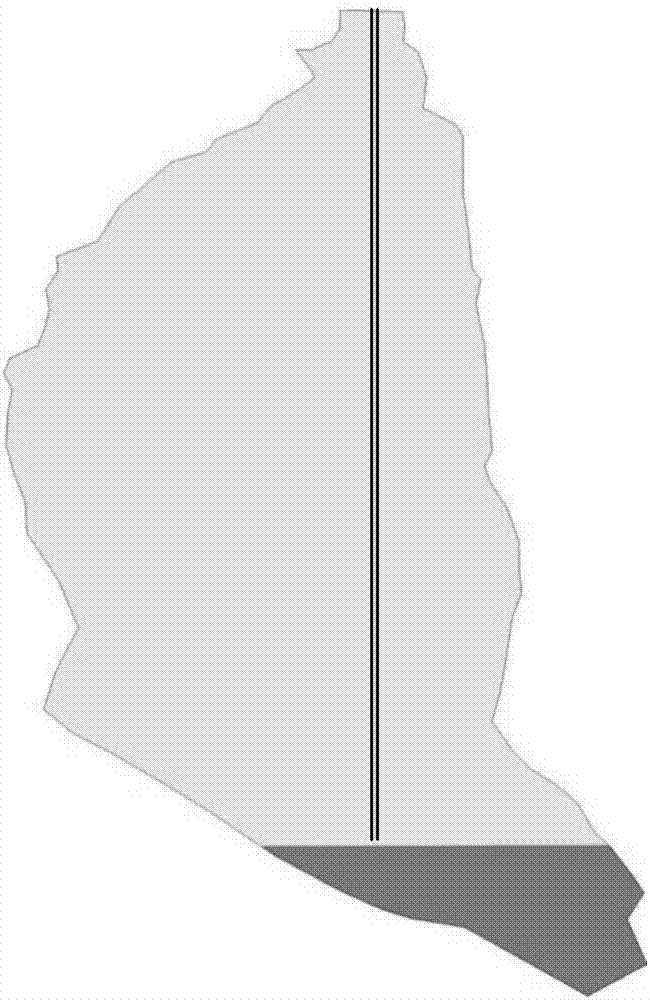
本發(fā)明屬于油氣儲運與資源開發(fā)領域,具體涉及一種連續(xù)油管管柱裝置,用于鹽穴儲氣庫底部鹵水的排出,以及利用該裝置在鹽穴地下儲氣庫排鹵擴容方法。
背景技術:
:在鹽穴儲氣庫建設過程中,鹽巖中的雜質和夾層等不溶于水的物質,不能在造腔過程中隨著鹵水被排出到腔體外,而是堆積在腔體底部。考慮到夾層具有較高的強度且其破壞模式復雜,破壞后形成的堆積體形狀差異較大;同時,堆積體中小不一的塊體相互疊壓和支撐,使得形成的堆積體中含有大量的孔隙,這些孔隙被鹵水充填。這些堆積物體積較大,一般可以占到腔體總體積20%-40%左右。注氣排鹵是指鹽穴地下儲氣庫單井在經(jīng)歷鉆井、溶腔形成后,在投入注采氣生產運行前,由干線來氣經(jīng)過站內壓縮機增壓,再經(jīng)過注氣管匯到注采氣井井口,到達井口的天然氣沿著井下注采管柱與排鹵管柱環(huán)空注入,鹽穴地下儲氣庫腔內的飽和鹵水從排鹵管柱排出。隨著天然氣源源不斷地注入、腔體內的飽和鹵水源源不斷地排出,最后達到儲存天然氣和調峰、應急采氣的目的。在國內外的鹽穴地下儲氣庫注氣排鹵過程中,都是通過下入排鹵管柱,利用注入天然氣和排出鹵水來完成整個注氣排鹵過程。排鹵管柱的下深,對于是否能夠充分進行注氣排鹵、最大程度利用已有溶腔腔體體積同時防止注氣排鹵過程中管柱堵塞有著至關重要的影響。當前的注氣排鹵工藝如附圖1所示,根據(jù)溶腔結束后的最后一次聲納測量數(shù)據(jù)和管柱探底數(shù)據(jù)、按照排鹵管柱距離腔底1.5-2.0米左右原則確定,排鹵完成后,排鹵管口以下的鹵水無法從腔體中排出。目前已有的注氣排鹵工藝無法對排鹵管口以下部分及沉渣空隙部位體積進行有效利用。排鹵管柱下入太深雖然能夠最大限度地利用已有溶腔腔體體積但容易導致注氣排鹵過程中管柱發(fā)生堵塞,下入太淺雖然能夠盡量避免注氣排鹵過程中管柱發(fā)生堵塞卻損失部分已有溶腔腔體體積。這就造成已有注氣排鹵方法存在以下2個方面的缺陷:(1)腔體內部鹵水不能全部排出,造成腔體有效體積浪費。由于鹽穴儲氣庫腔體底部直徑較大,以金壇鹽穴儲氣庫為例一般可以達到70m,這就意味著腔底無法排出的鹵水體積可以達到7000m3,而這部分體積無法進行天然氣存儲,如圖2所示。(2)無法對堆積物中的孔隙體積進行利用。由于排鹵管柱無法深入到堆積物內,無法將孔隙內的鹵水排出,從而形成儲氣空間。上述原因造成了鹽穴儲氣庫有效存儲體積的浪費,提高了單位有效溶腔體積的造腔費用,同時也降低了儲氣庫的調峰能力。技術實現(xiàn)要素:本發(fā)明的目的在于提供一種連續(xù)油管管柱裝置,該管柱可用于鹽穴儲氣庫底部鹵水的排出,可以沖洗管鞋周邊淤泥,防止管柱底部堵塞,一方面能確保管柱不被卡住,另一方面,可以增加排液深度,最大限度達到擴大腔容的目的。本發(fā)明的另一個目的在于提供一種在鹽穴地下儲氣庫排鹵擴容的方法,解決了當前注氣排鹵工藝存在的管柱堵塞與腔體體積損失之間的矛盾,排出常規(guī)注氣排鹵方法中無法排鹵腔體底部或低洼處的鹵水,最大程度地利用已有溶腔腔體體積。為了實現(xiàn)上述目的,本發(fā)明采用以下技術方案:一種連續(xù)油管管柱裝置,包括連續(xù)油管、油管外卡連接器、加重管、液壓安全接頭、旋轉沖洗工具,其結構示意圖如圖4所示,連續(xù)油管底端通過油管外卡連接器與加重管連接,加重管的另一端通過液壓安全接頭與旋轉沖洗工具連接。進一步地,所述的加重管的重量為500-800kg。進一步地,所述的連續(xù)油管外徑為50.8mm。在利用該裝置排鹵過程中,鹵水從旋轉沖洗工具外側進入連續(xù)油管中,排出鹵水。當排鹵過程中旋轉沖洗工具被外側腔底沉渣堵塞時,此時,在地面從連續(xù)油管中注入正沖洗清水,沖洗旋轉沖洗工具堵塞沉渣及外側沉渣,形成排鹵坑后繼續(xù)排鹵。一種鹽穴地下儲氣庫排鹵擴容的方法,其步驟是:1)采用常規(guī)注氣排鹵方法對溶腔進行排鹵作業(yè),根據(jù)聲納測試的腔體形狀數(shù)據(jù)和排鹵數(shù)據(jù),估算出鹽穴儲氣庫中腔體底部剩余鹵水量,確定利用連續(xù)油管管柱裝置的排鹵量;2)安裝連續(xù)油管作業(yè)機、地面配套設備及管線;3)安裝井口井控裝置與連續(xù)油管管柱裝置,進行井口井控裝置密封性測試;4)下連續(xù)油管管柱裝置至鹽穴地下儲氣庫腔底或低洼處,接近底部后反復探底1-3次,上提0-0.5米,從連續(xù)油管管柱裝置與注采管柱環(huán)空注天然氣,從連續(xù)油管管柱裝置排出鹵水,直至鹵水不再排出;5)將連續(xù)油管管柱裝置重新上提0-0.5米,通過地面注水設備從連續(xù)油管注入清水,對井底旋轉沖洗工具及外圍沉渣進行沖洗,結合步驟1)已有排鹵體積及已有聲納測量結果計算剩余未排出鹵水體積,根據(jù)剩余未排出鹵水體積并結合腔體形狀,繼續(xù)下放連續(xù)油管管柱裝置進行注氣排鹵至累計排鹵體積達到目標排鹵體積;6)排鹵結束,保持井內壓力,帶壓取出連續(xù)油管管柱裝置及排鹵工具。進一步地,所述的步驟6)中,在上提連續(xù)油管管柱裝置遇阻時,從連續(xù)油管內投球憋壓打掉液壓安全接頭及旋轉沖洗工具,起出上部連續(xù)油管。本發(fā)明提供的鹽穴地下儲氣庫排鹵擴容的方法是利用一種可以反復塑性變形、無螺紋接頭、單根長度可達萬米的連續(xù)油管,通過連續(xù)油管作業(yè)機將連續(xù)油管下入腔體底部或水平延伸至腔體形狀不規(guī)則的低洼處,然后從連續(xù)油管管柱裝置與注采管柱環(huán)空注入天然氣,繼續(xù)反復進行注氣排鹵,排出的鹵水通過連續(xù)油管返出地面,經(jīng)由地面輸鹵泵輸送至站內或者當?shù)佧}化企業(yè),達到擴容的目的,適用于所有鹽穴地下儲氣庫注氣排鹵的生產過程。與現(xiàn)有技術相比,本發(fā)明具有以下優(yōu)點及有益效果:(1)本發(fā)明采用連續(xù)油管作為排鹵管道,井口配套裝置不采用固定螺栓鎖死連續(xù)油管位置,能連續(xù)上提或下放油管,達到任意可排放鹵水的深度。而傳統(tǒng)排鹵油管,其安裝完成后底部排鹵管口深度完全固定,整個作業(yè)期間無法進行下放排鹵管口深度的調整。(2)基于第1條的優(yōu)點,連續(xù)油管排鹵管柱能下至腔體底部,并能夠深入腔底沉渣中進于排鹵,有效排鹵腔底底部及部分沉渣中鹵水,傳統(tǒng)排鹵油管不具有該項功能。(3)在接近底部沉渣部位發(fā)生沉渣堵塞時,利用旋轉沖洗工具能有效沖開堵塞的沉渣,重新形成排鹵通道,傳統(tǒng)排鹵油管不具有該項功能。(4)該連續(xù)油管能有效排出傳統(tǒng)排鹵管柱無法排鹵的腔底底部剩余約20%以內的殘余鹵水,有效增加腔體的儲氣體積,具有明顯的經(jīng)濟效益。附圖說明圖1為常規(guī)注氣排鹵示意圖圖2為鹽穴儲氣庫腔體形態(tài)及注氣排鹵后剩余鹵水示意圖圖3為本發(fā)明所述的連續(xù)油管裝置在鹽穴地下儲氣庫排鹵擴容的方法實施示意圖圖4為連續(xù)油管管柱裝置的結構示意圖圖5為連續(xù)油管外卡連接器結構示意圖圖6為液壓安全接頭圖7為連續(xù)油管旋轉沖洗工具結構示意圖圖8為井場平面布置圖其中,1-連續(xù)油管,2-油管外卡連接器,3-加重管,4-液壓安全接頭,5-旋轉沖洗工具。具體實施方式實施例1一種連續(xù)油管管柱裝置,包括連續(xù)油管1、油管外卡連接器2、加重管3、液壓安全接頭4、旋轉沖洗工具5、其結構示意圖如圖4所示,連續(xù)油管1的底端通過油管外卡連接器2與加重管3連接,加重管3的另一端通過液壓安全接頭4與旋轉沖洗工具5連接。連續(xù)油管采用外徑ф50.8mm,壁厚4.45mm,內徑41.9mm,鋼級ct-90,油管外卡連接器采用表1所示產品,如圖5所示。表1連續(xù)油管外卡連接器參數(shù)連續(xù)管尺寸工具外徑工具內徑數(shù)量底端連接扣型產地2.00"2-7/8"1.5"12-3/8"pac英國tdi加重管可使連續(xù)油管在鹽腔內保持垂直以減少深度誤差,通過計算和實驗,加重管重量優(yōu)選為500-800kg。液壓安全接頭如圖6所示,由于連續(xù)油管的外徑與旋轉沖洗工具外徑差距較大,排液后起管柱存在卡管柱風險,在旋轉沖洗工具上部接液壓安全接頭,卡管柱時可從連續(xù)油管內投球打壓,丟掉下部工具,起出連續(xù)油管。旋轉沖洗工具如圖7所示,該工具由中國石油集團渤海鉆探工程有限有公司井下技術服務分公司生產,產品型號bh-xzct-120。通過對該工具本體表面進行激光割縫,形成排鹵通道。該工具外徑120mm,底部有引鞋,防止排液過程中井底碎屑進入連續(xù)油管內,主要具有2個功能:①反氣舉排液:氣舉排鹵時工具保持暢通但旋轉部件不轉;②正循環(huán)旋轉沖洗:正打壓可旋轉沖洗,下至井底堆積物附近時可沖開一定體積的腔底沉積物,在腔底形成一定尺寸的坑,達到最佳排液深度。實施例2一種鹽穴地下儲氣庫排鹵擴容的方法,其步驟是:1.采用常規(guī)的注氣排鹵技術對鹽穴地下儲氣庫進行排鹵作業(yè),依據(jù)聲納測量和注氣排鹵結果,從已有的鹽穴地下儲氣庫注采氣井中篩選出擴容余地較大、擴容經(jīng)濟效益較好的注采氣井作為擴容目標井。選取金壇儲氣庫某四口已完成常規(guī)注氣排鹵腔體為例,常規(guī)注氣排鹵后腔體利用率有高有低,70%~97%;腔體積液量有多有少,7000~65000m3,若把腔體積液排出80%,則計算結果如下表。從表可以看出,可排出液量在5000~50000m3;腔體利用率將提高到95%以上。表1四口腔體注氣排鹵數(shù)據(jù)比對表根據(jù)篩選出的已有鹽穴地下儲氣庫注采氣井,以3#井為例,確定利用連續(xù)油管管柱裝置計劃排鹵量,估算可排出剩余鹵水20498m3的80%,約為16398m3。2.安裝連續(xù)油管作業(yè)機、地面配套設備及管線對已篩選出的擬擴容井井場條件進行現(xiàn)場勘察,確保井場場地及承載力滿足連續(xù)油管作業(yè)設備進場及安全施工的要求,根據(jù)勘察結果合理設置連續(xù)油管作業(yè)井場平面布置圖,如圖8所示。現(xiàn)場安裝連續(xù)油管作業(yè)機、儲液罐、分離器、地面泵以及地面管匯等設備,連接工作滾筒、自動關斷閥、油嘴管匯(地面注水泵)、分離器、儲液罐(燃燒池)、輸鹵泵、輸鹵管線,連接連續(xù)油管作業(yè)機液壓管線、插管、丈量油管校正計數(shù)器、防噴管,搭井口保護平臺。為防止作業(yè)過程中車輛磕碰或高空落物損傷原井采油樹,在井口四周加裝防護欄。施工期間將采油樹罩住,進行保護。3.安裝井口井控裝置與連續(xù)油管管柱裝置,進行井口井控裝置密封性測試(1)拆原井采氣樹帽及上法蘭,依次安裝變徑法蘭、閘門、連續(xù)油管防噴器組,安裝連續(xù)油管防噴管、防噴盒、注入頭,下連續(xù)油管至防噴器第一個半封閘板下,關閉防噴器,打開防噴盒,從連續(xù)油管工作滾筒試壓25兆帕,30分鐘防噴盒無滲漏、壓降不大于0.7兆帕為合格,試驗第二道半封閘板、剪切閘板至合格后,從防噴管和防噴器連接處拆開。(2)在連續(xù)油管的底端連接油管外卡連接器、加重管、液壓安全接頭,安裝拉盤,試驗拉力150kn,清水試壓25兆帕,30分鐘密封部位無滲漏、壓降不大于0.7兆帕為合格。卸掉拉盤,安裝旋轉沖洗工具,對接防噴器與防噴管。(3)用清水對變徑法蘭、閘門、防噴器組、防噴管、防噴盒、連續(xù)油管、工作滾筒管匯、油嘴管匯試壓21兆帕,30分鐘壓降不大于0.7兆帕為合格;用清水對分離器、分離器下游氣液管線試壓2.5兆帕,30分鐘壓降不大于0.7兆帕為合格;關閉總閘門,對變徑法蘭、防噴器組、防噴管、防噴盒、連續(xù)油管、工作滾筒管匯、油嘴管匯氣試壓15兆帕,30分鐘壓降不大于0.7兆帕為合格。4.下連續(xù)油管管柱裝置,注氣排鹵確認采氣樹及井下安全閥打開,計數(shù)器歸零,校正工具底部深度,下連續(xù)油管管柱裝置,控制下放速度小于6米/分,工具出7吋注采套管后控制下放速度小于1.5米/分,密切注意懸重變化,探底加壓小于5kn,復探1-3次,上提0-0.5米,從連續(xù)油管管柱裝置與注采管柱環(huán)空注天然氣,從連續(xù)油管管柱裝置排出鹵水,排出鹵水經(jīng)過管線進入分離器,通過分離器分離排鹵帶出的天然氣,氣體燒掉,液體進罐通過輸鹵泵外輸,直至鹵水不再排出。5.沖洗堵塞沉渣并排鹵將連續(xù)油管管柱裝置重新上提0-0.5米,關閉排鹵流程閥門,地面切換排鹵流程至沖洗流程,啟動地面清水泵,開啟清水接入管線閥門,使清水通過連續(xù)油管注入腔底,對井底旋轉沖洗工具及外圍沉渣進行沖洗,結合步驟1)已有排鹵體積及已有聲納測量結果計算剩余未排出鹵水體積,根據(jù)剩余未排出鹵水體積并結合腔體形狀,繼續(xù)下放連續(xù)油管管柱裝置進行注氣排鹵至累計排鹵體積達到目標排鹵體積;6.取出連續(xù)油管管柱裝置排鹵結束,保持井內壓力,帶壓取出連續(xù)油管管柱裝置及排鹵工具。若上提遇阻則控制上提負荷不能超過連續(xù)油管極限抗拉強度的80%,若上下緩慢活動多次仍不能解卡,則清水正沖洗,邊沖邊起。若仍無效果,則從連續(xù)油管內投球憋壓打掉液壓安全接頭及旋轉沖洗工具取出上部連續(xù)油管。3#腔體底部累計排鹵完畢,歷時二個月,累計排出腔體底部鹵水16200m3,腔體有效利用率由93.211%提高至98.6%。根據(jù)金壇鹽穴儲氣庫的造腔綜合成本100元/m3估算,直接經(jīng)濟效益約160萬元。附表2施工所需設備表。表2施工所需設備一覽表當前第1頁12