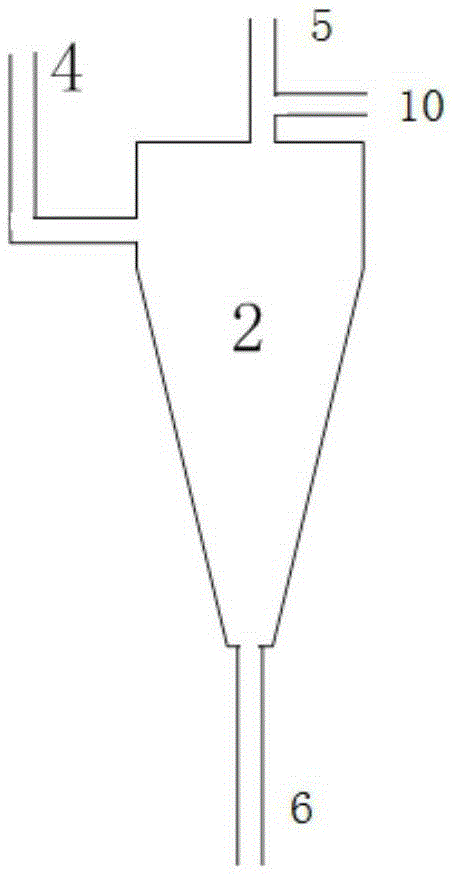
本發(fā)明涉及煉油領(lǐng)域,具體地,涉及一種劣質(zhì)原料油的輕質(zhì)化方法。
背景技術(shù):
:在傳統(tǒng)煉廠中,溶劑脫瀝青工藝主要用于從減壓渣油中制取高粘度潤(rùn)滑油基礎(chǔ)油,其中脫瀝青過程主要作用是脫去渣油中的瀝青以降低其殘?zhí)恐岛透纳粕珴?。但是現(xiàn)代煉廠所加工的原油重質(zhì)化程度加深,造成重油催化裂化及固定床渣油加氫等裝置的原料殘?zhí)恐瞪?、金屬含量增大,進(jìn)而影響上述裝置的運(yùn)轉(zhuǎn)周期。而渣油中的金屬等雜質(zhì)主要集中在瀝青質(zhì)組分中,因此通過溶劑脫瀝青工藝可以較為徹底地清除原料油中的瀝青質(zhì),使得脫瀝青油的殘?zhí)恐岛徒饘俸看蠓冉档?,從而能夠作為重油催化裂化、渣油加氫處理及渣油加氫裂化的?yōu)質(zhì)原料。溶劑脫瀝青過程同時(shí)產(chǎn)生一定量的脫油瀝青。脫油瀝青是一種較為特殊的膠體溶液,由于富集了渣油中絕大部分的瀝青質(zhì)和重膠質(zhì),使得其分子結(jié)構(gòu)高度芳構(gòu)化,可加工性能極差,并且難以成為道路瀝青產(chǎn)品。與常規(guī)減壓渣油相比,脫油瀝青的結(jié)焦傾向更為嚴(yán)重。目前,煉廠中脫油瀝青主要用于循環(huán)流化床和電廠鍋爐的燃料、燃料油調(diào)和組分和瀝青水漿原料,對(duì)資源造成一定的浪費(fèi)。乙烯焦油、催化裂化回?zé)捰图按呋鸦蜐{中均含有大量的重質(zhì)芳烴,不易在現(xiàn)有煉廠流程中進(jìn)一步加工。例如,CN101531924B中提到不同類型的重質(zhì)原料在催化裂化裝置中存在最佳轉(zhuǎn)化率區(qū)間,在該區(qū)間內(nèi)可以減少焦炭和干氣的生成;含有大量芳烴的未轉(zhuǎn)化重油如果進(jìn)一步在催化裂化裝置內(nèi)轉(zhuǎn)化,將會(huì)導(dǎo)致干氣和焦炭產(chǎn)率的急劇上升,必須采取其它技術(shù)途徑轉(zhuǎn)化。 CN101531924B和CN101531923B均公開了一種重油催化裂化與加氫處理組合工藝,將催化裂化分餾塔中大于260℃餾分作為固定床加氫處理的進(jìn)料,而加氫尾油則進(jìn)入催化裂化裝置。雖然該工藝可以減少干氣和焦炭的生成,但是仍然會(huì)產(chǎn)生一定量的油漿。此外,催化裂化油漿中含有大量催化劑粉末,容易沉積在催化劑床層上,造成床層壓降升高和堵塞,使其無法采用傳統(tǒng)的固定床加氫工藝輕質(zhì)化。目前,上述高芳烴組分主要用于燃料油、改性瀝青、針狀焦、炭黑和瀝青基碳纖維的制備等,同樣無法實(shí)現(xiàn)資源的全面有效利用。CN1195822C公開了一種脫油瀝青的減粘裂化方法。該現(xiàn)有技術(shù)將脫油瀝青和催化裂化油漿按照一定的比例摻混后,采用低溫長(zhǎng)時(shí)間的操作方式,在保證操作周期的基礎(chǔ)上,有效降低了原料的粘度。在分餾出少量的減粘氣體和減粘汽油后,生成可以作為重質(zhì)燃料油的減粘渣油。該方法的主要產(chǎn)品為減粘渣油,產(chǎn)品價(jià)值較低,且作為重質(zhì)燃料油使用也會(huì)對(duì)環(huán)境造成一定影響,無法實(shí)現(xiàn)原料的經(jīng)濟(jì)高效利用。CN102234536A則提到了一種溶劑脫瀝青-重油催化裂化-瀝青氣化-瀝青調(diào)和的組合工藝。其中脫油瀝青一部分作為瀝青氣化的原料用于生產(chǎn)化肥,另一部分與經(jīng)過拔頭的催化裂化油漿一起調(diào)和生產(chǎn)高等級(jí)道路瀝青。雖然該組合工藝實(shí)現(xiàn)了瀝青產(chǎn)品的高效利用,但是對(duì)于脫瀝青工藝過程和脫油瀝青的性質(zhì)均有明確的限制條件,原料的適應(yīng)范圍較窄,同時(shí)無法滿足輕質(zhì)餾分油生產(chǎn)的需要。現(xiàn)有技術(shù)既無法實(shí)現(xiàn)乙烯焦油、催化裂化回?zé)捰图按呋鸦蜐{等高芳烴組分的完全輕質(zhì)化,又無法適應(yīng)原料劣質(zhì)化的趨勢(shì)而高效加工脫油瀝青。因此,需要開發(fā)一種全新的轉(zhuǎn)化工藝,將不同性質(zhì)的脫油瀝青和/或高芳烴組分絕大部分或全部轉(zhuǎn)化為輕質(zhì)餾分油,以滿足我國對(duì)交通燃料日益增長(zhǎng)的需求。技術(shù)實(shí)現(xiàn)要素:本發(fā)明的目的是針對(duì)現(xiàn)有技術(shù)的不足,解決包括脫油瀝青和/或高芳烴組分(乙烯焦油、催化裂化回?zé)捰图按呋鸦蜐{等)在內(nèi)的劣質(zhì)原料油無法高效轉(zhuǎn)化為輕質(zhì)餾分油的問題。為了實(shí)現(xiàn)上述目的,本發(fā)明提供一種劣質(zhì)原料油的輕質(zhì)化方法,該方法包括:將包括劣質(zhì)原料油、加氫催化劑和氫氣的反應(yīng)物料引入漿態(tài)床反應(yīng)器中進(jìn)行加氫裂化反應(yīng),得到加氫裂化混合物;將所述加氫裂化混合物進(jìn)行分離,得到第一氣體、第一輕質(zhì)餾分油和含有加氫催化劑的重質(zhì)餾分油;將所述重質(zhì)餾分油引入旋液分離器中進(jìn)行分離,得到貧固含量組分的低密度餾分油和富固含量組分的高密度尾油;然后將所述低密度餾分油與所述第一輕質(zhì)餾分油引入固定床加氫處理裝置中進(jìn)行加氫反應(yīng),并將得到的加氫反應(yīng)產(chǎn)物進(jìn)行分餾,得到第二氣體、第二輕質(zhì)餾分油和加氫尾油;以及將所述高密度尾油循環(huán)回漿態(tài)床反應(yīng)器內(nèi)腔中。本發(fā)明的上述方法能夠高效地將包括脫油瀝青和/或高芳烴組分(乙烯焦油、催化裂化回?zé)捰图按呋鸦蜐{等)在內(nèi)的劣質(zhì)原料油轉(zhuǎn)化為輕質(zhì)餾分油。本發(fā)明的方法將漿態(tài)床反應(yīng)器和固定床渣油加氫處理裝置聯(lián)用,能夠避免固定床中催化劑失活和床層堵塞問題,因而能夠高效加工高金屬含量、高殘?zhí)恐岛透邽r青質(zhì)含量的脫油硬瀝青等劣質(zhì)物料,提高煉廠的整體輕質(zhì)餾分油收率,進(jìn)而提高其經(jīng)濟(jì)效益。本發(fā)明的其它特征和優(yōu)點(diǎn)將在隨后的具體實(shí)施方式部分予以詳細(xì)說明。附圖說明附圖是用來提供對(duì)本發(fā)明的進(jìn)一步理解,并且構(gòu)成說明書的一部分,與下面的具體實(shí)施方式一起用于解釋本發(fā)明,但并不構(gòu)成對(duì)本發(fā)明的限制。在 附圖中:圖1是本發(fā)明的一種優(yōu)選實(shí)施方式的旋液分離器的結(jié)構(gòu)示意圖。圖2是本發(fā)明的一種優(yōu)選實(shí)施方式的工藝流程圖。圖3是本發(fā)明的一種優(yōu)選實(shí)施方式的漿態(tài)床反應(yīng)器的結(jié)構(gòu)示意圖。附圖標(biāo)記說明1、反應(yīng)器殼體2、旋液分離器內(nèi)腔3、套筒4、旋液分離器入口5、氣相出口6、底流管7、氣體分布器8、反應(yīng)器內(nèi)腔9、出氣口10、產(chǎn)物油出口11、進(jìn)氣口12、卸劑口13、加劑口14、原料油入口15、出料口1a、劣質(zhì)原料油和加氫催化劑2a、加壓泵3a、換熱器4a、漿態(tài)床反應(yīng)器5a、第一熱高分6a、旋液分離器7a、待凈化氫氣8a、固定床加氫處理裝置9a、第二熱高分10a、蒸餾塔11a、高密度尾油12a、循環(huán)油13a、外甩油14a、循環(huán)氫15a、新鮮氫具體實(shí)施方式以下對(duì)本發(fā)明的具體實(shí)施方式進(jìn)行詳細(xì)說明。應(yīng)當(dāng)理解的是,此處所描述的具體實(shí)施方式僅用于說明和解釋本發(fā)明,并不用于限制本發(fā)明。本發(fā)明提供了一種劣質(zhì)原料油的輕質(zhì)化方法,該方法包括:將包括劣質(zhì)原料油、加氫催化劑和氫氣的反應(yīng)物料引入漿態(tài)床反應(yīng)器中進(jìn)行加氫裂化反應(yīng),得到加氫裂化混合物;將所述加氫裂化混合物進(jìn)行分離,得到第一氣體、第一輕質(zhì)餾分油和含有加氫催化劑的重質(zhì)餾分油;將所述重質(zhì)餾分油引入旋液分離器中進(jìn)行分離,得到貧固含量組分的低密度餾分油和富固含量組分的高密度尾油;然后將所述低密度餾分油與所述第一輕質(zhì)餾分油引入固定床加氫處理裝置中進(jìn)行加氫反應(yīng),并將得到的加氫反應(yīng)產(chǎn)物進(jìn)行分餾,得到第二氣體、第二輕質(zhì)餾分油和加氫尾油;以及將所述高密度尾油循環(huán)回漿態(tài)床反應(yīng)器內(nèi)腔中。在本發(fā)明中,在沒有特別說明的情況下,所述第一、第二等均是為了區(qū)分而不表示先后次序。本領(lǐng)域技術(shù)人員不應(yīng)理解為對(duì)本發(fā)明的技術(shù)方案的限制。在本發(fā)明中,所述反應(yīng)物料并不特指僅含有劣質(zhì)原料油、加氫催化劑和氫氣的物料,本文中的反應(yīng)物料泛指參與劣質(zhì)原料油輕質(zhì)化過程的所有物料,包括固相、氣相和液相物料,也包括反應(yīng)物、生成物等。優(yōu)選將劣質(zhì)原料油進(jìn)行加熱預(yù)處理后再引入所述漿態(tài)床反應(yīng)器中進(jìn)行加氫裂化反應(yīng)。所述加熱預(yù)處理是為了使得進(jìn)入所述漿態(tài)床反應(yīng)器中的反應(yīng)物流能夠更加高效地進(jìn)行加氫裂化反應(yīng)。優(yōu)選所述加熱預(yù)處理的條件包括溫度為320-380℃。本發(fā)明也可以將所述劣質(zhì)原料油與所述加氫催化劑提前進(jìn)行混合,形成均勻的漿液后再引入至所述漿態(tài)床反應(yīng)器中。將所述加氫裂化混合物進(jìn)行分離的方法可以有多種,本領(lǐng)域技術(shù)人員可以采用本領(lǐng)域內(nèi)常規(guī)使用的各種方法,只要能夠使得所述加氫裂化混合物進(jìn)行分離得到第一氣體、第一輕質(zhì)餾分油和含有加氫催化劑的重質(zhì)餾分油即可。例如,將所述加氫裂化混合物進(jìn)行分離的方法可以為引入熱高壓分離器 中進(jìn)行分離,所述熱高壓分離器分離優(yōu)選在溫度范圍為300-380℃的條件下進(jìn)行,壓力為10-30MPa。本發(fā)明的所述重質(zhì)餾分油中可以含有未轉(zhuǎn)化的尾油。優(yōu)選將得到的所述第一氣體進(jìn)行除雜提純及濃縮,并且將濃縮后得到的富氫氣體引入至后續(xù)的固定床加氫處理裝置中進(jìn)行加氫反應(yīng)。通過分離得到的所述重質(zhì)餾分油可以直接進(jìn)入旋液分離器分離,也可以先進(jìn)行降壓,在降壓后再進(jìn)入旋液分離器中進(jìn)行分離。優(yōu)選所述貧固含量組分的低密度餾分油中的固含量不高于0.5重量%;優(yōu)選所述富固含量組分的高密度尾油中的固含量范圍為5-50重量%,更優(yōu)選為10-40重量%。將所述第一輕質(zhì)餾分油與所述低密度餾分油混合后即可以得到漿態(tài)床加氫處理裝置的原料油,進(jìn)入后續(xù)的固定床加氫處理裝置,所述漿態(tài)床加氫處理裝置的原料油中固含量小于200ppm,Ni+V不大于80ppm,瀝青質(zhì)含量不大于5重量%。對(duì)所述固定床加氫處理裝置的種類沒有特別的限定,本領(lǐng)域技術(shù)人員能夠采用本領(lǐng)域內(nèi)常規(guī)使用的各種固定床加氫處理裝置。對(duì)所述固定床加氫處理裝置中進(jìn)行的加氫反應(yīng)的具體操作方法沒有特殊的限定,可以是本領(lǐng)域內(nèi)常規(guī)使用的各種具體操作方法。對(duì)將得到的加氫反應(yīng)產(chǎn)物進(jìn)行分餾的具體條件沒有特別的限定,只要能夠使得通過所述分餾得到第二氣體、第二輕質(zhì)餾分油和加氫尾油即可。本發(fā)明優(yōu)選所述第二輕質(zhì)餾分油和所述加氫尾油的切割點(diǎn)為330-380℃。所述漿態(tài)床反應(yīng)器內(nèi)腔是由漿態(tài)床反應(yīng)器殼體構(gòu)成的內(nèi)部空間。優(yōu)選氣體(氫氣)從位于漿態(tài)床反應(yīng)器殼體底部的進(jìn)氣口進(jìn)入漿態(tài)床反應(yīng)器內(nèi)腔的反應(yīng)物料中,引起反應(yīng)物料在漿態(tài)床反應(yīng)器內(nèi)腔中進(jìn)行相對(duì)運(yùn)動(dòng)從而有利于漿態(tài)床反應(yīng)器中反應(yīng)的進(jìn)行。優(yōu)選所述旋液分離器包括旋液分離器入口、旋液分離器內(nèi)腔、氣相出口、產(chǎn)物油出口和底流管。物料通過旋液分離器入口進(jìn)入旋液分離器內(nèi)腔中利用自身的離心力進(jìn)行分離,分離得到氣相物從所述氣相出口引出至所述旋液分離器之外,分離得到固含量較小的組分從位于旋液分離器上部的產(chǎn)物油出口引出至所述旋液分離器之外,分離得到的固含量較大的組分從位于旋液分離器下部的底流管引出至所述旋液分離器之外。根據(jù)本發(fā)明的一種優(yōu)選的具體實(shí)施方式,本發(fā)明所述的旋液分離器如圖1中所示,具體地:所述旋液分離器包括旋液分離器入口4、旋液分離器內(nèi)腔2、氣相出口5、產(chǎn)物油出口10和底流管6。物料通過旋液分離器入口4進(jìn)入旋液分離器內(nèi)腔2中利用自身的離心力進(jìn)行分離,分離得到氣相物從所述氣相出口5引出至所述旋液分離器之外,分離得到固含量較小的組分從位于旋液分離器上部的產(chǎn)物油出口10引出至所述旋液分離器之外,分離得到的固含量較大的組分從位于旋液分離器下部的底流管6引出至所述旋液分離器之外。優(yōu)選所述旋液分離器設(shè)置在所述漿態(tài)床反應(yīng)器內(nèi)腔以外,所述重質(zhì)餾分油從旋液分離器入口引入至旋液分離器內(nèi)腔中進(jìn)行分離,分離得到的所述低密度餾分油從旋液分離器的產(chǎn)物油出口引出至所述固定床加氫處理裝置中,分離得到的所述高密度尾油從所述旋液分離器下部的底流管引出,并且將所述高密度尾油循環(huán)回所述漿態(tài)床反應(yīng)器內(nèi)腔中,優(yōu)選地部分尾油外甩。所述漿態(tài)床反應(yīng)器為任意適用于漿態(tài)床重油加氫裂化的反應(yīng)器。優(yōu)選地,所述漿態(tài)床反應(yīng)器中設(shè)置有使得所述反應(yīng)物料在所述漿態(tài)床反應(yīng)器內(nèi)腔中進(jìn)行內(nèi)循環(huán)的套筒,所述套筒的下部通過內(nèi)徑小于所述套筒內(nèi)徑且伸入所述套筒內(nèi)部的導(dǎo)管與漿態(tài)床反應(yīng)器殼體上的進(jìn)氣口連通,所述氫氣通過所述進(jìn)氣口依次引入至所述導(dǎo)管和所述套筒中。通過設(shè)置所述套筒,并且氫氣從所述進(jìn)氣口進(jìn)入所述套筒內(nèi),使得套筒內(nèi)的反應(yīng)物料中的氣含量明顯比套筒 外的反應(yīng)物料中的氣含量要高,從而推動(dòng)套筒內(nèi)的反應(yīng)物料向上運(yùn)動(dòng),而套筒外的反應(yīng)物料相對(duì)向下運(yùn)動(dòng),如此在漿態(tài)床反應(yīng)器內(nèi)腔中形成內(nèi)循環(huán),促進(jìn)了反應(yīng)物料中氣、固、液三相之間的相互反應(yīng),從而能夠提高反應(yīng)效率。要求引導(dǎo)氫氣的所述導(dǎo)管的內(nèi)徑小于所述套筒的內(nèi)徑是為了使得所述漿態(tài)床反應(yīng)器內(nèi)腔中的反應(yīng)物料能夠從所述套筒的底部進(jìn)入所述套筒中。因此,本領(lǐng)域技術(shù)人員能夠據(jù)此確定所述導(dǎo)管和所述套筒的內(nèi)徑的比值。所述套筒為一根或至少兩根,至少兩根的所述套筒下部的所述導(dǎo)管與所述進(jìn)氣口之間設(shè)置有氣體分布器;所述氫氣通過所述進(jìn)氣口依次引入至所述氣體分布器、所述導(dǎo)管和所述套筒中。所述氣體分布器的設(shè)置是為了能夠使得進(jìn)入所述漿態(tài)床反應(yīng)器內(nèi)腔中的氫氣能夠更加均勻地分布,氫氣經(jīng)氣體分布器平均分配到每個(gè)內(nèi)置的套筒底部,在此處的氣體分布器將氫氣分散成小氣泡,每個(gè)套筒內(nèi)的氣泡均向上移動(dòng),使套筒內(nèi)的氣含量大于套筒外的氣含量。憑借套筒內(nèi)外流體密度的差異,在一定的垂直距離范圍內(nèi)形成壓差,該壓差推動(dòng)套筒外流體向下流動(dòng),在套筒內(nèi)流體向上流動(dòng),如此形成內(nèi)循環(huán)。從而有利于漿態(tài)床反應(yīng)器內(nèi)腔中反應(yīng)的高效進(jìn)行。優(yōu)選地,所述套筒的長(zhǎng)度為所述漿態(tài)床反應(yīng)器內(nèi)腔的長(zhǎng)度的2/5至4/5。所述漿態(tài)床反應(yīng)器內(nèi)腔的長(zhǎng)度與所述漿態(tài)床反應(yīng)器內(nèi)腔的內(nèi)徑之比可以為5-20:1;優(yōu)選為8-15:1。優(yōu)選地,所述漿態(tài)床反應(yīng)器內(nèi)腔的內(nèi)徑為50-6000mm,進(jìn)一步優(yōu)選為300-5000mm。優(yōu)選地,所述套筒的內(nèi)徑為所述漿態(tài)床反應(yīng)器內(nèi)腔的內(nèi)徑的1/100至3/4。優(yōu)選地,所述導(dǎo)管伸入所述套筒內(nèi)部的長(zhǎng)度為所述套筒的長(zhǎng)度的1/1000至1/10。根據(jù)本發(fā)明的一種優(yōu)選的具體實(shí)施方式,本發(fā)明所述的漿態(tài)床反應(yīng)器如 圖3中所示,具體地,該漿態(tài)床反應(yīng)器包括:反應(yīng)器殼體1,該反應(yīng)器殼體的下部設(shè)置有卸劑口12、進(jìn)氣口11和原料油入口14,該反應(yīng)器殼體的上部設(shè)置有出氣口9、加劑口13、出料口15;所述反應(yīng)器殼體1的內(nèi)部空間構(gòu)成反應(yīng)器內(nèi)腔8(本文中也可稱為漿態(tài)床反應(yīng)器內(nèi)腔)。該反應(yīng)器內(nèi)腔8的底部設(shè)置有使得反應(yīng)物料在所述反應(yīng)器內(nèi)腔8內(nèi)進(jìn)行內(nèi)循環(huán)的套筒3,所述套筒3的下部通過內(nèi)徑小于所述套筒內(nèi)徑且伸入所述套筒內(nèi)部的導(dǎo)管與所述反應(yīng)器殼體1的進(jìn)氣口11連通。并且,所述套筒3為1根或至少兩根,所述旋液分離器設(shè)置為1級(jí),套筒下部的所述導(dǎo)管與所述進(jìn)氣口11之間設(shè)置有氣體分布器7。優(yōu)選控制加氫裂化反應(yīng)的條件,使得所述重質(zhì)餾分油占漿態(tài)床反應(yīng)器進(jìn)料(即劣質(zhì)原料油)的40-60重量%。優(yōu)選所述重質(zhì)餾分油從旋液分離器入口沿切線方向進(jìn)入,流動(dòng)速率在5-15m/s之間,優(yōu)選在7-12m/s之間,在旋液分離器內(nèi)形成旋轉(zhuǎn)運(yùn)動(dòng),依靠離心力對(duì)所述重質(zhì)餾分油進(jìn)行分離。本發(fā)明的方法適用于本領(lǐng)域內(nèi)常規(guī)使用的加氫裂化反應(yīng)的條件,但是特別地,本發(fā)明的所述加氫裂化反應(yīng)的條件較緩和,優(yōu)選所述加氫裂化反應(yīng)的條件包括:壓力為10-30MPa;溫度為380-450℃;液時(shí)體積空速為0.1-2.0h-1,氫油體積比為200-5000。更加優(yōu)選所述加氫裂化反應(yīng)的條件包括:壓力為18-25MPa;溫度為410-440℃;液時(shí)體積空速為0.2-1.0h-1,氫油體積比為1000-2500。相對(duì)于每g所述劣質(zhì)原料油,以所述加氫催化劑中的金屬含量計(jì),所述加氫催化劑的用量可以為0.05-5重量%,優(yōu)選為0.1-3重量%。優(yōu)選地,第一方面,本發(fā)明所述加氫催化劑可以為高分散納米級(jí)負(fù)載型催化劑,所述加氫催化劑包括載體和金屬活性組分,所述金屬活性組分選自納米級(jí)的Mo、Ni、Co和V中的至少一種,所述載體為煤粉、活性炭、石墨 和炭黑中的至少一種碳基材料;優(yōu)選在所述加氫催化劑中,所述金屬活性組分的平均粒徑為10-100nm,優(yōu)選為20-50nm;更優(yōu)選在所述加氫催化劑中,所述載體的平均粒徑為20-200μm,優(yōu)選為50-120μm。根據(jù)所述第一方面,在所述加氫催化劑中,所述載體的比表面積為50-1000m2/g,優(yōu)選為300-800m2/g;優(yōu)選在所述加氫催化劑中,所述載體的孔徑為2-100nm,優(yōu)選為3-50nm;更加優(yōu)選所述加氫催化劑的載體的平均粒徑為60-100μm。優(yōu)選地,第二方面,本發(fā)明所述加氫催化劑中含有載體和活性金屬元素,所述載體包括氧化硅-氧化鋁和氧化鋁,所述活性金屬元素包括鐵、鈣和鉬,所述催化劑為微球型,且平均粒徑為20-200μm;優(yōu)選為50-120μm;更優(yōu)選為60-100μm。根據(jù)所述第二方面,以所述催化劑的總重量計(jì),所述活性金屬元素以氧化物計(jì)的含量為10-40重量%;優(yōu)選以所述加氫催化劑的總重量計(jì),鈣和鉬以氧化物計(jì)的含量分別為0.1-1重量%和5-10重量%。加氫催化劑的載體有豐富的孔結(jié)構(gòu)和較大的比表面積,一方面活性金屬可以在其表面得到高度分散,提高了加氫催化劑的反應(yīng)活性;另一方面,劣質(zhì)原料油中的瀝青質(zhì)和膠質(zhì)等大分子可以進(jìn)入載體孔道內(nèi)部,隨著加氫催化劑在反應(yīng)體系內(nèi)高度擴(kuò)散,阻止了生焦前驅(qū)體的聚集,減少了焦炭的生成。本發(fā)明的方法對(duì)所述加氫催化劑的制備方法沒有特別的限定,可以采用本領(lǐng)域內(nèi)常規(guī)使用的例如浸漬法等進(jìn)行制備,本發(fā)明在此不再贅述。加氫催化劑與劣質(zhì)原料油混合均勻后一起進(jìn)入漿態(tài)床反應(yīng)器進(jìn)行加氫 裂化反應(yīng),反應(yīng)系統(tǒng)平衡后,從所述旋液分離器底流管流出的高密度尾油部分外甩出反應(yīng)系統(tǒng),以一定速率除去漿態(tài)床反應(yīng)器加氫裂化反應(yīng)體系中的部分失活的加氫催化劑,同時(shí)按相同速率向原料中補(bǔ)充新鮮的加氫催化劑,使得所述漿態(tài)床反應(yīng)器中的催化劑含量保持在本發(fā)明的前述范圍內(nèi)。本發(fā)明的所述劣質(zhì)原料油的相對(duì)密度較大,膠質(zhì)及瀝青質(zhì)等大分子、硫氮雜原子及金屬含量高。在本發(fā)明中,優(yōu)選所述劣質(zhì)原料油為常減壓渣油、脫油瀝青、高芳烴油、重質(zhì)原油、超重質(zhì)原油、油砂、天然瀝青、頁巖油和煤焦油中的至少一種。更加優(yōu)選所述劣質(zhì)原料油為常減壓渣油、脫油瀝青、高芳烴油、重質(zhì)原油、超重質(zhì)原油、油砂、天然瀝青、頁巖油和煤焦油中的至少一種。更加優(yōu)選所述劣質(zhì)原料油為脫油瀝青和/或高芳烴油。特別優(yōu)選所述劣質(zhì)原料油為脫油瀝青和高芳烴油,所述脫油瀝青和所述高芳烴油的重量比可以為0.1-10:1。所述高芳烴油可以為乙烯焦油、催化裂化回?zé)捰图按呋鸦蜐{中的一種或幾種,初餾點(diǎn)>350℃,其中芳烴含量一般大于80重量%。優(yōu)選所述固定床加氫處理裝置中含有加氫處理催化劑,所述加氫處理催化劑是指具有渣油加氫脫金屬、加氫脫硫、加氫脫氮和加氫裂化功能的催化劑系列。優(yōu)選所述加氫處理催化劑包括作為載體的多孔氧化鋁和負(fù)載在所述載體上的選自第VIB族、第VIIB族和第VIII族中的至少一種活性金屬元素。具體地,所述加氫處理催化劑中的活性金屬元素可以為鉬、鎢、鈷、鎳中的一種或多種,所述加氫處理催化劑的級(jí)配方法優(yōu)選使得所述固定床加氫處理裝置中的反應(yīng)物流依次通過加氫脫金屬催化劑、加氫脫硫催化劑、加氫脫氮催化劑和加氫裂化催化劑。在具體的實(shí)施方式中,本領(lǐng)域技術(shù)人員能夠根據(jù)原料油的性質(zhì)和漿態(tài)床 反應(yīng)器的加氫結(jié)果,調(diào)整固定床加氫處理裝置中的工藝條件和其中的加氫處理催化劑的裝填量及級(jí)配方式。優(yōu)選所述固定床加氫處理裝置中進(jìn)行加氫反應(yīng)的條件包括:氫分壓為8-15MPa;溫度為350-410℃;液時(shí)體積空速為0.2-1.0h-1;氫油體積比為200-1000。本發(fā)明中將得到的加氫反應(yīng)產(chǎn)物進(jìn)行分餾中所得到的第二輕質(zhì)餾分油優(yōu)選包括汽油餾分和柴油餾分。更優(yōu)選所述汽油餾分和所述柴油餾分的切割點(diǎn)為180℃。特別地,所述加氫尾油與所述第二輕質(zhì)餾分油的切割點(diǎn)可以為350℃。根據(jù)本發(fā)明的一種優(yōu)選的具體實(shí)施方式,本發(fā)明的所述劣質(zhì)原料油的輕質(zhì)化方法按照?qǐng)D2所示的工藝流程圖進(jìn)行,具體地:將包括劣質(zhì)原料油和加氫催化劑1a的反應(yīng)物料依次通過加壓泵2a和換熱器3a引入漿態(tài)床反應(yīng)器4a中進(jìn)行加氫裂化反應(yīng),得到加氫裂化混合物;將所述加氫裂化混合物引入第一熱高分5a中進(jìn)行分離,得到第一氣體、第一輕質(zhì)餾分油和含有加氫催化劑的重質(zhì)餾分油;將所述重質(zhì)餾分油引入旋液分離器6a中進(jìn)行分離,得到貧固含量組分的低密度餾分油和富固含量組分的高密度尾油11a,并且得到富含氫氣的待凈化氫氣7a,所述待凈化氫氣7a經(jīng)分離除雜后作為循環(huán)氫14a與新鮮氫15a循環(huán)回反應(yīng)體系中;然后將所述低密度餾分油與所述第一輕質(zhì)餾分油引入固定床加氫處理裝置8a中進(jìn)行加氫反應(yīng),并將得到的加氫反應(yīng)產(chǎn)物依次引入第二熱高分9a中進(jìn)行分離以及引入蒸餾塔10a中進(jìn)行分餾,得到第二氣體、第二輕質(zhì)餾分油和加氫尾油;以及將所述高密度尾油的一部分作為循環(huán)油12a循環(huán)回漿態(tài)床反應(yīng)器內(nèi)腔中,并且將剩余部分的高密度尾油作為外甩油13a進(jìn)行外甩。具體地,本發(fā)明的方法具有如下優(yōu)點(diǎn):1、采用漿態(tài)床反應(yīng)器緩和加氫工藝,可以將脫油瀝青、催化裂化油漿、 催化裂化回?zé)捰图耙蚁┙褂偷攘淤|(zhì)原料油中的金屬和/或?yàn)r青質(zhì)脫去,使其滿足了固定床渣油加氫進(jìn)料的要求,擴(kuò)大了固定床渣油加氫的原料來源;2、脫油瀝青是一個(gè)復(fù)雜的膠溶體系,與普通減壓渣油相比,其中的瀝青質(zhì)等分散相分子稠合度更高,極性更強(qiáng),含量更多,而膠質(zhì)等連續(xù)相含量較低,因而具有更強(qiáng)的結(jié)焦傾向;高芳烴油的引入,一方面可以其解決高效加工問題,更重要的是提高了脫油瀝青體系的相對(duì)穩(wěn)定性,防止生焦前驅(qū)體的生存,從而有效抑制了漿態(tài)床反應(yīng)器加氫過程中焦炭的生成,延長(zhǎng)了裝置的連續(xù)運(yùn)轉(zhuǎn)周期;3、漿態(tài)床反應(yīng)器加氫過程采用緩和的操作條件,僅脫去進(jìn)料中的金屬和瀝青質(zhì),而不追求裂化轉(zhuǎn)化率,從而減少了漿態(tài)床反應(yīng)器過程中焦炭的生成,保證了重質(zhì)餾分油的性質(zhì);4、漿態(tài)床反應(yīng)器中可以使用來自固定床加氫處理裝置中的廢加氫處理催化劑,有利于降低裝置的操作成本,增加經(jīng)濟(jì)效益;5、重質(zhì)餾分油采用旋液分離器進(jìn)行分離,保證絕大部分加氫催化劑進(jìn)入高密度尾油中,避免其進(jìn)入固定床加氫處理裝置而造成的床層堵塞問題;6、本發(fā)明通過將高密度尾油在漿態(tài)床加氫處理裝置中的循環(huán),實(shí)現(xiàn)了劣質(zhì)原料的全轉(zhuǎn)化,除外排少量廢渣外,不產(chǎn)生難以處理的劣質(zhì)尾油,具有資源利用率高、環(huán)境友好的優(yōu)點(diǎn)。以下將通過實(shí)施例對(duì)本發(fā)明進(jìn)行詳細(xì)描述。選用脫油瀝青A和鎮(zhèn)海催化裂化油漿作為劣質(zhì)原料油,具體的性質(zhì)如表1中所示。在未作相反說明的情況下,使用的氣體和液體的體積數(shù)值均為25℃和1個(gè)標(biāo)準(zhǔn)大氣壓下的數(shù)值。表1脫油瀝青A鎮(zhèn)海油漿軟化點(diǎn)/℃165—(殘?zhí)?/重量%469.68(瀝青質(zhì))/重量%41.94.1(S)/重量%10.91.0(N)/重量%0.290.22(Ni+V)/(μg/g)43019.8實(shí)施例1-7用于說明本發(fā)明的劣質(zhì)原料油的輕質(zhì)化方法。實(shí)施例1-3實(shí)施例1-3中使用的加氫催化劑相同,為Mo系負(fù)載型催化劑,具體的組成為:以活性金屬計(jì),Mo(平均粒徑為45nm)含量為10重量%,其余為載體活性炭,加氫催化劑的平均粒徑為100μm。相對(duì)于每g所述劣質(zhì)原料油,以所述加氫催化劑中的金屬含量計(jì),所述加氫催化劑的用量如表2中所示。實(shí)施例1-3中使用的劣質(zhì)原料油相同,均為重量比為7:3的脫油瀝青A與鎮(zhèn)海催化裂化油漿。實(shí)施例1-3中實(shí)驗(yàn)所用的固定床加氫處理裝置為單反應(yīng)器小型固定床加氫裝置,依次裝填保護(hù)催化劑、脫金屬催化劑、脫硫催化劑和脫氮催化劑,所用的加氫處理催化劑的牌號(hào)依次為RG-20A、RDM-2B、RMS-1和RSN-2,均由中石化長(zhǎng)嶺催化劑廠生產(chǎn);4種催化劑的裝填體積比為5:30:20:45。實(shí)施例1-3的具體方法為:將前述劣質(zhì)原料油、加氫催化劑和氫氣引入漿態(tài)床反應(yīng)器中進(jìn)行加氫裂 化反應(yīng),加氫裂化反應(yīng)條件如表2中所示,得到加氫裂化混合物;將所述加氫裂化混合物在溫度為300℃、壓力為20MPa條件下進(jìn)行閃蒸分離,得到第一氣體、第一輕質(zhì)餾分油和含有加氫催化劑的重質(zhì)餾分油,將所述重質(zhì)餾分油引入旋液分離器中進(jìn)行分離,得到貧固含量組分的低密度餾分油和富固含量組分的高密度尾油,其中,所述重質(zhì)餾分油在旋液分離器入口處的速率V、低密度餾分油的固含量和高密度尾油的固含量分別如表2中所示;然后將所述低密度餾分油與第一輕質(zhì)餾分油作為固定床加氫處理裝置原料油引入固定床加氫處理裝置中進(jìn)行加氫反應(yīng),所述固定床加氫處理裝置原料油的性質(zhì)見表3,加氫反應(yīng)的條件如表4中所示,并將得到的加氫反應(yīng)產(chǎn)物進(jìn)行分餾,得到第二氣體、第二輕質(zhì)餾分油和加氫尾油;以及將所述高密度尾油循環(huán)回漿態(tài)床反應(yīng)器內(nèi)腔中。實(shí)施例1-3中使用的漿態(tài)床反應(yīng)器和旋液分離器均分別相同,且結(jié)構(gòu)分別如圖3和圖1中所示。具體地,套筒的長(zhǎng)度為漿態(tài)床反應(yīng)器內(nèi)腔的長(zhǎng)度的3/5;套筒的內(nèi)徑為300mm。反應(yīng)器內(nèi)腔的內(nèi)徑為5000mm。所述導(dǎo)管伸入所述套筒內(nèi)部的長(zhǎng)度為200mm。底流管的長(zhǎng)度為100mm。所述漿態(tài)床反應(yīng)器內(nèi)腔的長(zhǎng)度與所述漿態(tài)床反應(yīng)器內(nèi)腔的內(nèi)徑之比為10:1。旋液分離器的容積與漿態(tài)床反應(yīng)器內(nèi)腔的容積之比為1:600。漿態(tài)床反應(yīng)器內(nèi)腔中的反應(yīng)物料在套筒外的向下流動(dòng)的平均速率為0.2m/s。所述反應(yīng)物料在經(jīng)過所述旋液分離器的入口時(shí)的速率為8m/s。表2表3實(shí)施例1實(shí)施例2實(shí)施例3密度(20℃)/(g/cm3)0.9580.9530.940(殘?zhí)?/重量%8.27.76.4(S)/重量%3.12.91.8(N)/重量%0.120.080.06(Ni+V)/(μg/g)54.048.230.7(四組分)/重量%飽和烴18.618.726.4芳烴57.459.660.4膠質(zhì)19.217.514.2瀝青質(zhì)4.84.22.8表4實(shí)施例1實(shí)施例2實(shí)施例3反應(yīng)條件壓力/MPa1514.015溫度/℃390400400液時(shí)體積空速/h-10.20.20.5氫油體積比600800600產(chǎn)品分布/重量%第二氣體(C1-C4)1.212.830.85汽油餾分(C5-180℃)13.0114.112.78柴油餾分(180-350℃)17.8819.8815.35加氫尾油(>350℃)68.5764.5971.98加氫尾油的性質(zhì)(Ni+V)/(μg/g)19.6813.4211.52(殘?zhí)?/重量%4.423.453.55實(shí)施例4-5實(shí)施例4-5采用與實(shí)施例2相同的方法進(jìn)行加氫裂化反應(yīng),所不同的是,在所述固定床加氫處理裝置中的反應(yīng)溫度與實(shí)施例2中不相同,具體如表5中所示。表5實(shí)施例4實(shí)施例5反應(yīng)條件壓力/MPa14.014.0溫度/℃390410液時(shí)體積空速/h-10.20.2氫油體積比800800產(chǎn)品分布/重量%第二氣體(C1-C4)2.183.24汽油餾分(C5-180℃)13.416.35柴油餾分(180-350℃)18.5821.42加氫尾油(>350℃)66.4860.73加氫尾油性質(zhì)(Ni+V)/(μg/g)18.139.52(殘?zhí)?/重量%4.293.17從實(shí)施例2、實(shí)施例4和實(shí)施例5的結(jié)果可以看出隨著反應(yīng)溫度的升高,加氫尾油收率降低,同時(shí)加氫尾油的性質(zhì)變好,可以作為優(yōu)質(zhì)的重油催化裂化原料。實(shí)施例6-7本實(shí)施例采用與實(shí)施例1相同的劣質(zhì)原料油和裝置進(jìn)行加氫裂化反應(yīng),所不同的是,使用的加氫催化劑的平均粒徑為80μm,且其中活性組分以氧化物計(jì)的含量相對(duì)于所述加氫催化劑的總重量分別為Fe:25重量%,Mo:10重量%,Ca:1重量%。具體的反應(yīng)條件如表6中所示。表6實(shí)施例6實(shí)施例7反應(yīng)條件壓力/MPa1818溫度/℃430440加氫催化劑用量/μg/g20002000液時(shí)體積空速/h-10.20.2氫油體積比15001500反應(yīng)結(jié)果/重量%第一氣體收率8.078.45漿態(tài)床生成油收率81.2983.54高密度尾油收率10.517.96焦炭收率1.431.85V/m/s88固含量低密度餾分油/μg/g25.6823.15高密度尾油/重量%7.610.03對(duì)比例1-3對(duì)比例1-3的加氫裂化反應(yīng)分別與實(shí)施例1-3的加氫裂化反應(yīng)條件對(duì)應(yīng)相同,且劣質(zhì)原料油相同,對(duì)比例1-3分別采用與實(shí)施例1-3相同的漿態(tài)床 反應(yīng)器進(jìn)行加氫裂化反應(yīng),并對(duì)漿態(tài)床反應(yīng)器反應(yīng)后獲得的液相產(chǎn)物進(jìn)行蒸餾切割,而不采用本發(fā)明所述的旋液分離器進(jìn)行分離,蒸餾切割獲得的產(chǎn)品餾分油的性質(zhì)見表7。雖然產(chǎn)品餾分油能夠滿足固定床進(jìn)料的要求,但和產(chǎn)品的收率均較低,增加了漿態(tài)床反應(yīng)器的負(fù)荷,也增加了生產(chǎn)成本。其中表7中的所述餾分油收率是指能夠進(jìn)入后續(xù)的固定床加氫加氫處理裝置的油相的收率。表7對(duì)比例1對(duì)比例2對(duì)比例3反應(yīng)條件壓力/MPa182022溫度/℃420420420加氫催化劑用量/μg/g80010002000液時(shí)體積空速/h-10.20.51.5氫油體積比150015002000反應(yīng)結(jié)果/重量%氣體收率(C1-C4)6.028.075.43餾分油收率(IBP-500℃)69.0572.2976.45渣油收率24.2619.7119.74焦炭收率1.621.430.78從上述結(jié)果可以看出,采用本發(fā)明提供的上述方法能夠高效地將包括脫油瀝青和/或高芳烴組分(乙烯焦油、催化裂化回?zé)捰图按呋鸦蜐{等)在內(nèi)的劣質(zhì)原料油轉(zhuǎn)化為輕質(zhì)餾分油。以上詳細(xì)描述了本發(fā)明的優(yōu)選實(shí)施方式,但是,本發(fā)明并不限于上述實(shí)施方式中的具體細(xì)節(jié),在本發(fā)明的技術(shù)構(gòu)思范圍內(nèi),可以對(duì)本發(fā)明的技術(shù)方案進(jìn)行多種簡(jiǎn)單變型,這些簡(jiǎn)單變型均屬于本發(fā)明的保護(hù)范圍。另外需要說明的是,在上述具體實(shí)施方式中所描述的各個(gè)具體技術(shù)特征,在不矛盾的情況下,可以通過任何合適的方式進(jìn)行組合,為了避免不必要的重復(fù),本發(fā)明對(duì)各種可能的組合方式不再另行說明。此外,本發(fā)明的各種不同的實(shí)施方式之間也可以進(jìn)行任意組合,只要其不違背本發(fā)明的思想,其同樣應(yīng)當(dāng)視為本發(fā)明所公開的內(nèi)容。當(dāng)前第1頁1 2 3