2ml/h,噴絲口的內(nèi)徑為1mm;步驟三、將得到的聚苯乙烯-多巴氨復(fù)合薄膜纖維加入ph為8.5的0.06mol/l的三羥甲基氨基甲烷溶液中,密封反應(yīng),取出后用蒸餾水洗滌至ph值為中性,干燥,得到聚苯乙烯-聚多巴氨復(fù)合薄膜纖維;圖1~3示出了不同放大倍率下聚苯乙烯-聚多巴氨復(fù)合薄膜纖維的sem圖。實施例4:還包括,將混合溶液加入不銹鋼球形容器中,同時加入分散劑和助溶劑,將球形容器置于四軸研磨儀上,開啟四軸研磨儀,帶動不銹鋼球形容器無規(guī)旋轉(zhuǎn)60min;所述不銹鋼球形容器的進料口通過螺紋蓋密封,螺紋蓋密封連接后與不銹鋼球形容器的表面齊平;所述分散劑占聚苯乙烯重量的0.5%;所述助溶劑占聚苯乙烯重量的0.5%;所述混合溶液占不銹鋼球形容器容積的2/3;所述分散劑為1,3-二甲基咪唑四氟硼酸鹽;所述助溶劑為烷基酚聚氧乙烯醚;所述四軸研磨儀的主動軸轉(zhuǎn)速為100rpm,隨機轉(zhuǎn)變頻率為60s。其余工藝過程和參數(shù)與實施例3中的完全相同。實施例5:還包括,將混合溶液加入不銹鋼球形容器中,同時加入分散劑和助溶劑,將球形容器置于四軸研磨儀上,開啟四軸研磨儀,帶動不銹鋼球形容器無規(guī)旋轉(zhuǎn)90min;所述不銹鋼球形容器的進料口通過螺紋蓋密封,螺紋蓋密封連接后與不銹鋼球形容器的表面齊平;所述分散劑占聚苯乙烯重量的1%;所述助溶劑占聚苯乙烯重量的1%;所述混合溶液占不銹鋼球形容器容積的2/3;所述分散劑為重量比為1:2的1,3-二甲基咪唑四氟硼酸鹽和甲基戊醇;所述助溶劑為重量比為1:2的烷基酚聚氧乙烯醚和聚乙烯吡咯烷酮;所述四軸研磨儀的主動軸轉(zhuǎn)速為100rpm,隨機轉(zhuǎn)變頻率為60s。其余工藝過程和參數(shù)與實施例3中的完全相同。實施例6:還包括,將混合溶液加入不銹鋼球形容器中,同時加入分散劑和助溶劑,將球形容器置于四軸研磨儀上,開啟四軸研磨儀,帶動不銹鋼球形容器無規(guī)旋轉(zhuǎn)75min;所述不銹鋼球形容器的進料口通過螺紋蓋密封,螺紋蓋密封連接后與不銹鋼球形容器的表面齊平;所述分散劑占聚苯乙烯重量的1.5%;所述助溶劑占聚苯乙烯重量的1.5%;所述混合溶液占不銹鋼球形容器容積的2/3;所述分散劑為重量比為1:1的1-乙基-3-甲基咪唑乳酸和十二烷基硫酸鈉;所述助溶劑為重量比為1:2的聚芐基谷氨酸和聚氧乙烯酰胺;所述四軸研磨儀的主動軸轉(zhuǎn)速為120rpm,隨機轉(zhuǎn)變頻率為45s。其余工藝過程和參數(shù)與實施例3中的完全相同。實施例7:所述步驟三中,將得到的聚苯乙烯-多巴氨復(fù)合薄膜纖維加入ph為8.5的0.06mol/l的三羥甲基氨基甲烷溶液中,然后置于密封容器中,將該密封容器置于2.5mev、40ma的電子加速器中進行輻照攪拌處理,輻照劑量率為100kgy/h,輻照劑量為100kgy。其余工藝過程和參數(shù)與實施例3中的完全相同。實施例8:所述步驟三中,將得到的聚苯乙烯-多巴氨復(fù)合薄膜纖維加入ph為8.5的0.06mol/l的三羥甲基氨基甲烷溶液中,然后置于密封容器中,將該密封容器置于2.5mev、40ma的電子加速器中進行輻照攪拌處理,輻照劑量率為200kgy/h,輻照劑量為800kgy。其余工藝過程和參數(shù)與實施例3中的完全相同。實施例9:所述步驟三中,將得到的聚苯乙烯-多巴氨復(fù)合薄膜纖維加入ph為8.5的0.06mol/l的三羥甲基氨基甲烷溶液中,然后置于密封容器中,將該密封容器置于2.5mev、40ma的電子加速器中進行輻照攪拌處理,輻照劑量率為150kgy/h,輻照劑量為750kgy。其余工藝過程和參數(shù)與實施例3中的完全相同。實施例10:所述干燥采用微波輻射干燥,其過程為:將洗滌后的薄膜纖維放入石英干燥器中,然后置于微波輻射反應(yīng)爐內(nèi);以50ml/min的速度通入氮氣,對沉淀進行微波輻射干燥處理;所述微波輻射干燥處理的條件為:微波輻射頻率為2450±50mhz,微波輻射單位功率為0.10w/g,微波輻射時間為30min,微波輻射溫度為50℃。其余工藝過程和參數(shù)與實施例3中的完全相同。實施例11:所述干燥采用微波輻射干燥,其過程為:將洗滌后的薄膜纖維放入石英干燥器中,然后置于微波輻射反應(yīng)爐內(nèi);以100ml/min的速度通入氮氣,對沉淀進行微波輻射干燥處理;所述微波輻射干燥處理的條件為:微波輻射頻率為2450±50mhz,微波輻射單位功率為1w/g,微波輻射時間為60min,微波輻射溫度為60℃。其余工藝過程和參數(shù)與實施例3中的完全相同。實施例12:所述干燥采用微波輻射干燥,其過程為:將洗滌后的薄膜纖維放入石英干燥器中,然后置于微波輻射反應(yīng)爐內(nèi);以80ml/min的速度通入氮氣,對沉淀進行微波輻射干燥處理;所述微波輻射干燥處理的條件為:微波輻射頻率為2450±50mhz,微波輻射單位功率為0.5w/g,微波輻射時間為45min,微波輻射溫度為55℃。其余工藝過程和參數(shù)與實施例3中的完全相同。實施例13:還包括,將混合溶液加入不銹鋼球形容器中,同時加入分散劑和助溶劑,將球形容器置于四軸研磨儀上,開啟四軸研磨儀,帶動不銹鋼球形容器無規(guī)旋轉(zhuǎn)75min;所述不銹鋼球形容器的進料口通過螺紋蓋密封,螺紋蓋密封連接后與不銹鋼球形容器的表面齊平;所述分散劑占聚苯乙烯重量的1.5%;所述助溶劑占聚苯乙烯重量的1.5%;所述混合溶液占不銹鋼球形容器容積的2/3;所述分散劑為重量比為1:1的1-乙基-3-甲基咪唑乳酸和十二烷基硫酸鈉;所述助溶劑為重量比為1:2的聚芐基谷氨酸和聚氧乙烯酰胺;所述四軸研磨儀的主動軸轉(zhuǎn)速為120rpm,隨機轉(zhuǎn)變頻率為45s。其余工藝過程和參數(shù)與實施例9中的完全相同。實施例14:還包括,將混合溶液加入不銹鋼球形容器中,同時加入分散劑和助溶劑,將球形容器置于四軸研磨儀上,開啟四軸研磨儀,帶動不銹鋼球形容器無規(guī)旋轉(zhuǎn)75min;所述不銹鋼球形容器的進料口通過螺紋蓋密封,螺紋蓋密封連接后與不銹鋼球形容器的表面齊平;所述分散劑占聚苯乙烯重量的1.5%;所述助溶劑占聚苯乙烯重量的1.5%;所述混合溶液占不銹鋼球形容器容積的2/3;所述分散劑為重量比為1:1的1-乙基-3-甲基咪唑乳酸和十二烷基硫酸鈉;所述助溶劑為重量比為1:2的聚芐基谷氨酸和聚氧乙烯酰胺;所述四軸研磨儀的主動軸轉(zhuǎn)速為120rpm,隨機轉(zhuǎn)變頻率為45s。其余工藝過程和參數(shù)與實施例12中的完全相同。實施例15:所述干燥采用微波輻射干燥,其過程為:將洗滌后的薄膜纖維放入石英干燥器中,然后置于微波輻射反應(yīng)爐內(nèi);以80ml/min的速度通入氮氣,對沉淀進行微波輻射干燥處理;所述微波輻射干燥處理的條件為:微波輻射頻率為2450±50mhz,微波輻射單位功率為0.5w/g,微波輻射時間為45min,微波輻射溫度為55℃。其余工藝過程和參數(shù)與實施例9中的完全相同。實施例16:所述干燥采用微波輻射干燥,其過程為:將洗滌后的薄膜纖維放入石英干燥器中,然后置于微波輻射反應(yīng)爐內(nèi);以80ml/min的速度通入氮氣,對沉淀進行微波輻射干燥處理;所述微波輻射干燥處理的條件為:微波輻射頻率為2450±50mhz,微波輻射單位功率為0.5w/g,微波輻射時間為45min,微波輻射溫度為55℃。其余工藝過程和參數(shù)與實施例13中的完全相同。為了說明本發(fā)明的效果,發(fā)明人提供比較實驗如下:比較例1(b1):將濃度為15wt%的聚苯乙烯溶液,超聲;所述聚苯乙烯溶液的溶劑均為n,n-二甲基甲酰胺;所述超聲的頻率為40khz,超聲波功率密度為800w/l,超聲波采用間歇輻照,間歇輻照時的間歇時間為15s/10s(輻照時間/間歇時間);步驟二、將聚苯乙烯溶液進行靜電紡絲,接收板上包覆鋁箔,得到聚苯乙烯薄膜纖維;所述靜電紡絲采用的參數(shù)為:環(huán)境溫度為50℃、高壓電源的輸出電壓為15kv、接收板與噴絲口之間距離為12cm、流速為2ml/h,噴絲口的內(nèi)徑為1mm。比較例2(b2):采用濃度為15mg/ml的多巴胺溶液,其余工藝過程和參數(shù)與實施例3中的完全相同。比較例3(b3):采用濃度為45mg/ml的多巴胺溶液,其余工藝過程和參數(shù)與實施例3中的完全相同。采用以上實施例1~16和對比例1~3制備的薄膜纖維進行力學(xué)性能測試。拉伸強度結(jié)果如表1所示;表1采用以上實施例1~16和對比例1~3制備的薄膜纖維對重金屬銅離子進行靜態(tài)吸附研究。分別取上述實施例1~16和對比例1~3制備的聚苯乙烯-聚多巴氨復(fù)合薄膜纖維20mg與100ml40mg/l的銅離子溶液混合,調(diào)節(jié)ph為4,置于搖床振蕩2h,轉(zhuǎn)速為130rpm,吸附溫度為25℃,其吸附效果如表2所示,重金屬銅離子的去除率由以下公式(1)計算,去除率=(co-ce)/co×100%其中,co為吸附前重金屬離子的濃度,ce為吸附后重金屬離子的濃度。表2實施例12345678910去除率%94.894.795.197.597.497..797.997.898.196.8實施例111213141516b1b2b3去除率%96.696.999.1.98.998.899.685.690.390.5從表1可知,實施例1~16為采用本發(fā)明中原料的比例范圍制備得到的聚苯乙烯-聚多巴氨復(fù)合薄膜纖維對重金屬銅離子溶液的吸附效果,去除率均大于94%,而比較例中所采用的原料及其比例不在本發(fā)明所述的比例范圍之內(nèi),得到重金屬銅離子的去除率低于91%。可見,本發(fā)明中采用的原料按所述比例,并且在聚苯乙烯-聚多巴氨復(fù)合薄膜纖維的制備工藝過程中,各個原料及參數(shù)在所述的范圍內(nèi),制備的復(fù)合薄膜纖維對重金屬銅離子的吸附性能較好。盡管本發(fā)明的實施方案已公開如上,但其并不僅僅限于說明書和實施方式中所列運用,它完全可以被適用于各種適合本發(fā)明的領(lǐng)域,對于熟悉本領(lǐng)域的人員而言,可容易地實現(xiàn)另外的修改,因此在不背離權(quán)利要求及等同范圍所限定的一般概念下,本發(fā)明并不限于特定的細節(jié)和這里示出與描述的圖例。當前第1頁12