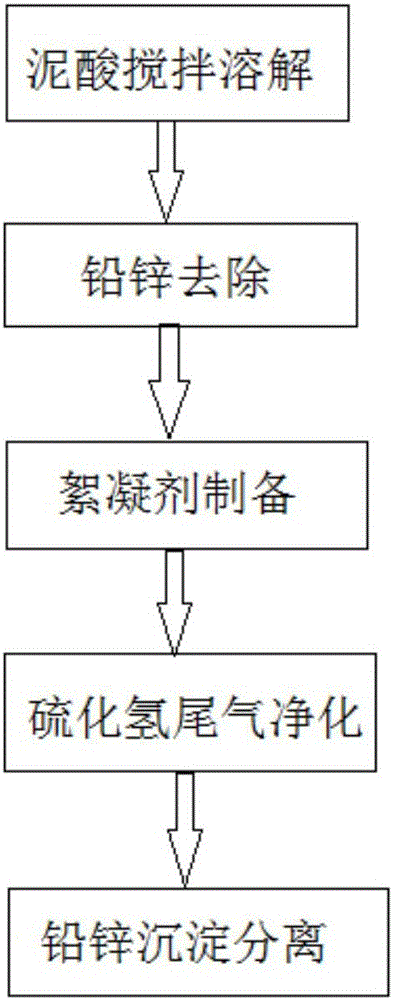
本發(fā)明屬于環(huán)境保護(hù)中固體危險(xiǎn)廢棄物資源化領(lǐng)域和廢水處理領(lǐng)域,具體地說(shuō),涉及一種鋼絲繩酸洗廢酸和含高鋅、鉛污泥共處置系統(tǒng)及工藝,是將鋼絲繩企業(yè)酸洗工藝產(chǎn)生的廢酸和生產(chǎn)過(guò)程中產(chǎn)生的高鋅、鉛污泥作為原料,制備具有附加值的工業(yè)產(chǎn)品的資源化共處置工藝。
背景技術(shù):
:鋼絲繩是至少由兩層鋼絲或多個(gè)股圍繞一個(gè)中心或一個(gè)繩芯螺旋捻制而成的結(jié)構(gòu),其表面在生產(chǎn)過(guò)程中生成的氧化鐵皮層需要用酸洗方法去除。目前國(guó)內(nèi)鋼絲繩企業(yè)以鹽酸酸洗為主,當(dāng)鹽酸液濃度降至10%以下,酸洗效果顯著下降達(dá)不到使用要求時(shí)需要被廢棄處理。鋼絲繩酸洗廢酸酸性強(qiáng)(pH<0)、含大量有毒有害重金屬元素(鉛、鋅等),按照國(guó)家環(huán)境保護(hù)排放要求不能直接排放,易引起嚴(yán)重的二次污染,已被國(guó)家列入危險(xiǎn)廢物進(jìn)行管理。鋼絲繩酸洗、磷化生產(chǎn)工藝還會(huì)產(chǎn)生大量含高鋅、鉛的酸性廢水,目前廣泛采用加入堿性沉淀劑的方法,通過(guò)中和作用形成含高鋅、鉛的污泥,從而去除鋅、鉛等有害雜質(zhì),使酸性廢水達(dá)到排放標(biāo)準(zhǔn)。高鋅、鉛污泥中含水率通常在80%以上,根據(jù)環(huán)境保護(hù)部HJ/T299固體廢物浸出毒性方法確定高鋅、鉛污泥屬于危險(xiǎn)廢物,不能直接傾倒或者填埋。因此,現(xiàn)在大部分鋼絲繩企業(yè)將高鋅、鉛污泥堆放在廠(chǎng)區(qū)內(nèi),這樣不僅占用大量的空間,還會(huì)引起廠(chǎng)區(qū)土壤重金屬污染,當(dāng)降水時(shí),污泥中的鋅、鉛會(huì)隨雨水遷移,從而造成水體污染。目前,鋼絲繩生產(chǎn)廠(chǎng)家通常是將酸洗廢酸與含高鋅、鉛污泥分別進(jìn)行單獨(dú)處理。其中,鋼絲繩酸洗廢酸的處理思路主要有兩種:第一種是將鋼絲繩酸洗廢酸當(dāng)作廢水進(jìn)行處理,向廢酸中加入堿性物料沉淀鉛、鋅后直接排放廢水。這種方法會(huì)產(chǎn)生大量含鋅、鉛的沉淀物,屬于危險(xiǎn)廢物,還需將其進(jìn)一步處置,成本高昂。第二種包括焙燒法、蒸餾結(jié)晶法、置換法等,其目的在于回收廢酸中的鹽酸和鐵元素,但因?yàn)榇嬖谶\(yùn)行成本高、產(chǎn)品質(zhì)量差、能耗大等缺點(diǎn)而無(wú)法運(yùn)用在實(shí)際操作中。鋼絲繩企業(yè)產(chǎn)生的高鋅、鉛污泥的處理也主要有兩種方法:第一種是水泥固化法,第二種是高溫氣化除鉛法,這兩種方法運(yùn)行成本均較高,需要占用填埋場(chǎng)地,且沒(méi)有對(duì)污泥中的金屬元素進(jìn)行資源化處置,從而造成大量金屬元素的浪費(fèi)。此外,將酸洗廢酸與含高鋅、鉛污泥分別進(jìn)行單獨(dú)處理還會(huì)大大增加生產(chǎn)廠(chǎng)家的勞動(dòng)強(qiáng)度,提高其處理成本。因此,如何實(shí)現(xiàn)鋼絲繩酸洗廢酸及鋼絲繩生產(chǎn)過(guò)程中產(chǎn)生的含高鋅、鉛污泥的高效處理、實(shí)現(xiàn)資源化、降低處理成本一直是困擾鋼絲繩生產(chǎn)廠(chǎng)家的一個(gè)重大難題。經(jīng)檢索,目前關(guān)于將鋼絲繩酸洗廢酸和高鋅、鉛污泥資源化共處置的研究還較少。其中,CN104843957A公開(kāi)了一種對(duì)鋼絲繩加工中產(chǎn)生的廢鹽酸和堿性污泥進(jìn)行綜合處理的方法,該申請(qǐng)案是將鋼絲繩加工過(guò)程中產(chǎn)生的廢鹽酸加入到鋼絲繩加工過(guò)程中產(chǎn)生的堿性污泥中,進(jìn)行攪拌使其充分反應(yīng),然后再除去不溶物的共處置方法,但其并沒(méi)有真正實(shí)現(xiàn)酸洗廢酸和污泥的資源化利用,只是簡(jiǎn)單的機(jī)械攪拌混合,處理后的最終產(chǎn)物是含高鋅、鉛的廢液,仍屬于危險(xiǎn)廢物,還需要經(jīng)過(guò)進(jìn)一步的深度處理才能進(jìn)行排放。又如,CN105271436A公開(kāi)了一種利用鋼絲繩污泥和廢鹽制備聚合氯化鐵絮凝劑的方法,該申請(qǐng)案是采用硫化物沉淀去除鉛離子,硫化氫氣體經(jīng)過(guò)降膜吸收、填料塔吸收和活性炭吸收處理,污泥殘?jiān)尤胨喙袒?,然后利用污泥中回收的鐵來(lái)制備絮凝劑。該申請(qǐng)案未考慮鋅元素的去除,但是目前鋼絲繩企業(yè)的生產(chǎn)廢酸液及污泥中鋅含量極高(>40000mg/L),需要將鋅元素除去才可以達(dá)標(biāo)排放,同時(shí)也沒(méi)有考慮硫化沉淀產(chǎn)物的處理,需要進(jìn)一步處理才能實(shí)現(xiàn)資源化利用。此外,該申請(qǐng)案在制取絮凝劑時(shí)加入堿溶液,最終所得絮凝劑的質(zhì)量相對(duì)較差,有待進(jìn)一步提高。技術(shù)實(shí)現(xiàn)要素:1.發(fā)明要解決的技術(shù)問(wèn)題本發(fā)明的目的在于克服目前鋼絲繩生產(chǎn)廠(chǎng)家處理酸洗廢酸及含高鋅、鉛污泥時(shí)存在的以上不足,提供了一種鋼絲繩酸洗廢酸和含高鋅、鉛污泥共處置系統(tǒng)及工藝。采用本發(fā)明的技術(shù)方案既可以實(shí)現(xiàn)鋼絲繩酸洗廢酸和高鋅、鉛污泥的共處置,能夠有效徹底去除鋅、鉛元素,實(shí)現(xiàn)危險(xiǎn)廢物的減量化,同時(shí)又可以克服傳統(tǒng)工藝的缺點(diǎn),制備具有較高附加值的工業(yè)產(chǎn)品,實(shí)現(xiàn)了資源化,給企業(yè)帶來(lái)了較大的利潤(rùn)。2.技術(shù)方案為達(dá)到上述目的,本發(fā)明提供的技術(shù)方案為:本發(fā)明的一種鋼絲繩酸洗廢酸和含高鋅、鉛污泥共處置系統(tǒng),包括泥酸攪拌溶解裝置、鉛鋅去除裝置、絮凝劑制取裝置、硫化氫吸收裝置和鉛鋅沉淀分離裝置,其中,所述的泥酸攪拌溶解裝置通過(guò)管道與鉛鋅去除裝置相連,該鉛鋅去除裝置通過(guò)管道分別與絮凝劑制取裝置、硫化氫吸收裝置及鉛鋅沉淀分離裝置相連。更進(jìn)一步的,所述的硫化氫吸收裝置包括依次相連的硫化氫吸收塔A、硫化氫吸收塔B和硫化氫吸收塔C,所述的硫化氫吸收塔A通過(guò)管道與鉛鋅去除裝置的排氣口相連,且硫化氫吸收塔B及硫化氫吸收塔C之間的管道上設(shè)有硫化氫泄漏報(bào)警器。更進(jìn)一步的,所述的鉛鋅沉淀分離裝置包括鉛鋅沉淀分離裝置A和鉛鋅沉淀分離裝置B,鉛鋅沉淀分離裝置A和鉛鋅沉淀分離裝置B均通過(guò)管道與鉛鋅去除裝置的污泥排放口相連,且鉛鋅沉淀分離裝置A及鉛鋅沉淀分離裝置B與鉛鋅去除裝置相連的管道上分別設(shè)有閥門(mén)A、閥門(mén)B。本發(fā)明的一種鋼絲繩酸洗廢酸和含高鋅、鉛污泥共處置工藝,其步驟為:A、泥酸攪拌溶解:將待處理污泥投加到泥酸攪拌溶解裝置中,然后向其中繼續(xù)投加廢酸液,經(jīng)攪拌充分反應(yīng)并靜置后將上清液抽至鉛鋅去除裝置中;B、鉛鋅去除:檢測(cè)溶解污泥后酸液中的鉛、鋅含量,向鉛鋅去除裝置中投加硫化物,攪拌反應(yīng)30-60min,過(guò)濾去除反應(yīng)產(chǎn)生的沉淀物并將上清液提升至絮凝劑制取裝置,同時(shí)將產(chǎn)生的硫化氫氣體通入硫化氫吸收裝置;C、制備聚鐵絮凝劑:檢測(cè)通入絮凝劑制取裝置的溶液中Fe2+和Fe3+的含量,并根據(jù)其含量配置氧化劑和堿液的混合液,其中,氧化劑與Fe2+的摩爾比為1:6,OH-與Fe3+的摩爾比為1-3:1,將上述混合液加入絮凝劑制取裝置進(jìn)行攪拌反應(yīng),反應(yīng)結(jié)束后經(jīng)成化處理即制成了聚鐵絮凝劑;D、硫化氫尾氣凈化:將通入硫化氫吸收裝置內(nèi)的硫化氫氣體使用飽和堿液進(jìn)行吸收,并將充分吸收了硫化氫的堿液回用到步驟B中;E、鉛鋅沉淀分離:使步驟B產(chǎn)生的鉛、鋅混合沉淀物質(zhì)進(jìn)入鉛鋅沉淀分離裝置,使用質(zhì)量濃度為30%-70%的醋酸鉛溶液進(jìn)行反應(yīng)分離,得到純度為99%以上的硫化鉛固體及符合工業(yè)純度的醋酸鋅固體。更進(jìn)一步的,所述步驟A中污泥的投加量為投加至泥酸攪拌溶解裝置的1/5-1/2體積處,廢酸液與污泥的體積比為1-10:1,且攪拌反應(yīng)時(shí)間為1-4小時(shí),靜置時(shí)間為1-5h。更進(jìn)一步的,所述步驟A中將上清液抽至鉛鋅去除裝置后向泥酸攪拌溶解裝置中繼續(xù)補(bǔ)充污泥,然后加入酸液進(jìn)行第二次污泥廢酸混合溶解,以此類(lèi)推,將經(jīng)多次反應(yīng)后底部沉淀的不溶性物質(zhì)水洗后當(dāng)作固體廢物直接填埋。更進(jìn)一步的,所述步驟B中鉛、鋅總摩爾數(shù)與硫化物的摩爾數(shù)之比,即n(鉛+鋅):n(硫化物)=1:2-3,且所述硫化物為硫化鈉、硫化鉀、硫化鈣、硫氫化鈉的一種或多種。更進(jìn)一步的,所述步驟C中的氧化劑為氯酸鈉和氯酸鉀中的一種或兩種的混合,堿液為氫氧化鈉、氫氧化鉀和氫氧化鈣溶液中的一種或一種以上的混合,且攪拌反應(yīng)的攪拌轉(zhuǎn)速為50-500r/min,攪拌反應(yīng)時(shí)間為45-120min,成化處理的時(shí)間為20-30h,且成化處理后蒸發(fā)10%-50%水分即制成聚鐵絮凝劑。更進(jìn)一步的,所述步驟D中硫化氫氣體先通入硫化氫吸收塔A進(jìn)行吸收處理,然后通入硫化氫吸收塔B中進(jìn)行二次吸收,經(jīng)二次吸收后的硫化氫氣體經(jīng)過(guò)硫化氫泄漏報(bào)警器,若報(bào)警器不報(bào)警則通過(guò)硫化氫吸收塔C直接排出;若報(bào)警器報(bào)警監(jiān)測(cè)到硫化氫氣體泄漏后,對(duì)硫化氫吸收塔B及硫化氫吸收塔C內(nèi)的堿液進(jìn)行更換,并將吸收了硫化氫的堿液回用到步驟B中;上述硫化氫吸收塔中的堿液為氫氧化鈉、氫氧化鉀及氫氧化鈣溶液中的一種或一種以上的混合。更進(jìn)一步的,所述步驟E中先打開(kāi)鉛鋅沉淀分離裝置A與鉛鋅去除裝置之間管道上的閥門(mén)A,關(guān)閉鉛鋅沉淀分離裝置B與鉛鋅去除裝置之間管道上的閥門(mén)B,將鉛、鋅混合沉淀物投加進(jìn)鉛鋅沉淀分離裝置A中,在250-500r/min的轉(zhuǎn)速下反應(yīng)30-45min并靜置30-60分鐘后將沉淀物轉(zhuǎn)移至鉛鋅沉淀分離裝置B中,在250-500r/min的轉(zhuǎn)速下反應(yīng)30-45min并靜置30-60分鐘后取出沉淀物即為純度為99%以上的硫化鉛固體;多次反應(yīng)后檢測(cè)鉛鋅沉淀分離裝置B中醋酸鉛的濃度低于0.5%時(shí)取出蒸發(fā)結(jié)晶得到符合工業(yè)純度的醋酸鋅固體;此后打開(kāi)閥門(mén)B,關(guān)閉閥門(mén)A,將鉛鋅沉淀分離裝置B作為第一次反應(yīng)的裝置,向鉛鋅沉淀分離裝置A中補(bǔ)充新的醋酸鉛溶液作為第二次反應(yīng)的裝置,依次往復(fù)進(jìn)行。3.有益效果采用本發(fā)明提供的技術(shù)方案,與現(xiàn)有技術(shù)相比,具有如下顯著效果:(1)本發(fā)明的一種鋼絲繩酸洗廢酸和含高鋅、鉛污泥共處置系統(tǒng),包括泥酸攪拌溶解裝置、鉛鋅去除裝置、絮凝劑制取裝置、硫化氫吸收裝置和鉛鋅沉淀分離裝置,其中,泥酸攪拌溶解裝置用于對(duì)待處理污泥與廢酸液進(jìn)行混合攪拌溶解,鉛鋅去除裝置用于去除溶解污泥后酸液中的鉛、鋅,通過(guò)硫化氫吸收裝置對(duì)鉛鋅去除裝置中產(chǎn)生的硫化氫氣體進(jìn)行吸收處理,防止直接排放污染環(huán)境,同時(shí)硫化氫吸收裝置中產(chǎn)生的硫化物能夠通入鉛鋅去除裝置進(jìn)行循環(huán)使用,有利于節(jié)約資源。鉛鋅去除裝置中產(chǎn)生的上清液進(jìn)入絮凝劑制取裝置用于制取絮凝劑,而通過(guò)鉛鋅沉淀分離裝置的設(shè)置能夠?qū)︺U鋅去除裝置中產(chǎn)生的鉛、鋅混合沉淀物進(jìn)行分離反應(yīng),制備純度較高的硫化鉛和醋酸鋅工業(yè)產(chǎn)品,實(shí)現(xiàn)了資源化利用。采用本發(fā)明的系統(tǒng)能夠有效實(shí)現(xiàn)鋼絲繩酸洗廢酸和含高鋅、鉛污泥的資源化共處置,減少環(huán)境污染,且工藝操作簡(jiǎn)單,能夠進(jìn)行自動(dòng)化控制。(2)本發(fā)明的一種鋼絲繩酸洗廢酸和含高鋅、鉛污泥共處置系統(tǒng),所述的硫化氫吸收裝置包括依次相連的硫化氫吸收塔A、硫化氫吸收塔B和硫化氫吸收塔C,通過(guò)三級(jí)吸收塔的設(shè)置可以有效保證硫化氫的充分吸收,進(jìn)一步減少環(huán)境污染。由于硫化氫吸收塔B及硫化氫吸收塔C之間的管道上設(shè)有硫化氫泄漏報(bào)警器,從而可以對(duì)排放氣體中所含硫化氫進(jìn)行監(jiān)測(cè),保證硫化氫的完全吸收,防止硫化氫的泄漏。(3)本發(fā)明的一種鋼絲繩酸洗廢酸和含高鋅、鉛污泥共處置系統(tǒng),其鉛鋅沉淀分離裝置包括鉛鋅沉淀分離裝置A和鉛鋅沉淀分離裝置B,通過(guò)鉛鋅沉淀分離裝置A和鉛鋅沉淀分離裝置B的配合能夠?qū)崿F(xiàn)鉛鋅沉淀的有效分離,保證所得分離產(chǎn)物的純度。(4)本發(fā)明的一種鋼絲繩酸洗廢酸和含高鋅、鉛污泥共處置工藝,通過(guò)泥酸攪拌溶解、鉛鋅去除、聚鐵絮凝劑的制備、硫化氫尾氣的凈化及鉛鋅沉淀分離實(shí)現(xiàn)了鋼絲繩酸洗廢酸和含高鋅、鉛污泥的資源化共處置,并通過(guò)對(duì)以上各工序的工序過(guò)程及工藝參數(shù)進(jìn)行優(yōu)化設(shè)計(jì),從而進(jìn)一步保證了鋼絲繩酸洗廢酸及含高鋅、鉛污泥資源化處置的效果,大大減小了對(duì)環(huán)境的污染。(5)本發(fā)明的一種鋼絲繩酸洗廢酸和含高鋅、鉛污泥共處置工藝,是采用補(bǔ)充污泥的方式進(jìn)行泥酸混合的,且混合過(guò)程中污泥是保持過(guò)量的,從而可以提高泥酸混合液中總鐵的含量,進(jìn)而保證后序制取的絮凝劑的質(zhì)量。同時(shí),本發(fā)明的泥酸混合工藝產(chǎn)生的不溶性物質(zhì)所含鋅、鉛含量相對(duì)較少,其成分主要為二氧化硅,進(jìn)行水洗后可當(dāng)作固體廢物直接填埋,進(jìn)一步減少了對(duì)環(huán)境的污染,保證了酸洗廢酸和含高鋅、鉛污泥中資源的有效利用率。(6)本發(fā)明的一種鋼絲繩酸洗廢酸和含高鋅、鉛污泥共處置工藝,在聚鐵絮凝劑的制備過(guò)程中,通過(guò)向絮凝劑制取裝置中添加氧化劑和堿液的混合液,并對(duì)氧化劑和堿液的添加量進(jìn)行有效控制,從而可以制取質(zhì)量更好、堿基度更佳的絮凝劑,保證絮凝劑的使用效果。(7)本發(fā)明的一種鋼絲繩酸洗廢酸和含高鋅、鉛污泥共處置工藝,鉛鋅沉淀分離工序中通過(guò)選用特定濃度的醋酸鉛溶液對(duì)鉛鋅沉淀進(jìn)行分離純化,并對(duì)其分離工藝進(jìn)行優(yōu)化設(shè)計(jì),從而可以有效保證鉛鋅沉淀的分離效果,大大提高了硫化鉛和醋酸鋅工業(yè)產(chǎn)品的純度。附圖說(shuō)明圖1為本發(fā)明的一種鋼絲繩酸洗廢酸和含高鋅、鉛污泥共處置系統(tǒng)的結(jié)構(gòu)示意圖;圖2為本發(fā)明的一種鋼絲繩酸洗廢酸和含高鋅、鉛污泥共處置工藝的流程圖。圖中:1、泥酸攪拌溶解裝置;2、鉛鋅去除裝置;3、絮凝劑制取裝置;4、硫化氫吸收塔A;5、硫化氫吸收塔B;6、硫化氫吸收塔C;7、硫化氫泄漏報(bào)警器;8、鉛鋅沉淀分離裝置A;9、鉛鋅沉淀分離裝置B;10、閥門(mén)A;11、閥門(mén)B。具體實(shí)施方式如圖1所示,本發(fā)明的一種鋼絲繩酸洗廢酸和含高鋅、鉛污泥共處置系統(tǒng),包括泥酸攪拌溶解裝置1、鉛鋅去除裝置2、絮凝劑制取裝置3、硫化氫吸收裝置和鉛鋅沉淀分離裝置,其中,泥酸攪拌溶解裝置1通過(guò)管道與鉛鋅去除裝置2相連,該鉛鋅去除裝置2通過(guò)管道分別與絮凝劑制取裝置3、硫化氫吸收裝置及鉛鋅沉淀分離裝置相連。上述泥酸攪拌溶解裝置1、鉛鋅去除裝置2、絮凝劑制取裝置3及鉛鋅沉淀分離裝置內(nèi)均設(shè)有攪拌器,且鉛鋅去除裝置2與泥酸攪拌溶解裝置1及絮凝劑制取裝置3相連的管道上均設(shè)有提升泵,該提升泵采用耐酸腐蝕提升泵。通過(guò)泥酸攪拌溶解裝置1對(duì)待處理污泥與廢酸液進(jìn)行混合攪拌溶解,將產(chǎn)生的上清液通過(guò)提升泵抽至鉛鋅去除裝置2中以去除溶解污泥后酸液中的鉛、鋅,使鉛、鋅發(fā)生沉淀,通過(guò)硫化氫吸收裝置對(duì)鉛鋅去除裝置中產(chǎn)生的硫化氫氣體進(jìn)行吸收處理,防止直接排放污染環(huán)境,同時(shí)硫化氫吸收裝置中產(chǎn)生的硫化物能夠通入鉛鋅去除裝置進(jìn)行循環(huán)使用,有利于節(jié)約資源。鉛鋅去除裝置2中產(chǎn)生的上清液進(jìn)入絮凝劑制取裝置3用于制取絮凝劑,而通過(guò)鉛鋅沉淀分離裝置的設(shè)置能夠?qū)︺U鋅去除裝置2中產(chǎn)生的鉛、鋅混合沉淀物進(jìn)行分離反應(yīng),制備純度較高的硫化鉛和醋酸鋅工業(yè)產(chǎn)品,實(shí)現(xiàn)了資源化利用。采用本發(fā)明的系統(tǒng)能夠有效實(shí)現(xiàn)鋼絲繩酸洗廢酸和含高鋅、鉛污泥的資源化共處置,減少環(huán)境污染,且工藝操作簡(jiǎn)單,能夠進(jìn)行自動(dòng)化控制。上述硫化氫吸收裝置包括依次相連的硫化氫吸收塔A4、硫化氫吸收塔B5和硫化氫吸收塔C6,其中硫化氫吸收塔A4通過(guò)管道與鉛鋅去除裝置2的排氣口相連,上述硫化氫吸收塔的頂部均設(shè)有噴淋裝置,通過(guò)噴淋裝置噴淋的吸收液對(duì)硫化氫氣體進(jìn)行吸收。通過(guò)三級(jí)吸收塔的設(shè)置可以有效保證硫化氫的充分吸收,進(jìn)一步減少環(huán)境污染。由于硫化氫吸收塔B5及硫化氫吸收塔C6之間的管道上設(shè)有硫化氫泄漏報(bào)警器7,從而可以對(duì)排放氣體中所含硫化氫進(jìn)行監(jiān)測(cè),保證硫化氫的完全吸收,防止硫化氫的泄漏。上述鉛鋅沉淀分離裝置包括鉛鋅沉淀分離裝置A8和鉛鋅沉淀分離裝置B9,鉛鋅沉淀分離裝置A8和鉛鋅沉淀分離裝置B9均通過(guò)管道與鉛鋅去除裝置2的污泥排放口相連,且鉛鋅沉淀分離裝置A8及鉛鋅沉淀分離裝置B9與鉛鋅去除裝置2相連的管道上分別設(shè)有閥門(mén)A10、閥門(mén)B11,通過(guò)鉛鋅沉淀分離裝置A和鉛鋅沉淀分離裝置B的配合能夠?qū)崿F(xiàn)鉛鋅沉淀的有效分離,保證所得分離產(chǎn)物的純度。本發(fā)明的一種鋼絲繩酸洗廢酸和含高鋅、鉛污泥共處置工藝的流程如圖2所示,其通過(guò)泥酸攪拌溶解、鉛鋅去除、聚鐵絮凝劑的制備、硫化氫尾氣的凈化及鉛鋅沉淀分離實(shí)現(xiàn)了鋼絲繩酸洗廢酸和含高鋅、鉛污泥的資源化共處置,并通過(guò)對(duì)以上各工序的工序過(guò)程及工藝參數(shù)進(jìn)行優(yōu)化設(shè)計(jì),從而進(jìn)一步保證了鋼絲繩酸洗廢酸及含高鋅、鉛污泥資源化處置的效果,大大減小了對(duì)環(huán)境的污染。該工藝的具體步驟為:A、泥酸攪拌溶解:將待處理污泥投加到泥酸攪拌溶解裝置1中,然后向其中繼續(xù)投加廢酸液,其中污泥的投加量為投加至泥酸攪拌溶解裝置1的1/5-1/2體積處,廢酸液與污泥的體積比為1-10:1,經(jīng)攪拌反應(yīng)1-4小時(shí)并靜置1-5h后將上清液抽至鉛鋅去除裝置2中。通過(guò)對(duì)廢酸液與污泥的投加比例以及反應(yīng)、靜置時(shí)間進(jìn)行有效控制,從而可以保證泥酸的充分溶解。將上清液抽至鉛鋅去除裝置2后向泥酸攪拌溶解裝置1中繼續(xù)補(bǔ)充污泥,然后加入酸液進(jìn)行第二次污泥廢酸混合溶解,以此類(lèi)推,將經(jīng)多次反應(yīng)后底部沉淀的不溶性物質(zhì)水洗后當(dāng)作固體廢物直接填埋。本發(fā)明通過(guò)采用補(bǔ)充污泥的方式進(jìn)行泥酸混合的,且混合過(guò)程中污泥是保持過(guò)量的,從而可以提高泥酸混合液中總鐵的含量,進(jìn)而保證后序制取的絮凝劑的質(zhì)量。同時(shí),本發(fā)明的泥酸混合工藝產(chǎn)生的不溶性物質(zhì)所含鋅、鉛含量相對(duì)較少,其成分主要為二氧化硅,進(jìn)行水洗后可當(dāng)作固體廢物直接填埋,進(jìn)一步減少了對(duì)環(huán)境的污染,保證了酸洗廢酸和含高鋅、鉛污泥中資源的有效利用率。B、鉛鋅去除:檢測(cè)溶解污泥后酸液中的鉛、鋅含量,向鉛鋅去除裝置2中投加硫化物,控制鉛鋅去除裝置2中鉛、鋅總摩爾數(shù)與硫化物的摩爾數(shù)之比,即n(鉛+鋅):n(硫化物)=1:2-3,經(jīng)攪拌反應(yīng)30-60min后過(guò)濾去除反應(yīng)產(chǎn)生的沉淀物并將上清液提升至絮凝劑制取裝置3,同時(shí)將產(chǎn)生的硫化氫氣體通入硫化氫吸收裝置。本發(fā)明的硫化物為硫化鈉、硫化鉀、硫化鈣、硫氫化鈉的一種或多種。C、制備聚鐵絮凝劑:檢測(cè)通入絮凝劑制取裝置3的溶液中Fe2+和Fe3+的含量,并根據(jù)其含量配置氧化劑和堿液的混合液,其中,氧化劑與Fe2+的摩爾比為1:6,OH-與Fe3+的摩爾比為1-3:1,將上述混合液加入絮凝劑制取裝置3進(jìn)行攪拌反應(yīng),攪拌轉(zhuǎn)速為50-500r/min,攪拌反應(yīng)時(shí)間為45-120min,反應(yīng)結(jié)束后,進(jìn)行成化處理20-30h,然后蒸發(fā)10%-50%水分即制成了聚鐵絮凝劑。上述氧化劑為氯酸鈉和氯酸鉀中的一種或兩種的混合,堿液為氫氧化鈉、氫氧化鉀和氫氧化鈣溶液中的一種或一種以上的混合。發(fā)明人在實(shí)驗(yàn)過(guò)程中發(fā)現(xiàn),單純的使用堿溶液來(lái)制取絮凝劑不能夠得到質(zhì)量較好的絮凝劑,且對(duì)資源的利用率相對(duì)較低,本發(fā)明通過(guò)選用氧化劑和堿液的混合液來(lái)制備聚鐵絮凝劑,并對(duì)氧化劑和堿液的添加量進(jìn)行優(yōu)化設(shè)計(jì),從而可以制取質(zhì)量更好、堿基度更佳的絮凝劑,保證絮凝劑的使用效果。D、硫化氫尾氣凈化:將通入硫化氫吸收裝置內(nèi)的硫化氫氣體使用飽和堿液進(jìn)行吸收,并將充分吸收了硫化氫的堿液回用到步驟B中。具體的,先將硫化氫氣體通入硫化氫吸收塔A4進(jìn)行吸收處理,然后通入硫化氫吸收塔B5中進(jìn)行二次吸收,經(jīng)二次吸收后的硫化氫氣體經(jīng)過(guò)硫化氫泄漏報(bào)警器7,若報(bào)警器不報(bào)警則通過(guò)硫化氫吸收塔C6直接排出;若報(bào)警器報(bào)警監(jiān)測(cè)到硫化氫氣體泄漏后,對(duì)硫化氫吸收塔B5及硫化氫吸收塔C6內(nèi)的堿液進(jìn)行更換,并將吸收了硫化氫的堿液回用到步驟B中。本發(fā)明硫化氫吸收塔中的堿液為氫氧化鈉、氫氧化鉀及氫氧化鈣溶液中的一種或一種以上的混合。E、鉛鋅沉淀分離:使步驟B產(chǎn)生的鉛、鋅混合沉淀物質(zhì)進(jìn)入鉛鋅沉淀分離裝置,使用質(zhì)量濃度為30%-70%的醋酸鉛溶液進(jìn)行反應(yīng)分離,得到純度為99%以上的硫化鉛固體及符合工業(yè)純度的醋酸鋅固體。具體的,先打開(kāi)鉛鋅沉淀分離裝置A8與鉛鋅去除裝置2之間管道上的閥門(mén)A10,關(guān)閉鉛鋅沉淀分離裝置B9與鉛鋅去除裝置2之間管道上的閥門(mén)B11,將鉛、鋅混合沉淀物投加進(jìn)鉛鋅沉淀分離裝置A8中,在250-500r/min的轉(zhuǎn)速下反應(yīng)30-45min并靜置30-60分鐘后將沉淀物轉(zhuǎn)移至鉛鋅沉淀分離裝置B9中,在250-500r/min的轉(zhuǎn)速下反應(yīng)30-45min并靜置30-60分鐘后取出沉淀物即為純度為99%以上的硫化鉛固體;多次反應(yīng)后檢測(cè)鉛鋅沉淀分離裝置B9中醋酸鉛的濃度低于0.5%時(shí)取出蒸發(fā)結(jié)晶得到符合工業(yè)純度的醋酸鋅固體;此后打開(kāi)閥門(mén)B11,關(guān)閉閥門(mén)A10,將鉛鋅沉淀分離裝置B9作為第一次反應(yīng)的裝置,向鉛鋅沉淀分離裝置A8中補(bǔ)充新的醋酸鉛溶液作為第二次反應(yīng)的裝置,依次往復(fù)進(jìn)行?,F(xiàn)有技術(shù)中對(duì)鋼絲繩廠(chǎng)廢酸液和污泥的處理通常會(huì)忽略重金屬鋅的去除,而鋼絲繩廠(chǎng)廢酸液和污泥中的鋅含量都是巨大的,如不有效去除鋅而直接排放,則同樣會(huì)造成嚴(yán)重的環(huán)境污染。本發(fā)明能夠?qū)︿摻z繩廠(chǎng)廢酸液和污泥中的鉛、鋅同時(shí)進(jìn)行有效去除,并對(duì)最后的沉淀物質(zhì)進(jìn)行了純化處理。其中,通過(guò)選用特定濃度的醋酸鉛溶液對(duì)鉛鋅沉淀進(jìn)行分離純化,并通過(guò)鉛鋅沉淀分離裝置A8與鉛鋅沉淀分離裝置B9的配合對(duì)分離純化的工藝進(jìn)行優(yōu)化設(shè)計(jì),從而可以有效保證鉛鋅沉淀的分離效果,大大提高了硫化鉛和醋酸鋅工業(yè)產(chǎn)品的純度。為進(jìn)一步了解本發(fā)明的內(nèi)容,現(xiàn)結(jié)合附圖和實(shí)施例對(duì)本發(fā)明作詳細(xì)描述。實(shí)施例1參考圖1、圖2,將鋼絲繩廠(chǎng)污泥經(jīng)板框壓濾后的污泥(含水率30%-75%)投加到泥酸攪拌溶解裝置1中,投加量為:投加至泥酸攪拌溶解裝置1的1/3體積處,再向泥酸攪拌溶解裝置1中投加廢酸液(H+濃度為13%,鉛含量為720mg/L,鋅含量為4000mg/L),投加量為V(廢酸液):V(污泥)=3:1,即體積為9立方米。經(jīng)攪拌反應(yīng)2小時(shí)并靜置3h后使用耐酸腐蝕的提升泵將上清液抽到鉛鋅去除裝置2中。經(jīng)檢測(cè),溶解泥后的酸液的鉛含量為799mg/L,鋅含量為6940mg/L,向鉛鋅去除裝置2中加入230kg硫化鈉固體,攪拌反應(yīng)30min,將產(chǎn)生的鉛鋅沉淀混合物通入鉛鋅沉淀分離裝置進(jìn)行分離純化處理,去除沉淀物后將上清液提升至絮凝劑制取裝置3,同時(shí)將產(chǎn)生的硫化氫氣體通入硫化氫吸收裝置進(jìn)行吸收處理,硫化氫吸收塔中堿液采用氫氧化鈉溶液(本實(shí)施例中氫氧化鈉溶液貯存于吸收塔塔底,通過(guò)管道及提升泵泵入吸收塔頂部的噴淋裝置,由噴淋裝置噴淋而下對(duì)硫化氫氣體進(jìn)行吸收,從而進(jìn)一步提高了對(duì)硫化氫氣體的吸收效果)。經(jīng)檢測(cè),通入絮凝劑制取裝置3的去除鉛、鋅后溶液中Fe2+和Fe3+的含量分別為:Fe2+為78.9g/L,F(xiàn)e3+為21.8g/L,根據(jù)Fe2+和Fe3+的含量配置氧化劑和堿液的混合液,氯酸鈉為225kg,氫氧化鈉為141g,加水溶解后泵入絮凝劑制取裝置3,以350r/min的轉(zhuǎn)速攪拌反應(yīng)45min,自然情況下成化24小時(shí)后即得到聚鐵絮凝劑。對(duì)本實(shí)施例制取的絮凝劑進(jìn)行檢測(cè),結(jié)果如下:表1實(shí)施例1制取的的絮凝劑指標(biāo)含量結(jié)果表明制取的絮凝劑,是符合HG_T4672-2014行業(yè)標(biāo)準(zhǔn)的。使用制取的絮凝劑,對(duì)印染廢水(濁度為100NTU,CODcr為956mg/L)進(jìn)行處理,1m3污水中添加1kg絮凝劑,實(shí)驗(yàn)發(fā)現(xiàn)對(duì)濁度的去除可達(dá)90%左右,COD去除率可達(dá)77%左右。實(shí)施例2參考圖1、圖2,將鋼絲繩廠(chǎng)污泥經(jīng)板框壓濾后的污泥(含水率40%-75%)投加到泥酸攪拌溶解裝置1中,投加量為:投加至泥酸攪拌溶解裝置1的1/2體積處,再向泥酸攪拌溶解裝置1中投加廢酸液(H+濃度為10%,鉛含量為4500mg/L,鋅含量為5100mg/L),投加量為V(廢酸液):V(污泥)=8:1,即體積為24立方米。經(jīng)攪拌反應(yīng)4小時(shí)并靜置5h后使用耐酸腐蝕的提升泵將上清液抽到鉛鋅去除裝置2中。經(jīng)檢測(cè),溶解泥后的酸液的鉛含量為6500mg/L,鋅含量為7000mg/L,向鉛鋅去除裝置2中加入1101kg硫化鉀固體,攪拌反應(yīng)60min,將產(chǎn)生的鉛鋅沉淀混合物通入鉛鋅沉淀分離裝置進(jìn)行分離純化處理,去除沉淀物后將上清液提升至絮凝劑制取裝置3,同時(shí)將產(chǎn)生的硫化氫氣體通入硫化氫吸收裝置進(jìn)行吸收處理,硫化氫吸收塔中堿液采用氫氧化鉀。檢測(cè)通入絮凝劑制取裝置3的去除鉛、鋅后溶液中的Fe2+和Fe3+的含量,F(xiàn)e2+為225g/L,F(xiàn)e3+為31.6g/L,根據(jù)Fe2+和Fe3+的含量配置氧化劑和堿液的混合液,氯酸鉀為1968kg,氫氧化鉀為2270kg,加水溶解后泵入絮凝劑制取裝置3,以500r/min的轉(zhuǎn)速攪拌反應(yīng)120min,自然情況下成化30小時(shí)后即得到聚鐵絮凝劑。對(duì)制取的絮凝劑進(jìn)行檢測(cè),結(jié)果如下:表2實(shí)施例2制取的的絮凝劑指標(biāo)含量結(jié)果表明制取的絮凝劑,是符合HG_T4672-2014行業(yè)標(biāo)準(zhǔn)的。使用制取的絮凝劑,對(duì)印染廢水(濁度為300NTU,CODcr為1200mg/L)進(jìn)行處理,1m3污水中添加0.9kg絮凝劑,實(shí)驗(yàn)發(fā)現(xiàn)對(duì)濁度的去除可達(dá)84%左右。COD去除率可達(dá)68%左右。實(shí)施例3參考圖1、圖2,將鋼絲繩廠(chǎng)污泥經(jīng)板框壓濾后的污泥(含水率40%-75%)投加到泥酸攪拌溶解裝置1中,投加量為:投加至泥酸攪拌溶解裝置1的1/5體積處,再向泥酸攪拌溶解裝置1中投加廢酸液(H+濃度為12%,鉛含量為3000mg/L,鋅含量為4200mg/L),投加量為V(廢酸液):V(污泥)=10:1,即體積為30立方米。經(jīng)攪拌反應(yīng)1小時(shí)并靜置1h后使用耐酸腐蝕的提升泵將上清液抽到鉛鋅去除裝置2中。檢測(cè)溶解泥后的酸液的鉛含量為5300mg/L,鋅含量為5600mg/L,向鉛鋅去除裝置2中加入483.5kg硫化鈣固體,攪拌反應(yīng)30min,將產(chǎn)生的鉛鋅沉淀混合物通入鉛鋅沉淀分離裝置進(jìn)行分離純化處理,去除沉淀物后將上清液提升至絮凝劑制取裝置3,同時(shí)將產(chǎn)生的硫化氫氣體通入硫化氫吸收裝置進(jìn)行吸收處理,硫化氫吸收塔中堿液采用氫氧化鈣溶液。檢測(cè)通入絮凝劑制取裝置3的去除鉛、鋅后溶液中的Fe2+和Fe3+的含量,F(xiàn)e2+為146g/L,F(xiàn)e3+為23.2g/L,根據(jù)Fe2+和Fe3+的含量配置氧化劑和堿液的混合液,氯酸鈉為1387kg,氫氧化鈣為919kg,加水溶解后泵入絮凝劑制取裝置3,以100r/min的轉(zhuǎn)速攪拌反應(yīng)45min,自然情況下成化20小時(shí)后即得到聚鐵絮凝劑。對(duì)制取的絮凝劑進(jìn)行檢測(cè),結(jié)果如下:表3實(shí)施例3制取的的絮凝劑指標(biāo)含量指標(biāo)數(shù)值Fe3+10.1%Fe2+0.3%鹽基度8%水不溶物0.03%密度1.20g/cm3Zn0.04%Pb0.008%Cd未檢出結(jié)果表明制取的絮凝劑,是符合HG_T4672-2014行業(yè)標(biāo)準(zhǔn)的。使用制取的絮凝劑,對(duì)印染廢水(濁度為400NTU,CODcr為700mg/L)進(jìn)行處理,1m3污水中添加1.2kg絮凝劑,實(shí)驗(yàn)發(fā)現(xiàn)對(duì)濁度的去除可達(dá)88%左右。COD去除率可達(dá)63%左右。實(shí)施例4參考圖1、圖2,將鋼絲繩廠(chǎng)污泥經(jīng)板框壓濾后的污泥(含水率30%-75%)投加到泥酸攪拌溶解裝置1中,投加量為:投加至泥酸攪拌溶解裝置1的1/4體積處,再向泥酸攪拌溶解裝置1中投加廢酸液(H+濃度為11%,鉛含量為800mg/L,鋅含量為3000mg/L),投加量為V(廢酸液):V(污泥)=5:1,即體積為15立方米。經(jīng)攪拌反應(yīng)3小時(shí)并靜置2h后使用耐酸腐蝕的提升泵將上清液抽到鉛鋅去除裝置2中。檢測(cè)溶解泥后的酸液的鉛含量為1100mg/L,鋅含量為4400mg/L,向鉛鋅去除裝置2中加入154kg硫氫化鈉固體,攪拌反應(yīng)50min,將產(chǎn)生的鉛鋅沉淀混合物通入鉛鋅沉淀分離裝置進(jìn)行分離純化處理,去除沉淀物后將上清液提升至絮凝劑制取裝置3,同時(shí)將產(chǎn)生的硫化氫氣體通入硫化氫吸收裝置進(jìn)行吸收處理,硫化氫吸收塔中堿液采用氫氧化鈉、氫氧化鈣和氫氧化鉀的混合液。檢測(cè)通入絮凝劑制取裝置3的去除鉛、鋅后溶液中的Fe2+和Fe3+的含量,F(xiàn)e2+為88g/L,F(xiàn)e3+為12g/L,根據(jù)Fe2+和Fe3+的含量配置氧化劑和堿液的混合液,氯酸鈉為416kg,氫氧化鈉為129kg,加水溶解后泵入絮凝劑制取裝置3,以450r/min的轉(zhuǎn)速攪拌反應(yīng)70min,自然情況下成化20小時(shí)后即得到聚鐵絮凝劑。對(duì)制取的絮凝劑進(jìn)行檢測(cè),結(jié)果如下:表4實(shí)施例4制取的絮凝劑指標(biāo)含量指標(biāo)數(shù)值Fe3+11%Fe2+0.9%鹽基度9%水不溶物0.05%密度1.13g/cm3Zn0.08%Pb0.004%Cd未檢出結(jié)果表明制取的絮凝劑,是符合HG_T4672-2014行業(yè)標(biāo)準(zhǔn)的。使用制取的絮凝劑,對(duì)印染廢水(濁度為500NTU,CODcr為800mg/L)進(jìn)行處理,1m3污水中添加0.8kg絮凝劑,實(shí)驗(yàn)發(fā)現(xiàn)對(duì)濁度的去除可達(dá)79%左右,COD去除率可達(dá)76%左右。實(shí)施例5參考圖1,將鋼絲繩廠(chǎng)污泥經(jīng)板框壓濾后的污泥(含水率30%-75%)投加到泥酸攪拌溶解裝置1中,投加量為:投加至泥酸攪拌溶解裝置1的1/4體積處,再向泥酸攪拌溶解裝置1中投加廢酸液(H+濃度為12%,鉛含量為900mg/L,鋅含量為3200mg/L),投加量為V(廢酸液):V(污泥)=1:1,即體積為3立方米。經(jīng)攪拌反應(yīng)3小時(shí)并靜置4h后使用耐酸腐蝕的提升泵將上清液抽到鉛鋅去除裝置2中。檢測(cè)溶解泥后的酸液的鉛含量為1200mg/L,鋅含量為4600mg/L,向鉛鋅去除裝置2中加入210kg硫化鈉、硫化鉀、硫化鈣和硫氫化鈉固體,攪拌反應(yīng)45min,將產(chǎn)生的鉛鋅沉淀混合物通入鉛鋅沉淀分離裝置進(jìn)行分離純化處理,去除沉淀物后將上清液提升至絮凝劑制取裝置3,同時(shí)將產(chǎn)生的硫化氫氣體通入硫化氫吸收裝置進(jìn)行吸收處理,硫化氫吸收塔中堿液采用氫氧化鈉、氫氧化鈣和氫氧化鉀的混合液。檢測(cè)通入絮凝劑制取裝置3的去除鉛、鋅后溶液中的Fe2+和Fe3+的含量,F(xiàn)e2+為90g/L,F(xiàn)e3+為11g/L,根據(jù)Fe2+和Fe3+的含量配置氧化劑和堿液的混合液,氯酸鈉為426kg,氫氧化鈉為130kg,加水溶解后泵入絮凝劑制取裝置3,以50r/min的轉(zhuǎn)速攪拌反應(yīng)120min,自然情況下成化30小時(shí)后即得到聚鐵絮凝劑。對(duì)制取的絮凝劑進(jìn)行檢測(cè),結(jié)果如下:表5實(shí)施例5制取的絮凝劑指標(biāo)含量指標(biāo)數(shù)值Fe3+11.4%Fe2+0.76%鹽基度10%水不溶物0.03%密度1.12g/cm3Zn0.07%Pb0.002%Cd未檢出結(jié)果表明制取的絮凝劑,是符合HG_T4672-2014行業(yè)標(biāo)準(zhǔn)的。使用制取的絮凝劑,對(duì)印染廢水(濁度為500NTU,CODcr為800mg/L)進(jìn)行處理,1m3污水中添加0.8kg絮凝劑,實(shí)驗(yàn)發(fā)現(xiàn)對(duì)濁度的去除可達(dá)73%左右,COD去除率可達(dá)71%左右。上述實(shí)施例僅僅是為清楚地說(shuō)明本發(fā)明所作的舉例,而并非對(duì)實(shí)施方式的限定。對(duì)于所屬領(lǐng)域的普通技術(shù)人員來(lái)說(shuō),在上述說(shuō)明的基礎(chǔ)上還可以做出其它的不同形式的變化或變動(dòng)。這里無(wú)需也無(wú)法對(duì)所有的實(shí)施方式予以窮舉。而由此所引申出的顯而易見(jiàn)的變化或變動(dòng)仍處于本發(fā)明的保護(hù)范圍之中。當(dāng)前第1頁(yè)1 2 3