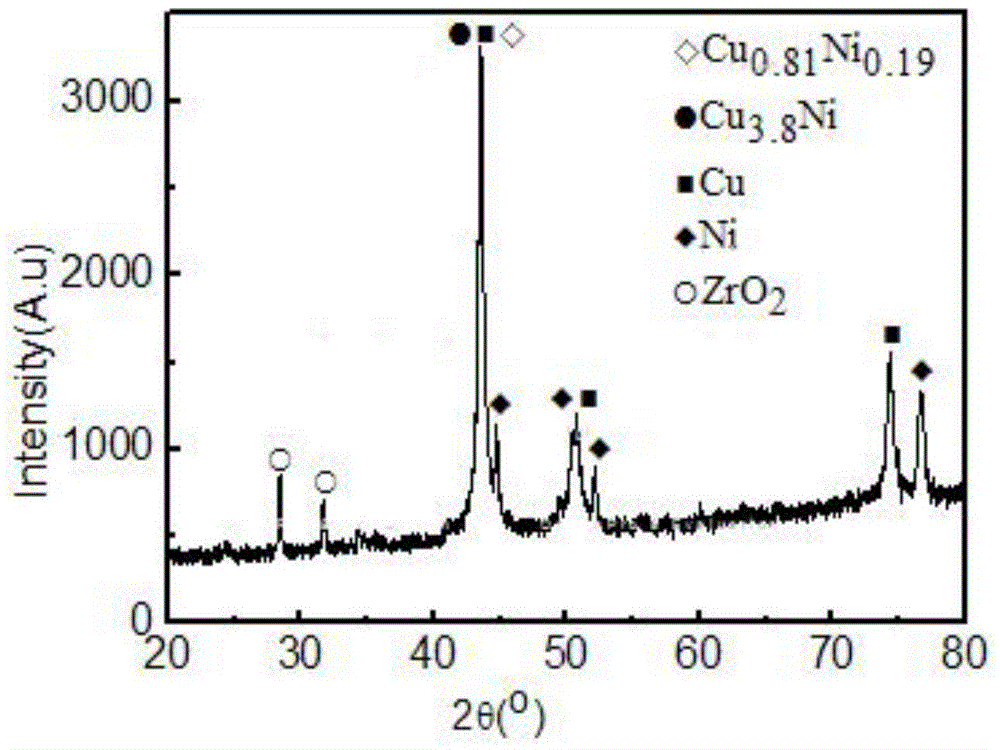
本發(fā)明屬于涂鍍層表面制備技術(shù)領(lǐng)域,具體涉及一種TC4鈦合金表面制備ZrO2/Cu復(fù)合鍍層的方法。
背景技術(shù):鈦及鈦合金已在各個(gè)制造領(lǐng)域特別是石油工業(yè)領(lǐng)域獲得廣泛的應(yīng)用,但由于鈦及鈦合金具有耐磨性能差,表面容易擦傷、咬死,且焊接性能差等缺點(diǎn),限制了鈦及鈦合金的應(yīng)用范圍?,F(xiàn)有技術(shù)中通常采用適當(dāng)?shù)碾婂児に噷?duì)鈦及鈦合金表面予以處理,能夠明顯的改善鈦及鈦合金的表面性能,賦予其新的物理性能,擴(kuò)大其應(yīng)用范圍。銅金屬具有良好的延展性和柔軟性,導(dǎo)電性和導(dǎo)熱性,容易拋光,而且熔點(diǎn)高,塑性好,應(yīng)用在金屬表面可顯著降低摩擦因數(shù),減小摩擦力,對(duì)改善金屬材料表面的摩擦磨損性能具有良好的效果。二氧化鋯是一種具有高熔點(diǎn)、高沸點(diǎn)、導(dǎo)熱系數(shù)小、熱膨脹系數(shù)大、耐磨性好和抗腐蝕性能優(yōu)良等特點(diǎn)的無(wú)機(jī)非金屬材料。傳統(tǒng)的鈦合金表面鍍Cu工藝,普遍存在以下問(wèn)題:1、Cu鍍層置于空氣中易氧化生成黑色CuO,影響鍍層的美觀;2、采用表面覆蓋Cu鍍層的鈦合金制備的高速柴油機(jī)缸體、汽車燃?xì)鉁u輪發(fā)動(dòng)機(jī)主軸等產(chǎn)品需要在高溫下長(zhǎng)期工作,這些產(chǎn)品很容易磨損損壞,傳統(tǒng)電鍍、噴涂等工藝對(duì)鈦合金表面進(jìn)行修復(fù)很難滿足耐高溫環(huán)境下對(duì)此類產(chǎn)品耐磨損的需要。
技術(shù)實(shí)現(xiàn)要素:本發(fā)明所要解決的技術(shù)問(wèn)題在于針對(duì)上述現(xiàn)有技術(shù)中的不足,提供一種TC4鈦合金表面制備ZrO2/Cu復(fù)合鍍層的方法。該方法利用配制含有ZrO2納米顆粒的電鍍液,通過(guò)適合的電鍍工藝條件在TC4鈦合金表面電沉積一層含有ZrO2納米顆粒和Cu的復(fù)合鍍層,該復(fù)合鍍層中ZrO2納米顆粒鑲嵌在Cu基體中,能夠有效阻礙高溫條件下氧在復(fù)合鍍層中的擴(kuò)散,從而大大降低了復(fù)合鍍層發(fā)生氧化反應(yīng)的速度,增強(qiáng)了TC4鈦合金表面的抗氧化性,此外,ZrO2納米顆粒的引入也顯著提高了復(fù)合鍍層的耐磨耐蝕性能。為解決上述技術(shù)問(wèn)題,本發(fā)明采用的技術(shù)方案是:一種TC4鈦合金表面制備ZrO2/Cu復(fù)合鍍層的方法,其特征在于,該方法包括以下步驟:步驟一、對(duì)TC4鈦合金表面進(jìn)行預(yù)處理,去除表面缺陷,然后將去除表面缺陷的TC4鈦合金置于活化液中活化處理5min~20min;所述活化液由體積比為(2~7):1的甲酰胺和氫氟酸混合制成;步驟二、配制電鍍液,然后向電鍍液中加入ZrO2納米顆粒,攪拌均勻后調(diào)節(jié)電鍍液的pH為2~5,靜置10h后待用,所述ZrO2納米顆粒的加入量為每升電鍍液中加入0.5g~20gZrO2納米顆粒;所述電鍍液由以下原料配制而成:硫酸銅100g/L~200g/L,濃硫酸40ml/L~70ml/L,氯化鈉0.02g/L~1.00g/L,吐溫800.02g/L~5g/L,十二烷基苯磺酸鈉0.02g/L~2g/L,余量為水;所述濃硫酸的質(zhì)量濃度不低于98%;步驟三、將兩塊相同的銅排和步驟一中經(jīng)活化處理后的TC4鈦合金置于步驟二中靜置后的電鍍液中,所述TC4鈦合金放置在兩塊銅排的中間位置,以兩塊銅排為陽(yáng)極,以TC4鈦合金為陰極,在攪拌條件下進(jìn)行氧化還原反應(yīng),使TC4鈦合金表面電沉積一層均勻的ZrO2/Cu復(fù)合鍍層;所述氧化還原反應(yīng)過(guò)程中電壓為0.3V~1.5V,電鍍液的溫度為20℃~45℃,所述氧化還原反應(yīng)的時(shí)間為5min~50min。上述的TC4鈦合金表面制備ZrO2/Cu復(fù)合鍍層的方法,其特征在于,步驟一中所述預(yù)處理的方法為:采用碳酸鈉和氫氧化鈉的混合溶液清洗TC4鈦合金去除表面油脂,然后對(duì)去除油脂后的TC4鈦合金進(jìn)行打磨處理去除表面缺陷,清洗后吹干。上述的TC4鈦合金表面制備ZrO2/Cu復(fù)合鍍層的方法,其特征在于,所述混合溶液中碳酸鈉的質(zhì)量濃度為10g/L,氫氧化鈉的質(zhì)量濃度為5g/L。上述的TC4鈦合金表面制備ZrO2/Cu復(fù)合鍍層的方法,其特征在于,步驟一中所述活化液由體積比為5:1的甲酰胺和氫氟酸混合制成。上述的TC4鈦合金表面制備ZrO2/Cu復(fù)合鍍層的方法,其特征在于,步驟二中所述電鍍液由以下原料配制而成:硫酸銅130g/L~170g/L,濃硫酸50ml/L~60ml/L,氯化鈉0.3g/L~0.8g/L,吐溫802g/L~4g/L,十二烷基苯磺酸鈉1g/L~1.5g/L,余量為水;所述ZrO2納米顆粒的加入量為每升電鍍液中加入5g~18gZrO2納米顆粒。上述的TC4鈦合金表面制備ZrO2/Cu復(fù)合鍍層的方法,其特征在于,所述電鍍液由以下原料配制而成:硫酸銅150g/L,濃硫酸55ml/L,氯化鈉0.5g/L,吐溫803g/L,十二烷基苯磺酸鈉1.3g/L,余量為水;所述ZrO2納米顆粒的加入量為每升電鍍液中加入13gZrO2納米顆粒。上述的TC4鈦合金表面制備ZrO2/Cu復(fù)合鍍層的方法,其特征在于,步驟二中調(diào)節(jié)所述電鍍液的pH為4。上述的TC4鈦合金表面制備ZrO2/Cu復(fù)合鍍層的方法,其特征在于,步驟三中所述電壓為0.6V~1.2V,電鍍液的溫度為30℃~40℃,所述氧化還原反應(yīng)的時(shí)間為20min~40min。上述的TC4鈦合金表面制備ZrO2/Cu復(fù)合鍍層的方法,其特征在于,所述電壓為1V,電鍍液的溫度為35℃,所述氧化還原反應(yīng)的時(shí)間為30min。本發(fā)明與現(xiàn)有技術(shù)相比具有以下優(yōu)點(diǎn):1、本發(fā)明的方法利用配制含有ZrO2納米顆粒的電鍍液,通過(guò)適合的電鍍工藝條件在TC4鈦合金表面電沉積一層含有ZrO2納米顆粒和Cu的復(fù)合鍍層,該復(fù)合鍍層中ZrO2納米顆粒鑲嵌在Cu基體中,能夠有效阻礙高溫條件下氧在復(fù)合鍍層中的擴(kuò)散,從而大大降低了復(fù)合鍍層發(fā)生氧化反應(yīng)的速度,增強(qiáng)了TC4鈦合金表面的抗氧化性,此外,ZrO2納米顆粒的引入也顯著提高了復(fù)合鍍層的耐磨耐蝕性能。2、本發(fā)明的方法中首先利用由甲酰胺和氫氟酸混合配制而成的活化液對(duì)去除表面缺陷的TC4鈦合金進(jìn)行活化處理,活化處理后在TC4鈦合金表面產(chǎn)生一層“活性膜”TiH2,該“活性膜”TiH2能夠保護(hù)TC4鈦合金基體在電鍍前不被氧化,使TC4鈦合金基體表面具有良好的鍍層結(jié)合力,然后通過(guò)合適的電鍍工藝條件在經(jīng)活化處理后的TC4鈦合金電沉積一層納米ZrO2/Cu復(fù)合鍍層,該復(fù)合鍍層兼具了優(yōu)良的耐磨耐蝕性能和高溫抗氧化性能,可滿足TC4鈦合金工程使用中對(duì)良好耐磨耐蝕性和抗氧化性的要求。3、本發(fā)明使用的復(fù)合渡液中各組分穩(wěn)定、無(wú)毒,且復(fù)合渡液易于配制,本發(fā)明的方法中設(shè)備投資少,操作比較簡(jiǎn)單,工藝過(guò)程易控,生產(chǎn)費(fèi)用低,能源消耗少,原材料利用率比較高,因此本發(fā)明的方法是一種能夠方便、經(jīng)濟(jì)的在TC4鈦合金表面獲得高性能鍍層的方法。下面通過(guò)附圖和實(shí)施例,對(duì)本發(fā)明的技術(shù)方案做進(jìn)一步的詳細(xì)描述。附圖說(shuō)明圖1為本發(fā)明實(shí)施例1中在TC4鈦合金表面制備的ZrO2/Cu復(fù)合鍍層的SEM照片。圖2為本發(fā)明實(shí)施例1中在TC4鈦合金表面制備的ZrO2/Cu復(fù)合鍍層的XRD譜圖。圖3為對(duì)比例1中在TC4鈦合金表面制備的Cu鍍層的SEM照片。圖4為本發(fā)明實(shí)施例1中在TC4鈦合金表面制備的ZrO2/Cu復(fù)合鍍層的動(dòng)電位極化曲線和對(duì)比例1中在TC4鈦合金表面制備的Cu鍍層的動(dòng)電位極化曲線。具體實(shí)施方式實(shí)施例1本實(shí)施例在TC4鈦合金表面制備ZrO2/Cu復(fù)合鍍層的方法包括以下步驟:步驟一、對(duì)TC4鈦合金表面進(jìn)行預(yù)處理,去除表面缺陷,然后將去除表面缺陷的TC4鈦合金置于活化液中活化處理15min;所述活化液由體積比為5:1的甲酰胺和氫氟酸混合制成;所述氫氟酸的質(zhì)量濃度為40%,所述預(yù)處理的方法為:采用碳酸鈉和氫氧化鈉的混合溶液清洗TC4鈦合金去除表面油脂,然后對(duì)去除油脂后的TC4鈦合金進(jìn)行打磨處理去除表面缺陷,清洗后吹干,所述混合溶液中碳酸鈉的質(zhì)量濃度為10g/L,氫氧化鈉的質(zhì)量濃度為5g/L;步驟二、配制電鍍液,然后向電鍍液中加入ZrO2納米顆粒,攪拌均勻后用氨水調(diào)節(jié)電鍍液的pH為4,靜置10h后待用,所述ZrO2納米顆粒的加入量為每升電鍍液中加入13gZrO2納米顆粒;所述電鍍液由以下原料配制而成:硫酸銅150g/L,濃硫酸55ml/L,氯化鈉0.5g/L,吐溫803g/L,十二烷基苯磺酸鈉1.3g/L,余量為水;所述濃硫酸的質(zhì)量濃度為98%;步驟三、將兩塊銅排和步驟一中經(jīng)活化處理后的TC4鈦合金置于步驟二中靜置后的電鍍液中,且TC4鈦合金放置在兩塊銅排的中間位置,以兩塊銅排為陽(yáng)極,以TC4鈦合金為陰極,在攪拌條件下進(jìn)行氧化還原反應(yīng),使TC4鈦合金表面電沉積一層均勻的ZrO2/Cu復(fù)合鍍層;所述氧化還原反應(yīng)過(guò)程中電壓為1V,電鍍液的溫度為35℃,所述氧化還原反應(yīng)的時(shí)間為30min。圖1為實(shí)施例1中在TC4鈦合金表面制備的ZrO2/Cu復(fù)合鍍層的SEM照片,從圖1中可看出ZrO2納米顆粒明顯鑲嵌或附著于Cu鍍層表面,ZrO2/Cu復(fù)合鍍層表面致密、均勻,鍍層結(jié)合良好,測(cè)試表面該復(fù)合鍍層的硬度為213HV。圖2為實(shí)施例1中在TC4鈦合金表面制備的ZrO2/Cu復(fù)合鍍層的XRD譜圖,從圖2中可看出,氧化還原反應(yīng)過(guò)程中ZrO2納米顆粒參與到鍍層的生長(zhǎng),形成了ZrO2/Cu復(fù)合鍍層。對(duì)比例1對(duì)比例1中在TC4鈦合金表面制備Cu鍍層的方法與實(shí)施例1的方法相同,其不同之處在于:步驟二中不向配制的電鍍液中加入ZrO2納米顆粒。圖3為對(duì)比例1中在TC4鈦合金表面制備的Cu鍍層的SEM照片,從圖3中可看出Cu鍍層表面致密、均勻,鍍層結(jié)合良好,測(cè)試表明該Cu鍍層的硬度為172HV。室溫條件下,分別將實(shí)施例1中制備的ZrO2/Cu復(fù)合鍍層和對(duì)比例1中制備的Cu鍍層置于質(zhì)量濃度為3.5%的氯化鈉溶液中,測(cè)量其動(dòng)電位極化曲線。圖4中曲線a為實(shí)施例1中在TC4鈦合金表面制備的ZrO2/Cu復(fù)合鍍層的動(dòng)電位極化曲線,曲線b為對(duì)比例1中在TC4鈦合金表面制備的Cu鍍層的動(dòng)電位極化曲線,從圖4中可看出,與Cu鍍層的腐蝕電位(-613mV)相比,ZrO2/Cu復(fù)合鍍層的腐蝕電位(-332mV)正移了281mV,腐蝕電流密度也明顯降低,說(shuō)明ZrO2/Cu復(fù)合鍍層的耐蝕性顯著優(yōu)于Cu鍍層的耐蝕性。將對(duì)比例1中表面電沉積有Cu鍍層的TC4鈦合金放置在空氣中5min后,Cu鍍層表面開(kāi)始發(fā)黑,這是因?yàn)镃u鍍層中的Cu易于被氧化生成黑色的CuO,而實(shí)施例1中表面電沉積有ZrO2/Cu復(fù)合鍍層的TC4鈦合金放置在空氣中5~6天后,復(fù)合鍍層仍然均勻光亮,表明該復(fù)合鍍層的抗氧化性能明顯提高。實(shí)施例1在TC4鈦合金表面制備的ZrO2/Cu復(fù)合鍍層中ZrO2納米顆粒鑲嵌于Cu基質(zhì)中,阻礙了氧在復(fù)合鍍層中的擴(kuò)散,從而降低了復(fù)合鍍層的氧化速度;此外,ZrO2納米顆粒增加了Cu基質(zhì)晶粒的成核速率,阻礙了Cu基質(zhì)晶粒的生長(zhǎng)速率,促進(jìn)Cu基質(zhì)晶粒的顯著細(xì)化,這能夠增加位錯(cuò)運(yùn)動(dòng)的阻力,Cu基質(zhì)晶粒的細(xì)化使復(fù)合鍍層致密,孔隙率下降,從而提高了復(fù)合鍍層的耐磨、耐腐蝕性能和抗氧化性能。實(shí)施例2本實(shí)施例在TC4鈦合金表面制備ZrO2/Cu復(fù)合鍍層的方法包括以下步驟:步驟一、對(duì)TC4鈦合金表面進(jìn)行預(yù)處理,去除表面缺陷,然后將去除表面缺陷的TC4鈦合金置于活化液中活化處理5min;所述活化液由體積比為2:1的甲酰胺和氫氟酸混合制成;所述氫氟酸的質(zhì)量濃度為40%,所述預(yù)處理的方法為:采用碳酸鈉和氫氧化鈉的混合溶液清洗TC4鈦合金去除表面油脂,然后對(duì)去除油脂后的TC4鈦合金進(jìn)行打磨處理去除表面缺陷,清洗后吹干,所述混合溶液中碳酸鈉的質(zhì)量濃度為10g/L,氫氧化鈉的質(zhì)量濃度為5g/L;步驟二、配制電鍍液,然后向電鍍液中加入ZrO2納米顆粒,攪拌均勻后用氨水調(diào)節(jié)電鍍液的pH為5,靜置10h后待用,所述ZrO2納米顆粒的加入量為每升電鍍液中加入18gZrO2納米顆粒;所述電鍍液由以下原料配制而成:硫酸銅130g/L,濃硫酸60ml/L,氯化鈉0.8g/L,吐溫804g/L,十二烷基苯磺酸鈉1.5g/L,余量為水;所述濃硫酸的質(zhì)量濃度為99%;步驟三、將兩塊銅排和步驟一中經(jīng)活化處理后的TC4鈦合金置于步驟二中靜置后的電鍍液中,且TC4鈦合金放置在兩塊銅排的中間位置,以兩塊銅排為陽(yáng)極,以TC4鈦合金為陰極,在攪拌條件下進(jìn)行氧化還原反應(yīng),使TC4鈦合金表面電沉積一層均勻的ZrO2/Cu復(fù)合鍍層;所述氧化還原反應(yīng)過(guò)程中電壓為0.6V,電鍍液的溫度為40℃,所述氧化還原反應(yīng)的時(shí)間為40min。本實(shí)施例在TC4鈦合金表面制備的ZrO2/Cu復(fù)合鍍層均勻光亮、致密,測(cè)試表面該復(fù)合鍍層的硬度為208HV,復(fù)合鍍層中ZrO2納米顆粒鑲嵌在Cu基體中,能夠有效阻礙高溫條件下氧在復(fù)合鍍層中的擴(kuò)散,從而降低了復(fù)合鍍層發(fā)生氧化反應(yīng)的速度,增強(qiáng)了TC4鈦合金表面的抗氧化性,此外,納米ZrO2的引入使復(fù)合鍍層的孔隙率下降,顯著提高了復(fù)合鍍層的耐磨耐蝕性能。實(shí)施例3本實(shí)施例在TC4鈦合金表面制備ZrO2/Cu復(fù)合鍍層的方法包括以下步驟:步驟一、對(duì)TC4鈦合金表面進(jìn)行預(yù)處理,去除表面缺陷,然后將去除表面缺陷的TC4鈦合金置于活化液中活化處理20min;所述活化液由體積比為7:1的甲酰胺和氫氟酸混合制成;所述氫氟酸的質(zhì)量濃度為40%,所述預(yù)處理的方法為:采用碳酸鈉和氫氧化鈉的混合溶液清洗TC4鈦合金去除表面油脂,然后對(duì)去除油脂后的TC4鈦合金進(jìn)行打磨處理去除表面缺陷,清洗后吹干,所述混合溶液中碳酸鈉的質(zhì)量濃度為10g/L,氫氧化鈉的質(zhì)量濃度為5g/L;步驟二、配制電鍍液,然后向電鍍液中加入ZrO2納米顆粒,攪拌均勻后用氨水調(diào)節(jié)電鍍液的pH為2,靜置10h后待用,所述ZrO2納米顆粒的加入量為每升電鍍液中加入5gZrO2納米顆粒;所述電鍍液由以下原料配制而成:硫酸銅170g/L,濃硫酸50ml/L,氯化鈉0.3g/L,吐溫802g/L,十二烷基苯磺酸鈉1g/L,余量為水;所述濃硫酸的質(zhì)量濃度為98%;步驟三、將兩塊銅排和步驟一中經(jīng)活化處理后的TC4鈦合金置于步驟二中靜置后的電鍍液中,且TC4鈦合金放置在兩塊銅排的中間位置,以兩塊銅排為陽(yáng)極,以TC4鈦合金為陰極,在攪拌條件下進(jìn)行氧化還原反應(yīng),使TC4鈦合金表面電沉積一層均勻的ZrO2/Cu復(fù)合鍍層;所述氧化還原反應(yīng)過(guò)程中電壓為1.2V,電鍍液的溫度為30℃,所述氧化還原反應(yīng)的時(shí)間為20min。本實(shí)施例在TC4鈦合金表面制備的ZrO2/Cu復(fù)合鍍層均勻光亮、致密,測(cè)試表面該復(fù)合鍍層的硬度為203HV,復(fù)合鍍層中ZrO2納米顆粒鑲嵌在Cu基體中,能夠有效阻礙高溫條件下氧在復(fù)合鍍層中的擴(kuò)散,從而降低了復(fù)合鍍層發(fā)生氧化反應(yīng)的速度,增強(qiáng)了TC4鈦合金表面的抗氧化性,此外,納米ZrO2的引入使復(fù)合鍍層的孔隙率下降,顯著提高了復(fù)合鍍層的耐磨耐蝕性能。實(shí)施例4本實(shí)施例在TC4鈦合金表面制備ZrO2/Cu復(fù)合鍍層的方法包括以下步驟:步驟一、對(duì)TC4鈦合金表面進(jìn)行預(yù)處理,去除表面缺陷,然后將去除表面缺陷的TC4鈦合金置于活化液中活化處理13min;所述活化液由體積比為3.5:1的甲酰胺和氫氟酸混合制成;所述氫氟酸的質(zhì)量濃度為40%,所述預(yù)處理的方法為:采用碳酸鈉和氫氧化鈉的混合溶液清洗TC4鈦合金去除表面油脂,然后對(duì)去除油脂后的TC4鈦合金進(jìn)行打磨處理去除表面缺陷,清洗后吹干,所述混合溶液中碳酸鈉的質(zhì)量濃度為10g/L,氫氧化鈉的質(zhì)量濃度為5g/L;步驟二、配制電鍍液,然后向電鍍液中加入ZrO2納米顆粒,攪拌均勻后用氨水調(diào)節(jié)電鍍液的pH為3.5,靜置10h后待用,所述ZrO2納米顆粒的加入量為每升電鍍液中加入0.5gZrO2納米顆粒;所述電鍍液由以下原料配制而成:硫酸銅100g/L,濃硫酸70ml/L,氯化鈉1.00g/L,吐溫800.02g/L,十二烷基苯磺酸鈉0.02g/L,余量為水;所述濃硫酸的質(zhì)量濃度為99%;步驟三、將兩塊銅排和步驟一中經(jīng)活化處理后的TC4鈦合金置于步驟二中靜置后的電鍍液中,且TC4鈦合金放置在兩塊銅排的中間位置,以兩塊銅排為陽(yáng)極,以TC4鈦合金為陰極,在攪拌條件下進(jìn)行氧化還原反應(yīng),使TC4鈦合金表面電沉積一層均勻的ZrO2/Cu復(fù)合鍍層;所述氧化還原反應(yīng)過(guò)程中電壓為0.3V,電鍍液的溫度為45℃,所述氧化還原反應(yīng)的時(shí)間為50min。本實(shí)施例在TC4鈦合金表面制備的ZrO2/Cu復(fù)合鍍層均勻光亮、致密,測(cè)試表面該復(fù)合鍍層的硬度為198HV,復(fù)合鍍層中ZrO2納米顆粒鑲嵌在Cu基體中,能夠有效阻礙高溫條件下氧在復(fù)合鍍層中的擴(kuò)散,從而降低了復(fù)合鍍層發(fā)生氧化反應(yīng)的速度,增強(qiáng)了TC4鈦合金表面的抗氧化性,此外,納米ZrO2的引入使復(fù)合鍍層的孔隙率下降,顯著提高了復(fù)合鍍層的耐磨耐蝕性能。實(shí)施例5本實(shí)施例在TC4鈦合金表面制備ZrO2/Cu復(fù)合鍍層的方法包括以下步驟:步驟一、對(duì)TC4鈦合金表面進(jìn)行預(yù)處理,去除表面缺陷,然后將去除表面缺陷的TC4鈦合金置于活化液中活化處理10min;所述活化液由體積比為3:1的甲酰胺和氫氟酸混合制成;所述氫氟酸的質(zhì)量濃度為40%,所述預(yù)處理的方法為:采用碳酸鈉和氫氧化鈉的混合溶液清洗TC4鈦合金去除表面油脂,然后對(duì)去除油脂后的TC4鈦合金進(jìn)行打磨處理去除表面缺陷,清洗后吹干,所述混合溶液中碳酸鈉的質(zhì)量濃度為10g/L,氫氧化鈉的質(zhì)量濃度為5g/L;步驟二、配制電鍍液,然后向電鍍液中加入ZrO2納米顆粒,攪拌均勻后用氨水調(diào)節(jié)電鍍液的pH為4,靜置10h后待用,所述ZrO2納米顆粒的加入量為每升電鍍液中加入20gZrO2納米顆粒;所述電鍍液由以下原料配制而成:硫酸銅200g/L,濃硫酸40ml/L,氯化鈉0.02g/L,吐溫805g/L,十二烷基苯磺酸鈉2g/L,余量為水;所述濃硫酸的質(zhì)量濃度為98%;步驟三、將兩塊銅排和步驟一中經(jīng)活化處理后的TC4鈦合金置于步驟二中靜置后的電鍍液中,且TC4鈦合金放置在兩塊銅排的中間位置,以兩塊銅排為陽(yáng)極,以TC4鈦合金為陰極,在攪拌條件下進(jìn)行氧化還原反應(yīng),使TC4鈦合金表面電沉積一層均勻的ZrO2/Cu復(fù)合鍍層;所述氧化還原反應(yīng)過(guò)程中電壓為1.5V,電鍍液的溫度為20℃,所述氧化還原反應(yīng)的時(shí)間為5min。本實(shí)施例在TC4鈦合金表面制備的ZrO2/Cu復(fù)合鍍層均勻光亮、致密,測(cè)試表面該復(fù)合鍍層的硬度為201HV,復(fù)合鍍層中ZrO2納米顆粒鑲嵌在Cu基體中,能夠有效阻礙高溫條件下氧在復(fù)合鍍層中的擴(kuò)散,從而降低了復(fù)合鍍層發(fā)生氧化反應(yīng)的速度,增強(qiáng)了TC4鈦合金表面的抗氧化性,此外,納米ZrO2的引入使復(fù)合鍍層的孔隙率下降,顯著提高了復(fù)合鍍層的耐磨耐蝕性能。實(shí)施例6本實(shí)施例在TC4鈦合金表面制備ZrO2/Cu復(fù)合鍍層的方法包括以下步驟:步驟一、對(duì)TC4鈦合金表面進(jìn)行預(yù)處理,去除表面缺陷,然后將去除表面缺陷的TC4鈦合金置于活化液中活化處理18min;所述活化液由體積比為6:1的甲酰胺和氫氟酸混合制成;所述氫氟酸的質(zhì)量濃度為40%,所述預(yù)處理的方法為:采用碳酸鈉和氫氧化鈉的混合溶液清洗TC4鈦合金去除表面油脂,然后對(duì)去除油脂后的TC4鈦合金進(jìn)行打磨處理去除表面缺陷,清洗后吹干,所述混合溶液中碳酸鈉的質(zhì)量濃度為10g/L,氫氧化鈉的質(zhì)量濃度為5g/L;步驟二、配制電鍍液,然后向電鍍液中加入ZrO2納米顆粒,攪拌均勻后用氨水調(diào)節(jié)電鍍液的pH為4,靜置10h后待用,所述ZrO2納米顆粒的加入量為每升電鍍液中加入10gZrO2納米顆粒;所述電鍍液由以下原料配制而成:硫酸銅150g/L,濃硫酸55ml/L,氯化鈉5g/L,吐溫802.5g/L,十二烷基苯磺酸鈉1g/L,余量為水;所述濃硫酸的質(zhì)量濃度為98%;步驟三、將兩塊銅排和步驟一中經(jīng)活化處理后的TC4鈦合金置于步驟二中靜置后的電鍍液中,且TC4鈦合金放置在兩塊銅排的中間位置,以兩塊銅排為陽(yáng)極,以TC4鈦合金為陰極,在攪拌條件下進(jìn)行氧化還原反應(yīng),使TC4鈦合金表面電沉積一層均勻的ZrO2/Cu復(fù)合鍍層;所述氧化還原反應(yīng)過(guò)程電壓為1V,電鍍液的溫度為35℃,所述氧化還原反應(yīng)的時(shí)間為30min。本實(shí)施例在TC4鈦合金表面制備的ZrO2/Cu復(fù)合鍍層均勻光亮、致密,測(cè)試表面該復(fù)合鍍層的硬度為202HV,復(fù)合鍍層中ZrO2納米顆粒鑲嵌在Cu基體中,能夠有效阻礙高溫條件下氧在復(fù)合鍍層中的擴(kuò)散,從而降低了復(fù)合鍍層發(fā)生氧化反應(yīng)的速度,增強(qiáng)了TC4鈦合金表面的抗氧化性,此外,納米ZrO2的引入使復(fù)合鍍層的孔隙率下降,顯著提高了復(fù)合鍍層的耐磨耐蝕性能。以上所述,僅是本發(fā)明的較佳實(shí)施例,并非對(duì)本發(fā)明作任何限制,凡是根據(jù)本發(fā)明技術(shù)實(shí)質(zhì)對(duì)以上實(shí)施例所作的任何簡(jiǎn)單修改、變更以及等效結(jié)構(gòu)變化,均仍屬于本發(fā)明技術(shù)方案的保護(hù)范圍內(nèi)。