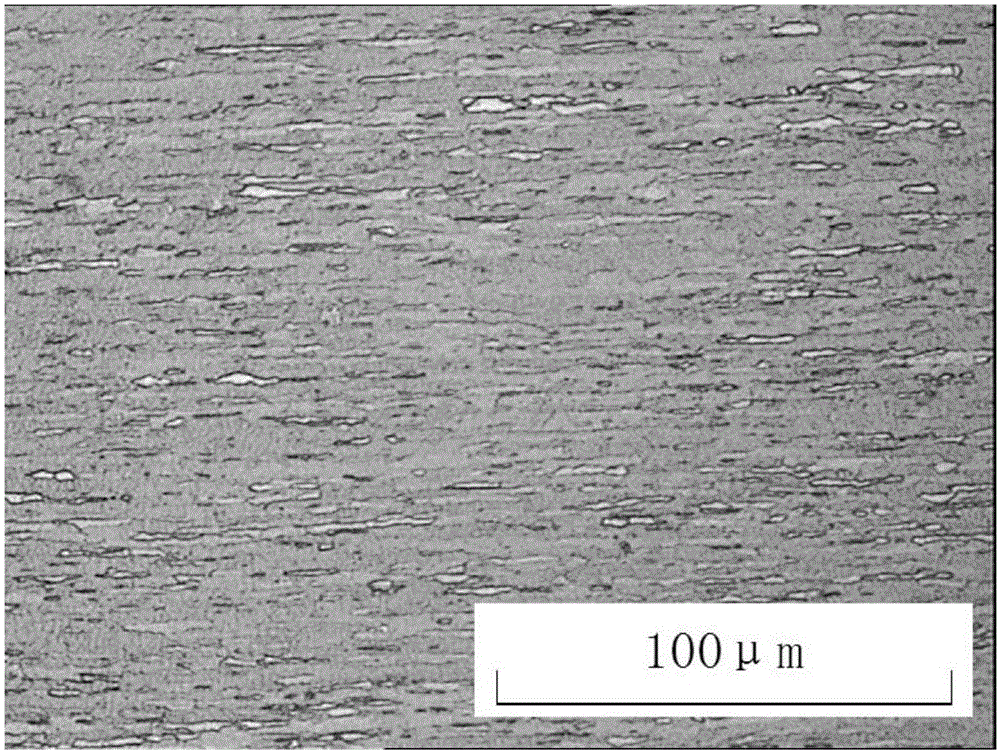
本發(fā)明涉及一種具有極高高溫抗蠕變性能的摻雜鉬板的生產(chǎn)工藝,具體涉及一種摻雜K、Si元素的高溫抗蠕變鉬板及其制備方法,屬于鉬板材料制備領域。
背景技術:
:隨著工業(yè)技術和材料技術的發(fā)展,越來越多的場合對材料在1500℃以上的高溫抗蠕變性能提出要求,例如,核燃料棒的承燒板、高溫陶瓷承燒板、燒結舟皿等。鎢、鉬材料具有極高的熔點和優(yōu)秀的耐化學腐蝕的性能,可以在這些使用環(huán)境中不發(fā)生熔化,但是卻容易在長期的重力或熱應力的作用下發(fā)生變形,從而影響設備的性能或一些精密產(chǎn)品的尺寸。鉬與鎢比較,有密度低、較為輕便、成本低等優(yōu)點,但其熔點較低,在一般情況下,純鉬的高溫抗蠕變性能明顯不如純鎢,以至于有些場合不得不使用純鎢或鎢合金,這樣就提高了成本,也提高了設備的負重。國內外已有不少人通過在鉬中同時摻雜K、Al、Si三種元素,或稀土氧化物等來提高鉬的高溫抗蠕變性能。但就目前摻雜K、Al、Si元素的技術而言,K、Al、Si的摻雜量較大,如果使用溫度過高,容易出現(xiàn)材料內的K、Al、Si蒸汽壓過高而自發(fā)分層和熔化的問題。同時,過大的摻雜量也容易影響設備內的氣氛。就摻雜方式而言,目前人們主要通過固固摻雜、固液摻雜和液液摻雜三種方式,固固摻雜成本低,但均勻性差;固液摻雜相對比較均勻,成本也比較適中;液液摻雜最為均勻,但需要長時間的攪拌和蒸干,成本較高。就摻雜元素而言,目前的鎢、鉬摻雜幾乎都是在材料中同時添加K、Al、Si三種元素。元素種類較多,容易對使用環(huán)境造成干擾。目前的技術,幾乎只對軋成的板坯做去應力退火或者一次再結晶退火,這樣的金相組織很難發(fā)揮這種鉬板的高溫抗蠕變性能。技術實現(xiàn)要素:針對現(xiàn)有技術的不足,本發(fā)明的目的在于提供一種摻雜K、Si元素的高溫抗蠕變鉬板及其制備方法,該鉬板具有極高高溫抗蠕變性能。為了實現(xiàn)上述目的,本發(fā)明采用了以下技術方案:一種摻雜K、Si元素的高溫抗蠕變鉬板的制備方法,所述鉬板中K的質量百分比含量為0.01~0.03%,Si的質量百分比含量為0.01~0.05%,所述制備方法包括如下步驟:步驟一,按照所述鉬板中K和Si的含量分別稱取所需的K源和Si源,配制得到混合溶液;步驟二,將步驟一得到的所述混合溶液與Mo源混合均勻并干燥,得到摻雜Mo源;步驟三,將步驟二得到的混合物進行還原處理,得到摻雜鉬粉;步驟四,將步驟三得到的摻雜鉬粉進行壓型、燒結、軋制處理,得到摻雜鉬板;步驟五,將步驟四得到的摻雜鉬板進行退火處理,得到高溫抗蠕變鉬板。上述制備方法的技術原理是:通過半液-液摻雜,使K和Si與鉬源粉混合均勻,還原得到摻雜鉬粉,經(jīng)過燒結、軋制形成特殊的纖維狀晶粒組織和鉀泡,經(jīng)過高溫退火,獲得特殊的長大晶組織。步驟一中考慮到后續(xù)的還原處理和燒結處理時的揮發(fā)因素,所需使用的K源和Si源應當適當過量,一般分別過量250ppm左右即可。上述制備方法中,作為一種優(yōu)選實施方式,步驟一中,稱取的K源和Si源的用量符合如下關系:按重量百分比,K:Si=1:0.8~1.5(比如1:0.9、1:1、1:1、1:1.2、1:1.3、1:1.4),更優(yōu)選地,K:Si=1:1。K和Si中,Si主要存在于晶界,能夠形成限制鉬板晶粒長大和等軸化,保存晶粒的高能量;K主要存在于晶內和晶界,能夠在高溫下促進晶粒長大,同時也有限制晶粒等軸化的作用,合理控制K和Si的比例可以更加理想地促使材料在高溫處理后長成長大晶組織。上述制備方法中,作為一種優(yōu)選實施方式,步驟一中,所述K源為KNO3,所述Si源為H2SiO3,KNO3和H2SiO3形成的混合溶液能夠組成相對穩(wěn)定的摻雜液,不會產(chǎn)生沉淀,對混合均勻非常有利。本申請將K和Si以不同形式的化合物加入能夠隨意調節(jié)K和Si的比例,同時摻雜液的流動性較好,有利于摻雜,更優(yōu)選地,所述混合溶液中,K的濃度為3~30g/L(比如11g/L、13g/L、15g/L、17g/L、19g/L、22g/L、25g/L、28g/L、29g/L),Si的濃度為3~35g/L(比如16g/L、19g/L、21g/L、25g/L、28g/L、30g/L、32g/L、33g/L、34g/L)。上述制備方法中,作為一種優(yōu)選實施方式,步驟二中,所述Mo源為四鉬酸銨。更優(yōu)選地,以100kg四鉬酸銨計,四鉬酸銨與2.5-10L(比如2.7L、3L、4L、5L、7L、8L、9L)所述混合溶液混合均勻并干燥,得到摻雜四鉬酸銨。進一步地,所述步驟二在雙錐式真空烘干機中進行。本發(fā)明Mo源采用四鉬酸銨相比于其他鉬酸鹽比如二鉬酸銨而言,生產(chǎn)得到的鉬粉晶粒不易聚團,同時粒度分布集中,利于燒結塊和板料的晶粒組織均勻。上述制備方法中,作為一種優(yōu)選實施方式,步驟三中,所述還原處理分為兩個階段,第一次還原處理得到摻雜二氧化鉬,第二次還原處理得到摻雜鉬粉。四鉬酸銨還原為鉬粉的反應方程式如下:(NH4)2Mo4O13+H2→NH3+MoO2+H2O;MoO2+H2→Mo+H2O;更優(yōu)選地,所述第一次還原處理的還原溫度為450-520℃(比如460℃、470℃、480℃、490℃、500℃、510℃、515℃),所述第二次還原處理的還原溫度為930-1000℃(比如935℃、950℃、960℃、970℃、980℃、990℃、995℃);進一步地,所述還原處理通過四管還原爐進行,所述第一次還原處理時,裝舟量為200-300g/舟(比如201g/舟、210g/舟、220g/舟、230g/舟、250g/舟、270g/舟、280g/舟、290g/舟),推舟速度為15-30min/舟(比如16min/舟、18min/舟、20min/舟、22min/舟、25min/舟、28min/舟、29min/舟);所述第二次還原處理時,裝舟量為0.8-1.5kg/舟(比如0.9kg/舟、1.0kg/舟、1.1kg/舟、1.2kg/舟、1.3kg/舟、1.4kg/舟),推舟速度為10-25min/舟(比如11min/舟、12min/舟、14min/舟、17min/舟、19min/舟、22min/舟、24min/舟)。上述制備方法中,作為一種優(yōu)選實施方式,步驟四中,所述壓型處理采用冷等靜壓成型,得到摻雜鉬板坯;更優(yōu)選地,成型壓力為150-200MPa(比如155MPa、170MPa、180MPa、185MPa、190MPa、195MPa),保壓時間15-25min(比如16min、18min、20min、22min、24min);進一步地,在所述壓型處理之前,對所述摻雜鉬粉過120-160目篩(比如120目篩、130目篩、140目篩、150目篩、160目篩),取篩下粉末進行壓型處理。上述制備方法中,作為一種優(yōu)選實施方式,步驟四中,所述燒結處理采用中頻爐燒結,得到摻雜鉬燒結板坯,燒結溫度為1920-1950℃(比如1922℃、1930℃、1935℃、1940℃、1945℃),燒結時間為2~8小時(比如3h、4h、5h、6h、7h、7.5h);所述軋制處理采用熱軋,得到所述摻雜鉬板,開軋溫度為1280~1400℃(比如1285℃、1300℃、1310℃、1330℃、1350℃、1360℃、1370℃、1380℃、1390℃),終軋溫度為700~1100℃(比如710℃、750℃、800℃、850℃、900℃、950℃、1000℃、1050℃、1090℃),所述摻雜鉬板的厚度為0.5~4mm(比如0.6mm、0.8mm、1mm、1.5mm、2mm、3mm、4mm)。上述制備方法中,作為一種優(yōu)選實施方式,步驟五中,所述退火處理的溫度為1550-1900℃(比如1560℃、1590℃、1610℃、1620℃、1650℃、1680℃、1720℃、1750℃、1780℃、1790℃、1850℃),時間為4-6h(比如4.2h、4.5h、4.8h、4.8h、5.2h、5.5h、5.8h)。在該退火溫度下可以更好地使產(chǎn)品結成長大晶的組織結構。低于該溫度范圍不利于結成該種組織;高于該溫度范圍可能會由于K和Si的蒸汽壓過大導致材料開裂。采用上述方法制備得到的摻雜K、Si元素的高溫抗蠕變鉬板。與現(xiàn)有技術相比,本發(fā)明的有益效果是:(1)將摻雜元素降低到兩種,即K、Si兩種元素。本發(fā)明將Al元素剔除,制備的鉬板同樣具備良好的高溫抗蠕變性能,減少元素的摻雜種類,有利于提高工藝穩(wěn)定性,以及減少使用時對設備的影響。(2)將K、Si含量分別降低至K:0.01~0.03%;Si:0.01~0.05%。這樣做可以提高使用溫度,提高材料純度,減少對設備和用戶產(chǎn)品的影響。(3)采用半液液摻雜方式摻雜。將摻雜液直接摻入到四鉬酸銨中,摻雜時有部分四鉬酸銨溶解,使溶解部分與摻雜液成液液摻雜,干燥后四鉬酸銨晶體與摻雜液中的K、Si成為互相結合的晶體,使其結合更好,而添加摻雜液的量沒有增加,因此沒有增加烘干的成本。(4)軋成板料后,將板料進行1550-1900℃再結晶退火,使其得到特殊的二次再結晶組織,從而得到具有高溫抗蠕變性能的材料。綜上所述,本發(fā)明在幾乎沒有提高生產(chǎn)成本和降低生產(chǎn)效率的情況下,探索了新的具有極高高溫抗蠕變性能的鉬板的生產(chǎn)工藝;本發(fā)明制備的鉬板有極高的高溫抗蠕變性能,在1900℃以下的抗蠕變性能遠優(yōu)于純鉬,可用作高溫燒結的承燒板,或高溫爐中的結構性部件。附圖說明圖1是本發(fā)明實施例1中軋制后摻雜鉬板的金相組織;圖2是本發(fā)明實施例1中高溫退火后摻雜鉬板的金相組織;圖3是用以測試本發(fā)明制備的鉬板的高溫抗蠕變性能的高溫載荷抗彎試驗的示意圖。具體實施方式為了使本發(fā)明的內容更容易被清楚地理解,下面根據(jù)本發(fā)明的具體實施例并結合附圖,對本發(fā)明作進一步詳細的說明。以下實施例中所用原料和試劑皆可從市場上購買。實施例1生產(chǎn)厚度4mm的高溫抗蠕變鉬板,其中,按重量百分比所述鉬板中K:0.03%,Si:0.04%。本實施例中,K源為KNO3,Si源為H2SiO3,Mo源為四鉬酸銨。具體制備方法如下:(1)考慮到還原和燒結時的揮發(fā),K和Si分別按照0.05%和0.06%摻入。KNO3、H2SiO3和四鉬酸銨的重量比例為:0.2247:0.2738:200。(2)分別稱取0.2247kgKNO3,0.2738kgH2SiO3配制成含KNO3、H2SiO3的混合溶液,稀釋至20L,倒入雙錐式真空干燥摻雜鍋的摻雜液罐中,待用。在摻雜鍋內裝入200kg四鉬酸銨,然后開始轉動摻雜鍋。利用空壓機壓力將混合溶液噴入摻雜鍋,待摻雜液罐中的溶液噴完。用蒸汽發(fā)生器產(chǎn)生的蒸汽加熱摻雜鍋,將水分蒸干,蒸汽發(fā)生器的壓力為0.2MPa左右,蒸干時間約為3h。蒸干后,在摻雜鍋的夾層通入冷卻水,冷卻時間約為2h。冷卻完成后,將摻雜好的四鉬酸銨卸出。(3)將步驟(2)得到的摻雜好的四鉬酸銨通過四管還原爐還原成摻雜二氧化鉬,還原溫度為500℃,裝舟量為250g/舟,推舟速度為20min/舟。(4)將步驟(3)還原得到的摻雜二氧化鉬,在四管還原爐中進行第二次還原,還原溫度為950℃,裝舟量為1kg/舟,推舟速度為15min/舟。(5)將步驟(4)還原得到的摻雜鉬粉,過120目篩,取篩下物進行冷等靜壓成型,成型壓力為160MPa,保壓時間20min,得到摻雜鉬板坯。(6)將步驟(5)得到的摻雜鉬板坯送入中頻爐燒結得到摻雜鉬燒結板坯,燒結溫度為1950℃,燒結時間為5h,板坯厚度為50mm。(7)步驟(6)得到的板坯經(jīng)熱軋得到4mm厚的鉬板,開軋溫度為1320℃,當軋制總變形量達到70%時,于1200℃退火1h,終軋溫度為1000℃。(8)將步驟(7)熱軋得到的板坯,再經(jīng)過1600℃、5h退火處理,最終得到具有極高的高溫抗蠕變性能的摻雜鉬板,其中K在摻雜鉬板中以K2O形式存在,Si在摻雜鉬板中以SiO2形式存在。圖1是本實施例軋制后摻雜鉬板的金相組織,從該圖可以看出,軋制后摻雜鉬板晶粒呈纖維狀組織;圖2是本實施例中高溫退火后摻雜鉬板的金相組織,從該圖可以看出,退火后摻雜鉬板晶粒呈長大晶組織,鉬板內部是呈直線排布的小氣泡串。通過高溫載荷抗彎試驗(如圖3所示,載荷重量1.2kg)來測試材料的高溫抗蠕變性能,經(jīng)測試,本實施例制備的鉬板測試參數(shù)和高溫抗蠕變性能數(shù)據(jù)見表1。實施例2生產(chǎn)厚度2.5mm的高溫抗蠕變鉬板,其中,按重量百分比鉬板中K:0.02%,Si:0.03%。本實施例中,K源為KNO3,Si源為H2SiO3,Mo源為四鉬酸銨。具體制備方法如下:(1)考慮到還原和燒結時的揮發(fā),K和Si分別按照0.04%和0.05%摻入。KNO3、H2SiO3和四鉬酸銨的重量比例為:0.1947:0.2417:200。(2)分別稱取0.1947kgKNO3,0.2417kgH2SiO3配制成含KNO3、H2SiO3的混合溶液,稀釋至18L,倒入雙錐式真空干燥摻雜鍋的摻雜液罐中,待用。在摻雜鍋內裝入200kg四鉬酸銨,然后開始轉動摻雜鍋。利用空壓機壓力將混合溶液噴入摻雜鍋,待摻雜液罐中的溶液噴完。用蒸汽發(fā)生器產(chǎn)生的蒸汽加熱摻雜鍋,將水分蒸干,蒸汽發(fā)生器的壓力為0.18MPa左右,蒸干時間約為2.7h。蒸干后,在摻雜鍋的夾層通入冷卻水,冷卻時間約為2h。冷卻完成后,將摻雜好的四鉬酸銨卸出。(3)將步驟(2)得到的摻雜好的四鉬酸銨通過四管還原爐還原成摻雜二氧化鉬,還原溫度為510℃,裝舟量為230g/舟,推舟速度為25min/舟。(4)將步驟(3)還原得到的摻雜二氧化鉬,在四管還原爐中進行第二次還原,還原溫度為970℃,裝舟量為1.2kg/舟,推舟速度為20min/舟。(5)將步驟(4)還原得到的摻雜鉬粉,過160目篩,取篩下物進行冷等靜壓成型,成型壓力為180MPa,保壓時間20min,得到摻雜鉬板坯。(6)將步驟(5)得到的摻雜鉬板坯送入中頻爐燒結得到摻雜鉬燒結板坯,燒結溫度為1920℃,燒結時間為3h,板坯厚度為35mm。(7)步驟(6)得到的板坯經(jīng)熱軋得到2.5mm厚的鉬板,開軋溫度為1300℃,當軋制總變形量達到70%時,于1200℃退火1h,終軋溫度為850℃。(8)將步驟(7)熱軋得到的板坯,再經(jīng)過1750℃、5h退火處理,最終得到具有極高的高溫抗蠕變性能的摻雜鉬板。本實施例軋制后摻雜鉬板的金相組織類似于實施例1軋制后摻雜鉬板的金相組織;本實施例中高溫退火后摻雜鉬板的金相組織類似于實施例1中高溫退火后摻雜鉬板的金相組織,晶粒呈長大晶組織。通過高溫載荷抗彎試驗(如圖3所示,載荷重量1.2kg)來測試材料的高溫抗蠕變性能,經(jīng)測試,本實施例制備的鉬板測試參數(shù)和高溫抗蠕變性能數(shù)據(jù)見表1。實施例3生產(chǎn)厚度1mm的高溫抗蠕變鉬板,其中,按重量百分比含有K:0.01%,Si:0.01%。本實施例中,K源為KNO3,Si源為H2SiO3,Mo源為四鉬酸銨。具體制備方法如下:(1)考慮到還原和燒結時的揮發(fā),K和Si分別按照0.03%和0.03%摻入。KNO3、H2SiO3和四鉬酸銨的重量比例為:0.1498:0.1611:200。(2)分別稱取0.1498kgKNO3,0.1611kgH2SiO3配制成含KNO3、H2SiO3的混合溶液,稀釋至18L,倒入雙錐式真空干燥摻雜鍋的摻雜液罐中,待用。在摻雜鍋內裝入200kg四鉬酸銨,然后開始轉動摻雜鍋。利用空壓機壓力將混合溶液噴入摻雜鍋,待摻雜液罐中的溶液噴完。用蒸汽發(fā)生器產(chǎn)生的蒸汽加熱摻雜鍋,將水分蒸干,蒸汽發(fā)生器的壓力為0.18MPa左右,蒸干時間約為2.7h。蒸干后,在摻雜鍋的夾層通入冷卻水,冷卻時間約為2h。冷卻完成后,將摻雜好的四鉬酸銨卸出。(3)將步驟(2)得到的摻雜好的四鉬酸銨通過四管還原爐還原成摻雜二氧化鉬,還原溫度為510℃,裝舟量為230g/舟,推舟速度為25min/舟。(4)將步驟(3)還原得到的摻雜二氧化鉬,在四管還原爐中進行第二次還原,還原溫度為970℃,裝舟量為1.2kg/舟,推舟速度為20min/舟。(5)將步驟(4)還原得到的摻雜鉬粉,過160目篩,冷等靜壓成型,成型壓力為180MPa,保壓時間20min,得到摻雜鉬板坯。(6)將步驟(5)得到的摻雜鉬板坯送入中頻爐燒結得到摻雜鉬燒結板坯,燒結溫度為1920℃,燒結時間為3h,板坯厚度為35mm。(7)步驟(6)得到的板坯經(jīng)熱軋得到1mm厚的鉬板,開軋溫度為1340℃,當軋制總變形量達到70%時,于1200℃退火1h,終軋溫度為850℃。(8)將步驟(7)熱軋得到的板坯,再經(jīng)過1750℃、5h退火處理,最終得到具有極高的高溫抗蠕變性能的摻雜鉬板。本實施例軋制后摻雜鉬板的金相組織類似于實施例1軋制后摻雜鉬板的金相組織;本實施例中高溫退火后摻雜鉬板的金相組織類似于實施例1中高溫退火后摻雜鉬板的金相組織,晶粒呈長大晶組織。通過高溫載荷抗彎試驗(如圖3所示,載荷重量1.2kg)來測試材料的高溫抗蠕變性能,經(jīng)測試,本實施例制備的鉬板測試參數(shù)和高溫抗蠕變性能數(shù)據(jù)見表1。實施例4生產(chǎn)厚度4mm的高溫抗蠕變鉬板,其中,按重量百分比含有K:0.03%,Si:0.024%。本實施例中,K源為KNO3,Si源為H2SiO3,Mo源為四鉬酸銨。除步驟(1)-(2)不同于實施例1以外,其他工藝參數(shù)與實施例1相同。步驟(1):考慮到還原和燒結時的揮發(fā),K和Si分別按照0.055%和0.049%摻入。KNO3、H2SiO3和四鉬酸銨的重量比例為:0.2746:0.2650:200。步驟(2):分別稱取0.2746kgKNO3,0.2650kgH2SiO3配制成含KNO3、H2SiO3的混合溶液,稀釋至20L,倒入雙錐式真空干燥摻雜鍋的摻雜液罐中,待用。在摻雜鍋內裝入200kg四鉬酸銨,然后開始轉動摻雜鍋。利用空壓機壓力將混合溶液噴入摻雜鍋,待摻雜液罐中的溶液噴完。用蒸汽發(fā)生器產(chǎn)生的蒸汽加熱摻雜鍋,將水分蒸干,蒸汽發(fā)生器的壓力為0.2MPa左右,蒸干時間約為3h。蒸干后,在摻雜鍋的夾層通入冷卻水,冷卻時間約為2h。冷卻完成后,將摻雜好的四鉬酸銨卸出。本實施例高溫退火后摻雜鉬板的金相組織,晶粒呈長大晶組織,高溫抗蠕變測試條件和性能數(shù)據(jù)見表1。實施例5-8除步驟(8)的退火溫度和時間不同于實施例1以外,其他工藝參數(shù)與實施例1相同。實施例5的退火條件為1550℃、5h,實施例6的退火條件為1700℃、5h,實施例7的退火條件為1800℃、5h,實施例8的退火條件為1850℃、5h。這四個實施例得到的鉬板的高溫抗蠕變測試條件和性能數(shù)據(jù)見表1。實施例9將實施例2制備的2.5mm的高溫抗蠕變鉬板打磨到厚度為2mm,其高溫抗蠕變測試條件和性能數(shù)據(jù)見表1。對比例1生產(chǎn)厚度2mm的普通純鉬板。(1)購買得到的鉬粉,過160目篩,冷等靜壓成型,成型壓力為180MPa,保壓時間20min,得到純鉬板坯。(2)將步驟(1)得到的摻雜鉬板坯送入中頻爐燒結得到摻雜鉬燒結板坯,燒結溫度為1920℃,燒結時間為5h,板坯厚度為35mm。(3)步驟(2)得到的板坯經(jīng)熱軋得到2mm厚的鉬板,開軋溫度為1250℃,終軋溫度為900℃。(4)將步驟(3)熱軋得到的板坯,再經(jīng)過900℃去應力退火得到普通純鉬板坯。表1本發(fā)明實施例和對比例所制備鉬板的高溫抗蠕變性能數(shù)據(jù)編號1700℃、3h彎曲度1800℃、3h彎曲度1900℃、3h彎曲度對比例112.1mm25.6mm>40mm實施例10.3mm0.6mm1.3mm實施例21.1mm2.7mm5.9mm實施例35.4mm12.8mm27.3mm實施例40.3mm0.6mm1.3mm實施例51.1mm2.8mm6.1mm實施例61.1mm2.7mm5.8mm實施例71.2mm2.8mm6.0mm實施例81.1mm2.7mm6.0mm實施例92.2mm3.9mm10.2mm顯然,上述實施例僅僅是為清楚地說明所作的舉例,而并非對實施方式的限定。對于所屬領域的普通技術人員來說,在上述說明的基礎上還可以做出其它不同形式的變化或變動。這里無需也無法對所有的實施方式予以窮舉。而由此所引伸出的顯而易見的變化或變動仍處于本發(fā)明創(chuàng)造的保護范圍之中。當前第1頁1 2 3