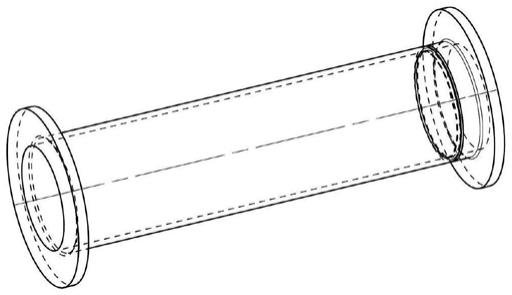
1.本發(fā)明涉及一種快速近凈成形航天發(fā)動機燃燒室的復(fù)合制造方法,具體涉及的是選區(qū)激光熔化技術(shù)、數(shù)控加工與分體焊接技術(shù)的組合應(yīng)用,屬于增材制造領(lǐng)域。
背景技術(shù):2.航天發(fā)動機燃燒室涉及環(huán)形內(nèi)腔、噴注器和異性結(jié)構(gòu)等復(fù)雜結(jié)構(gòu),一般地,其加工制造涉及鑄造、數(shù)控加工、電火花打孔和焊接等多道工序,材料利用率低,因而生產(chǎn)成本居高不下;此外,航天發(fā)動機工作環(huán)境溫度高,一般選用耐高溫、抗腐蝕的合金進行生產(chǎn),而此類金屬具有難變形、難加工的特殊性質(zhì),采用上述傳統(tǒng)工藝進行生產(chǎn)制造,風(fēng)險大、難度高,制造周期難以保證。選區(qū)激光熔化技術(shù)具有高柔性、短周期、復(fù)雜結(jié)構(gòu)一體成形的能力,高度契合具有內(nèi)流道、異形曲面等復(fù)雜結(jié)構(gòu)的航天發(fā)動機燃燒室的生產(chǎn)制造,然而,這種優(yōu)勢仍然受到諸如選區(qū)激光熔化設(shè)備成形尺寸、穩(wěn)定性等客觀因素困擾,使得選區(qū)激光熔化成形發(fā)動機燃燒室的實際應(yīng)用受到限制;目前主流的金屬選區(qū)激光熔化設(shè)備成形尺寸為600
㎜×
600
㎜×
600
㎜
或者650
㎜×
650
㎜×
800
㎜
,即使設(shè)備成形室尺寸可以滿足零件空間要求,但零件的打印風(fēng)險隨著零件尺寸幾何增長,一旦打印中途出現(xiàn)質(zhì)量問題,其造成的時間和經(jīng)濟損失將難以承受。
3.作為航天器的核心組成部件,保持發(fā)動機技術(shù)的領(lǐng)先具有重要的戰(zhàn)略意義,換言之,任何能顯著縮短航天發(fā)動機“設(shè)計-制造-試驗驗證”周期以及提高可靠性的技術(shù)方案,都將極大地推動航天發(fā)動機技術(shù)的發(fā)展革新。因此,亟需尋求一種新的復(fù)合制造工藝,既滿足發(fā)動機燃燒室復(fù)雜結(jié)構(gòu)一體精確成形需求,也能保證發(fā)動機燃燒室整體制造的低成本、短周期和可行性。
技術(shù)實現(xiàn)要素:4.本發(fā)明的目的在于提供一種快速近凈成形發(fā)動機燃燒室的復(fù)合制造方法,主要是解決一些大尺寸發(fā)動機燃燒室制造的難題,如在制造尺寸為600
㎜×
600
㎜×
900
㎜
或更大尺寸的發(fā)動機燃燒室時,通過現(xiàn)有技術(shù)就難以制造,或制造成本較高、周期較長。
5.為了實現(xiàn)上述目的,本發(fā)明提供如下技術(shù)方案:
6.(1)使用三維造型軟件處理燃燒室模型,將燃燒室分割成燃燒室主體和出口法蘭兩個部分;
7.(2)采用選區(qū)激光熔化技術(shù)成形燃燒室主體,保證燃燒室主體復(fù)雜結(jié)構(gòu)成形精度,
8.(3)采用數(shù)控加工成形出口法蘭;
9.(4)采用氬弧焊或激光焊將燃燒室主體與出口法蘭焊接為一體,得到完整的發(fā)動機燃燒室。
10.(5)對燃燒室進口和出口法蘭的裝配面采用數(shù)控機床進行精加工。
11.制造發(fā)動機燃燒室的材料選取具有焊接可行性的高溫合金和不銹鋼,如gh3625、gh3536、321l和1cr18ni9ti等。
12.步驟(1)中,使用三維造型軟件將超出選區(qū)激光熔化設(shè)備成形尺寸的燃燒室分割為兩段,第一段為燃燒室主體,包含環(huán)形內(nèi)腔和匯流槽等復(fù)雜結(jié)構(gòu),并且其高度不超過選區(qū)激光熔化設(shè)備成形高度極限;第二段為出口法蘭,包含出口法蘭和部分燃燒室腔體。燃燒室主體與出口法蘭連接處需預(yù)留60~90
°
的焊接坡口,燃燒室主體和出口法蘭需分別設(shè)置導(dǎo)向凸臺與導(dǎo)向凹槽。
13.步驟(2)中,采用選區(qū)激光熔化技術(shù)一體化近凈成形燃燒室主體,保證環(huán)形內(nèi)腔和匯流槽的尺寸精度滿足設(shè)計要求。
14.步驟(3)中,因出口法蘭結(jié)構(gòu)簡單,采用數(shù)控加工成形,不僅降低了生產(chǎn)成本,而且可與步驟(2)并聯(lián)進行,縮短了發(fā)動機燃燒室生產(chǎn)周期。
15.步驟(4)中,使用氬弧焊將燃燒室主體與出口法蘭連接成燃燒室零件,如燃燒室主體與出口法蘭是同種材料,則應(yīng)選擇相同牌號的焊絲,如燃燒室主體與出口法蘭為異種材料,則應(yīng)選擇中間成分的焊絲。
16.步驟(5)中,在進口法蘭和出口法蘭處進行精加工,避免焊接后導(dǎo)致的尺寸變形,確保滿足裝配需求。
17.與現(xiàn)有技術(shù)相比,本發(fā)明具有顯著的優(yōu)勢,具體表現(xiàn)在以下幾方面:
18.(1)現(xiàn)有設(shè)備無法滿足燃燒室全尺寸一體化增材制造,本發(fā)明基于分體成形思路克服了燃燒室尺寸超增材制造設(shè)備尺寸而無法一體成形的困難,實現(xiàn)了燃燒室的增材制造;
19.(2)與傳統(tǒng)的加工方法相比,工序難度減小,分體加工后只需在實體部分進行焊接即可,不僅大大降低了生產(chǎn)制造成本,還極大的提升產(chǎn)品可靠性和良品率,同時發(fā)動機燃燒室成形周期縮短14.7%,為火箭發(fā)動機技術(shù)的快速迭代提供了基礎(chǔ)。
附圖說明
20.圖1本發(fā)明發(fā)動機燃燒室三維模型;
21.圖2本發(fā)明發(fā)動機燃燒室剖視圖;
22.圖3本發(fā)明發(fā)動機燃燒室主體與出口法蘭的焊接坡口;
23.圖4是本發(fā)明的實現(xiàn)流程圖。
24.圖2中:1-入口法蘭;11-入口法蘭安裝面;2-出口法蘭;21-出口法蘭安裝面;3-燃燒室主體;4-焊接坡口。
具體實施方式
25.下面將結(jié)合本發(fā)明實施例中的附圖,對本發(fā)明實施例中的技術(shù)方案進行清楚、完整地描述;顯然,所描述的實施例僅僅是本發(fā)明一部分實施例,而不是全部的實施例,基于本發(fā)明中的實施例,本領(lǐng)域普通技術(shù)人員在沒有做出創(chuàng)造性勞動前提下所獲得的所有其他實施例,都屬于本發(fā)明保護的范圍。
26.在本發(fā)明的描述中,需要說明的是,術(shù)語“上”、“下”、“內(nèi)”、“外”、“頂/底端”等指示的方位或位置關(guān)系為基于附圖所示的方位或位置關(guān)系,僅是為了便于描述本發(fā)明和簡化描述,而不是指示或暗示所指的裝置或元件必須具有特定的方位、以特定的方位構(gòu)造和操作,因此不能理解為對本發(fā)明的限制。此外,術(shù)語“第一”、“第二”僅用于描述目的,而不能理解
為指示或暗示相對重要性。
27.下面將結(jié)合附圖對本發(fā)明專利進行進一步詳細(xì)描述:
28.實施例1:
29.使用商用三維建模軟件將總體尺寸為580
㎜×
550
㎜×
850
㎜
的發(fā)動機燃燒室模型分割為燃燒室主體和出口法蘭兩個部分,燃燒室主體包括環(huán)形內(nèi)腔和匯流槽等復(fù)雜結(jié)構(gòu),高度為800
㎜
,出口法蘭高50
㎜
。燃燒室主體和出口法蘭都選用gh3625合金,其中,采用大型工業(yè)級金屬激光選區(qū)熔化設(shè)備成形燃燒室主體,使用數(shù)控加工成形出口法蘭,兩道工序并聯(lián)進行。成形后,將燃燒室與出口法蘭拼接并固定,使用gh3625焊絲將兩者焊接為一體,得到發(fā)動機燃燒室,然后在裝配面進行精加工,整個生產(chǎn)周期由34天縮短為29天,降低了14.7%。
30.實施例2:
31.使用商用三維建模軟件將總體尺寸為580
㎜×
550
㎜×
650
㎜㎜
的發(fā)動機燃燒室模型分割為燃燒室主體和出口法蘭兩個部分,燃燒室主體包括環(huán)形內(nèi)流道和匯流槽等復(fù)雜結(jié)構(gòu),高度為600
㎜
,出口法蘭高50
㎜
。其中,燃燒室主體選用gh3625合金,采用大型工業(yè)級金屬激光選區(qū)熔化設(shè)備成形,出口法蘭選用321l不銹鋼,使用數(shù)控加工成形,兩道工序并聯(lián)進行,成形后,將燃燒室與出口法蘭拼接并固定,使用ernicrmo-3焊絲將兩者焊接為一體,得到發(fā)動機燃燒室,進一步降低了發(fā)動機燃燒室生產(chǎn)成本,同時將整個生產(chǎn)周期由30天縮短為25天,降低了16.7%。
32.以上內(nèi)容是結(jié)合具體的優(yōu)選實施方式對本發(fā)明所作的進一步詳細(xì)說明,不能認(rèn)定本發(fā)明的具體實施方式僅限于此,對于本發(fā)明所屬技術(shù)領(lǐng)域的普通技術(shù)人員來說,在不脫離本發(fā)明構(gòu)思的前提下,還可以做出若干簡單的推演或替換,都應(yīng)當(dāng)視為屬于本發(fā)明由所提交的權(quán)利要求書確定專利保護范圍。