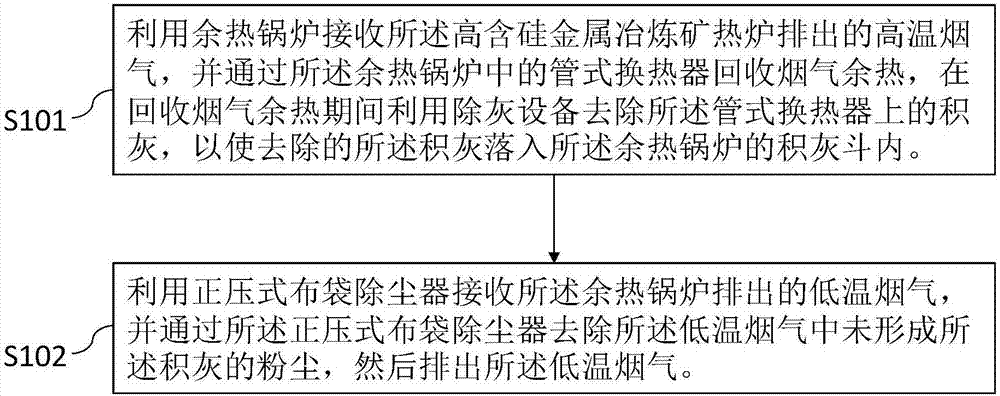
本發(fā)明屬于冶金
技術領域:
,具體涉及一種用于高含硅金屬冶煉礦熱爐的回收方法及一種用于高含硅金屬冶煉礦熱爐的回收裝置。
背景技術:
:高含硅金屬是指金屬硅、硅鐵合金、硅錳合金、硅鈣合金、硅鈣鋇鋁合金等硅含量遠遠大于10%(質量分數(shù))的金屬或合金。通常采用礦熱爐冶煉技術進行冶煉,所謂礦熱爐冶煉技術是在密閉或半密閉容器內,采用碳素電極加熱碳質還原劑還原的一種生產技術,其還原能力高于傳統(tǒng)高爐煉鐵技術,生產成本也高于傳統(tǒng)高爐煉鐵技術,礦熱爐產品按還原活性劃分介于高爐煉鐵技術以上,工業(yè)硅以下的產品。如鉻鐵、鉬鐵、錳鐵、鎳鐵(高鎳品種)等;各類含硅鐵合金:硅鐵、硅錳、硅鉻、硅鋁鐵等;以及工業(yè)硅,電石等。在該方法中,主要發(fā)生的反應為:mo+c→m+co↑式中:m可以是鐵、鋁、錳等金屬,也可以是硅。發(fā)明人在實施本發(fā)明的過程中發(fā)現(xiàn):高含硅金屬礦熱爐在冶煉時向外排出高溫煙氣,高溫煙氣將攜帶出金屬硅及其他金屬的液滴,這些液滴與空氣中的氧氣反應生成相應金屬氧化物微粒,例如硅氧化物微粒、鐵氧化物微粒等,但由于氧化物微粒很小,特別是二氧化硅微粒在隨煙氣向外流出時容易出現(xiàn)拉絲現(xiàn)象,即產生的粉塵呈現(xiàn)細纖維狀,且超細二氧化硅黏附性極強,黏附性極強的細纖維狀粉塵在余熱鍋爐內與換熱管接觸極易黏附于換熱管,導致?lián)Q熱效率顯著下降,最終高含硅金屬礦熱爐冶煉煙氣余熱的回收利用十分困難。技術實現(xiàn)要素:為了解決上述問題,本發(fā)明的目的不僅提供了一種用于高含硅金屬冶煉礦熱爐的回收方法,而且還提供了一種用于高含硅金屬冶煉礦熱爐的回收裝置,所述回收方法和回收裝置都能夠有效地回收高含硅金屬冶煉礦熱爐所產生的煙氣中的煙氣余熱和粉塵。本發(fā)明提供了一種用于高含硅金屬冶煉礦熱爐的回收方法,其步驟包括;第一步驟,利用余熱鍋爐接收所述高含硅金屬冶煉礦熱爐排出的高溫煙氣,并通過所述余熱鍋爐中的管式換熱器回收煙氣余熱,在回收煙氣余熱期間利用除灰設備去除所述管式換熱器上的積灰,以使去除的所述積灰落入所述余熱鍋爐的積灰斗內;第二步驟,利用正壓式布袋除塵器接收所述余熱鍋爐排出的低溫煙氣,并通過所述正壓式布袋除塵器去除所述低溫煙氣中未形成所述積灰的粉塵,然后排出所述低溫煙氣。本發(fā)明還提供了一種用于高含硅金屬冶煉礦熱爐的回收裝置,其特征在于,包括:煙氣通道;余熱鍋爐,所述余熱鍋爐通過所述煙氣通道與所述高含硅金屬冶煉礦熱爐相連,用以接收高溫煙氣,所述余熱鍋爐包括能夠從所述高溫煙氣中吸收熱量的管式換熱器、用于去除所述管式換熱器上的積灰的除灰設備和用于收集被去除的所述積灰的積灰斗,以及設于所述積灰斗的底部上卸料器;正壓式布袋除塵器,其與所述余熱鍋爐相連以用于去除所述余熱鍋爐排出的低溫煙氣中未形成所述積灰的粉塵,并排出所述低溫煙氣。本發(fā)明的用于高含硅金屬冶煉礦熱爐的回收方法和回收裝置不僅可通過除灰設備去除所述管式換熱器上的積灰,以保證煙氣余熱能夠被高效回收,而且還通過余熱鍋爐的積灰斗和正壓式布袋除塵器順序地回收高溫煙氣中的粉塵,以避免最終排放煙氣中的粉塵含量超標。本發(fā)明與現(xiàn)有技術相比,本發(fā)明的用于高含硅金屬冶煉礦熱爐的回收方法和回收裝置至少具有突出的有益效果:1、該回收方法和回收裝置的熱交換效率得到大幅提高,可以使熱交換效率穩(wěn)定維持在80%以上,使整體運行的經濟效益明顯提高;2、該回收方法和回收裝置能夠高效地回收金屬氧化物微粒,尤其是含量較高的硅氧化物微粒,不易產生漏灰現(xiàn)象。此外,本發(fā)明的用于高含硅金屬冶煉礦熱爐的回收方法和回收裝置所需要設備的結構簡單,成本低廉,使用安全可靠,便于實施推廣應用。附圖說明下面結合附圖詳細說明本發(fā)明。通過結合以下附圖所作的詳細描述,本發(fā)明的上述或其他方面的內容將變得更清楚和更容易理解。附圖中:圖1顯示了根據本發(fā)明實施例的用于高含硅金屬冶煉礦熱爐的回收裝置;圖2顯示了根據本發(fā)明實施例的用于高含硅金屬冶煉礦熱爐的回收方法的流程圖。具體實施方式下面結合附圖詳細說明本發(fā)明的具體實施方式。圖1顯示了根據本發(fā)明實施例的用于高含硅金屬冶煉礦熱爐的回收裝置100。如圖1所示,該回收裝置100包括煙氣通道10、余熱鍋爐20和正壓式布袋除塵器30。其中,余熱鍋爐20通過煙氣通道10與高含硅金屬冶煉礦熱爐相連,以接收高含硅金屬冶煉礦熱爐產生的高溫煙氣,而正壓式布袋除塵器30與余熱鍋爐20相連,以用于去除余熱鍋爐排出的低溫煙氣中未形成積灰的粉塵,并排出低溫煙氣。該余熱鍋爐20包括能夠從高溫煙氣中吸收熱量的管式換熱器、用于去除管式換熱器上的積灰的除灰設備和用于收集被去除的積灰的積灰斗,以及設于積灰斗的底部上的卸料器。需要說明的是,所謂的高溫煙氣意指其溫度比低溫煙氣的溫度高,反之低溫煙氣意指其溫度比高溫煙氣的溫度低,即“高”和“低”并不代表煙氣的溫度數(shù)值,只代表兩者相比之后的大小關系。上述高含硅金屬冶煉礦熱爐是具有密閉式爐體和爐門的礦熱爐,高溫煙氣是該礦熱爐在冶煉高含硅金屬的過程所產生的煙氣,在冶煉期間間歇式開啟所述爐門并利用搗料機捅破爐內熔體上冷凝形成的殼,使高含硅金屬熔體順暢加入參與反應,以提高反應速率的同時提高高溫煙氣的總量。例如,在本實施例中可應用電極電流測量技術、尤其是中國專利cn200810183102.6公開的埋弧電爐電極電流的測量方法或中國專利cn200920000154.5公開的熱爐電極電流參數(shù)測量系統(tǒng)來監(jiān)測,當測得某一電極電流值出現(xiàn)異常時,可以手動地開啟爐門,或者通過控制系統(tǒng)(例如中國專利cn200910000375.7)開啟爐門,然后利用搗料機捅破爐內熔體上形成的“殼”,待上述電流恢復正常時,搗料機后移退出,關閉爐門。根據本發(fā)明,當高含硅金屬冶煉礦熱爐產生的高溫煙氣進入余熱鍋爐20內時,高溫煙氣中的二氧化硅微粒極易黏附于管式換熱器的換熱管上,并在其上形成積灰,進而影響換熱效率,但本實例可通過上述除灰設備去除管式換熱器上的積灰,一方面可以迫使積灰落入余熱鍋爐20的積灰斗內,被余熱鍋爐20所收集,另一方面可以保證余熱鍋爐20的管式換熱器能夠有效吸收高溫煙氣的熱量。據實驗得知,當高含硅金屬冶煉礦熱爐產生的600℃至750℃高溫煙氣進入余熱鍋爐20后,余熱鍋爐20的管式換熱器所排出的蒸汽溫度通??蛇_450℃至500℃,而排出的低溫煙氣溫度一般低于150℃,其中管式換熱器的換熱效率一般在80%以上,而余熱鍋爐20的積灰(由高溫煙氣中的粉塵形成)約占高溫煙氣中粉塵總量的30%。正壓式布袋除塵器30能夠有效去低溫煙氣中的粉塵,以煙氣中的粉塵含量低于排出標準,以便通過煙囪排放。由于粉塵中細纖維狀、黏附性極強的二氧化硅微粒在正壓式布袋除塵器30上過濾時,該微粒黏附于布袋,對布袋的裹覆效應明顯,布袋氣阻大,過濾難度大,但由于正壓式布袋除塵器30采用正壓過濾方式,加大了布袋過濾壓差,提高了過濾效率,正壓式布袋除塵器30除去粉塵約占高溫煙氣中粉塵總量的70%,過濾后,煙氣粉塵含量低于10mg/nm3,可經過煙囪集中高空排放。在圖1所示的實施例中,該余熱鍋爐20通過煙氣通道10與高含硅金屬冶煉礦熱爐相連,其中在煙氣通道10中設有波紋管補償器,用以吸收煙氣通道10在徑向和軸向產生的位移。進入煙氣通道10的高溫煙氣的溫度高達650℃至800℃,且煙氣量大,故煙氣通道10的直徑需要大于φ5200mm,但大直徑的煙氣通道10飛熱應力的補充十分困難,本實施例通過波紋管補償器吸收煙氣通道10在徑向和軸向產生的位移,降低煙氣通道10對其支持結構的負載,以提高整個回收裝置的安全系數(shù)。其中,波紋管補償器的數(shù)量優(yōu)選是多個,以進一步提高整個回收裝置100的安全系數(shù)。多個波紋管補償器最好是自由復式波紋補償器和帶定向拉桿的波紋補償器二者的組合。在圖1所示的實施例中,除灰設備可選為機械掛刷式除灰設備。機械掛刷式除灰設備優(yōu)選是中國專利cn103471119a(申請?zhí)柺?01310386220.8)公開的往返式鋼球清灰結構,將黏附于管式換熱器上的積灰刷落,刷落積灰在被余熱鍋爐20底部的集灰斗收集,以保證管式換熱器的換熱效率。在圖1所示的實施例中,在正壓式布袋除塵器30與余熱鍋爐20之間設有引風機。引風機對高含硅金屬冶煉礦熱爐產生的煙氣進行抽吸使由煙氣通道10、余熱鍋爐20構成的前置部分內壓力保持在微負壓狀態(tài),由正壓式布袋除塵器30構成的后置部分內壓力保持在微正壓狀態(tài),通過該引風機促使煙氣在煙氣通道10、余熱鍋爐20和正壓式布袋除塵器30之間順利有序地流動,保證回收裝置100能夠穩(wěn)定高效的運行。在圖1所示的實施例中,該回收裝置100還包括第一開關閥門71、第二開關閥門72、空冷器40和旋風除塵器50,依次串聯(lián)的第一開關閥門71、空冷器40和旋風除塵器50與依次串聯(lián)的第二開關閥門72和余熱鍋爐20相并聯(lián),其中,第一開關閥門71比空冷器40更靠近煙氣通道10,而第二開關閥門72比余熱鍋爐20更靠近煙氣通道10。正常情況,關閉第一開關閥門71,打開第二開關閥門72,空冷器40和旋風除塵器50并不工作,煙氣通道10輸出的煙氣依次進入余熱鍋爐20和正壓式布袋除塵器30,然后被排放。但當余熱鍋爐20出現(xiàn)故障時,為確保生產,將打開第一開關閥門71而關閉第二開關閥門72,一方面可以防止高溫煙氣直接進入正壓式布袋除塵器30而損壞布袋,另一方面可以實現(xiàn)達標排放和穩(wěn)定生產的目的。圖2顯示了根據本發(fā)明實施例的用于高含硅金屬冶煉礦熱爐的回收方法的流程圖。如圖1所示,該回收方法包括第一步驟s101,即利用余熱鍋爐20接收高含硅金屬冶煉礦熱爐排出的高溫煙氣,并通過余熱鍋爐20中的管式換熱器回收煙氣余熱,在回收煙氣余熱期間利用除灰設備去除管式換熱器上的積灰,以使去除的積灰落入余熱鍋爐的積灰斗內。當高溫煙氣進入余熱鍋爐20內時,高溫煙氣中的二氧化硅微粒極易黏附于管式換熱器的換熱管上,并在其上形成積灰,進而影響換熱效率,但本實例通過除灰設備去除管式換熱器上的積灰,一方面可以迫使積灰落入余熱鍋爐的積灰斗內,并被余熱鍋爐20所收集,另一方面可以保證余熱鍋爐20的管式換熱器能夠有效吸收高溫煙氣熱量。據實驗得知,當600℃至750℃高溫煙氣在換熱后,管式換熱器所排出的蒸汽溫度通??蛇_450℃至500℃,而排出的低溫煙氣溫度一般低于150℃,管式換熱器的換熱效率可達到80%,而余熱鍋爐20的積灰(由高溫煙氣中的粉塵形成)約占高溫煙氣中粉塵總量的30%。如圖2所示,該回收方法還包括第二步驟s102,即利用正壓式布袋除塵器30接收余熱鍋爐排出的低溫煙氣,并通過正壓式布袋除塵器30去除低溫煙氣中未形成積灰的粉塵,然后排出低溫煙氣。正壓式布袋除塵器30能夠有效去低溫煙氣中的粉塵,促使煙氣中的粉塵含量低于排出標準,然后通過煙囪排放。由于粉塵中細纖維狀、黏附性極強的二氧化硅微粒在正壓式布袋除塵器30上過濾時,該微粒黏附于布袋,對布袋的裹覆效應明顯,布袋氣阻大,過濾難度大,但由于正壓式布袋除塵器30采用正壓過濾方式,加大了布袋過濾壓差,提高了過濾效率,正壓式布袋除塵器30除去粉塵約占高溫煙氣中粉塵總量的70%,過濾后,煙氣粉塵含量低于10mg/nm3,可經過煙囪集中高空排放。在該優(yōu)選的實施例中,該余熱鍋爐20通過煙氣通道10與高含硅金屬冶煉礦熱爐相連,其中在煙氣通道10中設有波紋管補償器,用以吸收煙氣通道在徑向和軸向產生的位移。進入煙氣通道10的高溫煙氣的溫度高達650℃至800℃,且煙氣量大,故煙氣通道的直徑需要大于φ5200mm,但大直徑的煙氣通道10熱應力的補充十分困難,本實施例通過波紋管補償器吸收煙氣通道10在徑向和軸向產生的位移,降低煙氣通道10對其支持結構的負載,以提高整個回收方法的安全系數(shù)。其中,波紋管補償器的數(shù)量優(yōu)選是多個,以進一步提高整個回收方法的安全系數(shù)。多個波紋管補償器最好是自由復式波紋補償器和帶定向拉桿的波紋補償器二者的組合。在該優(yōu)選實施例中,除灰設備可選為機械掛刷式除灰設備。機械掛刷式除灰設備優(yōu)選是中國專利cn103471119a(申請?zhí)?01310386220.8)公開的往返式鋼球清灰結構,將黏附于管式換熱器上的積灰刷落,刷落積灰在被余熱鍋爐20的底部的集灰斗收集,以保證管式換熱器的換熱效率。高含硅金屬冶煉礦熱爐是具有密閉式爐體和爐門的礦熱爐,高溫煙氣是該礦熱爐在冶煉高含硅金屬的過程所產生的煙氣,在冶煉期間間歇式開啟所述爐門并利用搗料機捅破爐內熔體上冷凝形成的殼,使高含硅金屬熔體順暢加入參與反應,以提高反應速率的同時提高高溫煙氣的總量。例如,在本實施例中可應用電極電流測量技術、尤其是中國專利cn200810183102.6公開的埋弧電爐電極電流的測量方法或中國專利cn200920000154.5公開的熱爐電極電流參數(shù)測量系統(tǒng)來監(jiān)測,當測得某一電極電流值出現(xiàn)異常時,可以手動地開啟爐門,或者通過控制系統(tǒng)(例如中國專利cn200910000375.7)開啟爐門,然后利用搗料機捅破爐內熔體上形成的“殼”,待上述電流恢復正常時,搗料機后移退出,關閉爐門。采用半密閉式爐體的礦熱爐及應用電極電流測量技術監(jiān)測爐體狀態(tài),使礦熱爐在通常狀態(tài)為爐門關閉狀態(tài),爐門關閉狀態(tài)時,通過爐門與爐體(爐門框)的接觸縫隙泄露的外部冷風,僅能保證反應生成的一氧化碳氧化所需氧氣,如果出現(xiàn)冷凝“殼”現(xiàn)象,基于電極電流測量值的自動控制系統(tǒng)縮短了搗料機工作時間,大幅度降低了冷風混入量,以保證排放煙氣量小,溫度高。采用這些措施后從礦熱爐排出的冶煉煙氣溫度在650℃至800℃。將本發(fā)明實施例的用于高含硅金屬冶煉礦熱爐的回收方法和回收裝置應用a廠中,具體內容如下:a廠工業(yè)硅生產的設備規(guī)模是:4臺45000kva高含硅金屬冶煉礦熱爐(簡稱礦熱爐),年產工業(yè)硅2萬噸。礦熱爐冶煉煙氣余熱與粉塵產生情況如下:煙氣量:200000nm3/h臺煙氣溫度:700℃含塵濃度:5.5g/nm3煙氣成份:成份n2co2o2h2oso2%64.65322.01.00.35煙塵成份:煙塵粒度:um≤1.01.0~10≥10%603010粉塵堆積密度粉塵平均粒徑粉塵比表面積0.18200-400nm20m2/g根據本發(fā)明實施例的用于高含硅金屬冶煉礦熱爐的回收方法和回收裝置配置如下:大直徑高溫煙道:4根直徑φ3400mm的煙氣煙道,余熱鍋爐:4臺引風機4臺:風量480000m3/h臺,全壓6800pa,配電機功率1400kw。正壓式布袋除塵器2臺:單臺過濾面積:26400m2/臺,過濾風速:0.61m/min,濾袋規(guī)格:∮292x10000mm,濾袋材質:玻纖覆膜濾料。高含硅金屬礦熱爐冶煉煙氣余熱與粉塵回收效果:余熱鍋爐:煙氣進口煙溫:620℃,排煙溫度:142℃,產生的主汽壓力:3.1mpa,主汽溫度:465℃,4臺余熱鍋爐產生的主汽流量:94t/h,配發(fā)電機功率:25mw,頻率:50hz。余熱鍋爐中的管式換熱器的換熱效率可達到80%,而余熱鍋爐的積灰(由高溫煙氣中的粉塵形成)約占高溫煙氣中粉塵總量的30%。正壓式布袋除塵器除去粉塵約占高溫煙氣中粉塵總量的70%。將本發(fā)明實施例的用于高含硅金屬冶煉礦熱爐的回收方法和回收裝置應用b廠中,具體內容如下:b廠工業(yè)硅生產的設備規(guī)模是:8臺33000kva硅鐵合金電爐,年產硅鐵5.6萬噸。礦熱爐冶煉煙氣余熱與粉塵產生情況如下:煙氣量:110000nm3/h煙氣溫度:700℃;煙氣含塵量:2.54g/nm3煙氣成份:成分h2oco2o2n2%1.018.01269.0煙塵成分:成分ccaosio2al2o3fe2o3其他%7.50.291.70.30.20.1煙塵粒度(um)>1010-33-11-0.50.5-0.1<0.17%5%10%16%47%15%根據本發(fā)明實施例的用于高含硅金屬冶煉礦熱爐的回收方法和回收裝置配置如下:礦熱爐:8臺33000kva工業(yè)硅合金電爐大直徑高溫煙道:兩根直徑φ3200mm的煙氣通道,余熱鍋爐:8臺引風機8臺:風量450000m3/h臺,全壓6500pa,配電機功率1250kw。正壓式布袋除塵器4臺:單臺過濾面積:26400m2/臺,過濾風速:0.57m/min,濾袋規(guī)格:∮292x10000mm,濾袋材質:玻纖覆膜濾料。工業(yè)硅礦熱爐冶煉煙氣余熱與粉塵回收效果:余熱鍋爐:煙氣進口煙溫:600-650℃,排煙溫度:140-145℃,產生的主汽壓力:3.6mpa,主汽溫度:470℃,2臺余熱鍋爐產生的主汽流量:180t/h,配發(fā)電機功率:2×25mw,頻率:50hz。余熱鍋爐中的管式換熱器的換熱效率可達到80%,而余熱鍋爐的積灰(由高溫煙氣中的粉塵形成)約占高溫煙氣中粉塵總量的30%。而正壓式布袋除塵器除去粉塵約占高溫煙氣中粉塵總量的70%。在本申請中,除非另有明確的規(guī)定和限定,術語“相接”、“相接合”、“相連”、“連接”等術語應做廣義理解,例如,可以是固定連接,也可以是可拆卸連接,或成一體;可以是機械連接,也可以是電連接;可以是直接相連,也可以通過中間媒介間接相連,可以是兩個元件內部的連通或兩個元件的相互作用關系。對于本領域的普通技術人員而言,可以根據具體情況理解上述術語在本發(fā)明中的具體含義。最后應說明的是:以上各實施例僅用以說明本發(fā)明的技術方案,而非對其限制;盡管參照前述各實施例對本發(fā)明進行了詳細的說明,本領域的普通技術人員應當理解:其依然可以對前述各實施例所記載的技術方案進行修改,或者對其中部分或者全部技術特征進行等同替換;而這些修改或者替換,并不使相應技術方案的本質脫離本發(fā)明各實施例技術方案的范圍,其均應涵蓋在本發(fā)明的權利要求和說明書的范圍當中。尤其是,只要不存在結構沖突,各個實施例中所提到的各項技術特征均可以任意方式組合起來。本發(fā)明并不局限于文中公開的特定實施例,而是包括落入權利要求的范圍內的所有技術方案。當前第1頁12